Polymaker is thrilled to announce the launch of PolyCore™ PC-7413, a cutting-edge pellet-based material made from 30% glass fiber reinforced polycarbonate (PC). This advanced material is specifically engineered for medium-temperature (80 °C - 120 °C) composite mold applications, an area that has rapidly evolved in recent years through the adoption of fused granule fabrication (FGF), also known as Large-Format Additive Manufacturing (LFAM). By leveraging FGF/LFAM, manufacturers achieve significant reductions in lead time and production costs.
“Over the past few years, producing large molds has rapidly become the most popular application of FGF/LFAM. PolyCore™ PC-7413 combines exceptional printability with cost-effectiveness to set a new benchmark in mold manufacturing.” Stated Raymond Huang, Director of Polymaker’s FGF Business.

Figure 1 | A mold was printed with PolyCore™ PC-7413
Key Features and Industry-Leading Capabilities
PolyCore™ PC-7413 boasts numerous advantages, making it an outstanding choice for medium-temperature composite mold applications.
- Excellent Heat Resistance: With a heat deflection temperature (HDT) of 136 °C at 1.82 MPa, PolyCore™ PC-7413 is ideal for autoclave curing processes up to 120 °C.
- Exceptional Printability: The glass fiber reinforcement minimizes warping during printing, and its finely tuned rheological behavior ensures smooth extrusion and excellent layer adhesion.
- Cost Effectiveness: PolyCore™ PC-7413 offers a cost-effective alternative to traditional carbon fiber reinforced materials, making it perfect for companies scaling up production without compromising on performance.
The material's performance was validated through a real-world case in which an aerospace-grade mold was successfully produced and subjected to additional rigorous testing. The mold met strict requirements for dimensional tolerance (± 0.2 mm) and airtightness, confirmed by high-precision laser scanning and vacuum tests. These results demonstrate the material’s exceptional heat resistance, strength, and dimensional stability, underscoring PolyCore™ PC-7413 as an ideal choice for composite mold applications.

Figure 2 | The mold and carbon fiber part after autoclaving

Figure 3 | Dimensional inspection result of the mold after autoclave curing
A Collaborative Success with Helio Additive
Beyond PolyCore™ PC-7413’s inherent material properties, we believe that the printing process, optimized by Dragon was also a critical factor in achieving the complete mold validation. By using a thermal history simulation for each voxel, Dragon’s optimization achieved a more uniform thermal distribution across the mold, reducing internal stress and enhancing layer adhesion. This process refinement contributed to the mold’s dimensional stability and airtightness, leading to a successful "First Time Right Print" with a 38% reduction in printing time.

Figure 4 | Optimization report from Dragon
“Materials are at the heart of what makes large format additive manufacturing powerful. Collaborating with Polymaker allows us to use the full power of Dragon with state-of-the-art materials to develop solutions for composite tooling.” Stated David Hartmann, CEO of Helio Additive
See PolyCore™ PC-7413 at Formnext 2024
Polymaker invites you to explore the capabilities of PolyCore™ PC-7413 and see firsthand how this new material can transform your manufacturing processes. Visit our booth at Formnext in Hall 12.1, Stand C21 to learn more.
For more information, or to explore how PolyCore™ PC-7413 can benefit your production, contact us at polycore.inquiry@polymaker.revolware.com.
Since its launch, Polymaker's PolyDryer™ has captured the attention and enthusiasm of the 3D printing industry. This innovative product has impressed consumers with its advanced features and exceptional performance, solidifying Polymaker's commitment to enhancing the user experience and simplifying creation.

Key Advantages and Market Enthusiasm
PolyDryer™ stands out in the market with its dual functionality, combining drying and sealing capabilities into one comprehensive solution. It effectively addresses common issues such as moisture-induced stringing, clogging, and poor surface quality. The product consists of two main components: the Dry Dock, which ensures stable temperatures for quick and even drying, and the PolyDryer™ Box, designed with superior sealing performance. Together, they provide a seamless experience for users, preventing common printing issues caused by moisture and dust.
The product has garnered positive feedback from key opinion leaders (KOLs) and consumers alike. Many have praised its efficient drying and storage capabilities, as well as its modular design, which allows for flexible usage. Users have expressed their excitement about the impact PolyDryer™ has had on their prints, inspiring them to experiment with new materials and techniques. Polymaker is thrilled to witness how PolyDryer™ has sparked creativity within the industry.


Sourced from YouTube

Sourced from X
Commitment to User Experience
Hang Qu, VP of Sales & Marketing in Polymaker, emphasized the company's dedication to user experience and continuous improvement. “At Polymaker, we value user feedback and market insights. We actively collect this information and communicate with our internal Product Engineering Department to explore potential improvements. Our goal is to ensure that our products not only meet but exceed user expectations.”
In response to the high demand, we are excited to announce that PolyDryer™ is back in stock! We appreciate the enthusiasm for this product and invite new users to experience its benefits.

Simplify Creation
Polymaker is dedicated to ongoing research and development to enhance user satisfaction and simplify the creation process. The success of PolyDryer™ is a testament to this commitment, showcasing our focus on providing high-quality, reliable solutions for 3D printing enthusiasts. As we continue to expand our range of materials and services, we remain focused on empowering users to achieve their best work.
With PolyDryer™, you can ensure optimal printing conditions and improved print quality. With Polymaker, you can enjoy high-quality filaments’ printing process and achieve outstanding results. Join us as we continue to innovate and inspire creativity in the world of 3D printing.
For more information and to purchase PolyDryer™, visit the link below.
US Web Shop: PolyDryer™ – Polymaker US
Find A Reseller: Find a Reseller - Polymaker
Polymaker, a leading producer of 3D printing materials, announces the expansion of its product portfolio with the launch of two new distinct product families, Fiberon™ and Panchroma™. Fiberon™ focuses on developing cutting-edge composite filaments with both high performance and excellent printability, while Panchroma™ offers filaments with the most diverse range of aesthetic properties. These new offerings underscore Polymaker's commitment to innovation and its ongoing efforts to meet the diverse needs of the 3D printing industry.
"We see two increasingly critical needs in the FDM/FFF industry – functional properties and aesthetics. Fiberon™ and Panchroma™ are our answers to address these customer needs," stated Dr. Xiaofan Luo, CEO of Polymaker.
Fiberon™
Master composite materials with Fiberon™, democratizing high performance composite 3D printing filaments with a comprehensive range of material properties. The launch of Fiberon™ introduces 3 new fiber reinforced materials to the market, PET-CF17, PETG-rCF08 & PPSCF10. These new materials are paired together with the existing composite filaments from Polymaker (PA6-CF20, PA6-GF25, PA612- CF10, PA12-CF10, PETG-ESD). In essence, Fiberon™ brings industrial-grade composite performance to the desktop, enabling a new wave of end-use part production and functional prototyping applications previously off-limits due to printer capabilities and pricing.

"Traditionally, desirable material properties like strength or heat resistance required expensive industrial printers. Fiberon™ challenges this. With advanced materials, users can print strong, stable, functional parts using entry-level printers. We’re democratizing high-performance 3D printing materials.” - Dr. Xiaofan Luo, CEO of Polymaker
Learn More: Fiberon 3D Printing Filament by Polymaker – High-Performance Composite Filaments
Panchroma™
Polymaker’s new aesthetic product family is designed to meet the growing demand for high-quality, visually stunning 3D prints by offering the widest selection of colors and surface finishes available on the market. Panchroma™ is committed to the highest consistency of color for its products with a multi-step process monitoring the quality control for color consistency.

Panchroma™ employs a number of extrusion techniques in order to create their filaments and the combinations of these techniques with the multitude of color expands the filament offering exponentially. Filaments are divided by their extrusion process, then surface finish and finally the color. This allows users to navigate through the vast array of options and find the filament they need.
To further assist customers with their workflows, Polymaker is developing a web-based tool that allows users to create realistic digital renders based on different Panchroma™ colors & surface finishes.
Learn More: Panchroma 3D Printing Filament – Where easy printing meets the world of color (polymaker.com)
On the occasion of the official launch of these two product families, Polymaker has completely upgraded the packaging to enhance the user experience.
• Adding Inside and Outside Spool Wrapping: This ensures smooth rotation of the spools in the AMS while preventing the cardboard dust from dropping during use.


Before vs After
•Modified Hole Shape and Spacing: These changes reduce the likelihood of breakage during threading, enhancing durability.


Before vs After
• Larger Windows on Both Sides of the Cardboard: This allows customers to easily see the filament color, providing a more intuitive selection process.


Get ready for the launch of these upgraded products!
Polymaker is excited to launch PolyDryer™, a revolutionary product designed to provide the ultimate solution for drying and storing 3D printing filaments which protects against dust and moisture. With advanced features, such as modular design, superior sealing performance and high drying efficiency, PolyDryer™ aims to enhance the quality of 3D prints by addressing common issues.

Printing with wet 3D filament can lead to various issues such as stringing, clogging and rough or poor surface quality, highlighting the necessity for drying or sealing. While existing drying or sealing products on the market solve these problems to some extent, combining drying and sealing functions into one comprehensive solution has been a focus for Polymaker, leading to the creation of PolyDryer™.

The whole product features modular design and consists of two units: Dry Dock, ensuring stable temperatures for quick and even drying with a precise heat control system and PTC heater, and PolyDryer™ Box, which offers superior sealing performance and continuous filament protection. These components can be used separately or together. Dry Dock evenly dries filaments in the PolyDryer™ Box above it, and PolyDryer™ Box can be used with or without the dock for separate storage.

Second key feature is its superior sealing performance. PolyDryer™ allows for extended drying and long-term protection of materials. Its exceptional sealing capability and visible desiccant indicator display maintains optimal humidity levels, ensuring that filaments are dry and ready for printing.

Thanks to the high precision heat control system, fan and PTC heater, PolyDryer™ can dry the most commonly used 3D filament types efficiently, including PLA, ABS, ASA, PETG, PA, TPU, PC and more. In addition, filament can also be dried during printing if you press and hold button "M" to activate Continuous Drying Mode, to ensure thorough drying of all filament layers, providing double assurance of material quality.

PolyDryer™ offers wide compatibility with various 3D printing materials, accommodates filament up to 1kg, and both of 1.75mm/2.85mm/3.00mm diameters can be used in it. Moreover, it has a compact footprint for which makes it easily portable.
"PolyDryer™ offers a one-stop solution for effective drying and sealing, ensuring optimal printing conditions and improved print quality," stated Dr. Luo Xiaofan, President of Polymaker. He added, "As a brand dedicated to meeting user needs, we aim to provide a complete 3D printing filament solution with this product. In the future, Polymaker will expand its presence in 3D printing materials, offering a wide range of material services to simplify creation.”

Now PolyDryer™ is available on the market, for more details or to purchase, click the link below.
US Store: https://us.polymaker.com/products/polydryer
Amazon: https://www.amazon.com/dp/B0CK1BX9G2
Find A Reseller: https://polymaker.revolware.com/find-a-reseller
In addition to the product, several PolyDryer™ exclusive accessories have been carefully designed to enhance your 3D printing experience, please follow us on Printables and MakerWorld:
Polymaker | Published - MakerWorld
Note: DIY modifications may affect the safety and performance of the PolyDryer™.
Christmas is coming, Polymaker is delighted to unveil our 2023 Christmas Limited Bundle. It is designed to ignite the holiday spirit and bring your Christmas creations to life.
This exclusive bundle features three exquisite filaments, each with its own unique characteristics, and is adorned with a festive "Merry Christmas" packaging that captures the joyful essence of the season. Each filament spool in the Christmas Bundle features a unique 2023 label, signifying its exclusivity as this year's Polymaker Christmas edition.

Let's explore the captivating features of our Christmas Bundle:
- Champagne Gold: Step into a world of elegance with this filament. This filament offers a silk-like texture, reminiscent of shimmering holiday lights. Its sheen appearance adds a touch of sophistication to your Christmas-themed prints, making them truly stand out.
- Comet's Extravagance Green: Unleash your creativity with Comet's Extravagance Green filament. This filament, with mesmerizing color-changing effect, referring the fact that stars appear in different colors and brightness when viewed from different angles, creates a captivating visual spectacle.
- Santa's Velvet Red: Experience the warmth and coziness of the holiday season with this filament. This rich and vibrant red filament exudes a silk texture that adds depth and dimension to your Christmas-inspired designs. It perfectly captures the essence of Santa's iconic suit.
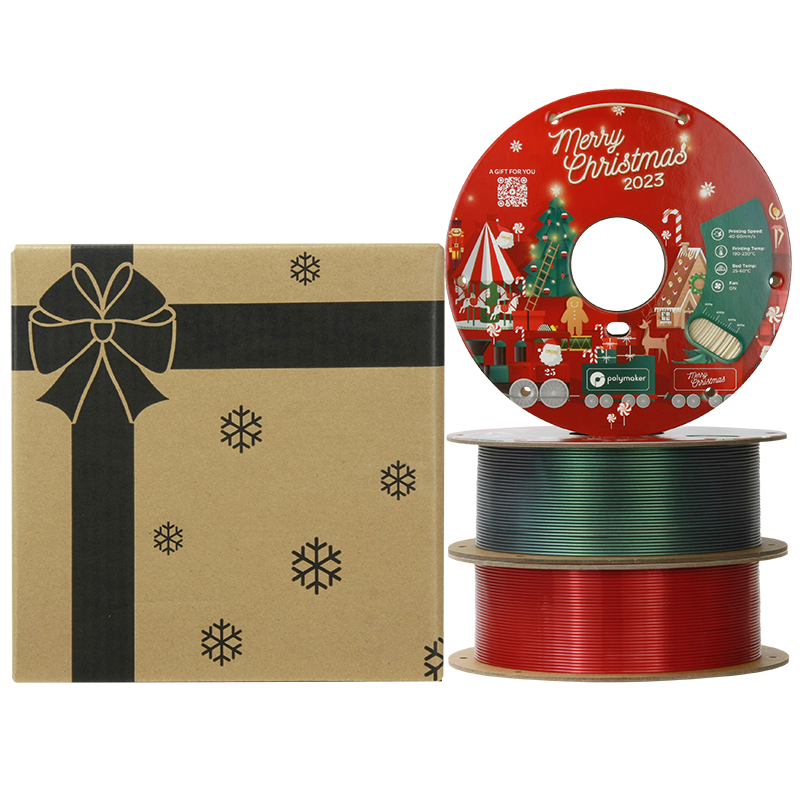
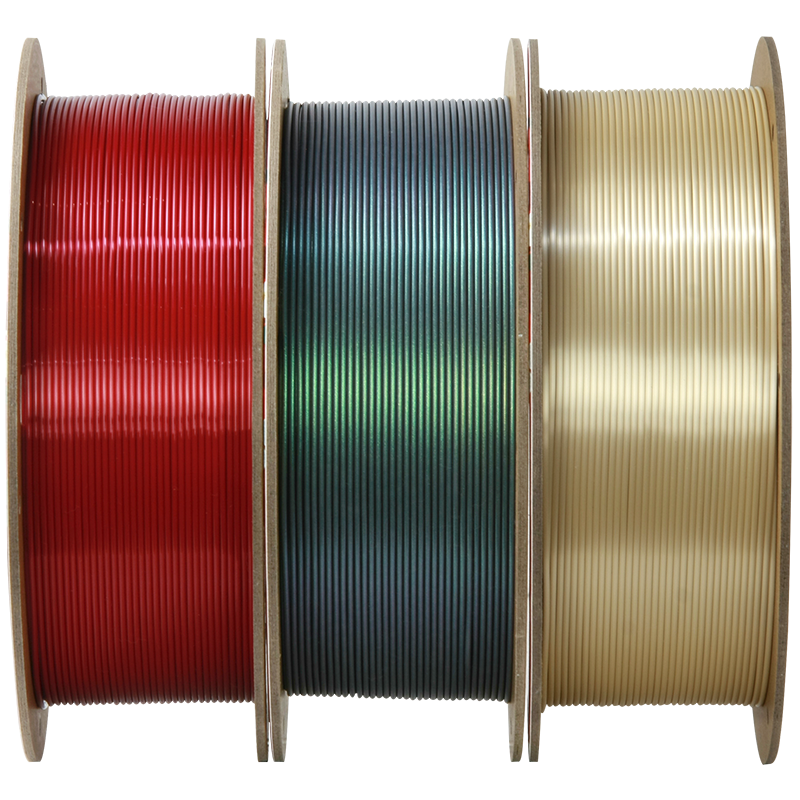
But that's not all! As a special treat, simply scan the QR code on the paper spool label, and discover the secret Christmas gift that Polymaker has prepared just for you.
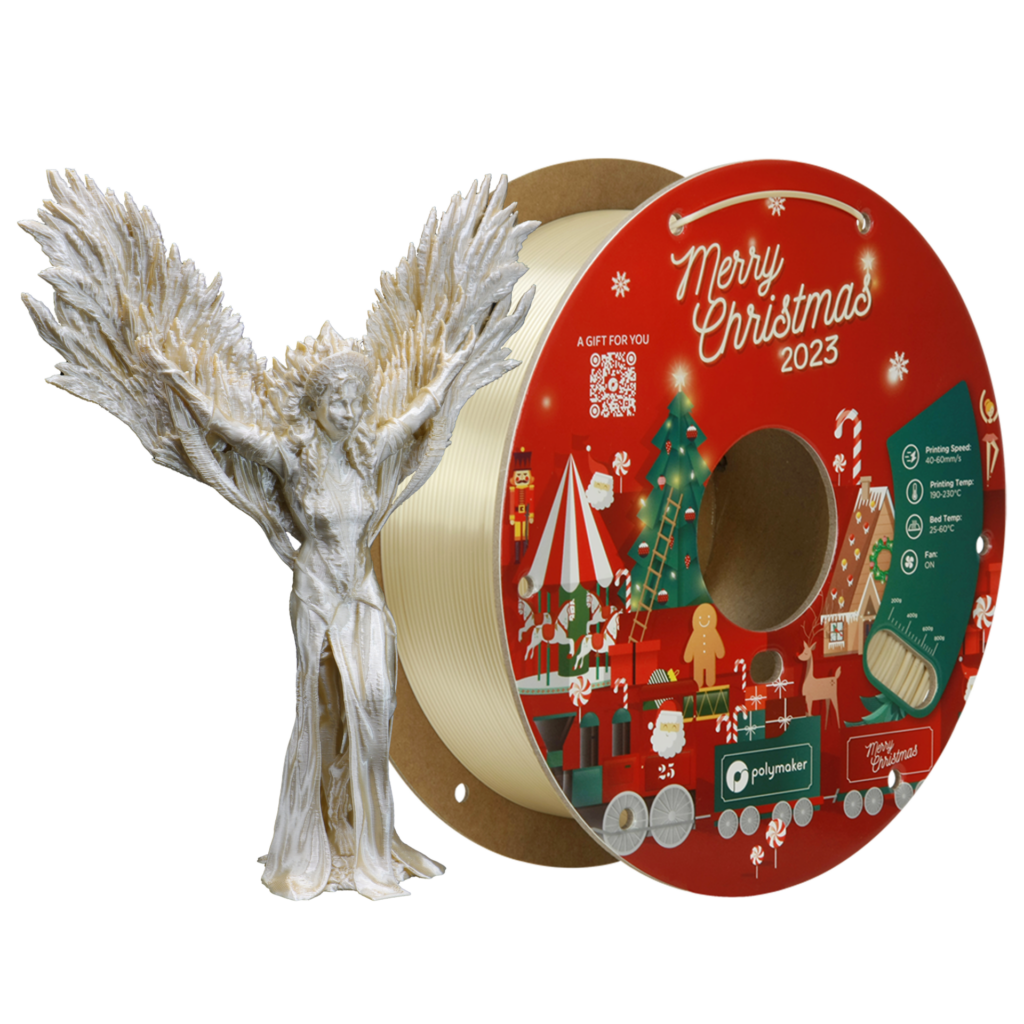
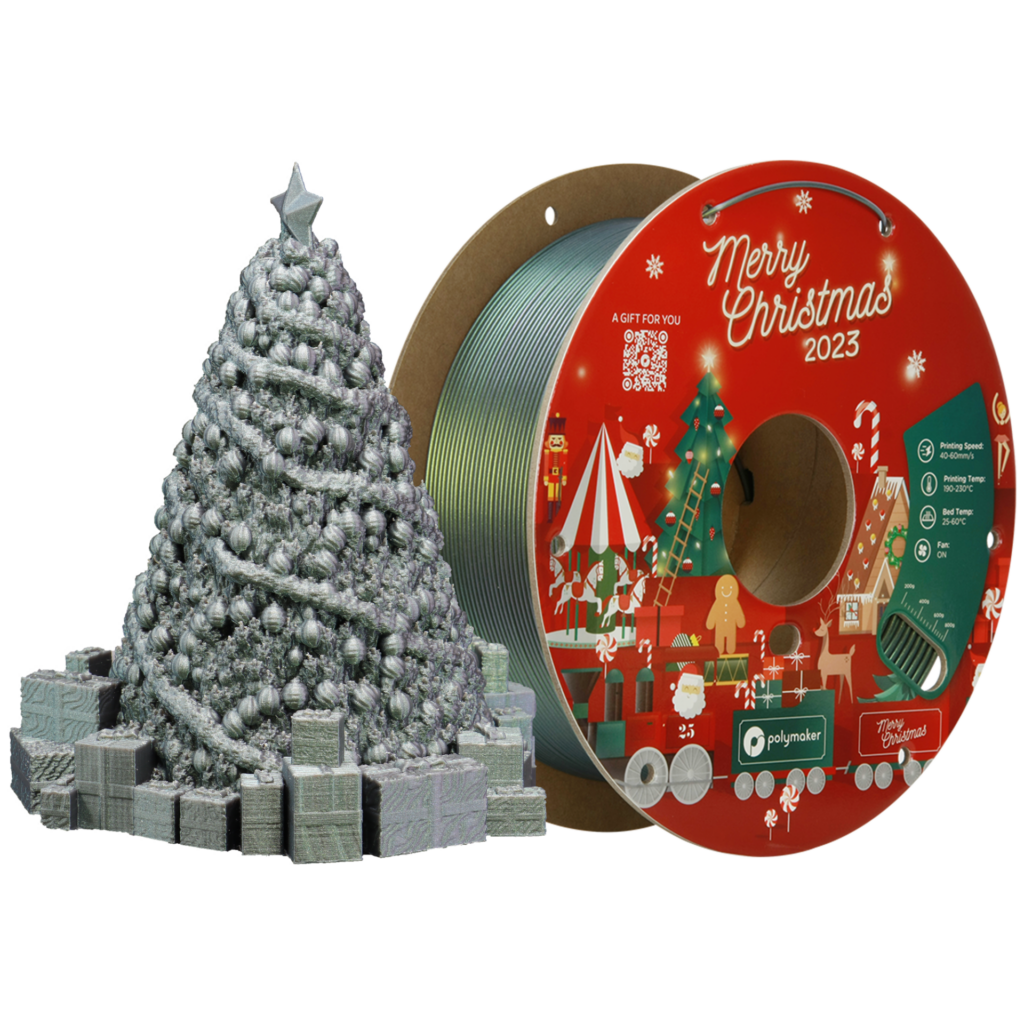
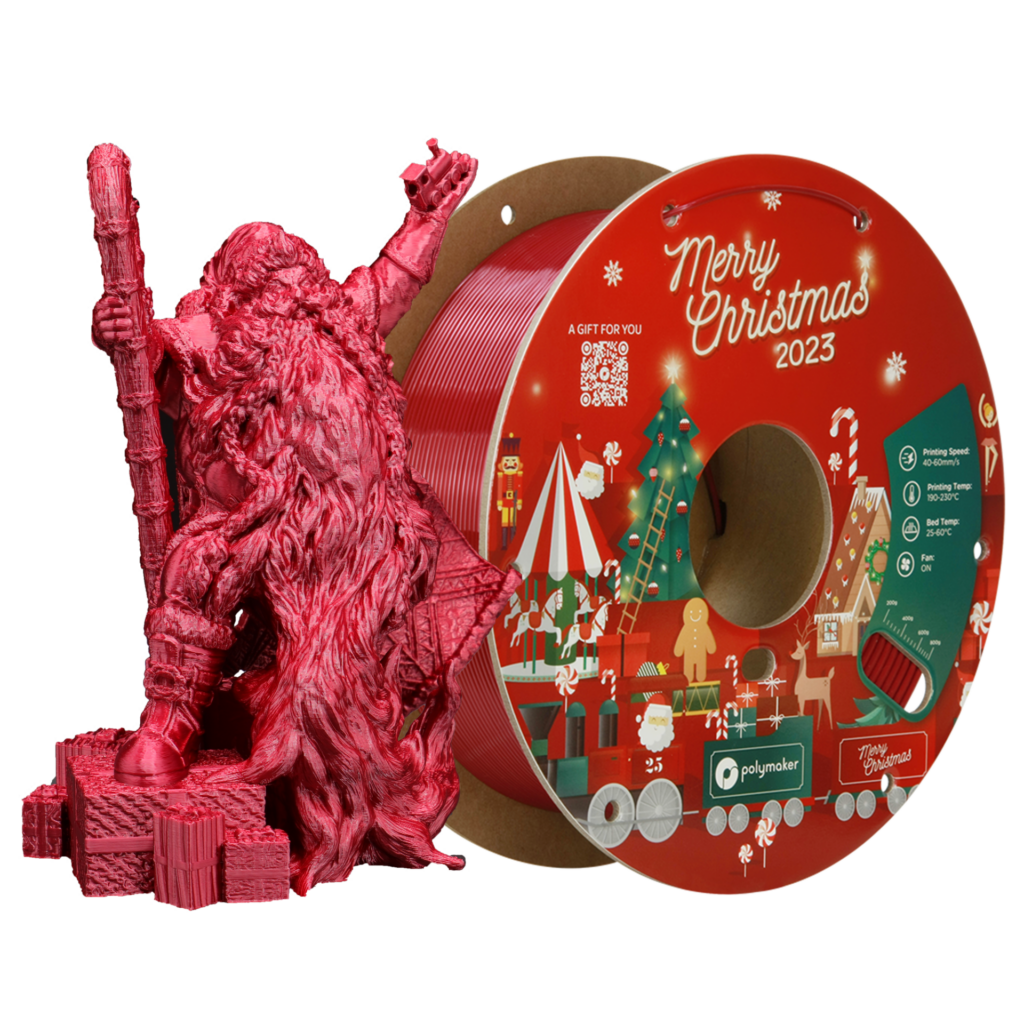
At Polymaker, we believe the combination of the Champagne Gold, Comet's Extravagance Green, and Santa's Velvet Red filaments will bring your Christmas prints to life, capturing the spirit of the season in every intricate detail.
Please click the below purchase links to get them~
US Web Store: Seasonal Packs (polymaker.com)
Reseller: Find a Reseller - Polymaker
Please note that the Christmas Bundle is available in limited quantities, adding an air of exclusivity to this special collection. Don't miss the opportunity to elevate your Christmas creations with our enchanting filaments and make this holiday season truly unforgettable.
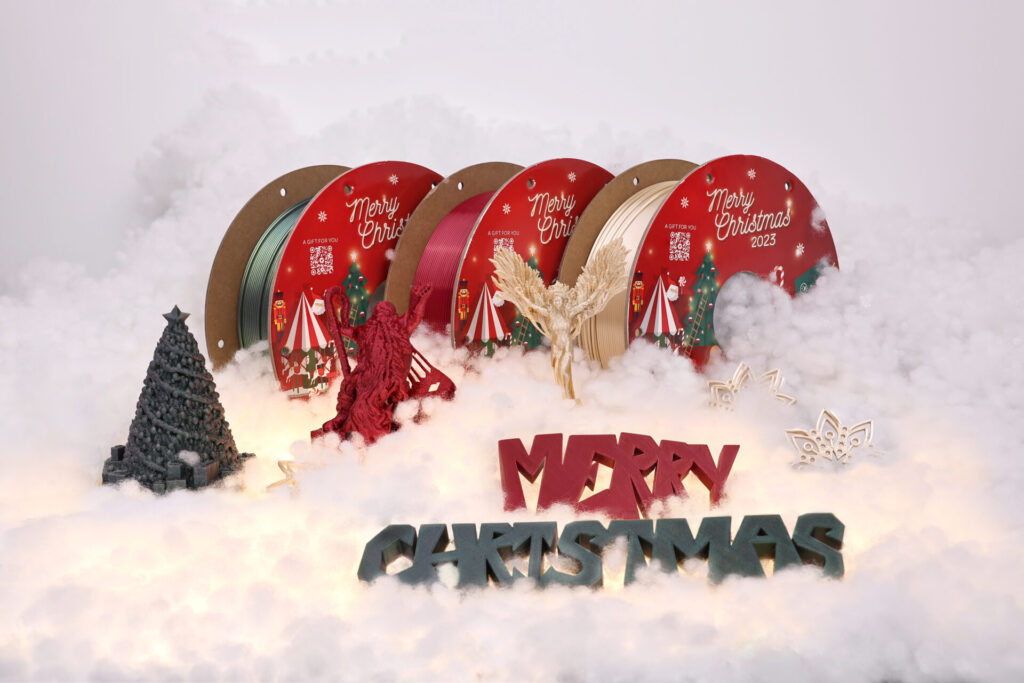
We are thrilled to announce the launch of our highly anticipated 2023 Polymaker Halloween Pack. This limited edition bundle is specifically designed to ignite the imagination of Halloween enthusiasts and creators, providing a unique color palette and special effects that will bring your spooky visions to life!
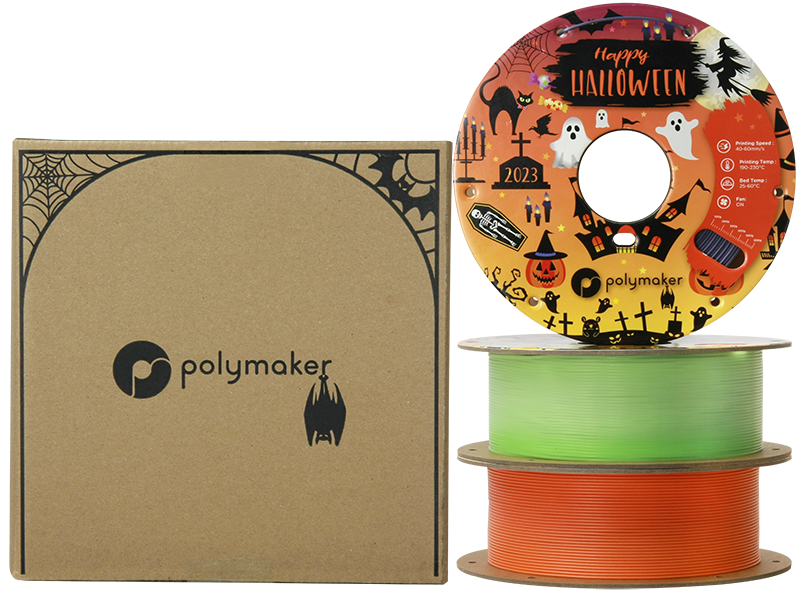
What makes our Halloween Limited Edition Bundle stand out? Let's dive into its incredible charming points:
- Unique Color Palette: The Halloween Bundle offers a captivating blend of colors, including the mesmerizing Pumpkin Patch Orange and Ghastly Purple from our PolyTerra™ Gradient Color series. These colors seamlessly transition from one shade to another, adding depth and dimension to your Halloween-themed prints.
- Gradient Color-Changing Effect: Each filament strand in the bundle boasts a remarkable gradient color-changing effect. Watch as your prints come to life with stunning visual transformations, creating an eye-catching spectacle that will leave everyone in awe.
- Glow-in-the-Dark Green: To add an extra element of fun and surprise, we've included our Slime Glow Green filament from the PolyLite™ Gradient Color series. This glow-in-the-dark feature will bring an enchanting glow to your Halloween-inspired designs, making them truly unforgettable.
- High-Quality Performance: Our PLA filament, used in the Halloween Pack, ensures smooth printing, excellent layer adhesion, and consistent results. We want to provide you with a hassle-free printing experience, whether you're a beginner or an experienced user.
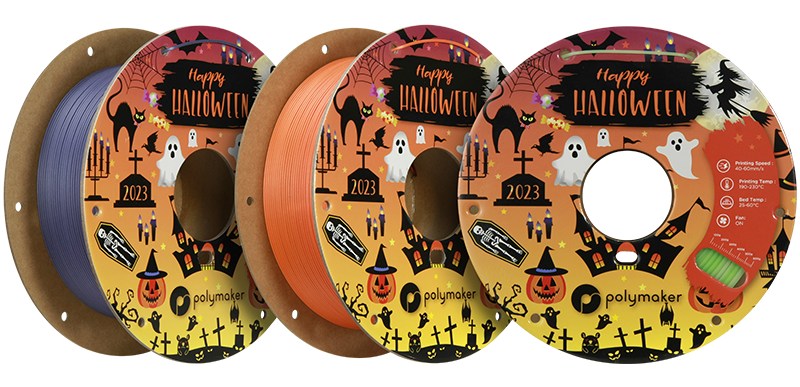
At Polymaker, we position our 2023 Halloween Pack as a must-have for those seeking to bring their spooky visions to life including Halloween enthusiasts, cosplayers, prop makers, hobbyists and collectors. The unique gradient color-changing effect and glow-in-the-dark feature will capture attention and create intrigue.
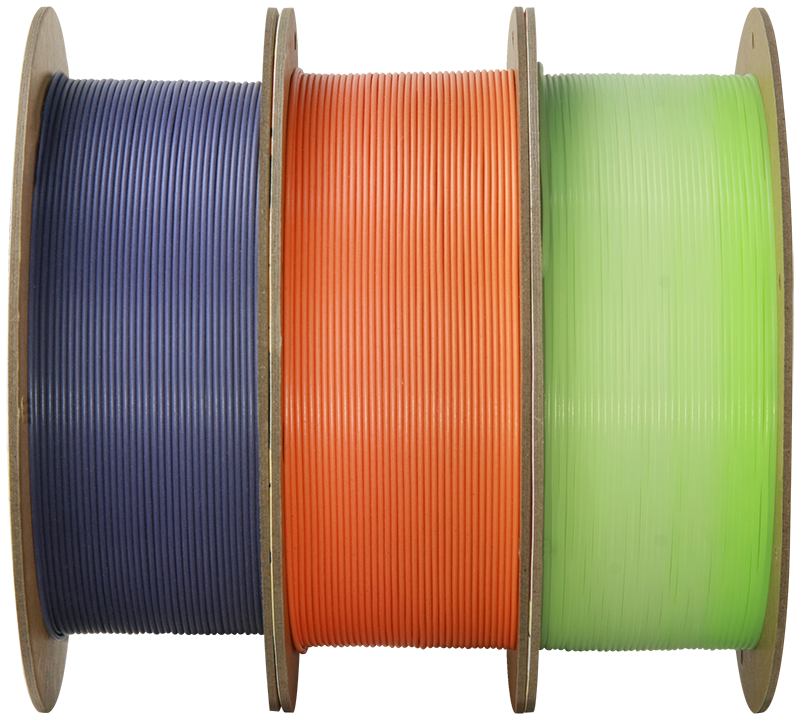
Limited availability adds exclusivity to our Halloween Pack, making it a coveted choice for Halloween-inspired prints. Don't miss out on the chance to elevate your Halloween creations with our captivating filaments and make this Halloween truly unforgettable!
Please click the below purchase links to get them~
US Web Store: Seasonal Packs (polymaker.com)
Reseller: Find a Reseller - Polymaker
We've got a treat for you – a set of spooky STL models you can grab and use! Join in the Halloween fun! Don't be shy, feel free to get creative and share your spooky creations with us!
https://www.printables.com/model/589860-polymaker-halloween-pack-models-2023
On the path of “Simplify Creation”, Polymaker has consistently refused to compromise and has pushed forward with creativity. Today, Polymaker launched a brand-new family of 3D printing filaments dedicated to high-speed 3D printing. This move aims to drive the industry forward by increasing the productivity of 3D printers, allowing a higher volume of parts per hour without compromising on printing characteristics or the mechanical strength of the printed part.
“The latest generation of 3D printers have set a new benchmark for fast printing. But materials are still the missing link. PolySonic™ is Polymaker’s answer to the new era of high-speed FFF Printing.” – Dr. Xiaofan Luo – Founder of Polymaker
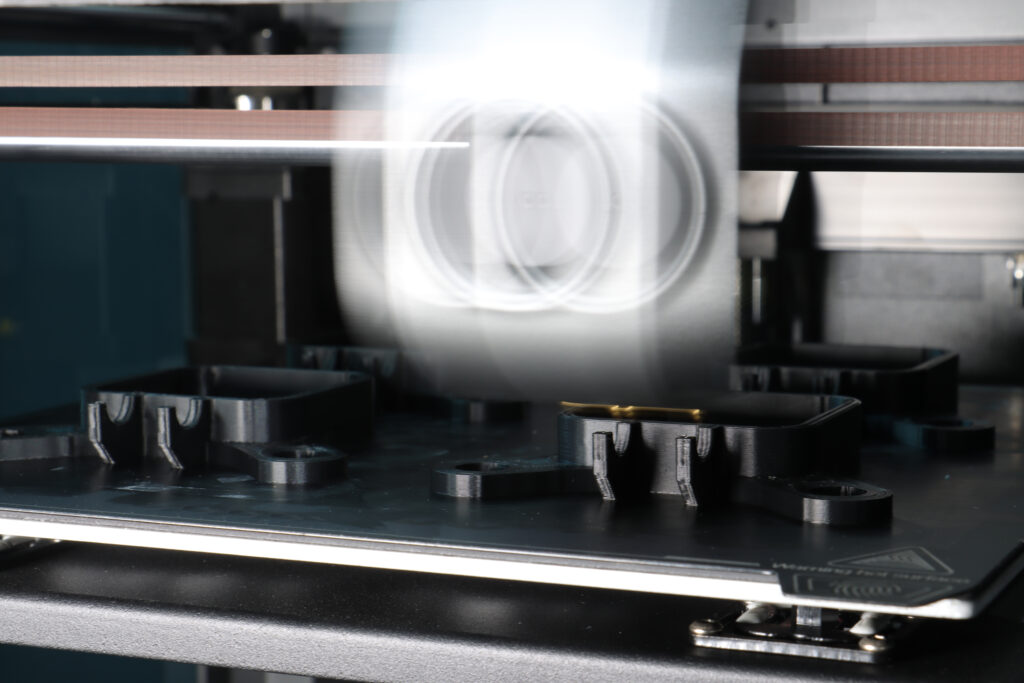
Three Crucial Aspects to Define High-Speed Filament:
Extrusion - PolySonic™ PLA filaments exhibit a wider extrusion window when compared to regular PLA filaments, producing a 30% increase in flow rate at the same printing temperatures when compared to regular PLA filaments. This boost in extrusion efficiency allows users to build profiles with higher printing speeds before noticing the effects of under-extrusion on the printed part.
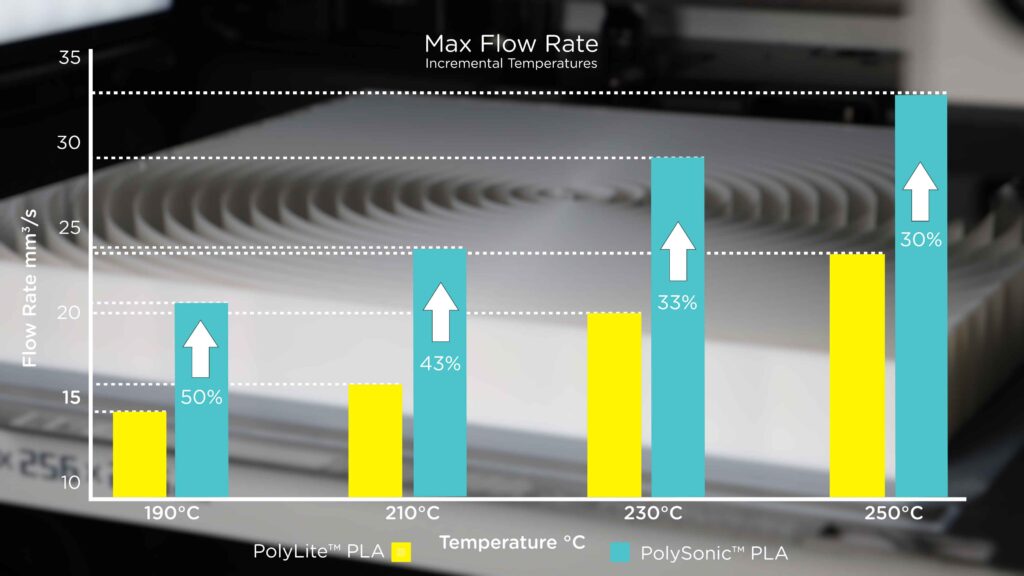
Forming - Polymaker scientists have optimized the rheology of the PolySonic™ so that it can transition from fluid to solid with near-zero shrinkage. This produces crisp corners, fine details and steep overhangs while still extruding at high flow rates. Moreover, it significantly enhances actual printing productivity compared to regular PLA, increasing production efficiency by up to 150%.
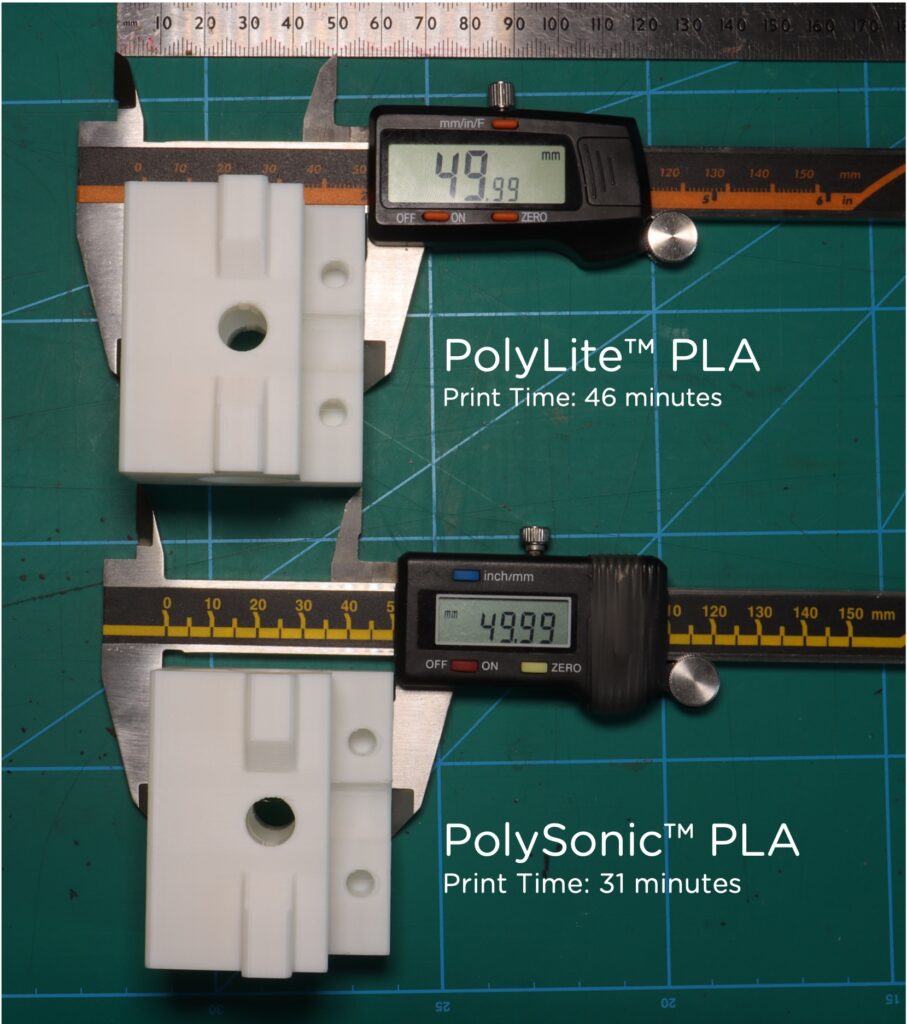
Mechanical Properties - PolySonic™ PLA shows only a 6% drop in mechanical properties when printing at high speed compared to the classic test specimen. In contrast, PolyLite™ PLA (regular PLA) witnesses a 24% drop when the speed is increased. This final factor allows PolySonic™ to print both fast and functional which has been the previous limitation to high-speed 3D printing. Users can increase the productivity of their machines without compromising on part strength or print quality.
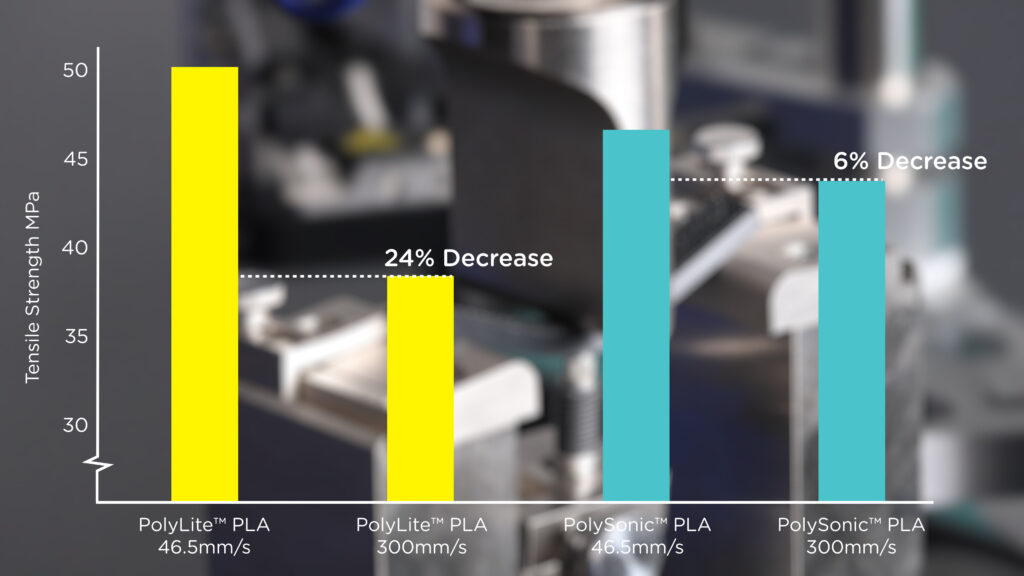
Two Types of Filaments to Meet Different Needs
PolySonic™ PLA, a revolutionary high-speed 3D printing filament, comfortably build printing profiles over 300mm/s with superior print characteristics. Its fast extrusion rate, high precision, and excellent interlayer adhesion greatly enhance 3D printing speed, providing users with a new and exciting experience! While accelerating printing efficiency, it also preserves its inherent mechanical performance, making it suitable for a wide range of applications, including functional prototyping, artistic creations, and production of end-use products. Initially available in 5 colors, it allows your colorful creativity to come to life!
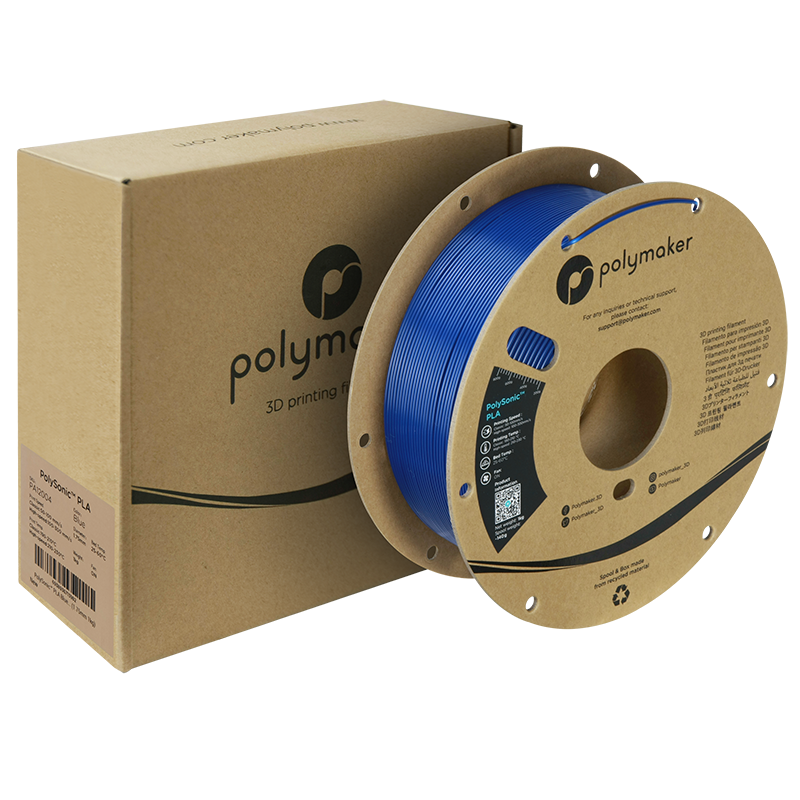
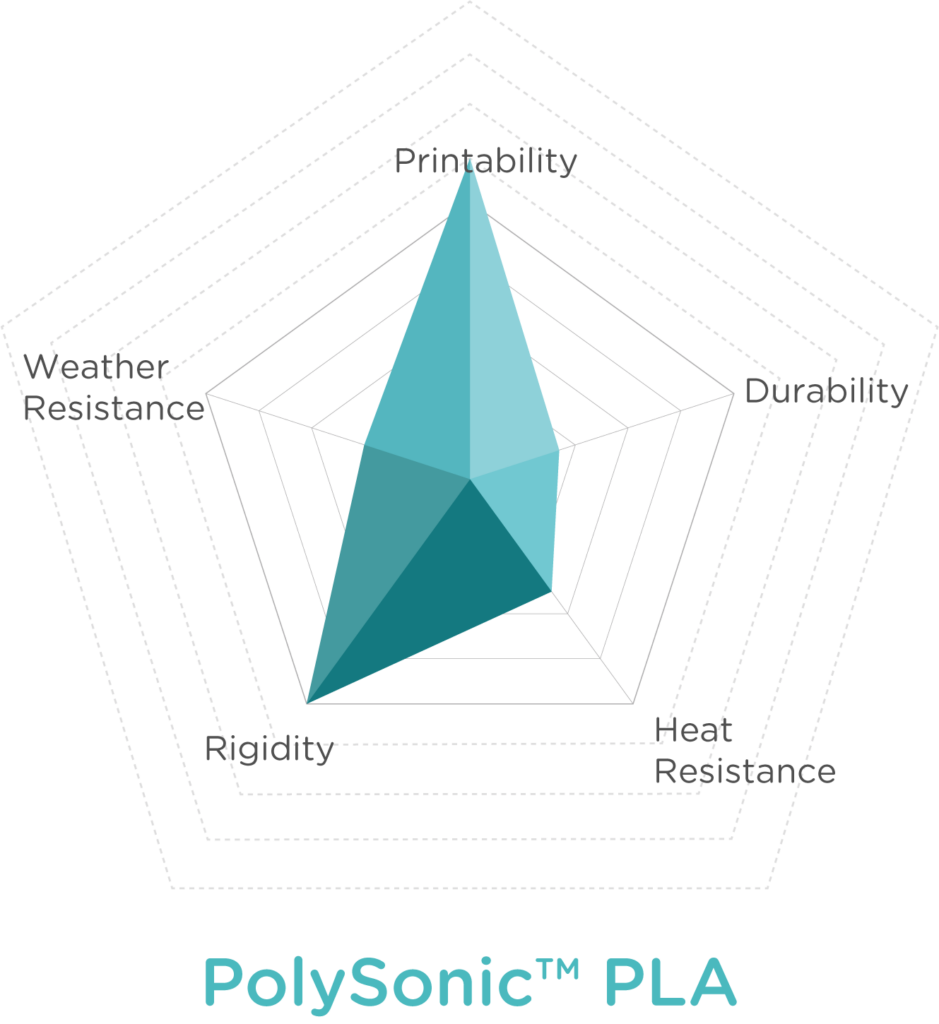
PolySonic™ PLA Pro is an improved toughness PLA compounded with impact modifiers that produce ductility similar to ABS and stiffness outperforming ASA & PETG. Its superior toughness and mechanical properties make it suitable for a wide range of applications, including creating finer functional prototypes, producing more durable end-use parts, and providing the necessary engineering components for industries such as automotive and consumer goods. It is an ideal choice for rapidly producing functional parts!
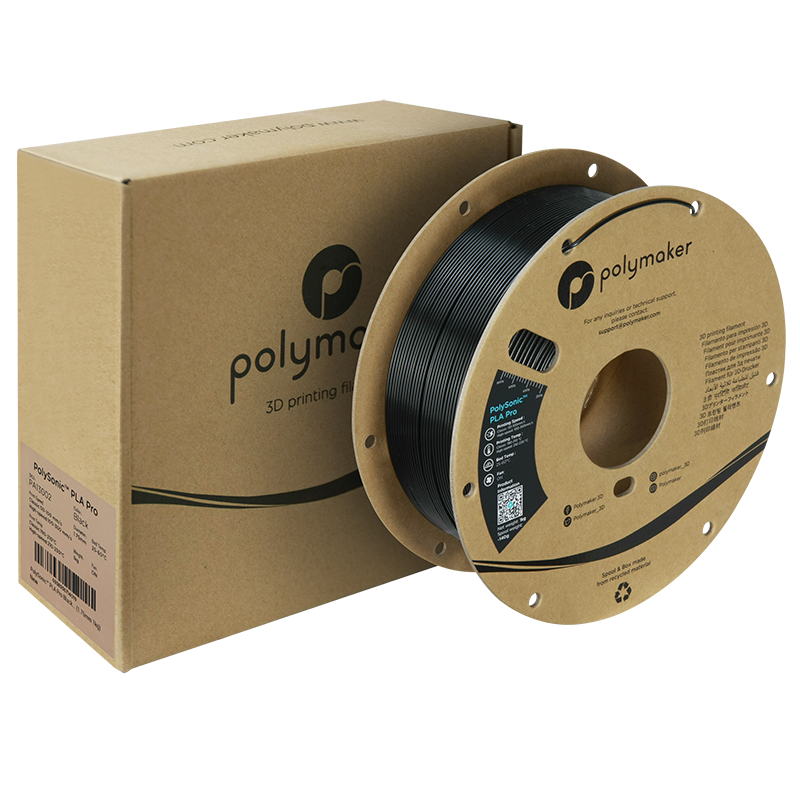
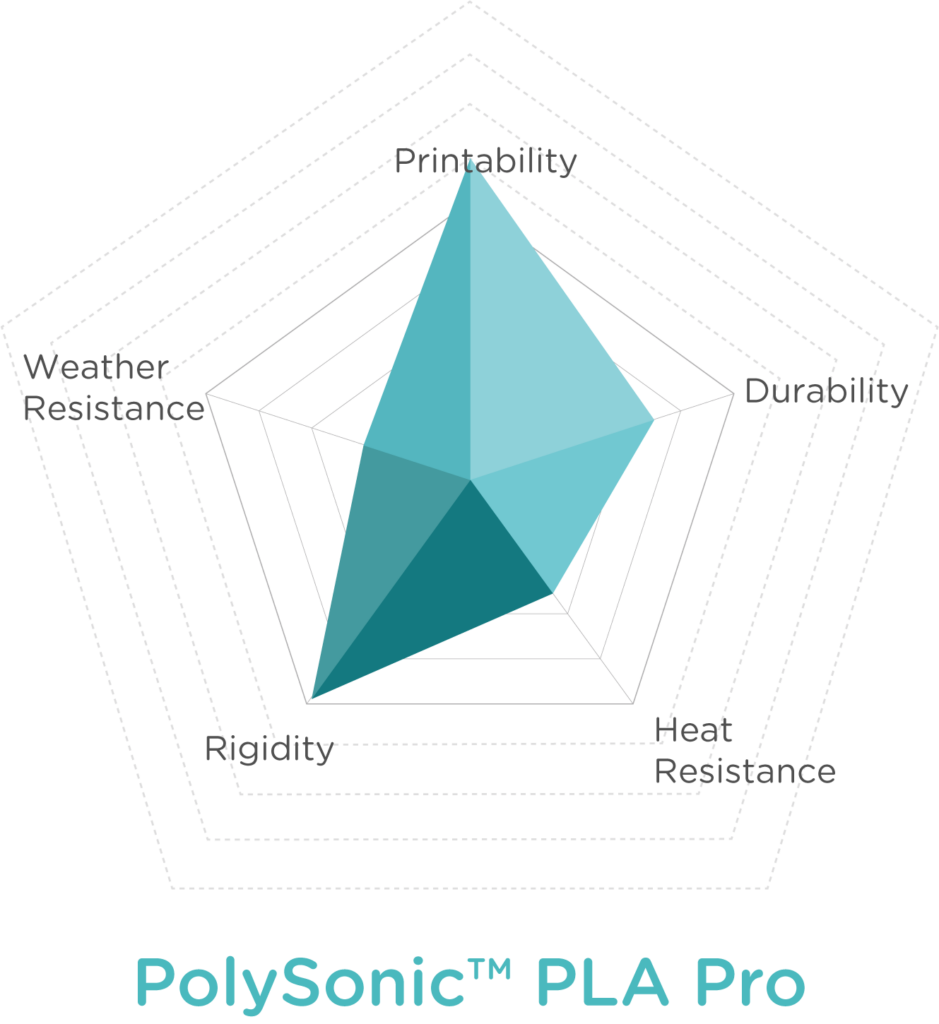
Overall, PolySonic™ is a new type of printing consumable that fully leverages printer efficiency without sacrificing the quality of 3D printed products. Whether you're a hobbyist, engineer, or designer, PolySonic™ PLA will bring your ideas to life faster and better than ever before. Unleash the speed of innovation and join the 3D printing revolution with PolySonic™ PLA.
The Polymaker spool adapter is designed to help your cardboard spools print more consistently by reducing friction and creating a structured rolling surface. The spool adapter clips around the face of the Polymaker cardboard spool and is fixed in place by three small tabs that grab the edge of the spool and a location pin that stops the adapter spinning.
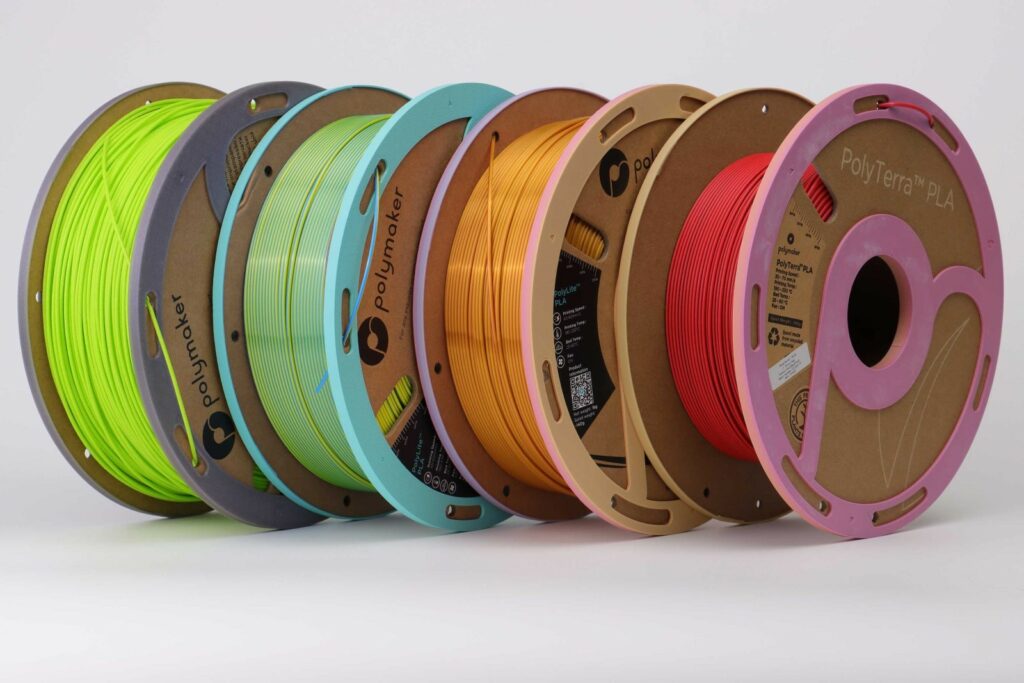
The adapter can help your 3D printer by reducing the rolling friction when mounted both internally or externally on almost every design of spool holder. One benefit that the cardboard spool provides is durability. The spool can be dropped off a table without shattering unlike our previous plastic spools. However, this bends or deforms the cardboard face of the spool leading it to unspool with a wobble. The spool adapter can solve this issue by providing a solid circular rolling surface to interface between the spool and spool holder.
Watch the video to see how the cardboard spool adapter works:
Multi-material stations that have assisted unspooling are often designed with small intricate gears that can get jammed by dust particles after hundreds of hours of printing. The spool adapter can eliminate the problem of dust build-up and allows Polymaker spools to be compatible with all multi-material stations, such as: Bambu Lab’s AMS or Ultimaker’s Material Station.
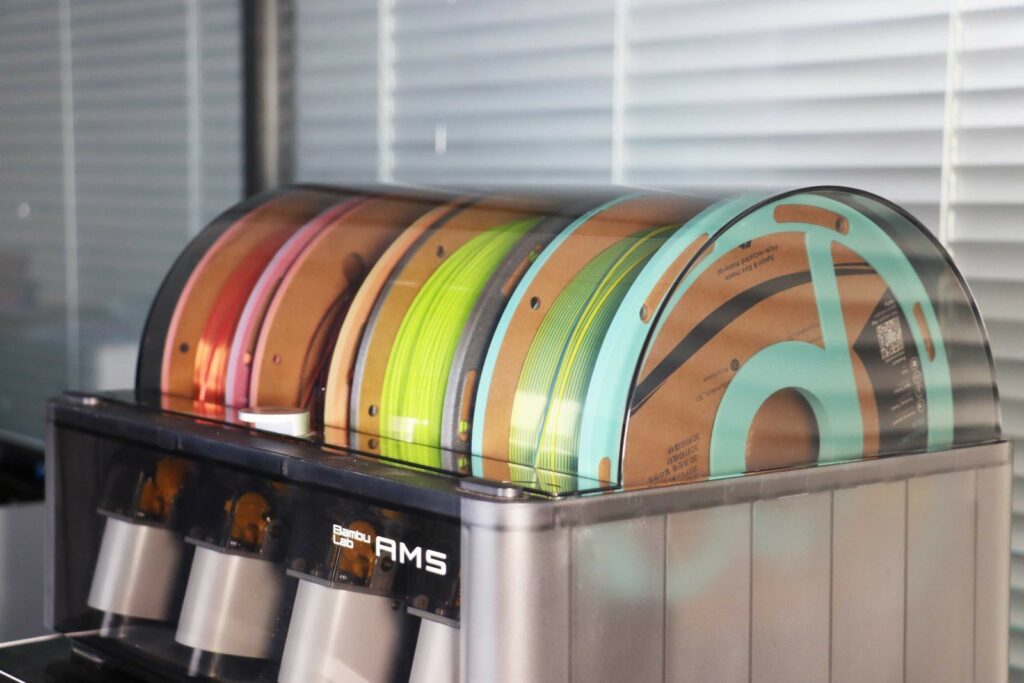
Our spool adapter design is by no means perfect, so we encourage you to remix and redesign to suit your needs where necessary. This design was inspired by our community so who have already designed and posted many similar rings and adapters. We are releasing the .STEP files as well as the .STL which will allow you to make some adjustments easily in the CAD software of your choice and everything is open source.
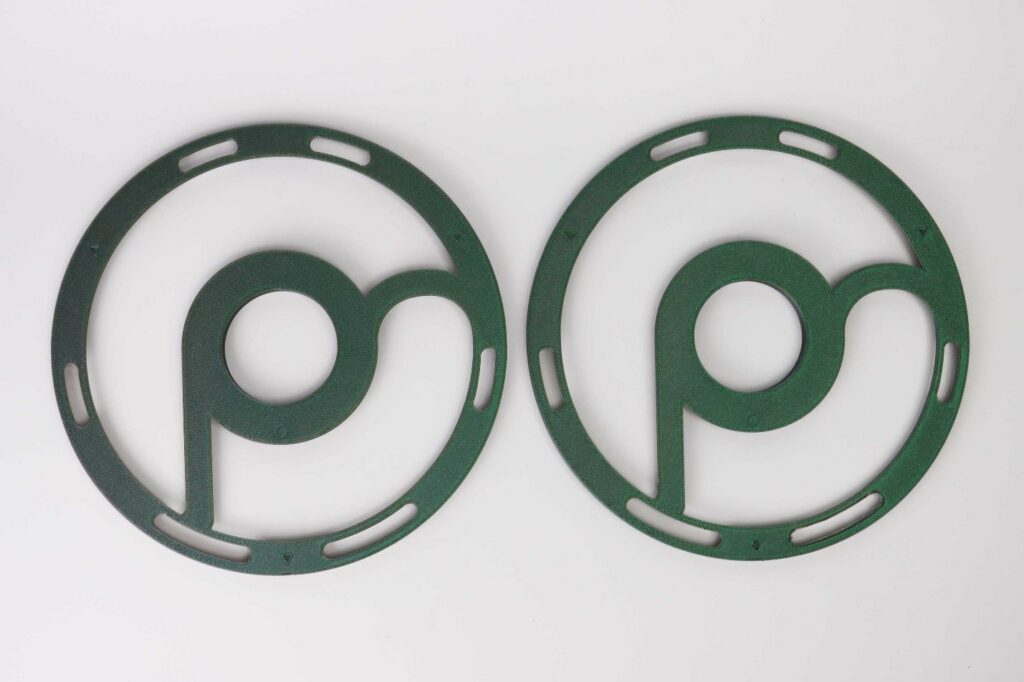
We tried to keep our design as light as possible, so it can be printed quickly and efficiently without using too much filament. You should be able to print one spool adapter in 40 mins, using 30g of filament and it should be able to be reused on many Polymaker spools. To lengthen the life of your spool adapter we suggest popping the location pin out first before removing the edge clips to reduce the stress on the adapter when changing spools. The design was intended to be printed in PLA however a much tougher material choice will result in a longer life for your spool adapter. Try PolyLite™ PETG, PolyLite™ ASA or PolyMax™ PLA for a spool adapter that can roll through the kilos.
Kindly find below link to fast download files and hope you enjoy the printing!
Printables: Polymaker Cardboard Spool Adapter by Polymaker | Download free STL model | Printables.com
Thingiverse: Polymaker Cardboard Spool Adapter by Polymaker_3D - Thingiverse
After releasing PolyTerra™ PLA on cardboard packaging earlier this year, we received many compliments from our customers praising our efforts to be eco-friendlier. Many customers loved our new cardboard spool both for its usability and disposability.
Fig.1 New Cardboard Spool
To further our efforts and establish a consistent brand image that contributes more on environmental protection, we decided to upgrade the whole Polymaker range from plastic spools onto cardboard spools!
Not only will this remove tonnes of plastic waste from the environment, it also provides a practical cardboard spool that is easy to rip apart after use and can be recycled in your regular paper recycling.
We are phasing in the new packaging while using up our plastic spools to save resources and avoid waste. This notification aims to avoid any confusion for our customers and we cannot guarantee which packaging you will receive during our transition stage. What we can guarantee is that you will receive the same high-quality filament that you expect from Polymaker.
Features of the New Spool
The new cardboard spool features a thick 4mm pressed and die-cut recycled cardboard spool face, glued onto a strip-rolled section of cardboard tube. The thickness of the cardboard ensures your filament is well protected and the spool can roll very efficiently on all designs of spool holder both internally or externally mounted.
Fig.2 Thick Cardboard Spool Face
On the front of the spool, you’ll find a QR code which will take you to the product information sheet on www.polymaker.com Here you can also find printing profiles, TDS, SDS, and all other documentation relevant to the filament.
Fig.3 QR Code for Product Information
The cardboard used to make the spool and box comes from 100% recycled sources.
Fig.4 Smaller Box, Larger Labels
On the box, we have created a new label with larger text making it easier to identify the material, diameter, and color of the filament. On the spool, we feature some basic printing information and the rough filament weight guide, a feature pioneered by Polymaker and followed by many filament manufacturers.
Fig.5 Weight Gauge
One of the biggest challenges for us was sourcing a glue that can withstand the high temperatures necessary to dry some of our filaments. Our nylon range, for example, needs to be dried at 100°C and the naturally sourced glue that holds our cardboard spools together has the ability to withstand those temperatures without melting.
Fig.6 Improved Winding
Our new product portfolio brand structure and visual identity set the tone for the future of our business – an organization that is customer-oriented, pioneering, creative, and responsible. We hope to create a diverse and innovative experience for our customers to help shape the world around them with 3D printing.
Thank you once again for your support and trust!
Polymaker
PolyMide™ PA12-CF: High stability nylon filament for 3D printing
PolyMide™ PA12-CF is a brand-new engineering filament offering high stability in both printing and application, delivering predictable mechanical properties regardless of the operating environment. PolyMide™ PA12-CF achieves this through its base polymer, nylon 12, which displays greater moisture stability when compared to common nylon 6 filaments. This means that PolyMide™ PA12-CF printed parts display minimal change in mechanical properties from the dry state to the wet state, therefore, more predictable mechanical properties in final printed parts. PA12-CF features 10% chopped carbon fibers which add strength and stiffness while also lowering the coefficient of thermal expansion, these characteristics, paired with Polymaker’s Warp-Free™ and Fiber Adhesion™ technologies provide an easy to print filament with extremely desirable properties.
Fig.1 Steering Wheel Core and Mould
The main difference between PA12 and PA6 is moisture stability. The longer PA12 polymer chain is much more resistant to moisture absorption and will reach moisture equilibrium at a lower % than PA6 filaments. Less moisture absorption means that there is less change in mechanical properties from the dry state to the wet state.
Water molecules are attracted from the surrounding air to the polyamide matrix, forming a polar bond onto the polymer chain. This water molecule acts as a plasticizer inside the nylon and while it decreases tensile strength and stiffness, it increases toughness and impact resistance. Unless your 3D printed parts operate in particularly dry environments or are post processed with a moisture barrier, its generally assumed that all nylon printed parts will end up in their wet state properties in every-day use. In many applications the wet state characteristics are more desirable and its common on many nylon injection moulding lines to eject moulded parts straight into a bath of water to condition them to wet state properties before leaving the factory.
In 3D printing filaments must be dry, otherwise, any moisture which is inside the filament will boil inside the hot end and rupture out of the side of the extruded plastic, this greatly decreases the mechanical properties, surface finish, layer bonding and produces some other undesirable printing characteristics such as stringing and oozing. Once the part is printed however, the nylon will absorb moisture from the air naturally and reach an equilibrium inside the part. For PA12-CF, the moisture equilibrium is roughly 1.5% by weight with other brand nylon filaments absorbing up to 5% and over, this has a more drastic effect on the final properties of the part and a noticeable difference in the performance from dry to wet states.
Fig. 3 Moisture Absorption Curve
As PolyMide™ PA12-CF displays a smaller shift in characteristics from dry to wet states it therefore delivers more predictable results in real-world applications. This allows you to design more accurately according to stress models and design loads, allowing you to further optimize your 3D printed parts.
Furthermore, the printability of the filament is also increased as the handling, storing, and printing of the material benefit from less moisture absorption. The filament is still hygroscopic, and we advise storing and printing PolyMide™ PA12-CF from inside the PolyBox™.
Fig. 4 Pipe Assembly Tool
Our material scientists have employed two Polymaker technologies into PolyMide™ PA12-CF. Warp-Free™ Technology, ensures no warping during printing, which is achieved by controlling the crystallisation behaviour of the polymer chains. Fiber-Adhesion™ Technology optimises the surface chemistry of the carbon fibers so they bond homogenously within the polymer matrix. This provides a greater strength on the z-axis when compared to competitor filaments whilst also offering easier printing on a multitude of 3D printers, desktop and industrial.
PolyMide™ PA12-CF features a heat deflection temperature of 131°C lending itself to operate in demanding environments where heat and stress are critical design factors. Paired with superior tensile strength and stiffness compared to other extrusion-based filaments, PolyMide™ PA12-CF is an engineering plastic that can outperform many other extrusion-based materials where strength to weight ratios are critical.
PolyTerra™ PLA is a bioplastic 3D printing filament designed from the ground up to create the next generation of environmentally friendly filaments. Polymaker has combined organic minerals with PLA which significantly reduces the plastic content producing a more environmentally friendly 3D printing material.
PolyTerra™ PLA prints exactly like PLA so you won’t have to change any print settings and the overhang and bridging capabilities can even surpass PLA. Featuring a wide printing temperature range of 190-230°C, PolyTerra™ PLA can plug and play on any extrusion-based 3D printers. The surface finish of 3D printed parts is uniquely matte which hides the layer lines, even when printing with large layer heights.
Polymaker has introduced four pastel colours alongside the ten regular colors which are all inspired by nature, offering a large choice of unique colors with a beautiful surface finish that’s bespoke to PolyTerra™ PLA.
The mechanical properties of PolyTerra™ PLA offer a wide range of potential applications as the material is tougher than regular PLA whilst still maintaining good stiffness similar to PolyMax™ PLA. This allows you to print anything from figurines to fixtures as the extra toughness that’s built into PolyTerra™ PLA does not affect the effortless printing capabilities.
PolyTerra™ PLA features easy support removal and 9 times out of 10 the support can be removed easily by hand without the use of tools. The support performs very well directly printing onto the build platform and also building from model. This allows users to push the boundaries of their machines and create ever more complex parts that are functional, tough and matte.
Post processing PolyTerra™ PLA is easy and the surface can be sanded without the plastic rolling over into long beads or chewing up. Printed parts can be sanded quickly and thanks to the softer surface power sanders can be used to quickly clean up and smooth large prints. The open pores on the surface allow paints to hold a strong bond onto the surface and due to the inert nature of the compound a wide range of paints can be applied.
PolyTerra™ PLA is wound on a fully recycled cardboard spool with recycled labels and outer packaging. The product information sheet has moved online, and any unnecessary paper has been removed from the packaging to cut down on waste.
To offset the carbon created to make and ship a spool of PolyTerra™ PLA, Polymaker will plant one tree for every spool sold, local to the place of purchase in partnership with OneTreePlanted.org. Once the tree hits maturity it has the ability to suck in 22kg of carbon dioxide each year massively offsetting the 4kg required to create a spool of PolyTerra™ PLA.
Teton’s Smart Slice is an integrated finite element analysis (FEA) simulation which allows users to verify the strength and stiffness of their 3D printed parts from inside the slicer. With this data the cloud-based engine can optimise the way the model is sliced to achieve the desired characteristics for the application. This technology has the ability to decrease printing time and material use creating lightweight printed parts that aren’t over engineered, saving time and money.
To validate their simulation system Teton must compare their FEA data against real 3D printed parts to demonstrate that yield loads, safety factors, and deflections are accurately simulated. (Read full white paper here)
The convenience of having FEA simulation integrated into the slicer is a vital step for 3D printing functional parts and integrating FFF technology into product manufacturing. When reliable data is paired with an engineering filament such as PolyMide™ CoPA the technology becomes extremely powerful for proving concepts and design iterations with minimal investment. This is further paving the way for integration of FFF parts in a variety of different manufacturing sectors.
In this demonstration Teton created a roof rack fixture printed in PolyMide™ CoPA. The simulation results can be compared to real data from their testing rig to accurately predict the trends in stiffness and strength in a part sliced and printed in three different ways. The technology requires inputs from the user such as directional forces and load points which are then sent to the cloud for g-code optimisation. With several variables available to the user the part can be tweaked to create the most efficient workflow. The result is a g-code which has all the necessary strength and stiffness with built in safety factors.
A load case was defined in Smart Slice that was based on the experimental test fixture and load application. The flat surfaces on the bottom of part and the 4 bottom holes were set as anchor surfaces (fixed in space) and a load of 2,500 N (Newtons) was applied to the top surface. Using the Validate feature in Smart Slice, the part stiffness and yield load values were computed and are shown in Table 1.
Table 1. Part stiffness and yield loads computed by Smart Slice for 20% infill and solid parts.
These results are compared to the real data from the printed parts. Smart Slice was also used to evaluate the performance of a generic ABS material in order to compare it to the performance of PolyMide™ CoPA. It is clear that PolyMide™ CoPA outperforms ABS in both stiffness and strength. For example, in order to get the same performance as the optimized part printed with PolyMide™ CoPA, a solid ABS part is required. This is important since the optimized part will print in less time and be lighter compared to the solid part. This demonstrates how Smart Slice can be used to evaluate different materials prior to printing so that the material itself can be optimized prior to printing any parts.
The Optimize feature in Smart Slice was used to automatically optimize the print settings based on user-defined performance requirements. These requirements effectively define the strength and stiffness targets for the part. The optimization algorithm explores the full design space of the major print settings and finds solutions that meet or exceed the performance. The algorithm realizes the areas of the part which require higher stress and creates modifier meshes which change the settings in these specific areas. This provides a higher infill and greater number of perimeters to strengthen only in the necessary areas of the 3D printed part.
This case study demonstrates the usefulness of Smart Slice in a 3D printing workflow. The Optimize feature was shown to automatically find a print configuration that minimizes print time and part mass while meeting stiffness and strength requirements. It was also shown how the Validate feature can be used to find the best material for a given application. In this study a high-performance material, Polymaker PolyMide™ CoPA, was shown to provide superior stiffness and strength compared to an ABS material.
Polymaker introduces two new flexible filaments to the PolyFlex™ family offering faster printing and more flexibility. With the surge of 3D printed personal protective equipment (PPE) last year, flexibles proved themselves as a vital tool in the additive repertoire. 3D printing as a production tool demonstrated its potential by manufacturing locally when existing supply chains were constrained. Flexible filaments were a key player in this space and the 3D printed flexible face mask extender was invented to help medical stuff relieve strain on their ears. However, the printability and printing speed for flexibles remains limited, a factor which is determined by the melt index of the filament. Polymaker has developed these two new materials in partnership with Covestro to help boost the productivity of flexibles in the additive workflow.
PolyFlex™ TPU95-HF, is a High Flow (HF) TPU created from Covestro’s Addigy®️ family. The flow rate of flexible materials has always lagged far behind rigid materials which has been the limiting factor effecting the printing speed. TPU95-HF has a melt index of 9.3 (g/10min at 185°C) which is even higher than regular PLA. This allows for double the printing speed compared to other flexible filaments. TPU95-HF is designed specifically for high speed printing, combined with excellent UV resistance, PolyFlex™ TPU95-HF unlocks new applications for flexible materials in manufacturing.
The increased melt index allows the material to print faster. Contrarily to other TPUs on the market, TPU95-HF does not require a high temperature for high speed printing which results in better cooling, improved surface quality, steeper overhangs and finer details. PolyFlex™ TPU95-HF is available in black and white.
Ultraviolet (UV) light is a damaging factor for plastics and long exposure changes the properties of the material often leading to brittle, weak, and discolored parts. All plastics which operate outdoors are therefore at risk which is usually mitigated by post processing parts with a protective coating. The color difference of PolyFlex™ TPU95-HF is imperceptible after being exposed to fluorescent UV after 72 hours under ISO 4892-2 weathering test standard.
PolyFlex™ TPU90, created from Covestro’s Addigy®️ family, is a thermoplastic polyurethane (TPU) based filament designed to provide a high degree of flexibility without compromising on printing ability. Displaying a high resistance to ultra-violet (UV) light, this filament is perfectly suited to demanding applications in a variety of environments.
The shore hardness of this new TPU is 90A and the elongation of break of it is 638.8% ± 15.5. This delivers printed parts with incredible toughness that can stretch over 6 times before breaking. Displaying more ductility than PolyFlex™ TPU95 (shore hardness 95A) while maintaining the same printability thanks to an improved melt index. Its UV resistance opens the door to exterior applications where flexibility and durability are required. PolyFlex™ TPU90 is available in black, white, grey, and teal.
The 2 new TPU products are now available from Polymaker resellers, Polymaker website, and on Amazon (US).
Tips for using Polymaker TPU products:
Bed surface:
The PolyFlex™ family can be printed on glass, buildtak or similar products, PEI sheet or painters tape. Using Magigoo Pro Flex can improve the adhesion of PolyFlex™ TPU95-HF on the printing surface.
Direct and indirect drive extruders
Usually it is recommended to use direct drive printers to print TPU, however the high flow properties of PolyFlex™ TPU95-HF allows the material to achieve high printing speed even on indirect drive printer.
Dry box system
TPU is susceptible to absorbing moisture from the air which can subsequently affect the quality and mechanical properties of the final prints. We recommend using PolyBox™ to prevent moisture absorption. If the filament has absorbed moisture it can be dried at 70˚C for 12 hours in a convection oven.
What is a TDS?
a Technical Data Sheet (TDS) summarizes the performance and technical properties of a 3D printing material delivered through a series of standardized tests. This allows users to choose certain characteristics specific to their application when choosing the right 3D printing material. With the advancement of Polymaker’s industrial range, the TDS plays an integral role in highlighting each product’s varying characteristics and additionally, supplies the end-user with the basic print settings and tips to begin developing print profiles.
All TDS tests are conducted with 3D printed specimens in the X-Y and Z axis and depending on the characteristics of the material, specific tests and environments are used. This provides our end-users with the most accurate and appropriate information for their 3D printing application.
Why does Polymaker introduce a new version TDS?
Polymaker's products are increasingly being used in professional and demanding applications. Knowing what to expect from a material is critical to a parts performance and can aid in the behavioral analysis and curation of 3D printed parts in end use applications. We want to build on the information already found in our TDS and provide more in-depth technical parameters for our customers.
What’s new?
- Moisture Absorption Curve
The moisture absorption curve is determined by the nature of the material itself with some materials more susceptible to moisture ingress than others. The problem of moisture absorption will not only affect the 3D printing process, but also is affecting the properties of a 3D printed part after printing.
If a filament has absorbed moisture, when reaching a heated nozzle, the moisture heats up and rapidly expands rupturing the filament, causing bubbles and inconsistent extrusion. This can significantly reduce mechanical properties and layer adhesion causing print defects such as oozing, stringing and poor surface quality.
In order to solve this problem, Polymaker completely dries all products before vacuum sealing them in an aluminum foil bag with a desiccant. Polymaker also offers the PolyBox™ as a storage solution for all filaments during storage and printing.
To help users to understand how filaments absorb moisture, Polymaker has added the Moisture Absorption Curve into the new version TDS.
In the Moisture Absorption Cure, you can learn how a filament absorbs moisture under the standardized testing condition of 70% relative humidity at 23℃。
- Heat Deflection Temperature (HDT) Curve
There are different ways to illustrate the concept of “Heat Resistance”. Polymaker used to provide glass transition temperature, melting temperature, crystallization temperature, decomposition temperature, and Vicat softening temperature in the TDS. Now Polymaker has added heat deflection temperature (HDT) to further the understanding of heat resistance in a 3D printed part.
The heat deflection temperature is the measure of the temperature at which a polymer undergoes a certain amount of deformation under a constant load. The test is conducted by placing a 3D printed specimen under a constant load, while steadily increasing the temperature by 2 °C/min. The displacement is measured over a range of 10mm and plotted to create the HDT curve.
The heat deflection temperature is determined by the following test procedure outlined in ISO 75. The test specimen is loaded in three-point bending rig in the edgewise direction. The outer fiber stress used for testing is either 0.455 MPa or 1.82 MPa, and the temperature is increased at 2 °C/min until the specimen deflects 0.34 mm. This is similar to the test procedure defined in the ISO 75 standard.
Whilst comparable to HDT, the Vicat softening temperature differs by providing a testing method that simulates the point at which temperature softens the material’s physical properties enough for an external object under a set pressure to penetrate the outside surface of the specimen by 1mm.
What else?
Aside from Moisture Absorption Curve and Heat Deflection Temperature (HDT) Curve, Polymaker will also add light transmission, flame retardancy, chemical resistance, thermal conductivity, and heat shrinkage rage into future versions of the TDS.
Where to find the new version TDS?
You can find the new version TDS from the DOWNLOAD section of Polymaker website.
Polycarbonate (PC) materials specifically designed for industrial 3D printers with a heated chamber
New materials bring strong mechanical and thermal properties to METHOD X 3D printer for a wide range of engineering applications.
BROOKLYN, N.Y., Sept. 17, 2020 – MakerBot, a global leader in 3D printing and subsidiary of Stratasys Ltd. (Nasdaq: SSYS), today announces that Polymaker, a leading provider of 3D printing materials, has qualified three polycarbonate materials for MakerBot LABS™ for the MakerBot METHOD X™ 3D printer.
Polymaker™ PC-PBT, PolyMax™ PC-FR, and PolyLite™ PC are available to print on the METHOD X 3D printer with the MakerBot LABS Experimental Extruder. This extruder turns METHOD into an open materials platform, enabling users to print with a wide variety of third-party materials on an industrial 3D printing platform. The latest material additions from Polymaker to the LABS portfolio aim to enable METHOD X users to harness the strong mechanical and thermal properties of polycarbonate (PC), while reducing problems such as warping and curling that typically occur when used with conventional desktop 3D printing machines.
Polycarbonate is a popular high-performance engineering material that possesses a unique balance of toughness, good light transmission, high heat resistance, and excellent electrical resistance. It is lightweight, has the ability to transmit light as effectively as glass, and withstand impacts better than other thermoplastics such as ABS. Due to these properties, PC materials are commonly used for functional prototyping and end-use parts in the production of automotive components, protective gear, medical device components, and exterior lighting fixtures.
However, polycarbonate can be challenging to print due to its ability to contract if it is cooled too quickly, which can cause warping and shrinkage of the printed part. Controlling the ambient temperature, such as with a heated chamber, is one of the most critical factors when printing polycarbonate.
The MakerBot METHOD X 3D printer is the only printer in its price class with a heated chamber that reaches up to 110°C, letting the parts cool down gradually to minimize curling and warping. METHOD controls how fast a part cools down during the printing process, allowing it to print polycarbonate and other advanced materials more successfully than typical desktop 3D printers that only have a heated build plate. In addition, with the moisture sensitivity of PC materials, Polymaker recommends using a material caddy, such as the Polymaker PolyBox™, to safeguard them from precipitation in the environment. MakerBot METHOD™ users can also use the Material Drying mode on the METHOD X to remove moisture from the materials.
"Polycarbonate is often the choice for parts that function in demanding applications. Its mechanical properties, flame retardance, and chemical resistance also allow engineers to push the boundaries of their 3D printed parts and experiment with new geometries,” said Xiaofan Luo, PhD, President of Polymaker. “Anyone who is serious about printing polycarbonate knows that a heated chamber is essential for printing large and strong complex parts. METHOD is bringing industrial capabilities to a desktop machine, and we think its users will really benefit from the material properties our PC range offers.”
“With its up to 110°C heated chamber, METHOD is a powerful and unique 3D printer platform for printing advanced engineering materials. The availability of Polymaker’s PC materials on METHOD offers allows engineers to print polycarbonate parts that they previously had to outsource to more expensive industrial 3D printers,” said Johan-Till Broer, VP of Product Development, MakerBot. “We are seeing increased interest in industrial materials as engineers advance from simple prototyping to 3D printing end-use parts. We are thrilled that Polymaker has qualified its industrial range of PC materials for MakerBot LABS.”
The addition of Polymaker polycarbonate materials brings the MakerBot LABS for METHOD portfolio of materials to nine and the total number of materials available on the METHOD platform to 19. The newly qualified polycarbonate materials from Polymaker include:
• Polymaker PC-PBT: This polymer blend combines the good chemical resistance of PBT (polybutylene terephthalate) with the strength and toughness of polycarbonate. Compared to PC resins and PC-ABS compounds, PC-PBT offers better resistance to chemicals, which enables printed applications where resistance to intermittent contact with fuels, oils, lubricants, or cleaners is necessary. It performs well under extreme circumstances, whether in contact with hydrocarbon-based chemicals or operating at subzero temperatures. Polymaker PC-PBT is a specialty material that maintains good toughness and natural ductile fracture behavior at low temperatures.
• PolyMax PC-FR: A flame retardant (FR) polycarbonate material, PolyMax PC-FR meets the UL-94 V0 standard, an important fire safety specification. The material displays excellent toughness, strength, and heat resistance, making it ideal for applications within the automotive, railway, and aerospace industries.
• PolyLite PC: PolyLite PC is produced using a polycarbonate resin specifically engineered for 3D printing. This material demonstrates a high modulus, making it ideal for applications that require good stiffness and light diffusion, such as outdoor light housings. PolyLite PC is available in transparent color, showing good optical clarity, rendering parts with an attractive crystal shine.
To further strengthen PC parts, Polymaker recommends annealing them right after the printing process to release the residual internal stress. The combination of METHOD’s heated chamber and annealing feature is designed to enable users to produce strong, manufacturing-grade parts. Polymaker materials can be purchased on the Polymaker site.
The MakerBot LABS extruder enables users to print with a wide variety of third-party materials on METHOD as an open materials platform, expanding the possibilities of applications. MakerBot offers a wide range of industrial materials through MakerBot LABS, and is continuing to identify additional advanced materials for the platform. Partners in the MakerBot LABS Materials Development Program include BASF 3D Printing Solutions, Jabil, Kimya, LEHVOSS Group, Mitsubishi Chemical, and Polymaker.
For more information, visit www.makerbot.com/method.
Polymaker is now offering PolyMax™ PLA GREY on a 3kg spool. You can find it from Polymaker’s resellers, Polymaker website, and also Amazon.
PolyMax™ PLA is produced with Polymaker’s patented Nano-reinforcement technology creating a filament that is much tougher than regular PLA while still keeping all the inherent printing qualities. Paired with Jam-Free™ technology, this material offers high strength parts that print perfectly on desktop printers. Engineers worldwide are already producing functional prototypes and working parts with PolyMax™ PLA.
The 3kg net weight enables continuous 3D printing without the need to change filament on large projects.
Grey now joins Black and White in the 3kg spool offering for PolyMax™ PLA.
Polymaker has launched 20 kinds of 3D printing filaments. In order to make it more convenient for customers to try out Polymaker's materials, Polymaker launched three Sample Boxes (click to see more information) last year and received good responses from customers.
In the 2nd half of last year, Polymaker launched three polycarbonate materials. To make it easier for users to test them, Polymaker now officially introduces Sample Box 4 to the market.
The Sample Box 4 contains 5*50g samples(in 1.75mm or 2.85mm): PolyLite™ PC, PolyMax™ PC, PolyMax™ PC-FR, Polymaker™ PC-ABS, and Polymaker™ PC-PBT. It also includes a Magigoo PC sample. These samples require a 3D printer with enclosure for better part performance.
PolyLite™ PC
PolyLite™ PC is produced using a polycarbonate resin specifically engineered for 3D printing. It delivers good stiffness and heat resistance with light-diffusing properties.
PolyMax™ PC
PolyMax™ PC is an engineered PC filament combining excellent strength, toughness, heat resistance and printing quality. It is the ideal choice for a wide range of engineering applications.
PolyMax™ PC-FR
PolyMax™ PC-FR is a flame-retardant PC filament (UL94V-0/1.5 mm) displaying excellent toughness, strength, and heat resistance. This filament opens new applications in the automotive, railway and aerospace industries.
Polymaker™ PC-ABS
Polymaker™ PC-ABS is a PC/ABS polymer blend which offers excellent toughness and heat resistance while displaying good surface finish and good compatibility with metal plating.
Polymaker™ PC-PBT
Polymaker™ PC-PBT is a PC/PBT polymer blend which offers good heat resistance and toughness at low temperature (-20˚C/-30˚C). Polymaker™ PC-PBT also features good chemical resistance.
Magigoo PC
Magigoo is an easy to use 3D printing adhesive designed to reduce warping in FDM/FFF 3D printers. This is MagigooPC, the adhesive specifically designed for 3D printing in polycarbonate plastics. It offers a strong adhesion platform for polycarbonate-based filaments.
Sample Box 4 is now available in both 1.75mm and 2.85 on www.polymaker.com .Click the GET A SAMPLE button on the product page and Polymaker Amazon shop to try the materials.
Back in November 2013, Polymaker installed its first dedicated production line and developed a flexible 3D printing filament as the few flexible filaments available at the time had poor compatibility with different 3D printers. Polymaker fine-tuned the plasticity of the thermoplastic to produce a filament that was easy to print while producing soft and flexible printed parts. PolyFlex™ TPU95 marked the third product to join the growing Polymaker portfolio.
PolyFlex™ TPU95 is a thermoplastic polyurethane (TPU) based filament specifically engineered to work on most desktop 3D printers. It has a shore hardness of 95A and can stretch more than 3 times its original length.
Recently, we have seen a rapid increase in demand for flexible 3D printing materials used for various applications. In order to respond to market demand, Polymaker decided to launch two new colors of PolyFlex™ TPU95: BLUE & RED.
They are now available on www.polymaker.com and Amazon with both 1.75mm & 2.85mm diameters.
Versatile materials for 3D printing
Polymaker, market leader in advanced 3D printing materials, announced the launch of three new polycarbonate-based 3D printing materials each with unique properties commonly used in the automotive industry. Polymaker has partnered with Covestro to bring these new materials to market taking formulas that are already well known to industry professionals and optimizing them for 3D printing.
The three new materials consist of:
- Polymaker™ PC-ABS – a blend of already commonly used 3D printing materials, polycarbonate and ABS. The advantages of this blend are high impact and heat resistantancy and easy to process. The polycarbonate boosts the heat resistance and toughness of the material while the ABS contributes to the good processing properties. This PC-ABS is also specialized for surface finishings, i.e. by electroplating and metallization, providing a good apporach for post processing.
Polymaker™ PC-ABS uses Covestro’s Bayblend® family as its base material which is a commonly used plastic in the automotive and information technology industry today.
- Polymaker™ PC-PBT – This polymer blend combines the good chemical resistance of PBT with the strength and toughness of polycarbonate. Polymaker™ PC-PBT performs very well under extreme circumstances whether in contact with hydrocarbon-based chemicals or operating at subzero temperatures. Polymaker™ PC-PBT maintains good toughness and its natural ductile fracture behavior at low temperatures.
Polymaker™ PC-PBT is created from Covestro’s Makroblend® family which is widely used in various industries. Compared to PC resins and PC-ABS compounds, PC-PBT has better resistance to chemicals, which enables printed applications where resistance to intermittent contact with fuels, oils, lubricants, cleaners is necessary.
- PolyMax™ PC-FR – creation from Covestro’s Makrolon® family, where the FR stands for flame retardant - the main feature of this polycarbonate-based compound. This base material achieves V0 performance in the UL94 flame retardancy test and benefits applications where respective material approval is required. This allows PolyMax™ PC-FR to be applied for battery housings, motor mounts in aerospace and other industries. Within the automotive and Electronics & Electrical industry, many professionals are well accustomed with such FR materials.
Polymaker has introduced its nano reinforcement technology that is featured in all PolyMax™ materials. This boosts the fracture toughness of the FR material and produces a flame-retardant filament that can still perform in demanding applications. PolyMax™ PC-FR uses Covestro’s Makrolon® showing a good balance between mechanical performance and safety, which has already been applied in electronic motorbikes, aerospace spare parts, and automotive production.
Polymaker boasts an ever-growing portfolio of cutting edge materials, with 17 unique products covering all your 3D printing needs. The Polymaker team wants to offer a convenient and cost-effective way for its customers to try and experience all of the different materials. These sample boxes allow users can find the most suitable filament for their application while also discovering new 3D printing materials.
Polymaker introduces Sample Box 1, Sample Box 2 and Sample Box 3 to the market.
Sample Box 1
Sample Box 1 contains 7 kinds of commonly used 3D printing filaments with each sample weighing 50g. All materials in Sample Box 1 are easy to use and are compatible with many 3D printers.
PolyLite™ PLA
PolyLite™ PLA is a high-quality PLA designed for reliability and ease of printing.
PolyLite™ PETG
PolyLite™ PETG is an affordable PETG filament with balanced mechanical properties and ease of printing.
PolyMax™ PLA
PolyMax™ PLA is an incredibly easy-to-print filament with improved mechanical properties, making it an excellent alternative to ABS.
PolyMax™ PETG
PolyMax™ PETG offers better mechanical properties than any other regular PETG making it a good candidate for a wide range of applications.
PolyFlex™ TPU95
PolyFlex™ TPU95 is a thermoplastic polyurethane (TPU) based filament specifically engineered to work on most desktop 3D printers. It has a shore hardness of 95A and can stretch more than 3 times its original length.
PolyWood™
PolyWood™ is a wood mimic filament without actual wood powder, which removes all risks of nozzle clogs. PolyWood™ is made entirely with PLA using a special foaming technology. It exhibits the same density and appearance as wood.
PolySmooth™
PolySmooth™ is a unique, easy-to-print filament designed for hands-free post processing. The surface can be smoothed with alcohol to achieve layer free models using the Polysher™.
Sample Box 2
Sample Box 2 contains 7 kinds of engineering 3D printing and supporting material, each weighing 50g. These products display better overall mechanical strength and thermal properties than the materials featured in Sample Box 1. Theses samples require a 3D printer with an enclosure or with dual extrusion capabilities.
PolyLite™ ABS
PolyLite™ ABS is made with a specialty bulk-polymerized ABS resin, which has significantly lower volatile content compared to traditional ABS resins. It delivers excellent printing quality with minimal odor during printing.
PolyLite™ ASA
PolyLite™ ASA is an alternative to ABS with improved weather resistance. Its UV resistance and excellent mechanical properties make it the perfect choice for real-life applications.
PolyLite™ PC
PolyLite™ PC is produced using a polycarbonate resin specifically engineered for 3D printing. It delivers good stiffness and heat resistance with light-diffusing properties.
PolyMax™ PC
PolyMax™ PC is an engineered PC filament combining excellent strength, toughness, heat resistance and printing quality. It is the ideal choice for a wide range of engineering applications.
PolyMide™ CoPA
PolyMide™ CoPA is based on a copolymer of Nylon 6 and Nylon 6,6. The filament combines excellent strength, toughness, and heat resistance of up to 180˚C.
PolyDissolve™ S1
PolyDissolve™ S1 is a water dissolvable support for PLA, TPU, PVB and Nylon based filaments from our portfolio. It is specifically engineered to have a perfect interface with these materials while also displaying good solubility.
PolySupport™
PolySupport™ is a breakaway support for Polymaker PLA based filaments. It has a perfect interface with PLA, strong enough to support it and easily removable by hand.
Sample Box 3
Sample Box 3 contains the first two Polymaker Industrial Range products – PolyMide™ PA6-CF and PolyMide™ PA6-GF, and each of them weighs 100g. The industrial range uses cutting-edge technologies to provide reliable, high-quality materials specially engineered for 3D printing in the industrial sector. These samples require a 3D printer capable of reaching a nozzle temperature of 300˚C and equipped with an abrasion resistant nozzle.
PolyMide™ PA6-CF
PolyMide™ PA6-CF is a carbon fiber reinforced PA6 (Nylon 6) filament. The carbon fiber reinforcement provides significantly improved stiffness, strength and heat resistance with outstanding layer adhesion.
PolyMide™ PA6-GF
PolyMide™ PA6-GF is a glass fiber reinforced PA6 (Nylon 6) filament. The material exhibits excellent thermal and mechanical properties without sacrificing the layer adhesion.
Now Sample Box 1, Sample Box 2 and Sample Box 3 are available in both 1.75mm and 2.85 on www.polymaker.com click the GET A SAMPLE button on any filament product page and Polymaker Amazon shop to try the materials.
Introducing PolyMide™ PA6-CF & PolyMide™ PA6-GF
Polymaker launch two new industrial materials to the 3D printing market offering the best in class for mechanical properties achievable from extrusion-based 3D printing. The two new materials are both fiber reinforced Nylon polymers that display, incredible strength and high heat deflection temperatures. This allows these new materials to function in more demanding environments and allows 3D printing to produce more practical functional parts. Both these materials feature Polymaker's latest development - Fiber Adhesion™ technology, boosting the layer adhesion of printed parts not only on the x-y axis but also on the z-axis.
PolyMide™ PA6-CF
PolyMide™ PA6-CF is a carbon fiber reinforced nylon (PA6) 3D printing material offering the highest strength, impact resistance and heat deflection of all Polymaker 3D printing materials. The carbon fiber reinforcement provides significantly improved stiffness, strength and heat resistance without affecting z-axis layer adhesion. Featuring a heat deflection temperature of 215°C, this material lends itself perfectly to functioning automotive applications where strength and heat resistance are required from the material.
PolyMide™ PA6-GF
PolyMide™ PA6-GF is a glass fiber reinforced Nylon (PA6) that offers outstanding mechanical properties, namely, impact strength and stiffness. The material exhibits excellent thermal and mechanical properties without sacrificing the layer adhesion. PolyMide™ PA6-GF can be used to print parts working in a wide temperature range and has been utilized to create custom lab equipment working at temperatures as low as -190°C.
Fiber Adhesion Technology™
Fiber Adhesion™ Technology improves the layer adhesion of fiber reinforced materials, by optimizing the surface chemistry of the fibers to achieve better dispersion and bonding to the polyamide matrix. This results in better strength along the Z-axis and reduced mechanical anisotropy when compared to a pure Nylon PA6 printed parts. This in-house technology was developed exclusively to combat the problem of adding fibers to filaments. All other brand fiber reinforced materials show a decrease in z-axis layer adhesion when compared with their non-fiber reinforced Nylons producing a part that is only stronger on the X-Y axis but detrimental to the Z axis. Polymaker's new technology not only solves this problem but actually increases Z axis tensile strength creating more isotropic parts that are strong in every direction.
Polymaker announces the worldwide launch of PolyLite™ ASA, the fifth member of the PolyLite™ family rounding up the most popular 3D printing materials available today.
What is ASA?
ASA (Acrylonitrile Styrene Acrylate) is a thermoplastic with properties similar to ABS (Acrylonitrile Butadiene Styrene), which you might be able to guess from their full names as they share two monomers. ASA features good mechanical strength and thermal properties, but its outstanding feature is its weather resistance, which makes it an ideal candidate for outdoor-use. As a 3D printing material, ASA has already become a popular choice for automotive prototypes, in construction, and household applications. Now Polymaker has made it widely available for users to print parts that can withstand the elements.
About PolyLite™ ASA
PolyLite™ ASA is similar to ABS but with improved weather resistance. Its UV resistance and excellent mechanical properties make it the perfect choice for real-life applications or parts that will spend time outdoors. Weather resistance can be broken down into 3 factors: UV resistance, water resistance and thermal stability of which ASA outperforms many other plastics.
Key features:
- Good thermal and mechanical properties:
To break it down, PolyLite™ ASA performs better in both thermal and mechanical properties compared with general ABS filaments. It also features a Vicat softening temperature of 105℃ which slightly exceeds ABS.
- UV resistant
Most plastics tend to become brittle and their color turns yellow when exposed to UV radiation or sunshine. 3D prints of PolyLite™ ASA are UV resistant meaning their appearance and mechanical properties are not influenced negatively by UV light.
- Water resistant
PolyLite™ ASA is resistant to Environmental Stress Cracking. This allows printed parts to face the outdoors, high humidity and rain over long periods of time.
Advantages:
Polymaker developed and produced the 3D printing material for the world largest 3D printed pedestrian footbridge project completed by Shanghai Construction Group. Polymaker was invited to join this project from the very beginning to help develop a custom ASA 3D printing material for the bridge. During the whole processes, through plenty of tests and experiments, Polymaker has mastered the properties, compounding formulas and production techniques of ASA. As a result, PolyLite™ ASA gains several advantages over other ASA filaments:
- Tougher
PolyLite™ ASA has better mechanical properties and is tougher than other brand ASA filaments. (More information on the technical data sheet below)
- Better flow
PolyLite™ ASA is engineered to have the best in class melt index, PolyLite™ ASA filament can be extruded smoothly and easily.
- Better layer adhesion
With experience gained from the 3D printed bridge, our engineers have developed an ASA filament with exceptional interlayer adhesion. PolyLite™ ASA displays better layer-bonding performance than similar products.
Printing tips:
- Building platform surface
Similar to ABS, PolyLite™ ASA tends to warp during printing. To ensure the success of printing, we recommend using BuildTak® or Magigoo on the build surface.
- Turn off the cooling fan
Deactivating the cooling fan will reduce warping and delamination.
- Build an enclosure for your printer
A printing enclosure will help retain heat for large prints increasing the performance of the final parts.
Availability
PolyLite™ ASA is now available in both 1.75mm and 2.85mm in White and Black. You can find it on polymaker.com, Amazon, and through our Polymaker resellers.
PolyLite™ ASA Technical Data Sheet
Layer-Free™ technology, developed by Polymaker was first introduced on their breakthrough PolySmooth™ 3D printing filament which offered users the chance to remove all layer lines from their 3D printed parts via an easy post process. This development allowed PolySmooth™ parts to achieve a finish that is usually void from 3D printed parts and is something that is more commonly seen from traditional injection molding processes. The technology was later used to create an award-winning material which has revolutionized the investment casting industry.
Plastic parts have been around a long time before 3D printing technology was developed and the surface finish has largely been the same, smooth, glossy surfaces that were soft to touch and appealing to the eye. Plastic parts were made this way to aid the manufacturing process, as smooth parts would eject from injection molds much easier as the surface friction is minimized between the plastic part and the steel mold. This enabled a faster production of plastic parts with higher repeatability, and so it became the normalized process for injection molding and standardized surface finish for all plastic parts. This, in turn, shaped the public perspective of what they know as a plastic part, an object that is inherently smooth and glossy object as this was the standard finish for almost all of the plastic parts they have ever encountered.
The introduction of 3D printing changed the way in which plastic parts could be manufactured allowing plastic parts with new geometries that could not be achieved by injection molding. The process of printing vs injection molding is also widely different in the process. 3D printing split computer-aided designs into individual layers and printed each layer on a 2D plane which together formed a 3D object. This naturally changed the surface finish of plastic parts as many layers fused together created a horizontal texture which was not as smooth as the steel injection molds that had been used previously. The surface finish of a 3D printed part greatly depends on the layer height in which it was printed. Smaller layer heights create more detail as more 2D layers can be squeezed into a smaller space and larger layers iron out details as less texture can be dedicated to the shape. With a small enough layer height, a 3D printed part could be printed in a way that made it feel smooth to touch, however, the layer lines are hard to hide from the human eye as the light would reflect differently from the high and low points of the layers obviously setting apart a 3D printed object from an injection molded object. Printing at very small layer heights can create a smoother finish but it also drastically increases the print time as every layer added further increases the path that the extruder must follow. This means to achieve the same feeling as an injection molded part a 3D part would take a very long time to manufacture which is naturally inefficient to production.
3D prints can also be post-processed by sanding the layers until the high points of the layers match the low point and a smooth plastic is revealed underneath. This could then, in turn, be painted or lacquered to achieve a glossy finish achieving the aesthetic look of an injection molded part. This would recreate the image of plastic parts as consumers knew them, but the problems faced are that is it unfeasible to manufacture with such an intense workload in the post-processing of plastic parts.
Polymaker set out to create a technology which could eliminate all layer lines from a 3D printed object while also being a hands-free process requiring no extra work or man hours. The process developed was named Layer-Free™ technology and was applied to their PolySmooth™ 3D printing filament. PolySmooth™ is a polyvinyl butyral (PVB) based material which displays excellent solubility in isopropyl alcohol (IPA), this meant that when a 3D printed part is exposed to IPA, the layers could be quickly melted and fused together. The result is a smooth glossy object that looks like an injection molded part. The Polysher™ was created as a desktop device that could deliver IPA to 3D printed parts in a very controlled manner. The Polysher™ uses an ultrasonic nebulizer to create a cold mist of liquid IPA which is contained within a chamber. 3D printed parts made from PolySmooth™ could be lowered into the chamber and exposed to the fog of IPA which would gently melt the surface layers together. Polymaker found that this process was the best way of applying IPA to PolySmooth™ parts as it polished objects quickly but wasn’t too aggressive allowing details on printed object to remain after polishing.
The Polysher™ also allowed for recycling of IPA as all of the mist is contained inside the chamber, this allows it to re-condense and flow back into the reservoir situated at the bottom of the machine. The Polysher™ also has several safety features that allow it to work alongside your printer as a desktop machine. Firstly, the Polysher™ has a raising platform which elevates the polished object out of the IPA fog allowing users the chance to replace the platform and continue polishing. As the IPA fog is heavier than air, all IPA mist sinks to the bottom of the chamber where is can condense into a liquid and return back to the reservoir. This reduces the chance of any IPA mist escaping from the chamber and into your workplace. The Polysher™ also features two warning lights which monitor the seal of the chamber as well as monitoring the nebulizer. These warning lights cease all polishing processes until the issues have been addressed and a new polishing cycle can be started. The chamber seal light monitors the z-axis position of the platform while checking to see if the chamber casing is properly seated ensuring an airtight seal within the chamber. The nebulizer warning light monitors the frequency of oscillations from the nebulizer membrane. From this data, the Polysher™ can determine if there is an issue with the nebulizer such as, no IPA in the reservoir, the nebulizer becoming unseated or an over-heating problem, all of which will cause the nebulizer warning light and cease the polishing cycle.
The Polysher™ features two different lighting applications, one is the main chamber light which can be dimmed or turned off, the other is a nebulizer light which can cycle through 15 different colours to illuminate the IPA mist!
PolySmooth™ can be used in many different applications ranging from prototyping to production ready parts. Thanks to the unique surface that can be achieved once PolySmooth™ prints have been polished it allows designers to give the finishing touch to their prototypes producing a realistic finish that was unachievable before Layer-Free™ technology. Due to the excellent solubility of PolySmooth™ in IPA, it also allows for large parts to be chemically welded together as the IPA can be used as a solvent glue. Painting just three layers of IPA on the surface of PolySmooth™ will allow individual parts to be joined together allowing for colour combinations with hard edges without introducing any foreign bonding materials. Furthermore, the surfaces can then be polished together to create a smooth surface across join lines, this technique leaves a homogenous surface.
The toughness of PolySmooth™ 3D printed parts also increases after the polishing process, as all the exterior layers are bonded together. This fusing of the layers helps 3D printed parts take an impact and also improves their tensile strength. The Z-axis strength is also greatly increased as fractures along the layers are most common in 3D printed parts. Polished parts also are completely watertight which makes PolySmooth™ a great material for any part that will come in contact with water. This can range from useable vases to kitchenware, to medical applications, the smooth surface is also very easy to clean. The many layers in unpolished 3D prints provide lots of surfaces for dirt to get caught and for microbes and bacteria to grow, eliminating the layers greatly reduces the chance of a part becoming moldy when in contact with skin and water.
PolySmooth™ also allows for easy support removal and clean up, the majority of 3D printers currently on the market are single extrusion machines, as a consequence, complex geometries that require support must use the same support material as the build material. In some cases, this can cause issues as the support can leave scarring on the interface surface where the support meets the model. PolySmooth™ can be cleaned away very easily and any scarring that is caused by the support material can be completely removed once the part has been polished.
Laura Jonas is a Czech company creating unique fashion items using PolySmooth™ and the Polysher™ to achieve a finish that is aesthetically pleasing for their jewelry range. Combining glossy plastic parts with materials more traditionally found in jewelry making, Laura Jonas has managed to create a look that is unique and beautiful.
Martin Jonas – Head Designer says “I love working with Polysmooth and the Polysher, I used to spend a lot of time sanding and buffing my 3D prints to get them to the industry standard surface finish. Polysmooth has completely removed this process, now I can print our accessories and get repeatable results in the polysher with no extra effort.”
PolySmooth™ has added a new dimension to the Laura Jonas fashion accessories and is a good example of using 3D printing to create final products.
Polymaker has developed a second material which employs Layer-Free™ technology, this material is a specialized casting material that can replace wax patterns used in the investment casting process. The use of Layer-Free™ technology is combined with Polymaker’s Ash-Free™ technology to create a 3D printing filament that both molds very well and burns away very cleanly. The material is called PolyCast™ and has been engineered directly for the metal casting industry. The process of making metal parts from wax patterns is well established and PolyCast™ fits into the process very nicely without disrupting traditional processes. Instead of injection molding wax patterns which are then used to create a ceramic mold, users can 3D print PolyCast™ patterns replacing the wax while also eliminating any need for tooling or injection molding. Tooling is often the limiting factor when bringing new products to market as it is time-consuming and costly. PolyCast™ allows for faster iteration of design and is not constrained by volume numbers or large minimum order quantities. This major advantage of time and money has seen widespread adoption of PolyCast™ by foundries worldwide, without deviating from their well-established process, they can test new geometries and streamline production by adopting additive manufacturing and PolyCast™.
As previously mentioned PolyCast™ also has Layer-Free™ technology allowing the 3D printed parts to be polished to a smooth glossy surface, this greatly helps the molding process as bubbles can get trapped in between the layers causing defects in the mold which transfer to the metal parts. A typical investment casting process will go as follows. CAD designs are 3D printed using PolyCast™ and then polished inside the Polysher™, they are then attached to a wax tree which can hold multiple parts and consists of sprues and risers which help guide the flow of molten metal. The tree is then dipped in a ceramic slurry which coats all the surfaces of the tree and 3D printed parts. This is then showered with a silica particle which adds thickness and strength to the mold. This process is then repeated until a ceramic shell is built up around the 3D printed parts that is thick enough to withstand the molten metal. The ceramic shell is then fired in a kiln at temperatures of 1200°C, this cures the ceramic to create a very hard and heat resistant shell. It is during this process that the 3D printed patterns are burnt out of the ceramic shells. Ash-Free™ technology typically leaves and an ash residue of 0.003% by weight after burn out. This means that the 3D printed part has been completely vaporized by the high temperatures in the kiln producing a very clean casting surface on the inside of the ceramic mold. The molds are then used to pour molten metal into which solidifies in the pattern of the 3D printed parts. The metal tree is then broken free from the brittle ceramic shell and the individual parts are cut away from the tree which can be recycled. Parts are generally post-processed by a CNC milling machine to achieve the desired tolerances for precise machinery. In some cases, metal parts can be easily cleaned up by hand and are production ready without the need of CNC milling. Having a mold that is completely free of ash is essential to the final quality of the metal part and is the key technology that is employed on PolyCast™, Layer-Free™ technology ensures a bubble-free interface layer on ceramic molds and also sealing all surfaces on the 3D printed part which reduces time in the final post-processing of metal parts.
Layer-Free™ technology has given 3D printed parts that finishing touch taking them into the league of traditionally manufactured plastic objects. With all the other benefits of 3D printing, the ability to create a smooth, glossy surface that's watertight and easy to clean is a major breakthrough for 3D printed parts and they serve as a daily aid to our modern lives. By unlocking new geometrical shapes, Layer-Free™ technology has helped open new doors for investment casing allowing shorter lead times and more customization of metal parts. This, in turn, will benefit many other industries and have a truly global impact as we create ever more efficient machines.
SHANGHAI March 6th – Polymaker, the global leader in 3D printing filaments today announced their partnership with Thought3D, producers of Magigoo 3D printing smart adhesives. Polymaker are now recommending Magigoo by adding their PC Smart Adhesive to polycarbonate product information sheets. PC Smart Adhesive aids bed adhesion and streamlines production workflow when printing with Polycarbonate based materials.
Polycarbonates offer some of the best mechanical characteristics of any 3D printing polymer, particularly when it comes to impact resistance. They have traditionally been popular among the automotive industry, applied in high vibration environments but have also gained traction across many other industries, notably Aerospace, Medical, Robotics and functional prototyping.
Polycarbonates can operate in temperatures well over 100°C but they also require high printing temperatures and warm environments, for larger parts bed adhesion is critical to the success rate of a polycarbonate 3D print. Thought3D have developed a special formula dedicated for polycarbonate bed adhesion. Using their smart adhesion technology, the PC formula adheres to printed parts locking them to the heated bed while also easily releasing at cold temperatures.
“There are other techniques for ensuring a good adhesion for PC parts, however, none of them work as seamlessly as Magigoo. The way in which printed parts release once the bed has cooled down is, for me, the best aspect of this product. For large PC prints, Magigoo will save the heart ache of wrenching away at your 3D printer to retrieve your PC part. Users printing PC regularly will understand the value immediately.” - Luke Taylor, Marketing Manager, Polymaker
In continuation with the Printer Manufacturer Partnership Program (PMPP) announced last year, Polymaker is continuing to deliver on its mission of bringing 3D printing to main-stream manufacturing. Functional and small-scale manufacturing relies on repeatable solutions that are achieved through interplay between machines and materials. Magigoo smart adhesives deliver a hassle-free interface between the printed object and machine raising the production efficiency for professional additive manufacturing.
With more industries adopting 3D printing, the specialisation of material, machine and process has become more focused. Thought3D has formulated new solutions to common sticking and warping problems for large format 3D printers dedicated to industrial plastics like Polypropylene, Polycarbonate and Nylons.
The new specialty mixes bring the convenience to industrial users. Adhesives are easily applied, require no change to the levelling of the 3D printing bed. They stick when hot and provide easy release when cooled down. The big difference a user will notice is the ease of cleaning the layer of Magigoo. In essence, new industrial mixes will provide same or better adhesion than alternatives and provide convenience and reliable use.
“We are really excited to work with Polymaker and their highly professional team. We have spent significant time cross referencing each other’s materials to provide highest value to end users. We love Polymaker filaments and are sure that this collaboration will benefit end-users and strengthen positions of both companies making the offering complete. We hope to provide a solution to any presently used and future filament. It is a win-win-win combination for all.” says Andrei-Andy Linnas, co-founder of Thought3D.
About Polymaker – Polymaker is a company dedicated to developing new and functional materials for the 3D printing industry. Since 2013 Polymaker has developed unique in-house technologies that optimize their materials for 3D printing. In 2017 Polymaker won two major awards: “Material Company of The Year” from 3D Printing Industry and “Technology Innovation Award – Materials” from TCT. This marked the company’s growing reputation which is now widely recognized at a global scale. Headquartered in Shanghai, China, Polymaker also has global offices in the USA, Netherlands and Japan. With their state-of-the-art research and development center, Polymaker place focus on pioneering development of engineering grade materials for applications across many industries.
About Thought3D - Thought3D is a R&D startup based in Malta. In 2014 the company experienced the first layer adhesion problem first hand and came up with a novel smart adhesive, that sticks when hot and releases when cold. Today, Thought3D produces and sells Magigoo and Magigoo PRO adhesives worldwide through a network of resellers and industry partners. Thought3D aims to provide superior user experience in 3D printing by solving the adhesion problem of FDM/FFF filaments.
Extrusion-based 3D printing remains the most accessible 3D printing technology, due to its wide range of material choice and great user community. However, all materials face the same challenge of surface quality as they cannot escape the layers. PolySmooth™ is one unique filament that offers an answer to layered prints and now Polymaker has launched 5 new colors to add to the range!
In April 2016, Polymaker launched a Kickstarter campaign for PolySmooth™ & Polysher™, a desktop post-processing machine to remove all layers from printed parts and a 3D printing filament that can be easily smoothed with isopropyl alcohol. The campaign was a huge success and the goal was reached in just four hours of launching the campaign. Polysher™ & PolySmooth™ still remains the most successful Kickstarter campaign for a 3D printing accessory to date.
PolySmooth™ offers excellent printing quality, balanced mechanical properties, and most importantly, it is engineered for hands-free post-processing. The surface can be smoothed with alcohol to achieve layer free models using the Polysher™. In the meanwhile, the printing setting of PolySmooth™ is designed to be very similar to PLA, which means it is 100% compatible with existing extrusion-based (FDM/FFF) 3D printers and extremely easy to work with.
PolySmooth™ has been available in global markets for over 2 years with 7 unique colors– black, white, coral red, electric blue, slate grey, transparent and Polymaker teal. Once a print has been polished it is transformed into a smooth glossy object giving the printed part the aesthetics of an injection moulded part. This means that the color of the filament is more paramount than a regular color on a different material. Users like to utilize the unique colors of PolySmooth™ to create innovative, interesting, and aesthetic items for various application scenarios. As a result, there are more and more voices asking for new colors.
So, we are now introducing PolySmooth™ 5 new colors to the market: Pink, Yellow, Beige, Green and Orange. They are now available on www.polymaker.com and Amazon with both 1.75mm & 2.85mm diameters.
We look forward to seeing more exciting 3D prints using these new colors!
Polymaker join the Ultimaker Material Alliance Program adding three engineering materials to the Ultimaker Workplace
SHANGHAI, 21st February 2019 – Polymaker, producer of advanced 3D printing materials, today announced during TCT Asia in Shanghai that they will join the Ultimaker Material Alliance Program. Polymaker will add three engineering filaments to the Cura workplace offering Polymaker material solutions to Ultimaker users.
Dr. Xiaofan Luo, President, Polymaker: “FFF 3D printing remains the most practical and accessible one of all 3D printing technologies. The 3 materials we offer via the Ultimaker Marketplace, including PolyMide™ PA6-CF, PolyMide™ CoPA and PolyCast™, are among the most unique and advanced materials in our portfolio. I believe they will open up countless new applications for a greater number of engineers."
In order to accelerate the synergy between 3D printing material and machine, Polymaker have added three advanced materials from their portfolio to the Cura workplace. This will increase the printing quality and repeatability of parts as all print profiles are stored on Cura. Users will simply select the material profile and start a print in a matter of seconds. Polymaker have started by adding PolyMide™ CoPA, PolyCast™ & PolyMide™ PA6-CF to the alliance program introducing 3 unique materials with engineering applications across a number of industries.
Jos Burger, CEO at Ultimaker: “The growing importance of 3D printing gives us—as a leader in desktop 3D printing—an important role in ensuring a perfect collaboration between hardware, software and materials. By offering material profiles directly to millions of end users via the Ultimaker Marketplace, we unlock new 3D printing applications for different industries. Polymaker is a well-respected material company, offering unique material properties that are relevant for engineers working in a wide diversity of industries. I am proud to recognize their commitment to the Ultimaker Material Alliance during TCT ASIA.”
PolyMide™ CoPA
PolyMide™ CoPA is a co-polymer polyamide (Nylon) filament which combines the high heat deflection of Nylon 6.6 with the stiffness and impact toughness of Nylon 6. Together they produce a well-rounded Nylon filament with a heat resistance of 180°C and a high tensile strength and process ability. PolyMide™ CoPA also features Polymaker’s Warp-Free™ technology, which allows the polymers to crystallise extremely slowly allowing any internal stresses that are caused by printing to be relaxed. This produces a nylon filament which prints with near zero warp on an open bed printer. Furthermore, Warp-Free™ technology allows crystals to form across layers producing isotropic strength on the Z-axis. Formerly, nylon filaments have required enclosed heated chambers, high nozzle temperatures and were generally limited to small printed parts. PolyMide™ CoPA with Warp-Free™ technology releases the constraints previously supressing nylon, allowing engineers more freedom in the design and production of functional 3D printed parts.
PolyCast™
PolyCast™ is a unique 3D printing filament designed specifically for investment metal casting. PolyCast™ completely removes any tooling from the traditional investment moulding process, by replacing wax patterns with 3D printed patterns. Using Polymaker’s Ash Free™ technology PolyCast™ prints can be burned away very cleaning, typically leaving an ash residue of 0.003%. This allows for investment moulds to be cast around 3D printed parts which can then in turn be used to create metal parts suitable for production. PolyCast™ allows for rapid design iteration and is unconstrained by large production volumes as the expensive and time-consuming tooling process is eliminated. Furthermore, investment casting foundries are able to test complex geometrical shapes which are unachievable via injection moulding without diverting from their current casting process.
PolyMide™ PA6-CF
PolyMide™ PA6-CF is a nylon 6 filament with carbon fibre reinforcement, displaying high heat deflection paired with superior stiffness and toughness. PolyMide™ PA6-CF is perfect for practical applications involving high vibration environments where toughness and heat deflection are required. Polymaker have optimised the carbon fiber surface chemistry so that the fibers integrate perfectly within the polyamide matrix. This results in not only a greater adhesion between polymer and fiber but translates into a greater layer adhesion between printed layers. This breakthrough technology has not been witnessed before as fibers generally add stiffness only on the X-Y axis while degrading the Z axis strength. PolyMide™ PA6-CF displays an increased inter layer adhesion creating printed parts that are 30% stronger in tensile strength along the Z axis. Polymaker have jumped the final hurdle inhibiting fiber reinforced filaments, furthermore, PolyMide™ PA6-CF actually improves the layer bond on the Z axis. Paired with Warp-Free™ technology, PolyMide™ PA6-CF demonstrates itself as an engineering material with properties that outperform almost every other filament.
About Polymaker
Polymaker is a company dedicated to developing new and functional materials for the 3D printing industry. Since 2013 Polymaker has developed unique in-house technologies that optimize their materials for 3D printing. In 2017 Polymaker won two major awards: “Material Company of The Year” from 3D Printing Industry and “Technology Innovation Award – Materials” from TCT. This marked the company’s growing reputation which is now widely recognized at a global scale. Headquartered in Shanghai, China, Polymaker also has global offices in the USA, Netherlands and Japan. With their state-of-the-art research and development center, Polymaker place focus on pioneering development of engineering grade materials for applications across many industries.
About Ultimaker
Since 2011, Ultimaker has built an open and easy-to-use solution of 3D printers, software, and materials that enable professional designers and engineers to innovate every day. Today, Ultimaker is the market leader in desktop 3D printing. From offices in the Netherlands, New York, Boston, and Singapore – plus production facilities in Europe and the US – its global team of over 400 employees work together to accelerate the world’s transition to local, digital manufacturing. ultimaker.com
Polymaker has an exciting product plan for the first half of 2019. We are adding 3 New filaments to our repertoire and new colors to existing filaments!
PolyLite™ ASA
PolyLite™ ASA will add more interesting application possibilities to the PolyLite™ range with its excellent weather resistance and thermal stability. The material of choice for prints that need to face the elements. PolyLite™ ASA also has good mechanical properties and printability.
PolySmooth™ & PolyLite™ PLA new colors
Polymaker will add more colors to the PolySmooth™ and PolyLite™ PLA range in order to offer a wider range of choices for users and allow them to transform their digital design into realistic 3D models. This will include, Orange, Yellow, Pink and Green for PolySmooth™ and a Sparkle range for PolyLite™ PLA of Grey and Blue.
PolyMide™ PA6-CF & PolyMide™ PA6-GF
After announcing Polymaker Industrial’s new N600 series, Polymaker is working on introducing PolyMide™ PA6-GF and PolyMide™ PA6-CF to extend PolyMide™ family of Nylon based material. These new products will offer higher mechanical and thermal properties while also featuring the now well-known Warp-Free™ technology. Print lightweight parts with incredible stiffness and durability.
Polymaker also has some new products lined up for Q3 & Q4 adding more materials to the PolyMax™, PolyFlex™ & PolyMide™ families.
Polymaker’s research and development lab continues to develop new technologies to ensure Polymaker materials stay the best option on the market.
PolyDissolve™ S1 is the first product of PolyDissolve™ family. This family offers dissolvable support solution for Polymaker filaments. PolyDissolve™ S1 is specifically engineered to have a perfect interface with materials while also displaying good solubility.
PolyDissolve™ S1 is a PVA (polyvinyl alcohol) material which dissolves in water. This main advantage makes it preferable solution to support when printing complex geometries, overhangs, internal cavities and complicated structures. It liberates you from support removal problems, and enables greater design freedom
So far, PolyDissolve™ S1 is compatible with PolyMax™ PLA, PolyLite™ PLA, PolyWood™, PolyFlex™ TPU95, PolySmooth™, PolyCast™, PolyMide™ CoPA.
Advantages of PolyDissolve™ S1
- It is engineered to have a good adhesion and perfect interface with supported materials.
- Only tap water is needed to dissolve it.
- It is compatible with 7 products from Polymaker portfolio.
Now it is available on www.polymaker.com and Amazon. You can also find it from Polymaker’s resellers.
PolyDissolve™ S1 Technical Data Sheet
PolyMax™ PETG is new member of PolyMax™ family. PolyMax™ family consists of advanced 3D printing filaments produced with Polymaker’s Nano-reinforcement technology, which delivers exceptional mechanical properties and printing quality.
PETG is a Glycol Modified version of Polyethylene Terephthalate (PET). It becomes more and more popular as 3D printing material. PETG 3D printing filament combines the advantages of 2 most popular kinds of FFF/FDM materials: PLA and ABS. It owns the reliability of PLA (easy to print, no warping, and odor during printing) and the functionality of ABS (strong, tough and heat resistant).
Just as PolyMax™ PLA and PolyMax™ PC (used to be called PC-Max™), which are the best of its kind, PolyMax™ PETG offers better mechanical properties than any other regular PETG making it a good candidate for a wide range of applications.
Pursuing the top-quality products, Polymaker applies the successful experience of creating PolyMax™ PLA and Nano-reinforcement technology to PETG material. Now we are delighted to introduce PolyMax™ PETG to you. PolyMax™ PETG has improved mechanical properties and printability.
Advantages of PolyMax™ PETG
- PolyMax™ PETG not only have the reliability of PLA (easy to print, no warping and odor during printing) but also have a greatly improved mechanical strength than normal PETG.
- PolyMax™ PETG’s heat resistance is up to around 80℃.
- PolyMax™ PETG has excellent layer adhesion.
- You don’t need to worry about warping or shrinking during the printing process, which ensures the dimensional stability.
Now it is available on www.polymaker.com and Amazon. You can also find it from Polymaker’s resellers.
PolyMax™ PETG Technical Data Sheet
The N600 series are a new set of Nylon 6 based filaments with excellent mechanical properties and heat resistance.
Designed for applications that require strong parts such as tooling in automotive, aerospace, industrial manufacturing and consumer goods.
The N600 series are equipped with Polymaker’s Warp-Free™ Technology which allows large scale printing without a heated chamber. The first three N600 series products are N600 (Nylon 6), N600GF25 (Glass fiber reinforced Nylon 6) and N600CF20 (Carbon fiber reinforced Nylon 6).
N600 is a PA6 filament with excellent mechanical properties and printability
N600GF25 is a glass fiber reinforced PA6 filament with excellent toughness and heat resistance
N600CF20 is a carbon fiber reinforced PA6 filament with extreme stiffness and excellent heat resistance
The Polysher™ transforms your 3D printed parts into smooth, glossy, layer free objects!