Polymaker is thrilled to announce the launch of PolyCore™ PC-7413, a cutting-edge pellet-based material made from 30% glass fiber reinforced polycarbonate (PC). This advanced material is specifically engineered for medium-temperature (80 °C - 120 °C) composite mold applications, an area that has rapidly evolved in recent years through the adoption of fused granule fabrication (FGF), also known as Large-Format Additive Manufacturing (LFAM). By leveraging FGF/LFAM, manufacturers achieve significant reductions in lead time and production costs.
“Over the past few years, producing large molds has rapidly become the most popular application of FGF/LFAM. PolyCore™ PC-7413 combines exceptional printability with cost-effectiveness to set a new benchmark in mold manufacturing.” Stated Raymond Huang, Director of Polymaker’s FGF Business.

Figure 1 | A mold was printed with PolyCore™ PC-7413
Key Features and Industry-Leading Capabilities
PolyCore™ PC-7413 boasts numerous advantages, making it an outstanding choice for medium-temperature composite mold applications.
- Excellent Heat Resistance: With a heat deflection temperature (HDT) of 136 °C at 1.82 MPa, PolyCore™ PC-7413 is ideal for autoclave curing processes up to 120 °C.
- Exceptional Printability: The glass fiber reinforcement minimizes warping during printing, and its finely tuned rheological behavior ensures smooth extrusion and excellent layer adhesion.
- Cost Effectiveness: PolyCore™ PC-7413 offers a cost-effective alternative to traditional carbon fiber reinforced materials, making it perfect for companies scaling up production without compromising on performance.
The material's performance was validated through a real-world case in which an aerospace-grade mold was successfully produced and subjected to additional rigorous testing. The mold met strict requirements for dimensional tolerance (± 0.2 mm) and airtightness, confirmed by high-precision laser scanning and vacuum tests. These results demonstrate the material’s exceptional heat resistance, strength, and dimensional stability, underscoring PolyCore™ PC-7413 as an ideal choice for composite mold applications.

Figure 2 | The mold and carbon fiber part after autoclaving

Figure 3 | Dimensional inspection result of the mold after autoclave curing
A Collaborative Success with Helio Additive
Beyond PolyCore™ PC-7413’s inherent material properties, we believe that the printing process, optimized by Dragon was also a critical factor in achieving the complete mold validation. By using a thermal history simulation for each voxel, Dragon’s optimization achieved a more uniform thermal distribution across the mold, reducing internal stress and enhancing layer adhesion. This process refinement contributed to the mold’s dimensional stability and airtightness, leading to a successful "First Time Right Print" with a 38% reduction in printing time.

Figure 4 | Optimization report from Dragon
“Materials are at the heart of what makes large format additive manufacturing powerful. Collaborating with Polymaker allows us to use the full power of Dragon with state-of-the-art materials to develop solutions for composite tooling.” Stated David Hartmann, CEO of Helio Additive
See PolyCore™ PC-7413 at Formnext 2024
Polymaker invites you to explore the capabilities of PolyCore™ PC-7413 and see firsthand how this new material can transform your manufacturing processes. Visit our booth at Formnext in Hall 12.1, Stand C21 to learn more.
For more information, or to explore how PolyCore™ PC-7413 can benefit your production, contact us at polycore.inquiry@polymaker.revolware.com.

Get ready for FormNext 2024, the international hub for Additive Manufacturing, happening at Messe Frankfurt from November 19 till 22. Polymaker will be there, showcasing our latest innovations in 3D printing at booth C21 in Hall 12, 1st floor.
It’s going to be a super busy event with more than 800 exhibitors and 30.000 visitors. To make sure we have enough time to meet, let us know that you are coming! And if you don’t have a ticket yet, you can request it right away!
What’s happening on the Polymaker booth:
Discover Fiberon
Fiberon™ is committed to developing high-performance composite filaments with the best printability and cost performance ratio.


Discover Panchroma
Explore 17 surface finishes in more than 150 color combinations. With every collection, we strive to bring a new color in a different application and surface finish.
Discover more…
Next to the new product lines mentioned above there are more new products being revealed during the event. But you can also take a look at our Polydryer™ released earlier this year and we have a section dedicated for Polycore pellets with some interesting prints and case studies.

Since its launch, Polymaker's PolyDryer™ has captured the attention and enthusiasm of the 3D printing industry. This innovative product has impressed consumers with its advanced features and exceptional performance, solidifying Polymaker's commitment to enhancing the user experience and simplifying creation.

Key Advantages and Market Enthusiasm
PolyDryer™ stands out in the market with its dual functionality, combining drying and sealing capabilities into one comprehensive solution. It effectively addresses common issues such as moisture-induced stringing, clogging, and poor surface quality. The product consists of two main components: the Dry Dock, which ensures stable temperatures for quick and even drying, and the PolyDryer™ Box, designed with superior sealing performance. Together, they provide a seamless experience for users, preventing common printing issues caused by moisture and dust.
The product has garnered positive feedback from key opinion leaders (KOLs) and consumers alike. Many have praised its efficient drying and storage capabilities, as well as its modular design, which allows for flexible usage. Users have expressed their excitement about the impact PolyDryer™ has had on their prints, inspiring them to experiment with new materials and techniques. Polymaker is thrilled to witness how PolyDryer™ has sparked creativity within the industry.


Sourced from YouTube

Sourced from X
Commitment to User Experience
Hang Qu, VP of Sales & Marketing in Polymaker, emphasized the company's dedication to user experience and continuous improvement. “At Polymaker, we value user feedback and market insights. We actively collect this information and communicate with our internal Product Engineering Department to explore potential improvements. Our goal is to ensure that our products not only meet but exceed user expectations.”
In response to the high demand, we are excited to announce that PolyDryer™ is back in stock! We appreciate the enthusiasm for this product and invite new users to experience its benefits.

Simplify Creation
Polymaker is dedicated to ongoing research and development to enhance user satisfaction and simplify the creation process. The success of PolyDryer™ is a testament to this commitment, showcasing our focus on providing high-quality, reliable solutions for 3D printing enthusiasts. As we continue to expand our range of materials and services, we remain focused on empowering users to achieve their best work.
With PolyDryer™, you can ensure optimal printing conditions and improved print quality. With Polymaker, you can enjoy high-quality filaments’ printing process and achieve outstanding results. Join us as we continue to innovate and inspire creativity in the world of 3D printing.
For more information and to purchase PolyDryer™, visit the link below.
US Web Shop: PolyDryer™ – Polymaker US
Find A Reseller: Find a Reseller - Polymaker
Rapid + TCT 2024, the largest and most influential additive manufacturing (AM) event in North America, was successfully held in Los Angeles Convention Center from June 25th to 27th. This year, this event attracted nearly 10,000 3D printing professionals and featured more than 400 exhibitors. During the 3 days, Polymaker drew significant attention from attendees with its brand new product families over the course. The diverse styles of booths, materials, and prints were also the highlights.

Forward-looking | Two New Product Families
This year, Polymaker announces the expansion of its product portfolio with the launch of two new distinct product families, Fiberon™ and Panchroma™. These new offerings underscore Polymaker's commitment to innovation and its ongoing efforts to meet the diverse needs of the 3D printing industry.


Fiberon™ focuses on developing cutting-edge composite filaments with both high performance and excellent printability and brings industrial-grade composite performance to the desktop, enabling a new wave of end-use part production and functional prototyping applications.



While Panchroma™, Polymaker’s new aesthetic product family, is designed to meet the growing demand for high-quality, visually stunning 3D prints by offering the widest selection of colors and surface finishes available on the market.



"We see two increasingly critical needs in the FDM/FFF industry – functional properties and aesthetics. Fiberon™ and Panchroma™ are our answers to address these customer needs," stated Dr. Xiaofan Luo, CEO of Polymaker.
Broadly-applicable | Multiple Application Examples
Polymaker also showcased a wide range of impressive prints created and printed entirely by our partners across various fields, highlighting the brand's robust and diverse cross-disciplinary application capabilities. These case studies were specially sent to us for the show, demonstrating the collaborative efforts and innovative spirit of our partners.

The Wisconsin Robotics team utilized PolyFlex™ TPU95 to print rover wheels for rugged outdoor environments. With these wheels, robot can climb slopes, carry heavy loads, and hike mountains with ease. This robot can even go to Mars, which is believed to be possible with the material's application properties.





Images Provided by Wisconsin Robotics
Printonic, based in the Netherlands, specializes in crafting exquisite guitars using 3D printing technology. Their beautifully designed instruments have even been played at the Dutch Paaspop Festival. At this exhibition, we proudly showcased an M87 guitar made from PolyLite™ PLA Pro and PolyTerra™ PLA.




Images Provided by Printonic 3D Geprinte Gitaren
The Smart Birdhouse next to the guitar is printed with PolyTerra™ PLA by The Peep Show. The roof of this smart birdhouse is equipped with a miniature camera that, when placed high up outdoors, allows people on their cell phones to see how the young birds inside the birdhouse are surviving so that they can help at any time.
Video Provided by The Peep Show
The booth featured several captivating displays that drew in many visitors. Among them was a helmet from a complete Iron Man MK45 costume, fully automated to open and close, and printed entirely in PolyLite™ CosPLA by Squires Cosplay. Other highlights included the RAYON Concept fashion shoes made from PolyFlex™ TPU95 by Kacimi, a fully functional RC boat named MiniRIPPER, with the outer structure printed in PolyLite™ ASA and the internal parts printed in PolyMide™ PA6-CF by Hillprinties, and custom hotends printed with PolyLite™ ABS, a collaborative project by BobFromCalifornia with contributions from numerous community members.




These works not only demonstrate the innovative use of 3D printing technology by designers from different fields, but also highlight the unlimited potential and diversity of Polymaker's material applications.
Through this year Rapid + TCT, Polymaker also actively interacted with the audience and communicated with other exhibitors, constantly injecting new vitality and power into the brand and opening up broader prospects for future development. Polymaker will continue to dedicate itself to innovation and quality, and continuously contribute to the development of the 3D printing industry.
Polymaker, a leading producer of 3D printing materials, announces the expansion of its product portfolio with the launch of two new distinct product families, Fiberon™ and Panchroma™. Fiberon™ focuses on developing cutting-edge composite filaments with both high performance and excellent printability, while Panchroma™ offers filaments with the most diverse range of aesthetic properties. These new offerings underscore Polymaker's commitment to innovation and its ongoing efforts to meet the diverse needs of the 3D printing industry.
"We see two increasingly critical needs in the FDM/FFF industry – functional properties and aesthetics. Fiberon™ and Panchroma™ are our answers to address these customer needs," stated Dr. Xiaofan Luo, CEO of Polymaker.
Fiberon™
Master composite materials with Fiberon™, democratizing high performance composite 3D printing filaments with a comprehensive range of material properties. The launch of Fiberon™ introduces 3 new fiber reinforced materials to the market, PET-CF17, PETG-rCF08 & PPSCF10. These new materials are paired together with the existing composite filaments from Polymaker (PA6-CF20, PA6-GF25, PA612- CF10, PA12-CF10, PETG-ESD). In essence, Fiberon™ brings industrial-grade composite performance to the desktop, enabling a new wave of end-use part production and functional prototyping applications previously off-limits due to printer capabilities and pricing.

"Traditionally, desirable material properties like strength or heat resistance required expensive industrial printers. Fiberon™ challenges this. With advanced materials, users can print strong, stable, functional parts using entry-level printers. We’re democratizing high-performance 3D printing materials.” - Dr. Xiaofan Luo, CEO of Polymaker
Learn More: Fiberon 3D Printing Filament by Polymaker – High-Performance Composite Filaments
Panchroma™
Polymaker’s new aesthetic product family is designed to meet the growing demand for high-quality, visually stunning 3D prints by offering the widest selection of colors and surface finishes available on the market. Panchroma™ is committed to the highest consistency of color for its products with a multi-step process monitoring the quality control for color consistency.

Panchroma™ employs a number of extrusion techniques in order to create their filaments and the combinations of these techniques with the multitude of color expands the filament offering exponentially. Filaments are divided by their extrusion process, then surface finish and finally the color. This allows users to navigate through the vast array of options and find the filament they need.
To further assist customers with their workflows, Polymaker is developing a web-based tool that allows users to create realistic digital renders based on different Panchroma™ colors & surface finishes.
Learn More: Panchroma 3D Printing Filament – Where easy printing meets the world of color (polymaker.com)
On the occasion of the official launch of these two product families, Polymaker has completely upgraded the packaging to enhance the user experience.
• Adding Inside and Outside Spool Wrapping: This ensures smooth rotation of the spools in the AMS while preventing the cardboard dust from dropping during use.


Before vs After
•Modified Hole Shape and Spacing: These changes reduce the likelihood of breakage during threading, enhancing durability.


Before vs After
• Larger Windows on Both Sides of the Cardboard: This allows customers to easily see the filament color, providing a more intuitive selection process.


Get ready for the launch of these upgraded products!
SHANGHAI, May 6, 2024 - Polymaker recently won the TCT Asia Best Application Award - Industrial Product Applications for its pellet product, PolyCore™, in the 3D printing of architectural stencils. This honor not only recognizes Polymaker's innovation and excellence, but also its continued leadership in the 3D printing industry.

With the continuous innovation and advancement of 3D printing technology, utilizing the advantages of 3D printing's high precision and large size, PolyCore™ was selected as the product range to produce a 5m(L)*0.4m(W)* 2m(H) brand wall for Polymaker.
Polymaker collaborated with Shanghai Mechanized Construction Group, a subsidiary of Shanghai Construction Group (SCG) and Shanghai Kuying Technology Co., Ltd. to develop and print this wall.
The design of the wall features the Polymaker logo and a multi-faceted pattern, which demonstrates the strength and advantages of 3D printing when implementing creative design ideas in the construction Industry.

The completion of this wall is of great significance. SCG said: “The application of 3D printing technology in large scale shaped concrete formwork will revolutionize the speed and accuracy of manufacturing such as molds in municipal and construction projects. Compared with traditional molds, 3D printing technology effectively reduces the manufacturing cost and construction time, and promotes the transformation of traditional construction to digitalization, industrialization, intelligence, and low-carbonization.”
It is a significant achievement for Polymaker to be recognized at TCT Asia (The most influential additive manufacturing event in Asia) and to be awarded the Best Application Award - Industrial Product Applications, further reinforcing Polymaker’s position and portfolio within the construction field. Detailed information about this case, please click "Architecture Molding Case Printed with PolyCore™".

“We are extremely honored to win this award at TCT Asia this year. It not only recognizes our team's unremitting efforts and continuous innovation, but also brings new insights to the construction industry. Polymaker has been a pioneer in applying 3D printing to the construction field, providing a variety of pellet products for the construction industry including indoor design and outdoor construction, and successfully creating projects such as Taopu Central Park Bridge in Shanghai, China, the “Liuyun Bridge” in Chengdu,China, and Namthaja’s Rakah Roundabout Sculptures. In the future, the brand will also continue to devote itself to technological innovation and product optimization to bring more intelligent manufacturing possibilities to the construction industry and make buildings glow with the beauty of intelligent manufacturing.” Polymaker CEO Dr. Luo Xiaofan said.
In addition to the Best Application Award - Industrial Product Applications, Polymaker was also honored as a “10 Years Exhibitor” on the occasion of the 10th anniversary of TCT Asia. This honor represents Polymaker's longstanding partnership and close relationship with TCT Asia, as well as the brand's continued contributions to the 3D printing industry.

In the future, Polymaker will continue to uphold the spirit of excellence and innovation, expanding the boundaries of the additive manufacturing field, providing customers and partners with superior solutions, and ultimately advancing the development of additive manufacturing technology.
At the 2024 TCT Asia exhibition which has come to an end at May 9th, Polymaker lit up the whole exhibition with a feast of vision and technology, and became the focus of attention. The booth was crowded and bustling with people, showcasing Polymaker's brand charm and innovative spirit.

Colorful PLA, Blooming Infinite Creations
Walking into Polymaker's booth, the most eye-catching area for visitors to stop and take photos was the colorful PLA area. From classic solid colors to lively clashing colors, the PLA display area inspired every visitor with its rich variety of color choices. These high-performance materials not only demonstrate the aesthetic potential of 3D printing materials, but also reflect Polymaker's deep expertise in material innovation, allowing visitors to touch the infinite possibilities of future designs.


PolyDryer™, A New Era of Drying & Storage
Another highlight of the exhibition was undoubtedly the public debut of PolyDryer™. This new product, which aims to be your ultimate 3D filament drying & storage solution, attracted the attention of many professional visitors with its modular design and outstanding performance. Equipped with the high precision heat control system, fan and PTC heater, PolyDryer™ can dry the most commonly used 3D filament types efficiently. In addition, filament can also be dried during printing if pressing and holding button "M" to activate Continuous Drying Mode, to ensure thorough drying of all filament layers, providing double assurance of material quality. Every feature makes the on-site experiencers marvel!


Ingenious And Eye-catching Exhibits
This year, an area of the booth was set aside to display original prints by domestic 3D printing enthusiasts and each exhibit is a perfect interpretation of Polymaker's material performance. These exhibits, either delicate or complex, demonstrated the creators' whimsical ideas and the unlimited potential of Polymaker materials, attracting waves of visitors to appreciate.


Case-study Area, Showcasing New Achievements
Especially worth mentioning is Polymaker's elaborate Golden Exhibits Area, which is crowded almost all day long and has become a stopping point during the exhibition. It not only showcases Polymaker's latest applications results in the industrial, technological and medical field, but also becomes a mecca for peer-to-peer exchanges and collision of inspirations, and every visitor is deeply attracted by this strong innovative atmosphere.


Media Focus, Highlighting Industry Leadership
During the exhibition, the TCT organizer conducted an in-depth bilingual interview with Dr. Luo Xiaofan, CEO of Polymaker, which covered brand concept and technological innovation, showing the brand's leading position in the 3D printing industry in all aspects. In addition, the visit of many media people has further boosted the popularity of the Polymaker booth, highlighting the enthusiasm and anticipation both inside and outside the industry.


With the above description of the wonderful moments, hope you can already appreciate the great charm of 3D printing and of Polymaker. During the three days exhibition, Polymaker not only demonstrated its strong strength in the field of 3D printing, but also connected with global users and industry partners closely, and sketched out a more brilliant blueprint with them for the future of 3D printing technology. Let's look forward to the next gathering. More innovation, More surprises!
Polymaker is excited to launch PolyDryer™, a revolutionary product designed to provide the ultimate solution for drying and storing 3D printing filaments which protects against dust and moisture. With advanced features, such as modular design, superior sealing performance and high drying efficiency, PolyDryer™ aims to enhance the quality of 3D prints by addressing common issues.

Printing with wet 3D filament can lead to various issues such as stringing, clogging and rough or poor surface quality, highlighting the necessity for drying or sealing. While existing drying or sealing products on the market solve these problems to some extent, combining drying and sealing functions into one comprehensive solution has been a focus for Polymaker, leading to the creation of PolyDryer™.

The whole product features modular design and consists of two units: Dry Dock, ensuring stable temperatures for quick and even drying with a precise heat control system and PTC heater, and PolyDryer™ Box, which offers superior sealing performance and continuous filament protection. These components can be used separately or together. Dry Dock evenly dries filaments in the PolyDryer™ Box above it, and PolyDryer™ Box can be used with or without the dock for separate storage.

Second key feature is its superior sealing performance. PolyDryer™ allows for extended drying and long-term protection of materials. Its exceptional sealing capability and visible desiccant indicator display maintains optimal humidity levels, ensuring that filaments are dry and ready for printing.

Thanks to the high precision heat control system, fan and PTC heater, PolyDryer™ can dry the most commonly used 3D filament types efficiently, including PLA, ABS, ASA, PETG, PA, TPU, PC and more. In addition, filament can also be dried during printing if you press and hold button "M" to activate Continuous Drying Mode, to ensure thorough drying of all filament layers, providing double assurance of material quality.

PolyDryer™ offers wide compatibility with various 3D printing materials, accommodates filament up to 1kg, and both of 1.75mm/2.85mm/3.00mm diameters can be used in it. Moreover, it has a compact footprint for which makes it easily portable.
"PolyDryer™ offers a one-stop solution for effective drying and sealing, ensuring optimal printing conditions and improved print quality," stated Dr. Luo Xiaofan, President of Polymaker. He added, "As a brand dedicated to meeting user needs, we aim to provide a complete 3D printing filament solution with this product. In the future, Polymaker will expand its presence in 3D printing materials, offering a wide range of material services to simplify creation.”

Now PolyDryer™ is available on the market, for more details or to purchase, click the link below.
US Store: https://us.polymaker.com/products/polydryer
Amazon: https://www.amazon.com/dp/B0CK1BX9G2
Find A Reseller: https://polymaker.revolware.com/find-a-reseller
In addition to the product, several PolyDryer™ exclusive accessories have been carefully designed to enhance your 3D printing experience, please follow us on Printables and MakerWorld:
Polymaker | Published - MakerWorld
Note: DIY modifications may affect the safety and performance of the PolyDryer™.
Polymaker, as a high-tech company specializing in 3D printing materials, recently announced that it has obtained the ISCC (International Sustainability & Carbon Certification). This certification signifies an important milestone for Polymaker in the field of environmental sustainability and further solidifies its leading position in the industry.


Initiated in 2006 through a multi-stakeholder dialogue and with assistance from the German Federal Ministry of Food and Agriculture (BMEL), the ISCC (International Sustainability & Carbon Certification) is a globally recognized and EU leading sustainability certification system.
The ISCC certification system covers all sustainable feedstocks, including biomass from agriculture, forestry and aquaculture, biogenic waste and residues, non-biological renewable materials and recycled carbon-based materials and products derived therefrom. It aims to protect forests, high-carbon stock areas, and biodiversity by certifying and managing sustainable, traceable, deforestation-free, and climate-friendly supply chains, contributing to the achievement of environmental, social, and economic sustainability.
To obtain the ISCC certification, Polymaker has redefined its supplier audit standards, planned and improved its own management capabilities and material production technologies. This ensures that Polymaker’s supply chain management and production processes complies with ISCC's strict standards and achieves 100% traceability.
Polymaker has a strong reputation in the industry as a world-renowned innovator and manufacturer of extrusion-based 3D printing materials. The first phase of implementing the ISCC system included two environmentally friendly materials: bio-based PC (polycarbonate) and bio-based PLA (polylactic acid). These two types of materials are important components of the Polymaker product family and have numerous applications in consumer, professional, and industrial markets.
"Gaining ISCC certification is of great significance to Polymaker," said Mr. Hang Qu, Vice President of Sales and Marketing at Polymaker. "This represents that Polymaker is not only meeting the functional needs of customers but also taking a solid step towards improving corporate ESG responsibilities. This commitment signifies Polymaker's strong willingness to promote sustainable development solutions and effectively deliver this value to downstream customers."
In the future, Polymaker will continue to focus on developing more innovative and environmentally friendly 3D printing materials and technologies. The company will actively seek additional certifications and collaboration opportunities to drive the progress of sustainable development.
To better serve the fast-moving filament market in Europe, Polymaker have opened their new distribution centre promising faster shipping, a more comprehensive stock and a wider range of materials available to European customers.
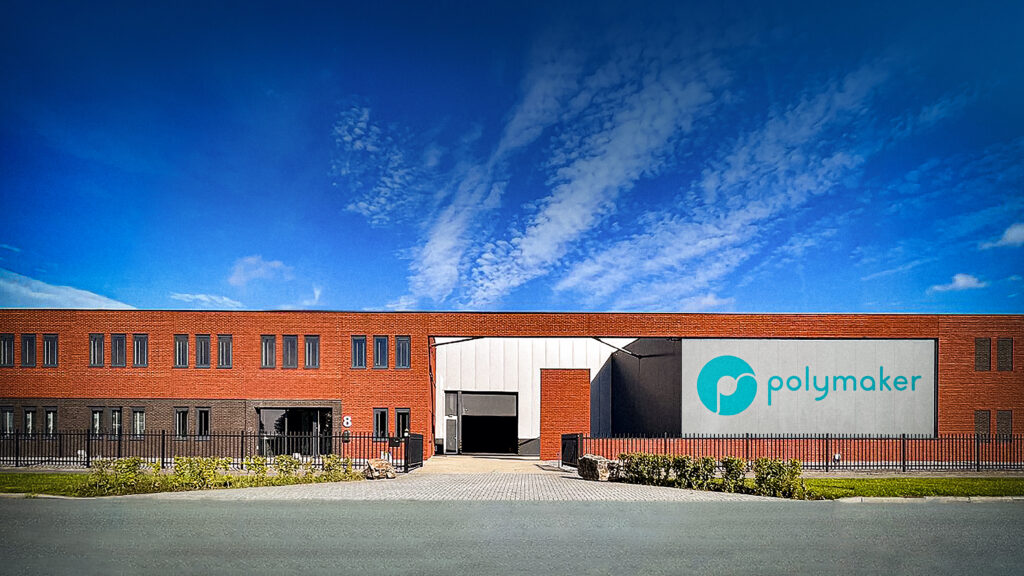
Located in a quaint industrial park in Houten, Netherlands, their around 1020m2 warehouse can hold the ever-growing repertoire of Polymaker products.
Visit “Global Locations" in "Why Polymaker” Page to view the detailed address of our new European Distribution Centre.
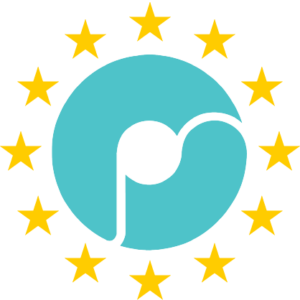
While it seems that customers can’t shake their relationship with Black PLA, Polymaker prides itself in offering the largest colour range of any filament manufacturer with over 140 colour variants in PLA alone. The list of filament options for engineering and aesthetic applications are seemingly endless and Polymaker's large research and development team are continuing to explore new technologies for extrusion-based 3D printing.
Polymaker have expanded their European team with a logistics manager, warehouse manager and team of handlers to expedite the picking & shipping of filaments to European customers. All handled in-house the ordering process has been optimized to promise quicker shipping times for customers across the region.
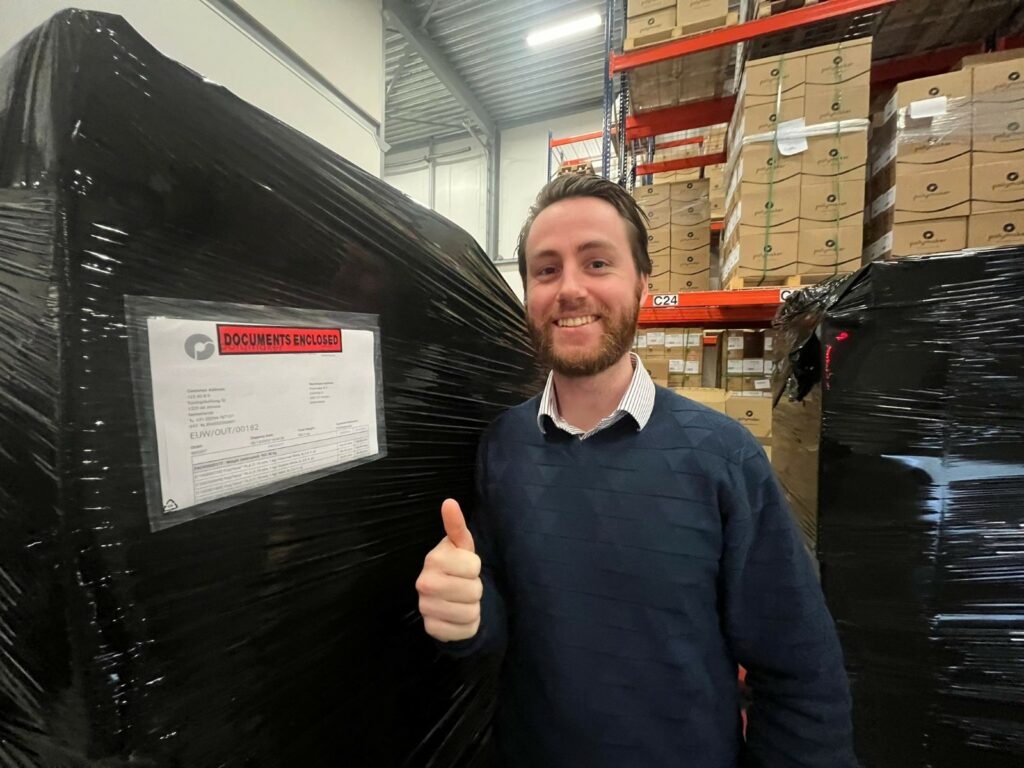
Aside from the new warehouse Polymaker has invested in an expertise centre and quadrupled the size of their print lab to continue material testing and better serve application partners across Europe.
As Polymaker continues to lead the market in quality and variety of 3D printing filaments, the new European distribution centre has the ability to best serve the imaginations of engineers, tinkerers and enthusiasts across the continent.
Recently, Luo Xiaofan, co-founder and president of Polymaker, was jointly interviewed by the industry's well-known media Science Valley and 3D Printing Industry to discuss the trends and challenges in the industry in 2023.
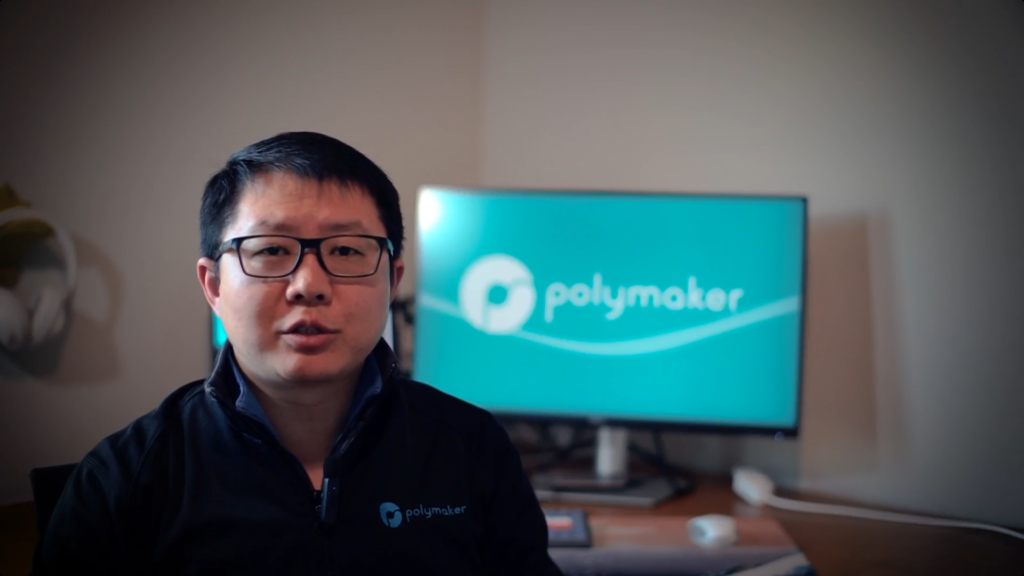
Here's what he said.
TRENDS
With the liberalization of epidemic control in China, the year of 2023 is very likely to be the first year when the 3D printing industry truly enters the “post-epidemic era”. I am looking forward to the recover of technical exchanges and market activities that were interrupted due to the epidemic. The high-speed and healthy development of 3D printing is inseparable from global exchanges and cooperation, so we (Polymaker) have also accelerated our global landscape: in 2023, we will establish the first overseas production base and technology center to accelerate 3D printing and to better serving our clients’ innovations around the world.
The second trend I see in 2023 is the further segmentation and specialization of additive manufacturing technology. In the past few years, most companies in the market can be divided into three categories: equipment, materials and services. However, this simple classification seems is unable to describe the current industry ecology. In many subdivided fields, such as core components, various design, simulation and process optimization software, and specific application solutions, more and more specific solutions have emerged. The specialization of technology is also a sign of the maturity of the additive manufacturing industry. I believe this trend will become more and more obvious in 2023, which will also bring more and more companies a new round of innovation and development opportunities.
In 2023, we will see 3D printing enter more application scenarios for the production of parts and end products. This is an irreversible trend; the epidemic in the past few years has also accelerated this trend in a sense. This can also be seen from the customers we serve: last year, the production purpose applications we served our customers have experienced several times of growth, and many of them will increase their investment this year (2023). In the process of serving the innovation of our clients, we have also gained a lot of sense of value creation, hence our vision of “Simplify Creation” is also unfolding step by step.
Generally speaking, I believe that after experiencing the ups and downs of the epidemic for three years, the 3D printing industry will usher in a more positive and optimistic situation in 2023: the specialization of 3d printing technology and the deepening application for final parts production will also bring more opportunities for innovation and development.
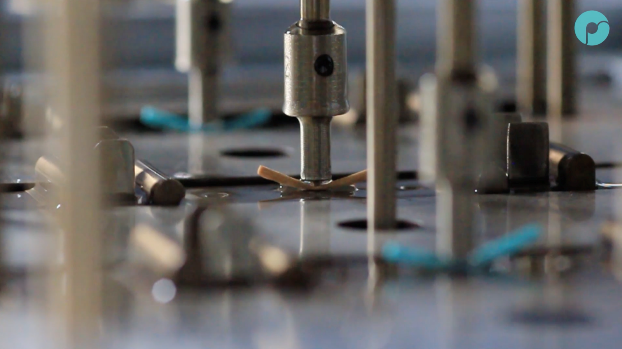
CHALLENGES
For most additive manufacturing technologies, I thinks process complexity is still the biggest technical challenge. Unlike most traditional manufacturing technologies, 3D printing has many process variables, and there is a highly coupled relationship between process, material and geometric structure; the traditional process development and optimization paradigm can no longer adapt to the highly complex process characteristics of 3D printing. This has also led to a series of challenges that the 3D printing industry is still facing: process development and optimization take a long time, printing process control is difficult, quality consistency is low, performance is unpredictable, and so on.
To solve this problem, this requires the coordination of many technologies. First of all, we need to improve the construction of the physical model of the printing process. Academia has done a lot of work in the past few years, and it should be said that a good foundation has been laid. What is needed next is to develop simulation software based on these accurate and verified physical models as the main tool for studying the 3D printing process, and at the same time establish a matching, standardized database of equipment, materials and processes. With this foundation, the application of process development, optimization and control can be built based on specific technologies and application requirements; the technical possibilities here are relatively rich, and it can be combined with artificial intelligence and data science to achieve efficient process optimization , It can also be combined with online monitoring of hardware to realize closed-loop control of the printing process, and can also be connected with design software to form a complete closed-loop from design to production.
The realization of the above technologies requires a lot of investment and multi-disciplinary efforts, but this is also the technical threshold that must be solved for additive manufacturing to further realize its potential and truly become a mainstream manufacturing technology. We (Polymaker) have also made a lot of investment and made a lot of progress with many partners in the past few years. In 2023, we will have more profound solutions to face to the market, and here you can also look forward to it.
Thanks to your support, Polymaker has been nominated for Sustainability in Additive Manufacturing and Material Company of the Year by 3D Printing Industry Awards 2022.
3D Printing Industry Awards 2022 - Vote Now! - 3D Printing Industry
Sustainability in Additive Manufacturing
Since the launch of PolyTerra™ at the beginning of last year, our customers have planted over 340,000 trees by choosing to print with PolyTerra™ PLA over other materials. Polymaker pledged to create the most environmentally friendly 3D printing material which is materialized by offsetting Co2 in partnership with One-Tree-Planted. With trees planted in 15 different regions spanning 6 continents, PolyTerra™ customers provide benefit to their local region and One-Tree-Planted ensures the diversity of forest is populated with local species. To date, the PolyTerra™ program has offset 6,800,000 Kg of Co2 in under 2 years with the trees set to continually offset Co2 for decades to come. It’s important to remember that the true benefits of trees and healthy forests go far beyond carbon storage. Their value for biodiversity, social impact, wellbeing and the stability of the global climate is well documented.
As for the material itself, PolyTerra™ PLA is a compound of PLA bio-plastic and bio-composite, containing less plastic to degrade and making the material more environmental friendly without affecting the printability. Now available in over 30 matte colors its clear to see why this 3D printing material is so popular and with its 100% recycled cardboard spool it’s hard to disagree.
Material Company of the Year
Polymaker strives to develop and manufacture diverse 3D printing materials providing our customers with the tools to push the boundaries on what’s conceivable. This year, Polymaker launched a number of new products, further diversifying the repertoire of the extrusion-based market. PolyMax™ PETG-ESD offers electrostatic dissipation through carbon nanotubes paired with tough PETG, making it perfect for applications in electronics industry. PolyMide™ PA612-CF, a nylon with excellent mechanical and thermal properties as well as good size stability, contribute to industrial and engineering tooling, automotive, and end-use industry. PolySupport™ for PA12 a breakaway support material for long chain nylons, 9 times out of 10 the quickest and easiest support removal choice is breakaway and Polymaker have filled a gap in the market with this easy to use product.
Diverse material families, a spectacular choice of colors, quick product iteration whilst maintaining the highest quality standards are just some of the reasons why customers choose Polymaker.
We would be honored with the recognition, so we ask for your vote!
3D Printing Industry Awards 2022 - Vote Now! - 3D Printing Industry
Polymaker rises to the top to take home the Creative Application Award at this year's TCT360 exhibition in Birmingham, UK. The LEGO Go-Kart created by Matt Denton in partnership with Polymaker impressed this year's judges and was a crowd favourite at the award ceremony, gaining lots of cheers even before the winner was announced. The Creative Application Finalist selection was filled with some fierce competition such as: Stratasys, BMW, Shapeways, Ricoh 3D and Gravity Industries among many other impressive projects.
Polymaker win 2022 Creative Application Award
The first fully-electric ridable giant LEGO Go-Kart from Matt Denton. Scaled up 3D printed LEGO blocks printed on desktop FFF printers assembled into a fully working electric Go- Kart.
While the aesthetics of the Go-Kart are inspired by the LEGO Technics kits #1972 released in 1985. It was the electrification that created a challenge that required an original solution to a design that was not intended for human transportation. The use of desktop 3D printing enabled Matt to print all the bricks needed to assemble the Go-Kart with only a few non-3D printed parts, such as motors, brakes, and electronics. The end result is something that looks like it shouldn't drive, but when it does it's guaranteed to put a smile on your face.
Matt Denton and the LEGO Go-Kart
The realisation that a fully functional Go-Kart can be 3D printed on your desktop and assembled with parts you can buy online will inspire people to think inside the blocks. Creativity can be applied to old concepts the same as new.
Absolutely everyone loves it, Matt has brought a childhood toy to life like something out of a pixar movie. Even the folks at LEGO spoke to Matt saying they love what he's doing. Matt displayed the Go-Kart on the Polymaker booth at FormNext 2021, the crowd response has been overwhelmingly positive with many people stopping to take pictures and ask Matt questions. Matt's YouTube videos have gained over 1.8 million views related to the Go-Kart project.
Sjoerd & Gisela collect the Creative Application Award at the TCT award ceremony
All materials for the Go-Kart were supplied by Polymaker. Matt choose a wide range of filaments as the material needs differed from brick to brick. The chassis bricks were printed in PolyMax™ Tough PLA, the gears in PolyMax™ Tough PETG, the axles in PolyMax™ Tough PC, the tyres in PolyFlex™ TPU95. Finally, PolyLite™ PLA was used for some cosmetics parts. The combination of materials allowed Matt to take advantage of the mechanical properties of a wide range of filaments which were all compatible with his desktop printing setup.
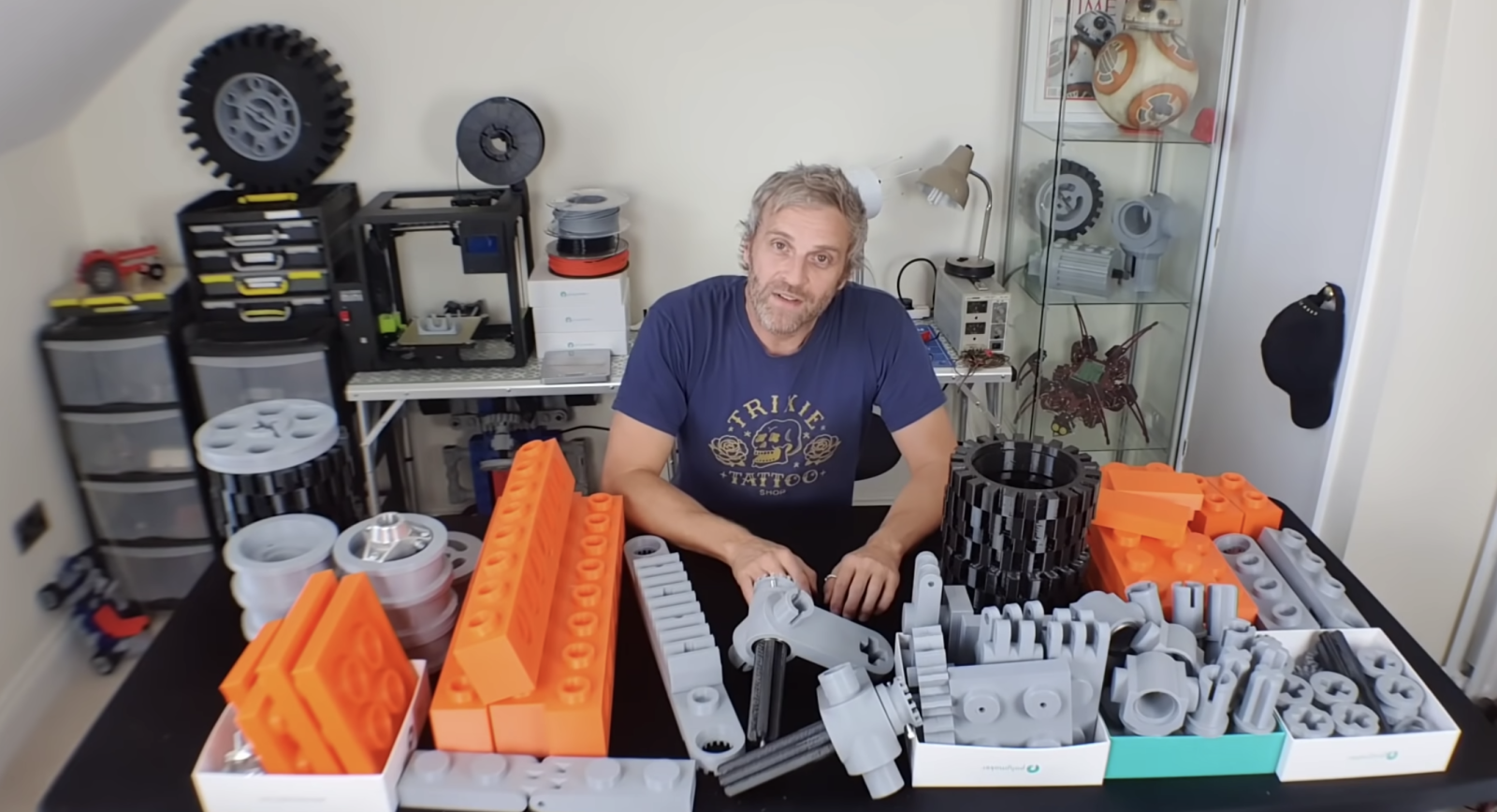
3D printing is the only way to create this Go-Kart. Even if you paid the ludicrous amount of money for the tooling of these giant blocks, a solid injection moulded brick would be too heavy. 3D printing allowed Matt to have a number of slight variations to the bricks so that they could hide bearings or route cables without spoiling the aesthetic. With a desktop 3D printer over 95% of all the parts were printed at home by Matt on a 300mm x 300mm x 300mm print bed.
Electric vehicles are the way forward as we reduce our carbon emissions. Showing people that they can print their own vehicles at home reduces heavy emitting big industry and localizes manufacturing. This, in turn, eliminates the need to ship products around the globe further reducing emissions. 3D printing gives the ability to manufacture locally and this project is a great example of what can be achieved with inexpensive desktop 3D printers at home in your bedroom.
The classic design touches a special place in our younger hearts, reminding us of a simpler time when our creativity could run free. Everyone who played with LEGO when they were a child is instantly reminded of the familiarity of this project. A large scale model on its own would still invoke this feeling, but the fact that this isn't just a model, its a rideable electric vehicle which adds even more charm to the project.
Just as the original technics kit from 1985 inspired Matt to take up engineering. He now hopes that this new generation armed with 3D printers can realize their potential by following in Matt's footsteps. The ability to design and customize parts enabled Matt to create the Go-Kart without spoiling the LEGO aesthetic. Matt's videos break down the individual parts and he explains the design choices he made. With over 20 years working in the special effects industry for TV & Film, Matt's experience paired with a fun project provides an engaging educational and problem-solving demonstration.
Matt has already posted his next video which involves some PolyMax™ PC drifting sleeves. The 3D printed sleeves will fit over the rear tyres greatly reducing the grip that the PolyFlex™ TPU95 provides, instead, the rear wheels can spin with less friction allowing Matt to drift the Go-Kart around.
Matt will reprint the PolyMax™ PETG gears to give a higher speed ratio necessary for drifting.
Wear Damage on the PolyMax™ PC drifting sleeves after intense usePoly
In recent decades, the rising trend of the green economy has swirled through the global market.
Polymaker, as one of the leading 3D printing companies, has put its efforts into upgrading materials and sustainable development.
Polymaker is a developer and manufacturer of 3D printing materials committed to innovation, quality, and sustainability. Its award-winning product portfolio has enabled numerous individuals and companies to better create and make. Headquartered in Changshu, China, Polymaker has multiple office locations in Shanghai, Utrecht, and Houston ready to serve customers across the globe.
Global plastic waste status in the last three years
In September 2021, global plastic waste has risen up to 75.9% of the entire plastic consumption. In 2019, the global plastic production amount was 368 million metric tons and after one year, this amount has increased by 3.5 percent in terms of the compound annual growth rate. The sum is approximately equal to the total weight of the earth's population. Among this, up to 50% of plastic is for single use and is disposed of immediately after use.
Approximately 6.3 billion tonnes of plastic were discarded as waste, of which around 79% has accumulated in landfills, 12% was incinerated, and 9% recycled. Only 1% of all plastic has ever been recycled more than once.
Now let’s take a look at how Polymaker has contributed to the eco-friendlier road in the past year. Polymaker has led several steps in reducing carbon footprint following four key developments.
Ⅰ Curbing plastic contamination, Polymaker launched bioplastic filament PolyTerra™ PLA
Detached from the traditional petroleum-based raw materials, Polymaker has developed the bio compound 3D printing filament PolyTerra™ PLA and launched in February 2021. PolyTerra™ PLA, extracted from plant photosynthesis, combines PLA bioplastic and biocomposite into one 3D printing filament. Compared with its petroleum-based counterparts, this filament is bio-based. The petroleum-based filament used to be the ideal choice for common 3D printing users due to its wide applicability. However, the old petroleum-based system is facing a turning point now, people no longer seek after unsustainable and limited resources, on the contrary, more environmentally adaptable bio-based ones are more attractive to them. PolyTerra™ PLA produces less carbon footprint than ordinary petroleum-based counterparts in the manufacturing process. PolyTerra™ PLA is also well-known for its biodegradability to which extensive independent reports have been created. Petroleum-based material needs a much longer time than bio-based filament in terms of decomposing. Unnecessary prints could be thrown away and normally end up in the landfill which takes thousands of years in natural degradation. PolyTerra™ PLA decomposing takes a much shorter time than that.
PolyTerra™ PLA is not only fashioned for its bio-compound nature but also the adoption of 100% cardboard spool has accelerated its circulation. The similarity between PolyTerra™ PLA and its outer packaging can be assorted into their decomposability. Under the right conditions, microorganisms and other substances decompose paper fibers from the cardboard packaging and return all organic elements to earth.
Ⅱ Altering plastic mainstream position, Polymaker transitions all plastic spools to 100% recycled cardboard spools
As the initial bio-product of Polymaker, PolyTerra™ PLA is the inspiration of another movement. The success of PolyTerra™ PLA led to the transformation of cardboard spools. Polymaker decided to enlarge the scale of cardboard spool manufacturing. Now the company is gradually replacing all plastic spools with 100% recycled cardboard spools.
Cardboard spool combines many meaningful elements in its design process. Apart from the new cardboard spool’s recycled nature, the entire part of which is available for generic paper recycling. For example, the empty spool can easily be ripped apart into two cardboard faces and a cardboard tube. Then, the old paper information sheet has been replaced by the product QR code. Via scanning it, customers can easily get all product info such as printing profiles, TDS, SDS…. By doing so, a large amount of paper consumption has been saved. In the meantime, the simplification of outer packaging reduces the carbon footprint emission in manufacturing.
Ⅲ Reducing carbon footprint, the initiation of PolyTerra™ PLA One Tree Planted program maintains ecological balance
With the launch of PolyTerra™ PLA, Polymaker announced a partnership with One Tree Planted in conducting the reforestation plan. For every spool of PolyTerra™ PLA sold, One Tree Planted, a non-profit planting organization will plant a tree local to where one spool sold. Up to now, over 140 thousand various types of trees have taken deep roots in several continents including Asia, Europe, Oceania, North America, and other regions. According to data shown on One Tree Planted, a sapling will need 5-10 years to reach its maturity and one mature tree can absorb an average of 22lbs of carbon dioxide per year. Therefore, within one year, Polymaker and its PolyTerra™ PLA customers will effectively remove over 2.2 million lbs of carbon dioxide from the atmosphere.
The growing plantation of trees will suck in greenhouse gases and cool the earth's temperature in the long run. As natural friends of mankind, trees work as the perfect purifier of air and water and provide habitat for more than 80% of terrestrial animals.
Ⅳ Cutting plastic waste, Polymaker develops 3D printing filament Polymaker™ PC-r through recycled waste plastics.
Moreover, Polymaker combines ecosystem protection with the recycling of plastic products.
Based on the conception of recycling discarded plastic, Polymaker collaborated with Covestro, a globally leading material supplier, in developing a polycarbonate filament for 3D printing. This material is named Polymaker™ PC-r, which selected raw materials on 19-liter bottles from Chinese water supplier Nongfu Spring. These discarded water bottles contain polycarbonate in a fairly pure form. Covestro blends the plastic waste with virgin material to yield a polycarbonate base that can extrude into filaments for use in electronics automotive and other industries. Compared to virgin material, filaments using recycled material have more advantages. Firstly, it produces a lower carbon footprint. The single-sourced material also eliminates the need for prior plastic sorting and identification that save manual labor hours. Secondly, the abundant source of raw materials comes from mineral water buckets that have high purity can be recycled cost-effectively. The above elements demonstrate the economic value of this technology upgrading, while at the same time, the development of Polymaker™ PC-r also stands up to the test of marketing requirements. By combining 3D printing technology in industrial production, Polymaker™ PC-r can provide strong support for brands looking to build sustainable supply chains. Endured with relevant professional tests such as blue Angel and EPEAT (Electronic Product Environmental Assessment Tool), this filament’s durability has met up to the production requirements of specific industries. Thus, it applies to various demands.
Polymaker is working on
more substantial solutions on ecosystem preservation and sustainable development and will move forward on optimizing production lines and developing sustainable products, that is the multi-year plan for all.
AMESOS and Polymaker announced today a strategic partnership to co-develop high-speed fused filament fabrication (FFF) based 3D printing solutions.
Polymaker is a well-known name in the 3D printing industry – the Shanghai-based company develops and manufactures a large variety of materials for material-extrusion based 3D printing. Their products have won multiple awards and are widely used by a large spectrum of professional and industrial users. AMESOS, on the other hand, was formed recently as a spin-off of Akribis Systems, a Singapore-based, global leader in direct drive motors and motion control technologies founded in 2004. Despite being a new entrant, the teams at AMESOS and Akribis have been working on 3D printing for the last 5 years. The deep technical capabilities in motor design and motion control from Akribis allowed the team to design 3D printing systems in ways that are very different from the status-quo.
It is widely known that speed is a key bottle neck for FFF based 3D printing. It is a major barrier to the wider adoption of the technology, particularly in series production applications. Despite this industry consensus, progress in improving the printing speed of FFF has been rather limited over the years. The key reason for the lack of progress, is that the problem is intrinsically hard. It requires multiple domains of technical expertise working in a concerted effort.
“We started by trying to solve the problem alone,” says Tommy Huang, the Co-Founder of AMESOS, “but very soon we realized we are only part of the solution and desperately need many other areas of expertise.”
“The process complexity of FFF 3D printing is orders of magnitude higher than traditional polymer processing technologies,” says Dr. Xiaofan Luo, President of Polymaker, “therefore to really tackle this problem we need some major paradigm shift in the R&D process.”
The goal of this partnership between AMESOS and Polymaker is to co-develop a high-speed FFF based 3D printing solution, which they call “FFF 2.0”. “We will take a process-centric and bottom-up approach,” Xiaofan explains, “we will start with studying and defining the process, which then guides the printer design and material development, not the other way around. And this is very different from how R&D is done today in many printer and material companies.”
To tackle the process complexity, Polymaker will also bring in Helio Additive, a new startup company which Polymaker helped co-found. Helio Additive is developing a unique software solution that combines physics-based simulation and data science to guide the development and optimization of printing processes. Helio’s software tool will be a vital part to the success of this partnership.
“We have already seen some promising preliminary results that have proved the viability and effectiveness of our partnership model.” Says Tommy, referring to the Blade 1 system, the first-generation 3D printing system AMESOS will introduce to the market later this quarter. Initial results show a consistent, over 60% reduction in printing times over existing FFF printers. This is achieved with no compromise in the overall printing quality. Furthermore, with the custom developed material by Polymaker, the mechanical properties are on par or even higher under high-speed printing.
“What we want is to achieve consistent high-speed printing without sacrificing part quality or properties,” says Tommy, “this is very different from some false claims you see in the industry – yes you can print faster but this comes with other, unspoken compromises. What we want is true speed improvement.”
“AMESOS and Polymaker have a shared vision about the future of FFF in series production,” says Xiaofan, “we are still in the beginning and there is huge, untapped potential to be explored.”
AMESOS and Polymaker are currently working on a multi-year technical roadmap. Their ultimate goal is to make FFF based 3D printing a competitive, widely adopted production technology.
About AMESOS
The Amesos team encompasses strong knowledge and experience in precision equipment design, hardware, software, processing parameter and industrial applications. Core knowhow in motion control and direct drive enable Blade Series to manifest both speed and precision at the same time. With global offices in Singapore, China, USA, Germany, Israel, Japan, Korea, Malaysia and Thailand, synergy with strategic partners, Amesos can offer a “FFF 2.0” turn-key solution in series production applications, focus on semiconductor, robot, auto, defense, aerospace, health care, energy and other industries.
About Polymaker
Polymaker is a developer and manufacturer of 3D printing materials committed to innovation, quality and sustainability. Its award-winning product portfolio has enabled numerous individuals and companies to better create and make. Headquartered in Changshu, China, Polymaker has multiple office locations in Shanghai, Utrecht and Houston ready to serve customers across the globe.
Polymaker recently announced the official completion to a round of funding that garnered them over 100 million CNY in investments led by IDG Capital, a leading global VC firm, followed by Sharelink Capital, Skytrace Capital, and Suzhou TechWisdom Capital.
Polymaker is a 3D printing company committed to developing new material technologies to drive in-depth applications of 3D printing in various industries. They are widely recognized as a top innovator and supplier of material extrusion-based 3D printing materials, with their products being used all over the world in a large variety of fields including automotive, aerospace, industrial manufacturing, medical devices, and consumer products.
Since its founding, Polymaker has constantly been making technical innovations with its R&D processes. In 2017, Polymaker was awarded the Material Technology Innovation Award by TCT, a world’s leading authority in additive manufacturing, as well as the Material Company of The Year Award by 3D Printing Industry, a top online media company and long-time industry observer in 3D printing. In the same year, the company launched a new product family, Polymaker Industrial, to further refine its positioning in the industrial market. In 2019, Polymaker successively launched a series of high-performance 3D printing filaments covering a wide variety of engineering materials including Nylon, polycarbonate, and fiber-reinforced composites. At the same time that pellets were gaining popularity with large-scale construction and manufacturing industries, PolyCore™, a new family of pellet-based 3D printing materials developed by Polymaker, was successfully used for the construction of three 3D printed landscape bridges in Shanghai, Quanzhou, and Chengdu. In 2020, Polymaker received the highly prestigious Ernst & Young-Fudan China’s Most Promising Enterprise Award.
Polymaker actively participates in top exhibitions for additive manufacturing in China and abroad, including TCT, Rapid Show, and Formnext, for promoting cooperation with other industries while improving its brand awareness.
Figure 1:The world's first 3D printed production car by XEV using Polymaker materials
Figure 2:3D-Printed Pavillion by JZ3D using Polymaker materials
Figure 3:Polymaker exhibit - 3D Printed Jewelry (Designer: Laura Jonas)
Figure 4:Polymaker exhibit - 3D Printed Vase
Polymaker is about to enter its tenth year in the 3D printing industry, and this new round of funding will be used to expand the team, product R&D, and production capacity. By creating a comprehensive and innovative R&D methodology, they aim to meet the growing market demand for diverse, high-performance materials through material innovation, production optimization, and product standardization.
Figure 1:One of the 3D printed Landscape Bridges by Polymaker in cooperation with Shanghai Construction Group and Shanghai Kuying Technology Co., Ltd
Figure 2:Metal parts produced with Polymaker's PolyCast material (credit: LulzBot)
Figure 3:Full electric superbike by Sarolea using multiple 3D printed parts, such as the battery housing, and air ducts made by Polymaker materials
Dr. Luo Xiaofan, the CEO of Polymaker, said “IDG is a great company that has helped reshape many industries, and we are excited to enter this partnership with IDG. I look forward to further driving the development of 3D printing to penetrate more industries.”
Wang Xin, partner of IDG capital, said “As an emerging industry, 3D printing is developing rapidly and constantly realizing breakthrough applications for traditional industries. Polymaker is currently focused not only on the production of 3D printing materials, but also the application of 3D printing materials in various industrial fields. IDG capital is confident and excited about Polymaker’s future with its core technologies and R&D capabilities, rapidly expanding market shares, and exploration of applications for various 3D printing technologies in the industrial sector. We look forward to seeing Polymaker’s innovations reshaping traditional manufacturing in the near future.”
After releasing PolyTerra™ PLA on cardboard packaging earlier this year, we received many compliments from our customers praising our efforts to be eco-friendlier. Many customers loved our new cardboard spool both for its usability and disposability.
Fig.1 New Cardboard Spool
To further our efforts and establish a consistent brand image that contributes more on environmental protection, we decided to upgrade the whole Polymaker range from plastic spools onto cardboard spools!
Not only will this remove tonnes of plastic waste from the environment, it also provides a practical cardboard spool that is easy to rip apart after use and can be recycled in your regular paper recycling.
We are phasing in the new packaging while using up our plastic spools to save resources and avoid waste. This notification aims to avoid any confusion for our customers and we cannot guarantee which packaging you will receive during our transition stage. What we can guarantee is that you will receive the same high-quality filament that you expect from Polymaker.
Features of the New Spool
The new cardboard spool features a thick 4mm pressed and die-cut recycled cardboard spool face, glued onto a strip-rolled section of cardboard tube. The thickness of the cardboard ensures your filament is well protected and the spool can roll very efficiently on all designs of spool holder both internally or externally mounted.
Fig.2 Thick Cardboard Spool Face
On the front of the spool, you’ll find a QR code which will take you to the product information sheet on www.polymaker.com Here you can also find printing profiles, TDS, SDS, and all other documentation relevant to the filament.
Fig.3 QR Code for Product Information
The cardboard used to make the spool and box comes from 100% recycled sources.
Fig.4 Smaller Box, Larger Labels
On the box, we have created a new label with larger text making it easier to identify the material, diameter, and color of the filament. On the spool, we feature some basic printing information and the rough filament weight guide, a feature pioneered by Polymaker and followed by many filament manufacturers.
Fig.5 Weight Gauge
One of the biggest challenges for us was sourcing a glue that can withstand the high temperatures necessary to dry some of our filaments. Our nylon range, for example, needs to be dried at 100°C and the naturally sourced glue that holds our cardboard spools together has the ability to withstand those temperatures without melting.
Fig.6 Improved Winding
Our new product portfolio brand structure and visual identity set the tone for the future of our business – an organization that is customer-oriented, pioneering, creative, and responsible. We hope to create a diverse and innovative experience for our customers to help shape the world around them with 3D printing.
Thank you once again for your support and trust!
Polymaker
Polymaker unveiled the "Liuyun Bridge", a 3D printed polymer bridge built jointly by Shanghai Construction Group Co., Ltd., Polymaker, and Shanghai Kuying Technology Co., Ltd., in Yimahe Park, Longquanyi District, Chengdu in 2021. Inspired by the free-flowing shape of the stagecoach and dancing silk, “Liuyun Bridge” achieves bold innovations in landscape design using new technology and materials unlike ever before while managing to overcome many obstacles in the 3D printing process. Polymaker was largely responsible for the conception and completion of this project, providing the materials and spearheading the exploration of landscape bridge design.
The printing process of "Liuyun Bridge"
Innovating on the printing process, the “Liuyun Bridge” takes advantage of Polymaker’s materials and creatively employs new technology to complete its construction not only quicker, but also with higher quality. The bridge manages to shorten its construction period using the Kuying Tech’s 5-Axis Milling and Additive Manufacturing Integrated Machine (BGAM), which allows for uninterrupted 3D printing to continuously occur at all hours of the day without any manual interaction, finishing the printing of “Liuyun Bridge’s” main components in only thirty-five days.
Polymaker guarantees the bridge’s stability and safety for years to come with their polymer pellets PolyCore™ ASA-3012, a material with excellent anti-aging. Another new method used to improve the printing process, closed-loop printing ensures there are minimal deformations by monitoring the temperature of the material during the printing process. The “Liuyun Bridge” consumes several tons of materials to finally complete its construction by printing segmented components to be assembled on site. Heavily dependent on Polymaker and their materials, “Liuyun Bridge” is a one-of-a-kind landscape bridge that only found its success through Polymaker.
A tremendous feat for 3D printing like the “Liuyun Bridge” never could have been accomplished without the collaboration between Shanghai Construction Group Co., Ltd., Polymaker, and Shanghai Kuying Co., Ltd. The actual design for the bridge was a product from both Shanghai Construction Group Co., Ltd. and Polymaker while Shanghai Kuying Co., Ltd. was responsible for the technology that let the material reach its fullest potential, crafting the bridge’s components with few errors and in an extremely short amount of time. However, Polymaker’s PolyCore™ ASA-3012 laid the foundation for this incredible achievement in 3D printing as the material made the design feasible in reality and continues to support its everyday use.
Materials used for “Liuyun Bridge”
The “Liuyun Bridge” used many new methods specific to Polymaker’s material to expand on the bridge’s performance. As the optimal material for the bridge, PolyCore™ ASA-3012 has mechanical properties suited for outdoor use and works specifically for large 3D prints, enhancing their dimensional stability and interlayer adhesion. Currently, most additive manufacturing technologies result in residual stress and warpage when using the fused deposition molding process. However, “Liuyun Bridge” incorporates a multi-factor analysis method, controlling ambient temperature and the three-stage melting of materials with different parameters like temperature, glass transition temperature, and single-layer printing time, to prevent any warping or deformations caused by rapid cooling.
During the printing process, heating the workspace before and after printing strengthens the layer-by-layer adhesion of the 3D printed materials, further reducing any possible problems with the printed components. Allowing the design of “Liuyun Bridge” to be fully realized, the high-precision five-axis CNC processing system of Kuying’s BGAM removes the typical margin of error reserved for printing deformations and heightens the accuracy of segmented printing components. With Polymaker’s PolyCore™ ASA-3012 being so advantageous, it solves many previous printing issues while still bolstering “Liuyun Bridge’s” stability and structure.
“Liuyun Bridge” is not the first bridge to use 3D printing technology though. Polymaker has worked in the construction of a few other 3D printed bridges, both at home and abroad, to realize new breakthroughs and accomplishments on each of their projects.
Polymaker’s 3D printed bridges in China
Shanghai Taopu Central Park Bridge
In 2019, China’s first composite landscape bridge was constructed in Shanghai Taopu Central Park by Shanghai Construction Group Co., Ltd., Polymaker, and Shanghai Kuying Technology Co., Ltd. As the first composite landscape bridge with one-time molding and a multi-dimensional curved surface, the Taopu Central Park Bridge breaks through the shackles of traditional bridge design and frees the landscape bridge to be more flexible and diverse in space. Like with “Liuyun Bridge”, the Taopu Central Park Bridge owes its conception and dynamic shape to Polymaker and their materials.
The printing process of this 3D printed landscape bridge went through nearly one hundred printing tests to be continuously optimized. The super-large gantry 3D printer, jointly developed by Shanghai Construction Group Co., Ltd. and Kuying Technology Co., Ltd., allows for more diverse printing of larger sizes while still improving the printing’s accuracy. The Taopu Central Park Bridge is also composed of Polymaker's PolyCore™ ASA-3012 material, so the bridge can withstand long-term exposure to the sun and rain.
Quanzhou Bridge
Polymaker installed China’s second 3D printed bridge in the ecological belt of Baiqi Lake in Quanzhou, Fujian in 2019 as the second collaboration between Shanghai Construction Group Co., Ltd., Polymaker, and Shanghai Kuying Technology Co., Ltd. Spanning 17.5 meters, the Quanzhou Bridge also uses Polymaker’s PolyCore™ ASA-3012 material for its body and drastically improves on the manufacturing time of traditional concrete grouting, completing its construction in only five weeks.
With the bridge’s manufacturing saving a considerable amount of time, it continues to compete with traditional grouting by providing strength that can withstand a pressure of two kilonewtons for each square meter, guaranteeing its ability to carry any amount of traffic. The Quanzhou Bridge utilizes a segmented design, unlike the Taopu Central Park Bridge, allowing its segments to be connected through a unique link mechanism to meet necessary mechanical requirements. Together, Polymaker's PolyCore™ ASA-3012 and the BGAM print the different components of the bridge to be assembled and painted for the finished construction, like with the printing process of the “Liuyun Bridge”.
The future of 3D printed bridges
Polymaker plays a role throughout the entire process of their 3D printed landscape bridges, covering many different facets from modeling, construction, and conception to data design. 3D printing technology truly emphasizes the "link of artistic inspiration with the power of science and technology" by pushing both sides to reach a product that stands above expectations. Polymaker’s application of 3D printing technology in landscape design greatly expands opportunities for technological innovation and exploration in the industry.
With 3D printing technology only continuing to grow, it has become an important consideration in constructing footbridges and large-sized printing quicker, with more cost effectiveness, and in a sustainable manner. Large-sized printing solutions are becoming more and more popular in different fields too, and Polymaker wants to fuel their growth by actively developing and producing materials that can bring ambitious projects to reality.
Without the material Polymaker has been creating, 3D printed bridges would never be as developed as they are now because Polymaker’s material not only provides the flexibility to meet any design’s needs, but also the strength to sustain the bridge for many years. Polymaker advances the world of 3D printing in more ways than only with their materials though. Their passion to push the industry and venture into unexplored territory has given 3D printing new capabilities and unimaginable possibilities.
Shanghai Construction Group Co., Ltd.:
Shanghai Construction Group Co., Ltd. is a leading enterprise in China's construction industry, ranking among the world's top 500 companies. Over the past sixty years, Shanghai Construction Group Co., Ltd. has repeatedly set records in the history of engineering construction in China and even in the world. It has contributed to many excellent projects in more than 100 cities across the country and in more than 30 countries and regions around the world. In recent years, Shanghai Construction Group Co., Ltd. has made every effort to promote national development, strengthen the synergy of the entire industry chain, and continue to form new commanding heights in business areas such as urban renewal, water conservancy, environmental governance, digital industrial construction, and construction services. They are now accelerating construction to become a widely acclaimed service provider for the whole life cycle of construction.
Shanghai Kuying Technology Co., Ltd.:
Shanghai Kuying Technology Co., Ltd. is a high-tech enterprise specializing in the research and development of super-large 3D printing solutions. The company adheres to the concept of "exploring future manufacturing methods" and is based on the innovative model of "integration of addition and reduction of materials, research and development of new materials, and intelligent control" in order to help manufacturing companies reduce costs and improve efficiency. The company’s existing intelligent equipment products include the Tech’s 5-Axis Milling and Additive Manufacturing Intergrated (BGAM), the high-speed pellet printer (SGAM), and the robotic additive manufacturing system (BRAM). These main products are widely used in architectural landscape, aerospace, shipbuilding, rail transit, energy, automobiles, medical products, and many other industries.
Polymaker transitions all filaments onto 100% recycled cardboard spools
Reducing plastic waste in 3D printing
Polymaker, a leading producer of 3D printing materials announced today that filament production has ceased on all plastic spools. Moving forward, Polymaker will produce all filaments on a 100% recycled cardboard spools. This move aims to reduce plastic waste in 3D printing to create a more environmentally friendly product with packaging which can be easily recycled after use.
“Sustainability is a top priority for Polymaker, and I am glad to see our team taking this important initiative. We will continue the innovation to make all our products more sustainable.” – Dr. Xiaofan Luo – Founder of Polymaker
- The new cardboard spool features a thick, 4mm pressed and die cut cardboard spool face, glued onto a strip rolled section of cardboard tube. The thickness of the cardboard ensures the filament is well protected and the spool can roll very efficiently on all designs of spool holder both internally or externally mounted.
"Polymaker’s adoption of cardboard spools is in agreement with circular economy principles such as decoupling from petrochemical-based plastics and creating an after-use economy for recycled materials with their use of recycled fiber. Polymaker has long demonstrated these circular economy values, most recently with the launch of their PolyTerra™ filament, made from renewable biobased Ingeo™ biopolymer, with which they piloted the use of these cardboard spools. We are proud of our partnership with Polymaker and their progress towards environmentally friendly and sustainable practices in 3D printing." - Dan Sawyer - Natureworks
The new spool features a QR code which takes customers to the product information sheet on www.polymaker.com alongside: printing profiles, TDS, SDS and all other documentation relevant to the filament. The paper product information sheet will no longer be shipped inside the packaging further reducing waste.
PolyMide™ PA12-CF: High stability nylon filament for 3D printing
PolyMide™ PA12-CF is a brand-new engineering filament offering high stability in both printing and application, delivering predictable mechanical properties regardless of the operating environment. PolyMide™ PA12-CF achieves this through its base polymer, nylon 12, which displays greater moisture stability when compared to common nylon 6 filaments. This means that PolyMide™ PA12-CF printed parts display minimal change in mechanical properties from the dry state to the wet state, therefore, more predictable mechanical properties in final printed parts. PA12-CF features 10% chopped carbon fibers which add strength and stiffness while also lowering the coefficient of thermal expansion, these characteristics, paired with Polymaker’s Warp-Free™ and Fiber Adhesion™ technologies provide an easy to print filament with extremely desirable properties.
Fig.1 Steering Wheel Core and Mould
The main difference between PA12 and PA6 is moisture stability. The longer PA12 polymer chain is much more resistant to moisture absorption and will reach moisture equilibrium at a lower % than PA6 filaments. Less moisture absorption means that there is less change in mechanical properties from the dry state to the wet state.
Water molecules are attracted from the surrounding air to the polyamide matrix, forming a polar bond onto the polymer chain. This water molecule acts as a plasticizer inside the nylon and while it decreases tensile strength and stiffness, it increases toughness and impact resistance. Unless your 3D printed parts operate in particularly dry environments or are post processed with a moisture barrier, its generally assumed that all nylon printed parts will end up in their wet state properties in every-day use. In many applications the wet state characteristics are more desirable and its common on many nylon injection moulding lines to eject moulded parts straight into a bath of water to condition them to wet state properties before leaving the factory.
In 3D printing filaments must be dry, otherwise, any moisture which is inside the filament will boil inside the hot end and rupture out of the side of the extruded plastic, this greatly decreases the mechanical properties, surface finish, layer bonding and produces some other undesirable printing characteristics such as stringing and oozing. Once the part is printed however, the nylon will absorb moisture from the air naturally and reach an equilibrium inside the part. For PA12-CF, the moisture equilibrium is roughly 1.5% by weight with other brand nylon filaments absorbing up to 5% and over, this has a more drastic effect on the final properties of the part and a noticeable difference in the performance from dry to wet states.
Fig. 3 Moisture Absorption Curve
As PolyMide™ PA12-CF displays a smaller shift in characteristics from dry to wet states it therefore delivers more predictable results in real-world applications. This allows you to design more accurately according to stress models and design loads, allowing you to further optimize your 3D printed parts.
Furthermore, the printability of the filament is also increased as the handling, storing, and printing of the material benefit from less moisture absorption. The filament is still hygroscopic, and we advise storing and printing PolyMide™ PA12-CF from inside the PolyBox™.
Fig. 4 Pipe Assembly Tool
Our material scientists have employed two Polymaker technologies into PolyMide™ PA12-CF. Warp-Free™ Technology, ensures no warping during printing, which is achieved by controlling the crystallisation behaviour of the polymer chains. Fiber-Adhesion™ Technology optimises the surface chemistry of the carbon fibers so they bond homogenously within the polymer matrix. This provides a greater strength on the z-axis when compared to competitor filaments whilst also offering easier printing on a multitude of 3D printers, desktop and industrial.
PolyMide™ PA12-CF features a heat deflection temperature of 131°C lending itself to operate in demanding environments where heat and stress are critical design factors. Paired with superior tensile strength and stiffness compared to other extrusion-based filaments, PolyMide™ PA12-CF is an engineering plastic that can outperform many other extrusion-based materials where strength to weight ratios are critical.
PolyTerra™ PLA is a bioplastic 3D printing filament designed from the ground up to create the next generation of environmentally friendly filaments. Polymaker has combined organic minerals with PLA which significantly reduces the plastic content producing a more environmentally friendly 3D printing material.
PolyTerra™ PLA prints exactly like PLA so you won’t have to change any print settings and the overhang and bridging capabilities can even surpass PLA. Featuring a wide printing temperature range of 190-230°C, PolyTerra™ PLA can plug and play on any extrusion-based 3D printers. The surface finish of 3D printed parts is uniquely matte which hides the layer lines, even when printing with large layer heights.
Polymaker has introduced four pastel colours alongside the ten regular colors which are all inspired by nature, offering a large choice of unique colors with a beautiful surface finish that’s bespoke to PolyTerra™ PLA.
The mechanical properties of PolyTerra™ PLA offer a wide range of potential applications as the material is tougher than regular PLA whilst still maintaining good stiffness similar to PolyMax™ PLA. This allows you to print anything from figurines to fixtures as the extra toughness that’s built into PolyTerra™ PLA does not affect the effortless printing capabilities.
PolyTerra™ PLA features easy support removal and 9 times out of 10 the support can be removed easily by hand without the use of tools. The support performs very well directly printing onto the build platform and also building from model. This allows users to push the boundaries of their machines and create ever more complex parts that are functional, tough and matte.
Post processing PolyTerra™ PLA is easy and the surface can be sanded without the plastic rolling over into long beads or chewing up. Printed parts can be sanded quickly and thanks to the softer surface power sanders can be used to quickly clean up and smooth large prints. The open pores on the surface allow paints to hold a strong bond onto the surface and due to the inert nature of the compound a wide range of paints can be applied.
PolyTerra™ PLA is wound on a fully recycled cardboard spool with recycled labels and outer packaging. The product information sheet has moved online, and any unnecessary paper has been removed from the packaging to cut down on waste.
To offset the carbon created to make and ship a spool of PolyTerra™ PLA, Polymaker will plant one tree for every spool sold, local to the place of purchase in partnership with OneTreePlanted.org. Once the tree hits maturity it has the ability to suck in 22kg of carbon dioxide each year massively offsetting the 4kg required to create a spool of PolyTerra™ PLA.
Polymaker introduces two new flexible filaments to the PolyFlex™ family offering faster printing and more flexibility. With the surge of 3D printed personal protective equipment (PPE) last year, flexibles proved themselves as a vital tool in the additive repertoire. 3D printing as a production tool demonstrated its potential by manufacturing locally when existing supply chains were constrained. Flexible filaments were a key player in this space and the 3D printed flexible face mask extender was invented to help medical stuff relieve strain on their ears. However, the printability and printing speed for flexibles remains limited, a factor which is determined by the melt index of the filament. Polymaker has developed these two new materials in partnership with Covestro to help boost the productivity of flexibles in the additive workflow.
PolyFlex™ TPU95-HF, is a High Flow (HF) TPU created from Covestro’s Addigy®️ family. The flow rate of flexible materials has always lagged far behind rigid materials which has been the limiting factor effecting the printing speed. TPU95-HF has a melt index of 9.3 (g/10min at 185°C) which is even higher than regular PLA. This allows for double the printing speed compared to other flexible filaments. TPU95-HF is designed specifically for high speed printing, combined with excellent UV resistance, PolyFlex™ TPU95-HF unlocks new applications for flexible materials in manufacturing.
The increased melt index allows the material to print faster. Contrarily to other TPUs on the market, TPU95-HF does not require a high temperature for high speed printing which results in better cooling, improved surface quality, steeper overhangs and finer details. PolyFlex™ TPU95-HF is available in black and white.
Ultraviolet (UV) light is a damaging factor for plastics and long exposure changes the properties of the material often leading to brittle, weak, and discolored parts. All plastics which operate outdoors are therefore at risk which is usually mitigated by post processing parts with a protective coating. The color difference of PolyFlex™ TPU95-HF is imperceptible after being exposed to fluorescent UV after 72 hours under ISO 4892-2 weathering test standard.
PolyFlex™ TPU90, created from Covestro’s Addigy®️ family, is a thermoplastic polyurethane (TPU) based filament designed to provide a high degree of flexibility without compromising on printing ability. Displaying a high resistance to ultra-violet (UV) light, this filament is perfectly suited to demanding applications in a variety of environments.
The shore hardness of this new TPU is 90A and the elongation of break of it is 638.8% ± 15.5. This delivers printed parts with incredible toughness that can stretch over 6 times before breaking. Displaying more ductility than PolyFlex™ TPU95 (shore hardness 95A) while maintaining the same printability thanks to an improved melt index. Its UV resistance opens the door to exterior applications where flexibility and durability are required. PolyFlex™ TPU90 is available in black, white, grey, and teal.
The 2 new TPU products are now available from Polymaker resellers, Polymaker website, and on Amazon (US).
Tips for using Polymaker TPU products:
Bed surface:
The PolyFlex™ family can be printed on glass, buildtak or similar products, PEI sheet or painters tape. Using Magigoo Pro Flex can improve the adhesion of PolyFlex™ TPU95-HF on the printing surface.
Direct and indirect drive extruders
Usually it is recommended to use direct drive printers to print TPU, however the high flow properties of PolyFlex™ TPU95-HF allows the material to achieve high printing speed even on indirect drive printer.
Dry box system
TPU is susceptible to absorbing moisture from the air which can subsequently affect the quality and mechanical properties of the final prints. We recommend using PolyBox™ to prevent moisture absorption. If the filament has absorbed moisture it can be dried at 70˚C for 12 hours in a convection oven.
What is a TDS?
a Technical Data Sheet (TDS) summarizes the performance and technical properties of a 3D printing material delivered through a series of standardized tests. This allows users to choose certain characteristics specific to their application when choosing the right 3D printing material. With the advancement of Polymaker’s industrial range, the TDS plays an integral role in highlighting each product’s varying characteristics and additionally, supplies the end-user with the basic print settings and tips to begin developing print profiles.
All TDS tests are conducted with 3D printed specimens in the X-Y and Z axis and depending on the characteristics of the material, specific tests and environments are used. This provides our end-users with the most accurate and appropriate information for their 3D printing application.
Why does Polymaker introduce a new version TDS?
Polymaker's products are increasingly being used in professional and demanding applications. Knowing what to expect from a material is critical to a parts performance and can aid in the behavioral analysis and curation of 3D printed parts in end use applications. We want to build on the information already found in our TDS and provide more in-depth technical parameters for our customers.
What’s new?
- Moisture Absorption Curve
The moisture absorption curve is determined by the nature of the material itself with some materials more susceptible to moisture ingress than others. The problem of moisture absorption will not only affect the 3D printing process, but also is affecting the properties of a 3D printed part after printing.
If a filament has absorbed moisture, when reaching a heated nozzle, the moisture heats up and rapidly expands rupturing the filament, causing bubbles and inconsistent extrusion. This can significantly reduce mechanical properties and layer adhesion causing print defects such as oozing, stringing and poor surface quality.
In order to solve this problem, Polymaker completely dries all products before vacuum sealing them in an aluminum foil bag with a desiccant. Polymaker also offers the PolyBox™ as a storage solution for all filaments during storage and printing.
To help users to understand how filaments absorb moisture, Polymaker has added the Moisture Absorption Curve into the new version TDS.
In the Moisture Absorption Cure, you can learn how a filament absorbs moisture under the standardized testing condition of 70% relative humidity at 23℃。
- Heat Deflection Temperature (HDT) Curve
There are different ways to illustrate the concept of “Heat Resistance”. Polymaker used to provide glass transition temperature, melting temperature, crystallization temperature, decomposition temperature, and Vicat softening temperature in the TDS. Now Polymaker has added heat deflection temperature (HDT) to further the understanding of heat resistance in a 3D printed part.
The heat deflection temperature is the measure of the temperature at which a polymer undergoes a certain amount of deformation under a constant load. The test is conducted by placing a 3D printed specimen under a constant load, while steadily increasing the temperature by 2 °C/min. The displacement is measured over a range of 10mm and plotted to create the HDT curve.
The heat deflection temperature is determined by the following test procedure outlined in ISO 75. The test specimen is loaded in three-point bending rig in the edgewise direction. The outer fiber stress used for testing is either 0.455 MPa or 1.82 MPa, and the temperature is increased at 2 °C/min until the specimen deflects 0.34 mm. This is similar to the test procedure defined in the ISO 75 standard.
Whilst comparable to HDT, the Vicat softening temperature differs by providing a testing method that simulates the point at which temperature softens the material’s physical properties enough for an external object under a set pressure to penetrate the outside surface of the specimen by 1mm.
What else?
Aside from Moisture Absorption Curve and Heat Deflection Temperature (HDT) Curve, Polymaker will also add light transmission, flame retardancy, chemical resistance, thermal conductivity, and heat shrinkage rage into future versions of the TDS.
Where to find the new version TDS?
You can find the new version TDS from the DOWNLOAD section of Polymaker website.
Anisoprint, developer of continuous fiber 3D printing technology for the manufacturing of optimal composites, has presented two new 3D printing materials developed by Polymaker — Smooth PA & CFC PA.
These new materials have been developed to work in tandem with the Composite Fiber Co-extrusion (CFC) technology at the heart of Anisoprint. This can deliver continuous fiber reinforcement within 3D printed parts which greatly improves tensile strength and stiffness allowing further refinement and practicality of end-use 3D printed parts.
The success of CFC 3D printed parts is dependant on the mating of material and fiber inlay to create a homogenous plastic part. The CFC PA provides the perfect interface surface with Anisoprint's composite fibers, while the Smooth PA delivers a higher quality surface finish for exterior perimeters and details. This combination delivers incredibly tangible 3D printed parts with a lustrous surface finish while benefitting from the added strength and stiffness of the continuous composite fiber.
"We see huge potential in CFC 3D printing, the ability to enhance 3D printed parts in this fashion allows an even greater degree of part optimization. When you hold one of these parts in your hands you really understand the benefits that the Anisoprint technology offers." - Luke Taylor - Marketing Manager, Polymaker
Besides the 3D printers, reinforcing materials and software, Desktop Anisoprinting includes:
- verified printing profiles, developed by Anisoprints application engineers team;
- and training courses from the experts with more than 10 years of experience in composite materials development.
In combination with Anisoprint’s science-intensive technology of continuous fiber 3D printing, Desktop Anisoprinting allows manufacturers to obtain optimal composite parts with the minimum risk of failure, wasting no time and money.
Printing profiles
Anisoprint’s engineers have developed and verified printing profiles for a wide range of plastics, that include ideal temperature, speed, layer thickness, cooling, and other settings. There is no more need to waste material for tuning, you can print perfect composite parts right away.
Composites basics online training course
Anisoprint technology was developed by engineers and scientists with decades of experience in composite materials manufacturing. Now you can use their knowledge to take special training courses. This way implementation of continuous fiber 3D printing technologies to your manufacturing process will be as if you’re working together with the composite materials experts.
‘Adopting new technologies is always a challenge, but it's the only way to compete and survive in the modern economy. We want to support our customers in this journey and help them to make it smooth. That's why we are launching Desktop Anisoprinting - there is everything you need to start 3D printing with composites and introduce yourself to the future of manufacturing’ — says Fedor Antonov, CEO of Anisoprint.
Desktop anisoprinting solution will be available for sale from the end of November. You can get a quotation at the company’s website: www.anisoprint.com
To learn more, join the webinar on the 15th of October where Fedor Antonov, Anisoprint CEO, will tell more about Desktop Anisoprinting. Register for free here:
https://us02web.zoom.us/meeting/register/tZ0odOitrD8tGNVowx6X19f9LeaFHP0vNBFE
Polycarbonate (PC) materials specifically designed for industrial 3D printers with a heated chamber
New materials bring strong mechanical and thermal properties to METHOD X 3D printer for a wide range of engineering applications.
BROOKLYN, N.Y., Sept. 17, 2020 – MakerBot, a global leader in 3D printing and subsidiary of Stratasys Ltd. (Nasdaq: SSYS), today announces that Polymaker, a leading provider of 3D printing materials, has qualified three polycarbonate materials for MakerBot LABS™ for the MakerBot METHOD X™ 3D printer.
Polymaker™ PC-PBT, PolyMax™ PC-FR, and PolyLite™ PC are available to print on the METHOD X 3D printer with the MakerBot LABS Experimental Extruder. This extruder turns METHOD into an open materials platform, enabling users to print with a wide variety of third-party materials on an industrial 3D printing platform. The latest material additions from Polymaker to the LABS portfolio aim to enable METHOD X users to harness the strong mechanical and thermal properties of polycarbonate (PC), while reducing problems such as warping and curling that typically occur when used with conventional desktop 3D printing machines.
Polycarbonate is a popular high-performance engineering material that possesses a unique balance of toughness, good light transmission, high heat resistance, and excellent electrical resistance. It is lightweight, has the ability to transmit light as effectively as glass, and withstand impacts better than other thermoplastics such as ABS. Due to these properties, PC materials are commonly used for functional prototyping and end-use parts in the production of automotive components, protective gear, medical device components, and exterior lighting fixtures.
However, polycarbonate can be challenging to print due to its ability to contract if it is cooled too quickly, which can cause warping and shrinkage of the printed part. Controlling the ambient temperature, such as with a heated chamber, is one of the most critical factors when printing polycarbonate.
The MakerBot METHOD X 3D printer is the only printer in its price class with a heated chamber that reaches up to 110°C, letting the parts cool down gradually to minimize curling and warping. METHOD controls how fast a part cools down during the printing process, allowing it to print polycarbonate and other advanced materials more successfully than typical desktop 3D printers that only have a heated build plate. In addition, with the moisture sensitivity of PC materials, Polymaker recommends using a material caddy, such as the Polymaker PolyBox™, to safeguard them from precipitation in the environment. MakerBot METHOD™ users can also use the Material Drying mode on the METHOD X to remove moisture from the materials.
"Polycarbonate is often the choice for parts that function in demanding applications. Its mechanical properties, flame retardance, and chemical resistance also allow engineers to push the boundaries of their 3D printed parts and experiment with new geometries,” said Xiaofan Luo, PhD, President of Polymaker. “Anyone who is serious about printing polycarbonate knows that a heated chamber is essential for printing large and strong complex parts. METHOD is bringing industrial capabilities to a desktop machine, and we think its users will really benefit from the material properties our PC range offers.”
“With its up to 110°C heated chamber, METHOD is a powerful and unique 3D printer platform for printing advanced engineering materials. The availability of Polymaker’s PC materials on METHOD offers allows engineers to print polycarbonate parts that they previously had to outsource to more expensive industrial 3D printers,” said Johan-Till Broer, VP of Product Development, MakerBot. “We are seeing increased interest in industrial materials as engineers advance from simple prototyping to 3D printing end-use parts. We are thrilled that Polymaker has qualified its industrial range of PC materials for MakerBot LABS.”
The addition of Polymaker polycarbonate materials brings the MakerBot LABS for METHOD portfolio of materials to nine and the total number of materials available on the METHOD platform to 19. The newly qualified polycarbonate materials from Polymaker include:
• Polymaker PC-PBT: This polymer blend combines the good chemical resistance of PBT (polybutylene terephthalate) with the strength and toughness of polycarbonate. Compared to PC resins and PC-ABS compounds, PC-PBT offers better resistance to chemicals, which enables printed applications where resistance to intermittent contact with fuels, oils, lubricants, or cleaners is necessary. It performs well under extreme circumstances, whether in contact with hydrocarbon-based chemicals or operating at subzero temperatures. Polymaker PC-PBT is a specialty material that maintains good toughness and natural ductile fracture behavior at low temperatures.
• PolyMax PC-FR: A flame retardant (FR) polycarbonate material, PolyMax PC-FR meets the UL-94 V0 standard, an important fire safety specification. The material displays excellent toughness, strength, and heat resistance, making it ideal for applications within the automotive, railway, and aerospace industries.
• PolyLite PC: PolyLite PC is produced using a polycarbonate resin specifically engineered for 3D printing. This material demonstrates a high modulus, making it ideal for applications that require good stiffness and light diffusion, such as outdoor light housings. PolyLite PC is available in transparent color, showing good optical clarity, rendering parts with an attractive crystal shine.
To further strengthen PC parts, Polymaker recommends annealing them right after the printing process to release the residual internal stress. The combination of METHOD’s heated chamber and annealing feature is designed to enable users to produce strong, manufacturing-grade parts. Polymaker materials can be purchased on the Polymaker site.
The MakerBot LABS extruder enables users to print with a wide variety of third-party materials on METHOD as an open materials platform, expanding the possibilities of applications. MakerBot offers a wide range of industrial materials through MakerBot LABS, and is continuing to identify additional advanced materials for the platform. Partners in the MakerBot LABS Materials Development Program include BASF 3D Printing Solutions, Jabil, Kimya, LEHVOSS Group, Mitsubishi Chemical, and Polymaker.
For more information, visit www.makerbot.com/method.
Polymaker is now offering PolyMax™ PLA GREY on a 3kg spool. You can find it from Polymaker’s resellers, Polymaker website, and also Amazon.
PolyMax™ PLA is produced with Polymaker’s patented Nano-reinforcement technology creating a filament that is much tougher than regular PLA while still keeping all the inherent printing qualities. Paired with Jam-Free™ technology, this material offers high strength parts that print perfectly on desktop printers. Engineers worldwide are already producing functional prototypes and working parts with PolyMax™ PLA.
The 3kg net weight enables continuous 3D printing without the need to change filament on large projects.
Grey now joins Black and White in the 3kg spool offering for PolyMax™ PLA.
July 8, 2020- On the first day of the TCT Asia exhibition in Shanghai, Polymaker and Covestro are jointly promoting their latest application - 3D printed fabric.
Covestro and Polymaker have been in partnership for years to promote high-performance 3D printing materials and to develop new 3D printing applications. This time, Covestro and Polymaker have jointly developed a new processing technology with the industry's top 3D printer manufacturers INTAMSYS and Raise3D to improve mass production and efficiency of 3D printed fabrics. The INTAMSYS FLEX 510 printer and Raise3D E2 printer are highly adapted for printing flexible materials which match the characteristics required for 3D printed fabric.
As 3D printing technology has been widely integrated into manufacturing, sport & leisure, medical and other fields. 3D printing is now offering new applications to the textile industry which offer both mass production alongside mass customization. 3D printing fabric may not only provide a more environmentally friendly solution, but also offers a new manufacturing method to the centuries old weaving process.
The 3D printed fabric jointly developed by Covestro and Polymaker takes a new approach to fabric manufacture by utilizing 3D printing to create a 2D fabric. This has more practical value other than waste reduction and can create patterns and style with use of computer algorithms. The 2D fabrics are then integrated into the existing workflow to create a customized 3D object such as: hats, shoes, bags, scarves, gloves and other clothing accessories.
Compared with traditional fabrics, 3D printing fabrics have many advantages, such as:
- Flexible production process with both mass production and customized production
Taking the production of 3D printed shoe uppers as an example, a complete upper could be printed in 30 minutes. A single 3D printer could produce 48 uppers 24 hours a day. And due to the characteristics of 3D printing technology, the design of each shoe upper produced in theory can be completely different. So, 30 devices could produce more than 10,000 fully customized uppers in a week.
Customization and mass production of 3D printed fabrics could go hand in hand for the first time.
- Unique textures and patterns
Relying on 3D printing technology, it is possible to make textures and patterns that are difficult to produce with traditional production methods, such as moiré, shape changes, and density gradient effects.
For this unique advantage, Polymaker has developed a software for the designing and slicing of 3D printing fabric.
- Digital design and automated production
The design of the 3D printed fabric can be fully digitized. Using the software developed by Polymaker, design styles such as shape change, density gradient, and random lines can be achieved through algorithms. While the design freedom is greatly improved, 3D printing technology can also be able to produce these complex styles.
The production process of 3D printing fabrics can all be handed over to 3D printers to achieve 24-hour automated production, without human intervention in the printing production process.
- Programmable property
In order to meet different elasticity, strength, and hardness requirements, in addition to the performance of the material itself, the texture design and printing method of the fabric also have a critical impact. Polymaker and Covestro have explored and developed valuable methods and experience in this regard using algorithms to generate organic texture where strength is needed while allowing more breathability in areas of less stress. This allows designers to optimize their fabric and create tailored 2D patterns in the most lightweight and efficient way, in high-stress applications such as the printing of running shoe patterns this advantage becomes obvious, where lower stress fabrics can make use of the aesthetic advantages.
In the selection of materials for the development of 3D printing fabrics, Polymaker cooperated with Covestro to select from the many varieties of TPU for 3D printing development. TPU (Thermoplastic polyurethanes) is a thermoplastic polyurethane elastomer, which has a wide range of hardness, wear resistance, oil resistance, transparency, and good elasticity. It is widely used in daily necessities, sports goods, toys, decorative materials and other fields in traditional manufacture.
Covestro TPU materials are rich in variety and performance. In response to different elasticity, strength and hardness requirements, Polymaker selected the corresponding TPU raw materials, formulated the 3D printing technology modulation formula, and developed 3D printing materials. The 3D printing fabrics released this time include 90A and 95A, two hardness materials.
- Integrated design and production to reduce waste in the production process
Facing the important global issue of environmental protection, 3D printing may better reflect its advantages. The integrated design of 3D printing could reduce the waste in the production process, and even target zero waste. In addition, in the production process of 3D printing, no water is used, no water is wasted, and water is not polluted. Compared with traditional production methods, the advantages of environmental protection could be significant.
Polymaker and Covestro have joined forces to vigorously promote the application of 3D printing in the textile industry and help the transformation and upgrading of 3D printed fabrics from artwork to industrialization.
Covestro Business Development & Partnering APAC Yvonne Wang (left) and Polymaker VP Hang Qu (right)
CEO of INTAMSYS Charles Han (middle), Polymaker VP Hang Qu (right) and Polymaker Strategic Business Development department senior manager Raymond Huang (left)
CEO of Raise3D Edward Feng (left) and Polymaker VP Hang Qu (right)
About Polymaker
Polymaker is a high-tech company specializing in 3D printing materials. It is committed to promoting 3D printing technology in various industries with leading technology, high-quality products and meticulous service. Polymaker products are widely used in automotive, aerospace, industrial manufacturing, medical, consumer and other fields by customers around the world.
About Covestro
With 2019 sales of EUR 12.4 billion, Covestro is among the world’s largest polymer companies. Business activities are focused on the manufacture of high-tech polymer materials and the development of innovative solutions for products used in many areas of daily life. The main segments served are the automotive, construction, wood processing and furniture, and electrical and electronics industries. Other sectors include sports and leisure, cosmetics, health and the chemical industry itself. Covestro has 30 production sites worldwide and employs approximately 17,200 people (calculated as full-time equivalents) at the end of 2019.
Polymaker has launched 20 kinds of 3D printing filaments. In order to make it more convenient for customers to try out Polymaker's materials, Polymaker launched three Sample Boxes (click to see more information) last year and received good responses from customers.
In the 2nd half of last year, Polymaker launched three polycarbonate materials. To make it easier for users to test them, Polymaker now officially introduces Sample Box 4 to the market.
The Sample Box 4 contains 5*50g samples(in 1.75mm or 2.85mm): PolyLite™ PC, PolyMax™ PC, PolyMax™ PC-FR, Polymaker™ PC-ABS, and Polymaker™ PC-PBT. It also includes a Magigoo PC sample. These samples require a 3D printer with enclosure for better part performance.
PolyLite™ PC
PolyLite™ PC is produced using a polycarbonate resin specifically engineered for 3D printing. It delivers good stiffness and heat resistance with light-diffusing properties.
PolyMax™ PC
PolyMax™ PC is an engineered PC filament combining excellent strength, toughness, heat resistance and printing quality. It is the ideal choice for a wide range of engineering applications.
PolyMax™ PC-FR
PolyMax™ PC-FR is a flame-retardant PC filament (UL94V-0/1.5 mm) displaying excellent toughness, strength, and heat resistance. This filament opens new applications in the automotive, railway and aerospace industries.
Polymaker™ PC-ABS
Polymaker™ PC-ABS is a PC/ABS polymer blend which offers excellent toughness and heat resistance while displaying good surface finish and good compatibility with metal plating.
Polymaker™ PC-PBT
Polymaker™ PC-PBT is a PC/PBT polymer blend which offers good heat resistance and toughness at low temperature (-20˚C/-30˚C). Polymaker™ PC-PBT also features good chemical resistance.
Magigoo PC
Magigoo is an easy to use 3D printing adhesive designed to reduce warping in FDM/FFF 3D printers. This is MagigooPC, the adhesive specifically designed for 3D printing in polycarbonate plastics. It offers a strong adhesion platform for polycarbonate-based filaments.
Sample Box 4 is now available in both 1.75mm and 2.85 on www.polymaker.com .Click the GET A SAMPLE button on the product page and Polymaker Amazon shop to try the materials.
Back in November 2013, Polymaker installed its first dedicated production line and developed a flexible 3D printing filament as the few flexible filaments available at the time had poor compatibility with different 3D printers. Polymaker fine-tuned the plasticity of the thermoplastic to produce a filament that was easy to print while producing soft and flexible printed parts. PolyFlex™ TPU95 marked the third product to join the growing Polymaker portfolio.
PolyFlex™ TPU95 is a thermoplastic polyurethane (TPU) based filament specifically engineered to work on most desktop 3D printers. It has a shore hardness of 95A and can stretch more than 3 times its original length.
Recently, we have seen a rapid increase in demand for flexible 3D printing materials used for various applications. In order to respond to market demand, Polymaker decided to launch two new colors of PolyFlex™ TPU95: BLUE & RED.
They are now available on www.polymaker.com and Amazon with both 1.75mm & 2.85mm diameters.
Sarolea is a revived Belgian motorcycle manufacturer that took on the historic Sarolea brand after the original company ceased production in the 1960’s. The revived brand now focuses solely on electric powered motorcycles, but at the heart of the company is the same passion of motorcycles that founded the original brand back in 1850.
Sarolea develop and manufacture their motorcycles from the ground up using in house technologies originally developed for track racing bikes. After gaining popularity of their designs on the race track, Sarolea decided to design a road going version of their first race bike the Manx 7. Sarolea have been using 3D printing technology at each stage of their production process and have established close technical relationship with Polymaker.
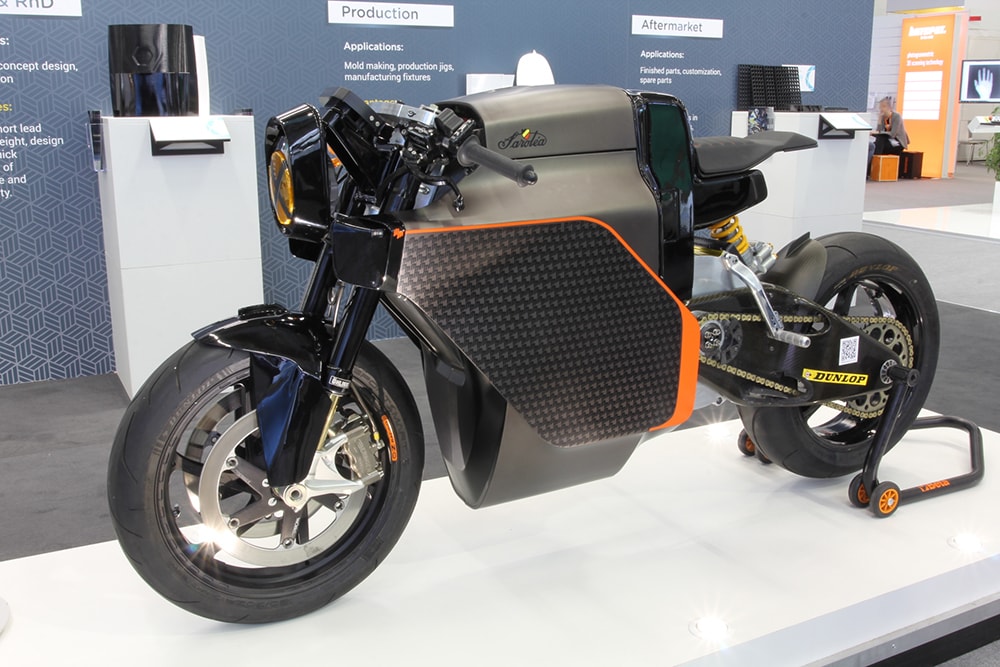
3D printing technology can bring huge advantages to the automotive industry in all aspects. Sarolea has integrated 3D printing into every stage of their production cycle, utilizing many different materials and their unique properties in the design, production and ultimately for the manufacture of parts that operate on the road and race bikes.
Stage 1: Design & RnD
Applications: Prototyping, concept design, design iteration
Advantages: low cost, short lead time, lightweight, design freedom, quick verification of appearance and functionality.
Description:
Both PolyMax ™ PLA and PolyMax ™ PETG are used for prototyping. For the Manx 7 electric superbike, the entire bodywork was prototyped using PolyMax ™ PLA. The printability, reliability and toughness play a role in this application. On the N60 model, Sarolea used PolyMax ™ PETG for bodywork prototyping. Compared to PolyMax ™ PLA, PolyMax ™ PETG is easier to sand and polish, offering an additional 20°C heat resistance compared to PLA. This allowed Sarolea to print and test body work with a professional finish.
PolyMax ™ PLA for bodywork prototyping
PolyMax ™ PETG for bodywork prototyping
Stage 2: Production
Application: mould making, production jigs, manufacturing fixtures
Advantages: fast and low-cost manufacturing of specific tools for custom parts, effectively reduce production cycle by printing in house. Print negative moulds for direct carbon fibre lay-up.
Description:
Sarolea are 3D printing moulds in PolyMide™ CoPA which they are using to produce final parts in carbon fibre. Both the Manx 7 and N60 have a carbon fiber monocoque chasis, this requires a number of intricate moulds that help with the lay up of the carbon fibre. PolyMide™ CoPA can withstand the high heat and pressures involved in vacuum curing process while the carbon fiber is baked in the autoclave. PolyMax™ PETG is also widely used to make production tools, jigs and fixtures necessary when assembling the bikes.
PolyMide™ CoPA mould
Stage 3: Aftermarket
Application: Printing production ready parts, customization and spare parts
Advantages: Print finished parts in advanced materials, provide full customization to customers on existing parts, keep digital database of spare parts.
Description:
Sarolea features a number of 3D printed parts in final production thanks to the advanced materials that Polymaker offer. PolyMide™ PA6-CF is used widely in the high velocity air flows and Polymaker™ PC-PBT in use as a cell holder within the custom-made batteries. PolyMax™ PC-FR offers a fire rated material to print fixtures and holdings for the many high voltage circuits and wires that are necessary to run the bike.
Polymaker™ PC-PBT cell holder
PolyMide™ PA6-CF air duct
Sarolea has found that Polymaker materials are an invaluable tool not only in prototyping but also in the manufacturing and final production of parts for their motorbikes. The technical partnership between the two companies allows Sarolea to push the boundaries of vehicle electrification.
Belgian based electric superbike manufacturer Sarolea has joined forces with Polymaker under a technical partnership.
Sarolea is a revived motorcycle brand that now focuses solely on electric superbikes. Their bikes are built from the ground up and they have been utilizing 3D printing in every stage of production. Sarolea is using a wide range of Polymaker materials in their production processes and sought to gain a closer relationship with Polymaker by using their application engineer's expertise in tuning and printing of parts. This has proven to be valuable for Sarolea as they explore the printing of new materials such as Polymaker PC-PBT in their battery configurations.
"We use the Polymaker filaments during the design process to check components and assemblies. We also use printing as rapid tooling to create moulds for carbon fibre components and thanks to the incredible high quality of Polymaker filament and the expertise of their engineers, certain components on our racing and production bikes are accurately printed. Components that are inhibitively complex and onerous to make with traditional production processes." - Rob Mitchell, Sarolea
Polymaker will be featuring the N60 electric superbike at the Polymaker booth during FormNext 2019 (Booth Number 1211-E111). Displaying three parts that represent stages of production in use at Sarolea. Furthermore, Rob Mitchell from Sarolea will be hosting an open talk during the show on the Polymaker booth, explaining Sarolea's relationship with 3D printing and the journey from prototyping to production.
Versatile materials for 3D printing
Polymaker, market leader in advanced 3D printing materials, announced the launch of three new polycarbonate-based 3D printing materials each with unique properties commonly used in the automotive industry. Polymaker has partnered with Covestro to bring these new materials to market taking formulas that are already well known to industry professionals and optimizing them for 3D printing.
The three new materials consist of:
- Polymaker™ PC-ABS – a blend of already commonly used 3D printing materials, polycarbonate and ABS. The advantages of this blend are high impact and heat resistantancy and easy to process. The polycarbonate boosts the heat resistance and toughness of the material while the ABS contributes to the good processing properties. This PC-ABS is also specialized for surface finishings, i.e. by electroplating and metallization, providing a good apporach for post processing.
Polymaker™ PC-ABS uses Covestro’s Bayblend® family as its base material which is a commonly used plastic in the automotive and information technology industry today.
- Polymaker™ PC-PBT – This polymer blend combines the good chemical resistance of PBT with the strength and toughness of polycarbonate. Polymaker™ PC-PBT performs very well under extreme circumstances whether in contact with hydrocarbon-based chemicals or operating at subzero temperatures. Polymaker™ PC-PBT maintains good toughness and its natural ductile fracture behavior at low temperatures.
Polymaker™ PC-PBT is created from Covestro’s Makroblend® family which is widely used in various industries. Compared to PC resins and PC-ABS compounds, PC-PBT has better resistance to chemicals, which enables printed applications where resistance to intermittent contact with fuels, oils, lubricants, cleaners is necessary.
- PolyMax™ PC-FR – creation from Covestro’s Makrolon® family, where the FR stands for flame retardant - the main feature of this polycarbonate-based compound. This base material achieves V0 performance in the UL94 flame retardancy test and benefits applications where respective material approval is required. This allows PolyMax™ PC-FR to be applied for battery housings, motor mounts in aerospace and other industries. Within the automotive and Electronics & Electrical industry, many professionals are well accustomed with such FR materials.
Polymaker has introduced its nano reinforcement technology that is featured in all PolyMax™ materials. This boosts the fracture toughness of the FR material and produces a flame-retardant filament that can still perform in demanding applications. PolyMax™ PC-FR uses Covestro’s Makrolon® showing a good balance between mechanical performance and safety, which has already been applied in electronic motorbikes, aerospace spare parts, and automotive production.
Polymaker boasts an ever-growing portfolio of cutting edge materials, with 17 unique products covering all your 3D printing needs. The Polymaker team wants to offer a convenient and cost-effective way for its customers to try and experience all of the different materials. These sample boxes allow users can find the most suitable filament for their application while also discovering new 3D printing materials.
Polymaker introduces Sample Box 1, Sample Box 2 and Sample Box 3 to the market.
Sample Box 1
Sample Box 1 contains 7 kinds of commonly used 3D printing filaments with each sample weighing 50g. All materials in Sample Box 1 are easy to use and are compatible with many 3D printers.
PolyLite™ PLA
PolyLite™ PLA is a high-quality PLA designed for reliability and ease of printing.
PolyLite™ PETG
PolyLite™ PETG is an affordable PETG filament with balanced mechanical properties and ease of printing.
PolyMax™ PLA
PolyMax™ PLA is an incredibly easy-to-print filament with improved mechanical properties, making it an excellent alternative to ABS.
PolyMax™ PETG
PolyMax™ PETG offers better mechanical properties than any other regular PETG making it a good candidate for a wide range of applications.
PolyFlex™ TPU95
PolyFlex™ TPU95 is a thermoplastic polyurethane (TPU) based filament specifically engineered to work on most desktop 3D printers. It has a shore hardness of 95A and can stretch more than 3 times its original length.
PolyWood™
PolyWood™ is a wood mimic filament without actual wood powder, which removes all risks of nozzle clogs. PolyWood™ is made entirely with PLA using a special foaming technology. It exhibits the same density and appearance as wood.
PolySmooth™
PolySmooth™ is a unique, easy-to-print filament designed for hands-free post processing. The surface can be smoothed with alcohol to achieve layer free models using the Polysher™.
Sample Box 2
Sample Box 2 contains 7 kinds of engineering 3D printing and supporting material, each weighing 50g. These products display better overall mechanical strength and thermal properties than the materials featured in Sample Box 1. Theses samples require a 3D printer with an enclosure or with dual extrusion capabilities.
PolyLite™ ABS
PolyLite™ ABS is made with a specialty bulk-polymerized ABS resin, which has significantly lower volatile content compared to traditional ABS resins. It delivers excellent printing quality with minimal odor during printing.
PolyLite™ ASA
PolyLite™ ASA is an alternative to ABS with improved weather resistance. Its UV resistance and excellent mechanical properties make it the perfect choice for real-life applications.
PolyLite™ PC
PolyLite™ PC is produced using a polycarbonate resin specifically engineered for 3D printing. It delivers good stiffness and heat resistance with light-diffusing properties.
PolyMax™ PC
PolyMax™ PC is an engineered PC filament combining excellent strength, toughness, heat resistance and printing quality. It is the ideal choice for a wide range of engineering applications.
PolyMide™ CoPA
PolyMide™ CoPA is based on a copolymer of Nylon 6 and Nylon 6,6. The filament combines excellent strength, toughness, and heat resistance of up to 180˚C.
PolyDissolve™ S1
PolyDissolve™ S1 is a water dissolvable support for PLA, TPU, PVB and Nylon based filaments from our portfolio. It is specifically engineered to have a perfect interface with these materials while also displaying good solubility.
PolySupport™
PolySupport™ is a breakaway support for Polymaker PLA based filaments. It has a perfect interface with PLA, strong enough to support it and easily removable by hand.
Sample Box 3
Sample Box 3 contains the first two Polymaker Industrial Range products – PolyMide™ PA6-CF and PolyMide™ PA6-GF, and each of them weighs 100g. The industrial range uses cutting-edge technologies to provide reliable, high-quality materials specially engineered for 3D printing in the industrial sector. These samples require a 3D printer capable of reaching a nozzle temperature of 300˚C and equipped with an abrasion resistant nozzle.
PolyMide™ PA6-CF
PolyMide™ PA6-CF is a carbon fiber reinforced PA6 (Nylon 6) filament. The carbon fiber reinforcement provides significantly improved stiffness, strength and heat resistance with outstanding layer adhesion.
PolyMide™ PA6-GF
PolyMide™ PA6-GF is a glass fiber reinforced PA6 (Nylon 6) filament. The material exhibits excellent thermal and mechanical properties without sacrificing the layer adhesion.
Now Sample Box 1, Sample Box 2 and Sample Box 3 are available in both 1.75mm and 2.85 on www.polymaker.com click the GET A SAMPLE button on any filament product page and Polymaker Amazon shop to try the materials.
The Indiana School for the Blind and Visually Impaired (ISBVI) have embraced 3D printing to a degree exceeding all other bodies of education with 3D printed models entering the curriculum in every subject taught on campus. Three years ago, ISBVI started a 3D printing Fab Lab at the school, managed by former student Jacob Ayers.
Dr. Matthew Maurer Ph.D. a professor at ISBVI instantly saw the value of 3D printing and helped Jacob to grow the 3D printing lab into a full-scale operation. With recent boosts in funding and donations, the ISBVI Fab Lab has grown from a janitor’s cupboard with Jacob operating his personal kit-built RepRap to a fully functioning print farm with over 200 3D printers in operation.
Jacob reached out to Polymaker seeking a donation of PolySmooth™ to help provide 3D printed models to the students at ISBVI. Polymaker we happy to donate five hundred pounds of PolySmooth™ 3D printing filament and 5 Polyshers to help post-process the models.
“We’ve been using PolySmooth almost exclusively for the past 2 years of the 3 years we’ve been running. We use the plastic because its: easy to print, it’s easy to post-process, it sands well, it files well compared to other plastics and its smoothable with the Polysher” – Jacob Ayers, Fab Lab Manager, ISBVI.
“When we started this project, the main aim was making models for the classroom, which is important because a lot of blind children see objects only in two dimensions, usually through raised lined drawings. When you put a 3D printed model in their hands, there is a eureka moment when everything falls into place and the subject makes sense for the students.” – Dr. Matthew Maurer, Ph.D. ISBVI
The ISBVI Fab Lab is now encouraging students to join workshops and learn about additive manufacturing as part of design & technology as well as in extracurricular activities. This allows students to gain knowledge of 3D printer operation, CAD software, and post-processing of materials.
“We see some game-changing employment possibilities and workforce development, we are very excited about the possibilities of training students in the additive manufacturing world. Students can learn from the materials and equipment that we have and then drive that knowledge into a career.” – Dr. Matthew Maurer, Ph.D. ISBVI
One project that the seniors are working on is a 3D printed face model of all the class members that are graduating this semester. In this project, the students are learning 3D scanning and file preparation, 3D printing and post-processing. The end result is a 3D printed object they can feel and touch to gain a deeper understanding of their classmate's appearance while also learning new skills.
“We can make the ultimate tactile friendly surface for someone who is blind or visually impaired. When we are creating a tactile object for classroom use, where the information being presented is vital. We don’t want to misconstrued print imperfections for detail. With the Polysher and PolySmooth, we can eliminate all of that with minimal work.” – Jacob Ayers, Fab Lab Manager ISBVI
ISBVI has also partnered with the Benjamin Harrison Presidential Site in Indianapolis, who are working on digitizing their collection of over 10,000 artifacts detailing the life and times of the 23rd President. Charles Hyde, President, and CEO of the Benjamin Harrison Presidential Site explains how digitizing museum artifacts can help educators access and utilize the collection in a compelling and engaging way. The ISBVI Fab Lab is helping print and process the artifacts to create a touch box of five selected artifacts from the Benjamin Harrison collection to give to the students at ISBVI.
“We are literally taking the collection and putting it in the hands of their students. So, we can explain what these five objects are and how they share the wider story of an American presidency.” – Charles Hyde – President & CEO Benjamin Harrison Presidential Site.
The students can then visit the home of Benjamin Harrison and experience the smells and sounds of the presidential home built-in 1874.
The Benjamin Harrison Presidential website have 3D scanned over 60 items, ranging from chairs to swords to top hats. All the OBJ files are free to download through their sketchfab collection.
Introducing PolyMide™ PA6-CF & PolyMide™ PA6-GF
Polymaker launch two new industrial materials to the 3D printing market offering the best in class for mechanical properties achievable from extrusion-based 3D printing. The two new materials are both fiber reinforced Nylon polymers that display, incredible strength and high heat deflection temperatures. This allows these new materials to function in more demanding environments and allows 3D printing to produce more practical functional parts. Both these materials feature Polymaker's latest development - Fiber Adhesion™ technology, boosting the layer adhesion of printed parts not only on the x-y axis but also on the z-axis.
PolyMide™ PA6-CF
PolyMide™ PA6-CF is a carbon fiber reinforced nylon (PA6) 3D printing material offering the highest strength, impact resistance and heat deflection of all Polymaker 3D printing materials. The carbon fiber reinforcement provides significantly improved stiffness, strength and heat resistance without affecting z-axis layer adhesion. Featuring a heat deflection temperature of 215°C, this material lends itself perfectly to functioning automotive applications where strength and heat resistance are required from the material.
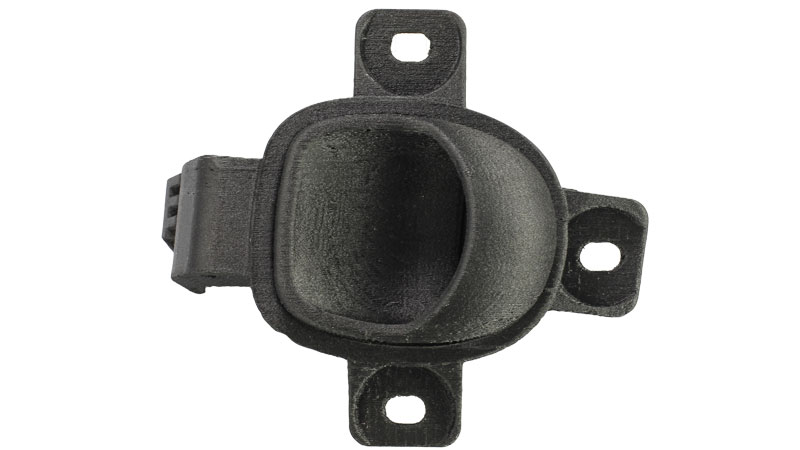
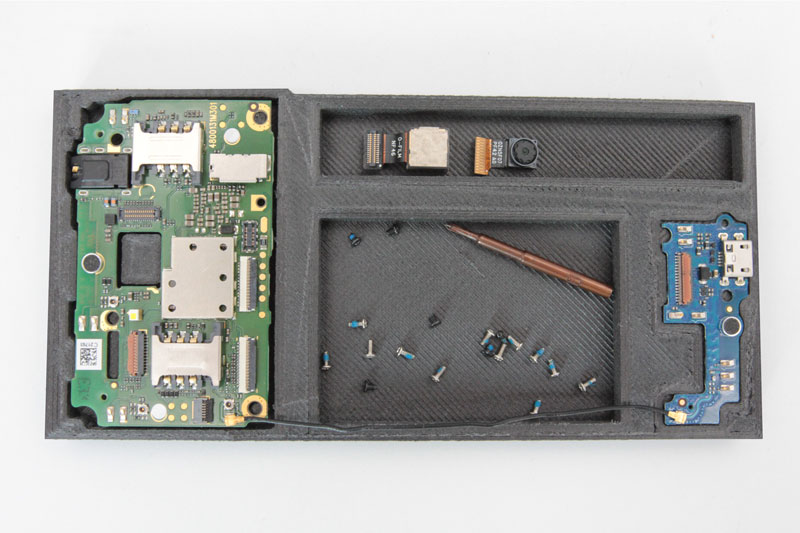
PolyMide™ PA6-GF
PolyMide™ PA6-GF is a glass fiber reinforced Nylon (PA6) that offers outstanding mechanical properties, namely, impact strength and stiffness. The material exhibits excellent thermal and mechanical properties without sacrificing the layer adhesion. PolyMide™ PA6-GF can be used to print parts working in a wide temperature range and has been utilized to create custom lab equipment working at temperatures as low as -190°C.
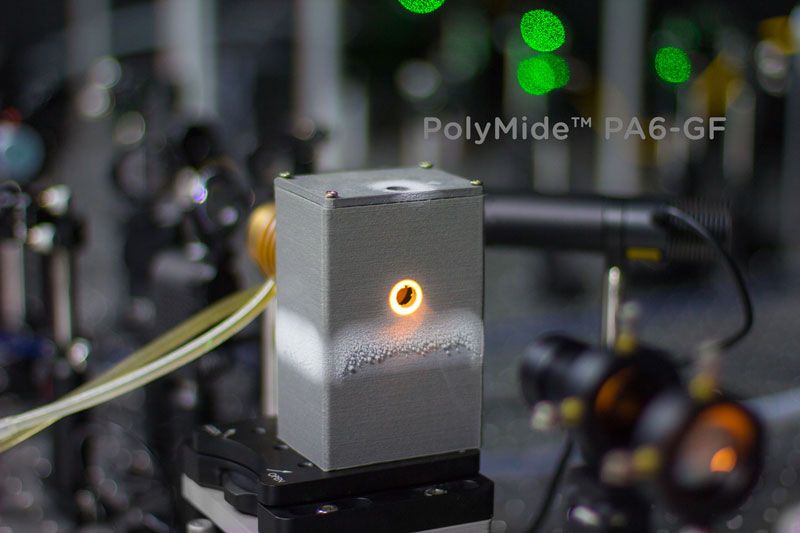
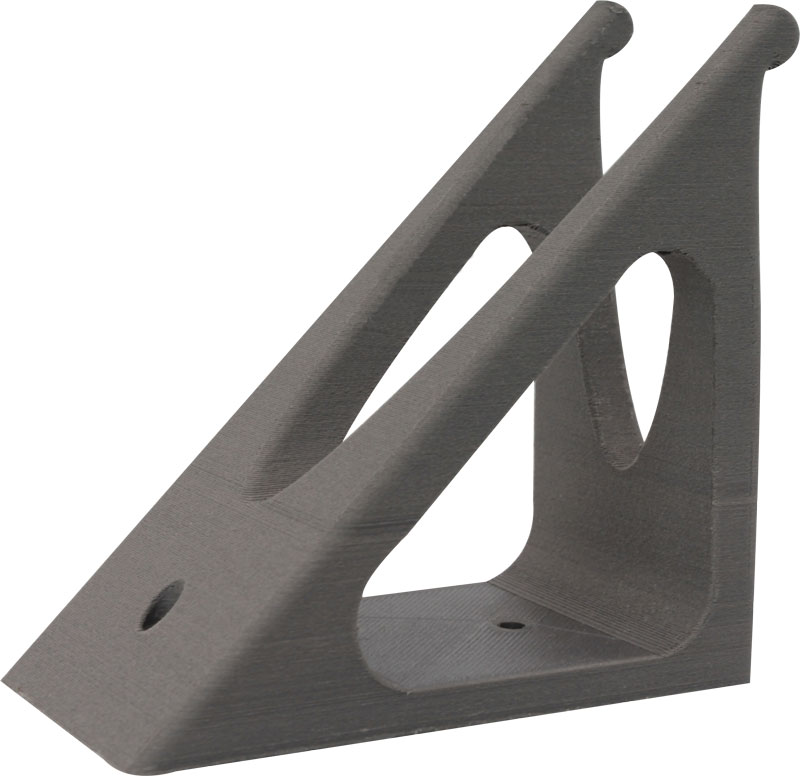
Fiber Adhesion Technology™
Fiber Adhesion™ Technology improves the layer adhesion of fiber reinforced materials, by optimizing the surface chemistry of the fibers to achieve better dispersion and bonding to the polyamide matrix. This results in better strength along the Z-axis and reduced mechanical anisotropy when compared to a pure Nylon PA6 printed parts. This in-house technology was developed exclusively to combat the problem of adding fibers to filaments. All other brand fiber reinforced materials show a decrease in z-axis layer adhesion when compared with their non-fiber reinforced Nylons producing a part that is only stronger on the X-Y axis but detrimental to the Z axis. Polymaker's new technology not only solves this problem but actually increases Z axis tensile strength creating more isotropic parts that are strong in every direction.
Polymaker announces the worldwide launch of PolyLite™ ASA, the fifth member of the PolyLite™ family rounding up the most popular 3D printing materials available today.
What is ASA?
ASA (Acrylonitrile Styrene Acrylate) is a thermoplastic with properties similar to ABS (Acrylonitrile Butadiene Styrene), which you might be able to guess from their full names as they share two monomers. ASA features good mechanical strength and thermal properties, but its outstanding feature is its weather resistance, which makes it an ideal candidate for outdoor-use. As a 3D printing material, ASA has already become a popular choice for automotive prototypes, in construction, and household applications. Now Polymaker has made it widely available for users to print parts that can withstand the elements.
About PolyLite™ ASA
PolyLite™ ASA is similar to ABS but with improved weather resistance. Its UV resistance and excellent mechanical properties make it the perfect choice for real-life applications or parts that will spend time outdoors. Weather resistance can be broken down into 3 factors: UV resistance, water resistance and thermal stability of which ASA outperforms many other plastics.
Key features:
- Good thermal and mechanical properties:
To break it down, PolyLite™ ASA performs better in both thermal and mechanical properties compared with general ABS filaments. It also features a Vicat softening temperature of 105℃ which slightly exceeds ABS.
- UV resistant
Most plastics tend to become brittle and their color turns yellow when exposed to UV radiation or sunshine. 3D prints of PolyLite™ ASA are UV resistant meaning their appearance and mechanical properties are not influenced negatively by UV light.
- Water resistant
PolyLite™ ASA is resistant to Environmental Stress Cracking. This allows printed parts to face the outdoors, high humidity and rain over long periods of time.
Advantages:
Polymaker developed and produced the 3D printing material for the world largest 3D printed pedestrian footbridge project completed by Shanghai Construction Group. Polymaker was invited to join this project from the very beginning to help develop a custom ASA 3D printing material for the bridge. During the whole processes, through plenty of tests and experiments, Polymaker has mastered the properties, compounding formulas and production techniques of ASA. As a result, PolyLite™ ASA gains several advantages over other ASA filaments:
- Tougher
PolyLite™ ASA has better mechanical properties and is tougher than other brand ASA filaments. (More information on the technical data sheet below)
- Better flow
PolyLite™ ASA is engineered to have the best in class melt index, PolyLite™ ASA filament can be extruded smoothly and easily.
- Better layer adhesion
With experience gained from the 3D printed bridge, our engineers have developed an ASA filament with exceptional interlayer adhesion. PolyLite™ ASA displays better layer-bonding performance than similar products.
Printing tips:
- Building platform surface
Similar to ABS, PolyLite™ ASA tends to warp during printing. To ensure the success of printing, we recommend using BuildTak® or Magigoo on the build surface.
- Turn off the cooling fan
Deactivating the cooling fan will reduce warping and delamination.
- Build an enclosure for your printer
A printing enclosure will help retain heat for large prints increasing the performance of the final parts.
Availability
PolyLite™ ASA is now available in both 1.75mm and 2.85mm in White and Black. You can find it on polymaker.com, Amazon, and through our Polymaker resellers.
PolyLite™ ASA Technical Data Sheet
Watch the video below to see the history of Polymaker from its humble beginnings to the present day. The Timeline follows all the product launches, technological advancements and key events that shaped Polymaker over the last 6 years.
Layer-Free™ technology, developed by Polymaker was first introduced on their breakthrough PolySmooth™ 3D printing filament which offered users the chance to remove all layer lines from their 3D printed parts via an easy post process. This development allowed PolySmooth™ parts to achieve a finish that is usually void from 3D printed parts and is something that is more commonly seen from traditional injection molding processes. The technology was later used to create an award-winning material which has revolutionized the investment casting industry.
Plastic parts have been around a long time before 3D printing technology was developed and the surface finish has largely been the same, smooth, glossy surfaces that were soft to touch and appealing to the eye. Plastic parts were made this way to aid the manufacturing process, as smooth parts would eject from injection molds much easier as the surface friction is minimized between the plastic part and the steel mold. This enabled a faster production of plastic parts with higher repeatability, and so it became the normalized process for injection molding and standardized surface finish for all plastic parts. This, in turn, shaped the public perspective of what they know as a plastic part, an object that is inherently smooth and glossy object as this was the standard finish for almost all of the plastic parts they have ever encountered.
The introduction of 3D printing changed the way in which plastic parts could be manufactured allowing plastic parts with new geometries that could not be achieved by injection molding. The process of printing vs injection molding is also widely different in the process. 3D printing split computer-aided designs into individual layers and printed each layer on a 2D plane which together formed a 3D object. This naturally changed the surface finish of plastic parts as many layers fused together created a horizontal texture which was not as smooth as the steel injection molds that had been used previously. The surface finish of a 3D printed part greatly depends on the layer height in which it was printed. Smaller layer heights create more detail as more 2D layers can be squeezed into a smaller space and larger layers iron out details as less texture can be dedicated to the shape. With a small enough layer height, a 3D printed part could be printed in a way that made it feel smooth to touch, however, the layer lines are hard to hide from the human eye as the light would reflect differently from the high and low points of the layers obviously setting apart a 3D printed object from an injection molded object. Printing at very small layer heights can create a smoother finish but it also drastically increases the print time as every layer added further increases the path that the extruder must follow. This means to achieve the same feeling as an injection molded part a 3D part would take a very long time to manufacture which is naturally inefficient to production.
3D prints can also be post-processed by sanding the layers until the high points of the layers match the low point and a smooth plastic is revealed underneath. This could then, in turn, be painted or lacquered to achieve a glossy finish achieving the aesthetic look of an injection molded part. This would recreate the image of plastic parts as consumers knew them, but the problems faced are that is it unfeasible to manufacture with such an intense workload in the post-processing of plastic parts.
Polymaker set out to create a technology which could eliminate all layer lines from a 3D printed object while also being a hands-free process requiring no extra work or man hours. The process developed was named Layer-Free™ technology and was applied to their PolySmooth™ 3D printing filament. PolySmooth™ is a polyvinyl butyral (PVB) based material which displays excellent solubility in isopropyl alcohol (IPA), this meant that when a 3D printed part is exposed to IPA, the layers could be quickly melted and fused together. The result is a smooth glossy object that looks like an injection molded part. The Polysher™ was created as a desktop device that could deliver IPA to 3D printed parts in a very controlled manner. The Polysher™ uses an ultrasonic nebulizer to create a cold mist of liquid IPA which is contained within a chamber. 3D printed parts made from PolySmooth™ could be lowered into the chamber and exposed to the fog of IPA which would gently melt the surface layers together. Polymaker found that this process was the best way of applying IPA to PolySmooth™ parts as it polished objects quickly but wasn’t too aggressive allowing details on printed object to remain after polishing.
The Polysher™ also allowed for recycling of IPA as all of the mist is contained inside the chamber, this allows it to re-condense and flow back into the reservoir situated at the bottom of the machine. The Polysher™ also has several safety features that allow it to work alongside your printer as a desktop machine. Firstly, the Polysher™ has a raising platform which elevates the polished object out of the IPA fog allowing users the chance to replace the platform and continue polishing. As the IPA fog is heavier than air, all IPA mist sinks to the bottom of the chamber where is can condense into a liquid and return back to the reservoir. This reduces the chance of any IPA mist escaping from the chamber and into your workplace. The Polysher™ also features two warning lights which monitor the seal of the chamber as well as monitoring the nebulizer. These warning lights cease all polishing processes until the issues have been addressed and a new polishing cycle can be started. The chamber seal light monitors the z-axis position of the platform while checking to see if the chamber casing is properly seated ensuring an airtight seal within the chamber. The nebulizer warning light monitors the frequency of oscillations from the nebulizer membrane. From this data, the Polysher™ can determine if there is an issue with the nebulizer such as, no IPA in the reservoir, the nebulizer becoming unseated or an over-heating problem, all of which will cause the nebulizer warning light and cease the polishing cycle.
The Polysher™ features two different lighting applications, one is the main chamber light which can be dimmed or turned off, the other is a nebulizer light which can cycle through 15 different colours to illuminate the IPA mist!
PolySmooth™ can be used in many different applications ranging from prototyping to production ready parts. Thanks to the unique surface that can be achieved once PolySmooth™ prints have been polished it allows designers to give the finishing touch to their prototypes producing a realistic finish that was unachievable before Layer-Free™ technology. Due to the excellent solubility of PolySmooth™ in IPA, it also allows for large parts to be chemically welded together as the IPA can be used as a solvent glue. Painting just three layers of IPA on the surface of PolySmooth™ will allow individual parts to be joined together allowing for colour combinations with hard edges without introducing any foreign bonding materials. Furthermore, the surfaces can then be polished together to create a smooth surface across join lines, this technique leaves a homogenous surface.
The toughness of PolySmooth™ 3D printed parts also increases after the polishing process, as all the exterior layers are bonded together. This fusing of the layers helps 3D printed parts take an impact and also improves their tensile strength. The Z-axis strength is also greatly increased as fractures along the layers are most common in 3D printed parts. Polished parts also are completely watertight which makes PolySmooth™ a great material for any part that will come in contact with water. This can range from useable vases to kitchenware, to medical applications, the smooth surface is also very easy to clean. The many layers in unpolished 3D prints provide lots of surfaces for dirt to get caught and for microbes and bacteria to grow, eliminating the layers greatly reduces the chance of a part becoming moldy when in contact with skin and water.
PolySmooth™ also allows for easy support removal and clean up, the majority of 3D printers currently on the market are single extrusion machines, as a consequence, complex geometries that require support must use the same support material as the build material. In some cases, this can cause issues as the support can leave scarring on the interface surface where the support meets the model. PolySmooth™ can be cleaned away very easily and any scarring that is caused by the support material can be completely removed once the part has been polished.
Laura Jonas is a Czech company creating unique fashion items using PolySmooth™ and the Polysher™ to achieve a finish that is aesthetically pleasing for their jewelry range. Combining glossy plastic parts with materials more traditionally found in jewelry making, Laura Jonas has managed to create a look that is unique and beautiful.
Martin Jonas – Head Designer says “I love working with Polysmooth and the Polysher, I used to spend a lot of time sanding and buffing my 3D prints to get them to the industry standard surface finish. Polysmooth has completely removed this process, now I can print our accessories and get repeatable results in the polysher with no extra effort.”
PolySmooth™ has added a new dimension to the Laura Jonas fashion accessories and is a good example of using 3D printing to create final products.
Polymaker has developed a second material which employs Layer-Free™ technology, this material is a specialized casting material that can replace wax patterns used in the investment casting process. The use of Layer-Free™ technology is combined with Polymaker’s Ash-Free™ technology to create a 3D printing filament that both molds very well and burns away very cleanly. The material is called PolyCast™ and has been engineered directly for the metal casting industry. The process of making metal parts from wax patterns is well established and PolyCast™ fits into the process very nicely without disrupting traditional processes. Instead of injection molding wax patterns which are then used to create a ceramic mold, users can 3D print PolyCast™ patterns replacing the wax while also eliminating any need for tooling or injection molding. Tooling is often the limiting factor when bringing new products to market as it is time-consuming and costly. PolyCast™ allows for faster iteration of design and is not constrained by volume numbers or large minimum order quantities. This major advantage of time and money has seen widespread adoption of PolyCast™ by foundries worldwide, without deviating from their well-established process, they can test new geometries and streamline production by adopting additive manufacturing and PolyCast™.
As previously mentioned PolyCast™ also has Layer-Free™ technology allowing the 3D printed parts to be polished to a smooth glossy surface, this greatly helps the molding process as bubbles can get trapped in between the layers causing defects in the mold which transfer to the metal parts. A typical investment casting process will go as follows. CAD designs are 3D printed using PolyCast™ and then polished inside the Polysher™, they are then attached to a wax tree which can hold multiple parts and consists of sprues and risers which help guide the flow of molten metal. The tree is then dipped in a ceramic slurry which coats all the surfaces of the tree and 3D printed parts. This is then showered with a silica particle which adds thickness and strength to the mold. This process is then repeated until a ceramic shell is built up around the 3D printed parts that is thick enough to withstand the molten metal. The ceramic shell is then fired in a kiln at temperatures of 1200°C, this cures the ceramic to create a very hard and heat resistant shell. It is during this process that the 3D printed patterns are burnt out of the ceramic shells. Ash-Free™ technology typically leaves and an ash residue of 0.003% by weight after burn out. This means that the 3D printed part has been completely vaporized by the high temperatures in the kiln producing a very clean casting surface on the inside of the ceramic mold. The molds are then used to pour molten metal into which solidifies in the pattern of the 3D printed parts. The metal tree is then broken free from the brittle ceramic shell and the individual parts are cut away from the tree which can be recycled. Parts are generally post-processed by a CNC milling machine to achieve the desired tolerances for precise machinery. In some cases, metal parts can be easily cleaned up by hand and are production ready without the need of CNC milling. Having a mold that is completely free of ash is essential to the final quality of the metal part and is the key technology that is employed on PolyCast™, Layer-Free™ technology ensures a bubble-free interface layer on ceramic molds and also sealing all surfaces on the 3D printed part which reduces time in the final post-processing of metal parts.
Layer-Free™ technology has given 3D printed parts that finishing touch taking them into the league of traditionally manufactured plastic objects. With all the other benefits of 3D printing, the ability to create a smooth, glossy surface that's watertight and easy to clean is a major breakthrough for 3D printed parts and they serve as a daily aid to our modern lives. By unlocking new geometrical shapes, Layer-Free™ technology has helped open new doors for investment casing allowing shorter lead times and more customization of metal parts. This, in turn, will benefit many other industries and have a truly global impact as we create ever more efficient machines.
Extrusion-based 3D printing remains the most accessible 3D printing technology, due to its wide range of material choice and great user community. However, all materials face the same challenge of surface quality as they cannot escape the layers. PolySmooth™ is one unique filament that offers an answer to layered prints and now Polymaker has launched 5 new colors to add to the range!
In April 2016, Polymaker launched a Kickstarter campaign for PolySmooth™ & Polysher™, a desktop post-processing machine to remove all layers from printed parts and a 3D printing filament that can be easily smoothed with isopropyl alcohol. The campaign was a huge success and the goal was reached in just four hours of launching the campaign. Polysher™ & PolySmooth™ still remains the most successful Kickstarter campaign for a 3D printing accessory to date.
PolySmooth™ offers excellent printing quality, balanced mechanical properties, and most importantly, it is engineered for hands-free post-processing. The surface can be smoothed with alcohol to achieve layer free models using the Polysher™. In the meanwhile, the printing setting of PolySmooth™ is designed to be very similar to PLA, which means it is 100% compatible with existing extrusion-based (FDM/FFF) 3D printers and extremely easy to work with.
PolySmooth™ has been available in global markets for over 2 years with 7 unique colors– black, white, coral red, electric blue, slate grey, transparent and Polymaker teal. Once a print has been polished it is transformed into a smooth glossy object giving the printed part the aesthetics of an injection moulded part. This means that the color of the filament is more paramount than a regular color on a different material. Users like to utilize the unique colors of PolySmooth™ to create innovative, interesting, and aesthetic items for various application scenarios. As a result, there are more and more voices asking for new colors.
So, we are now introducing PolySmooth™ 5 new colors to the market: Pink, Yellow, Beige, Green and Orange. They are now available on www.polymaker.com and Amazon with both 1.75mm & 2.85mm diameters.
We look forward to seeing more exciting 3D prints using these new colors!
Polymaker join the Ultimaker Material Alliance Program adding three engineering materials to the Ultimaker Workplace
SHANGHAI, 21st February 2019 – Polymaker, producer of advanced 3D printing materials, today announced during TCT Asia in Shanghai that they will join the Ultimaker Material Alliance Program. Polymaker will add three engineering filaments to the Cura workplace offering Polymaker material solutions to Ultimaker users.
Dr. Xiaofan Luo, President, Polymaker: “FFF 3D printing remains the most practical and accessible one of all 3D printing technologies. The 3 materials we offer via the Ultimaker Marketplace, including PolyMide™ PA6-CF, PolyMide™ CoPA and PolyCast™, are among the most unique and advanced materials in our portfolio. I believe they will open up countless new applications for a greater number of engineers."
In order to accelerate the synergy between 3D printing material and machine, Polymaker have added three advanced materials from their portfolio to the Cura workplace. This will increase the printing quality and repeatability of parts as all print profiles are stored on Cura. Users will simply select the material profile and start a print in a matter of seconds. Polymaker have started by adding PolyMide™ CoPA, PolyCast™ & PolyMide™ PA6-CF to the alliance program introducing 3 unique materials with engineering applications across a number of industries.
Jos Burger, CEO at Ultimaker: “The growing importance of 3D printing gives us—as a leader in desktop 3D printing—an important role in ensuring a perfect collaboration between hardware, software and materials. By offering material profiles directly to millions of end users via the Ultimaker Marketplace, we unlock new 3D printing applications for different industries. Polymaker is a well-respected material company, offering unique material properties that are relevant for engineers working in a wide diversity of industries. I am proud to recognize their commitment to the Ultimaker Material Alliance during TCT ASIA.”
PolyMide™ CoPA
PolyMide™ CoPA is a co-polymer polyamide (Nylon) filament which combines the high heat deflection of Nylon 6.6 with the stiffness and impact toughness of Nylon 6. Together they produce a well-rounded Nylon filament with a heat resistance of 180°C and a high tensile strength and process ability. PolyMide™ CoPA also features Polymaker’s Warp-Free™ technology, which allows the polymers to crystallise extremely slowly allowing any internal stresses that are caused by printing to be relaxed. This produces a nylon filament which prints with near zero warp on an open bed printer. Furthermore, Warp-Free™ technology allows crystals to form across layers producing isotropic strength on the Z-axis. Formerly, nylon filaments have required enclosed heated chambers, high nozzle temperatures and were generally limited to small printed parts. PolyMide™ CoPA with Warp-Free™ technology releases the constraints previously supressing nylon, allowing engineers more freedom in the design and production of functional 3D printed parts.
PolyCast™
PolyCast™ is a unique 3D printing filament designed specifically for investment metal casting. PolyCast™ completely removes any tooling from the traditional investment moulding process, by replacing wax patterns with 3D printed patterns. Using Polymaker’s Ash Free™ technology PolyCast™ prints can be burned away very cleaning, typically leaving an ash residue of 0.003%. This allows for investment moulds to be cast around 3D printed parts which can then in turn be used to create metal parts suitable for production. PolyCast™ allows for rapid design iteration and is unconstrained by large production volumes as the expensive and time-consuming tooling process is eliminated. Furthermore, investment casting foundries are able to test complex geometrical shapes which are unachievable via injection moulding without diverting from their current casting process.
PolyMide™ PA6-CF
PolyMide™ PA6-CF is a nylon 6 filament with carbon fibre reinforcement, displaying high heat deflection paired with superior stiffness and toughness. PolyMide™ PA6-CF is perfect for practical applications involving high vibration environments where toughness and heat deflection are required. Polymaker have optimised the carbon fiber surface chemistry so that the fibers integrate perfectly within the polyamide matrix. This results in not only a greater adhesion between polymer and fiber but translates into a greater layer adhesion between printed layers. This breakthrough technology has not been witnessed before as fibers generally add stiffness only on the X-Y axis while degrading the Z axis strength. PolyMide™ PA6-CF displays an increased inter layer adhesion creating printed parts that are 30% stronger in tensile strength along the Z axis. Polymaker have jumped the final hurdle inhibiting fiber reinforced filaments, furthermore, PolyMide™ PA6-CF actually improves the layer bond on the Z axis. Paired with Warp-Free™ technology, PolyMide™ PA6-CF demonstrates itself as an engineering material with properties that outperform almost every other filament.
About Polymaker
Polymaker is a company dedicated to developing new and functional materials for the 3D printing industry. Since 2013 Polymaker has developed unique in-house technologies that optimize their materials for 3D printing. In 2017 Polymaker won two major awards: “Material Company of The Year” from 3D Printing Industry and “Technology Innovation Award – Materials” from TCT. This marked the company’s growing reputation which is now widely recognized at a global scale. Headquartered in Shanghai, China, Polymaker also has global offices in the USA, Netherlands and Japan. With their state-of-the-art research and development center, Polymaker place focus on pioneering development of engineering grade materials for applications across many industries.
About Ultimaker
Since 2011, Ultimaker has built an open and easy-to-use solution of 3D printers, software, and materials that enable professional designers and engineers to innovate every day. Today, Ultimaker is the market leader in desktop 3D printing. From offices in the Netherlands, New York, Boston, and Singapore – plus production facilities in Europe and the US – its global team of over 400 employees work together to accelerate the world’s transition to local, digital manufacturing. ultimaker.com
Polymaker has an exciting product plan for the first half of 2019. We are adding 3 New filaments to our repertoire and new colors to existing filaments!
PolyLite™ ASA
PolyLite™ ASA will add more interesting application possibilities to the PolyLite™ range with its excellent weather resistance and thermal stability. The material of choice for prints that need to face the elements. PolyLite™ ASA also has good mechanical properties and printability.
PolySmooth™ & PolyLite™ PLA new colors
Polymaker will add more colors to the PolySmooth™ and PolyLite™ PLA range in order to offer a wider range of choices for users and allow them to transform their digital design into realistic 3D models. This will include, Orange, Yellow, Pink and Green for PolySmooth™ and a Sparkle range for PolyLite™ PLA of Grey and Blue.
PolyMide™ PA6-CF & PolyMide™ PA6-GF
After announcing Polymaker Industrial’s new N600 series, Polymaker is working on introducing PolyMide™ PA6-GF and PolyMide™ PA6-CF to extend PolyMide™ family of Nylon based material. These new products will offer higher mechanical and thermal properties while also featuring the now well-known Warp-Free™ technology. Print lightweight parts with incredible stiffness and durability.
Polymaker also has some new products lined up for Q3 & Q4 adding more materials to the PolyMax™, PolyFlex™ & PolyMide™ families.
Polymaker’s research and development lab continues to develop new technologies to ensure Polymaker materials stay the best option on the market.
PolyDissolve™ S1 is the first product of PolyDissolve™ family. This family offers dissolvable support solution for Polymaker filaments. PolyDissolve™ S1 is specifically engineered to have a perfect interface with materials while also displaying good solubility.
PolyDissolve™ S1 is a PVA (polyvinyl alcohol) material which dissolves in water. This main advantage makes it preferable solution to support when printing complex geometries, overhangs, internal cavities and complicated structures. It liberates you from support removal problems, and enables greater design freedom
So far, PolyDissolve™ S1 is compatible with PolyMax™ PLA, PolyLite™ PLA, PolyWood™, PolyFlex™ TPU95, PolySmooth™, PolyCast™, PolyMide™ CoPA.
Advantages of PolyDissolve™ S1
- It is engineered to have a good adhesion and perfect interface with supported materials.
- Only tap water is needed to dissolve it.
- It is compatible with 7 products from Polymaker portfolio.
Now it is available on www.polymaker.com and Amazon. You can also find it from Polymaker’s resellers.
PolyDissolve™ S1 Technical Data Sheet
PolyMax™ PETG is new member of PolyMax™ family. PolyMax™ family consists of advanced 3D printing filaments produced with Polymaker’s Nano-reinforcement technology, which delivers exceptional mechanical properties and printing quality.
PETG is a Glycol Modified version of Polyethylene Terephthalate (PET). It becomes more and more popular as 3D printing material. PETG 3D printing filament combines the advantages of 2 most popular kinds of FFF/FDM materials: PLA and ABS. It owns the reliability of PLA (easy to print, no warping, and odor during printing) and the functionality of ABS (strong, tough and heat resistant).
Just as PolyMax™ PLA and PolyMax™ PC (used to be called PC-Max™), which are the best of its kind, PolyMax™ PETG offers better mechanical properties than any other regular PETG making it a good candidate for a wide range of applications.
Pursuing the top-quality products, Polymaker applies the successful experience of creating PolyMax™ PLA and Nano-reinforcement technology to PETG material. Now we are delighted to introduce PolyMax™ PETG to you. PolyMax™ PETG has improved mechanical properties and printability.
Advantages of PolyMax™ PETG
- PolyMax™ PETG not only have the reliability of PLA (easy to print, no warping and odor during printing) but also have a greatly improved mechanical strength than normal PETG.
- PolyMax™ PETG’s heat resistance is up to around 80℃.
- PolyMax™ PETG has excellent layer adhesion.
- You don’t need to worry about warping or shrinking during the printing process, which ensures the dimensional stability.
Now it is available on www.polymaker.com and Amazon. You can also find it from Polymaker’s resellers.
PolyMax™ PETG Technical Data Sheet
The N600 series are a new set of Nylon 6 based filaments with excellent mechanical properties and heat resistance.
Designed for applications that require strong parts such as tooling in automotive, aerospace, industrial manufacturing and consumer goods.
The N600 series are equipped with Polymaker’s Warp-Free™ Technology which allows large scale printing without a heated chamber. The first three N600 series products are N600 (Nylon 6), N600GF25 (Glass fiber reinforced Nylon 6) and N600CF20 (Carbon fiber reinforced Nylon 6).
N600 is a PA6 filament with excellent mechanical properties and printability
N600GF25 is a glass fiber reinforced PA6 filament with excellent toughness and heat resistance
N600CF20 is a carbon fiber reinforced PA6 filament with extreme stiffness and excellent heat resistance
Polymaker has already confirmed to attend some of the best 3D printing exhibitions in the world in 2019. If you want to know about Polymaker’s products, solutions and applications, please keep an eye on the following 5 exhibitions. Polymaker team is looking forward to having a face-to-face communication with you.
CES 2019
Date: 8th - 11th January
Venue: South Hall 3, LVCC (Las Vegas Convention Center), Las Vegas, NV, USA
Booth: 32024
CES serves as a global stage for introducing innovations and breakthrough technologies to the markets. Polymaker provides consumer and professional markets with best in class 3D printing materials. Welcome to visit Polymaker at CES this year!
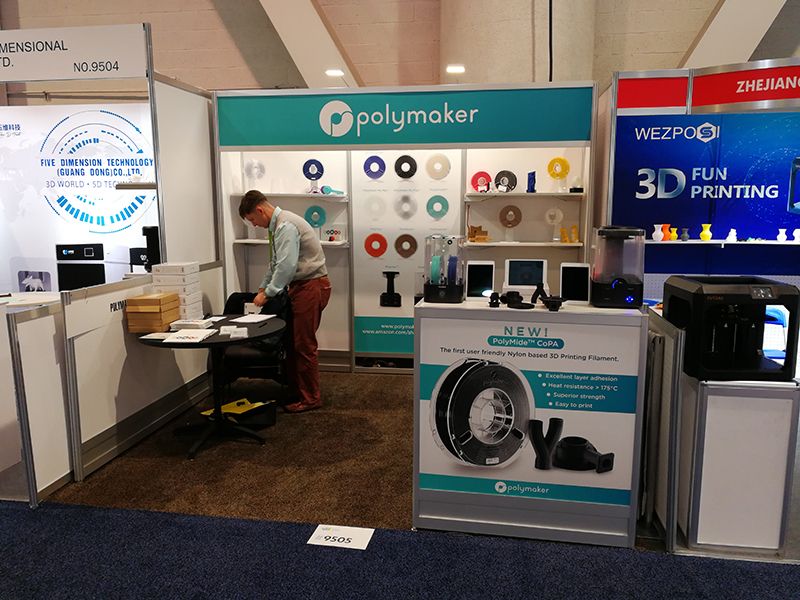
TCT Japan 2019
Date: 30th January - 1st February
Venue: East Exhibition Hall 6, Tokyo Big Sight, Japan
Booth: 6N-22
3D Printing Japan is the number one event in Japan for additive manufacturing and 3D printing technology. From 2019, 3D Printing Japan is renamed as “TCT Japan”. Polymaker will attend this professional and the best exhibition in Japan at the end of this month.
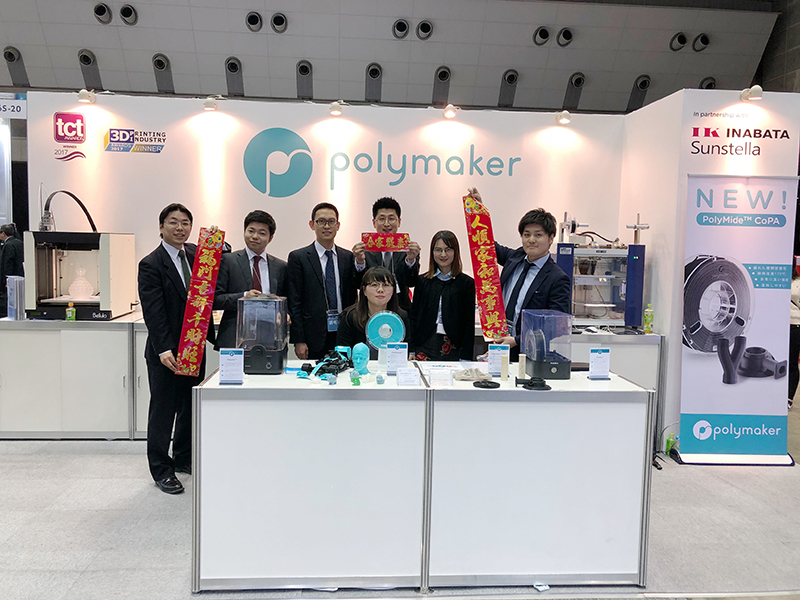
TCT Asia 2019
Date: 21st - 23rd February
Venue: Hall W5, SNIEC (Shanghai New International Expo Center), Shanghai, China
Booth: W5 - F50
TCT Asia has built its fame as one of the leading 3D technology exhibitions in the Asia market. As usual, Polymaker will make full preparations for this show.
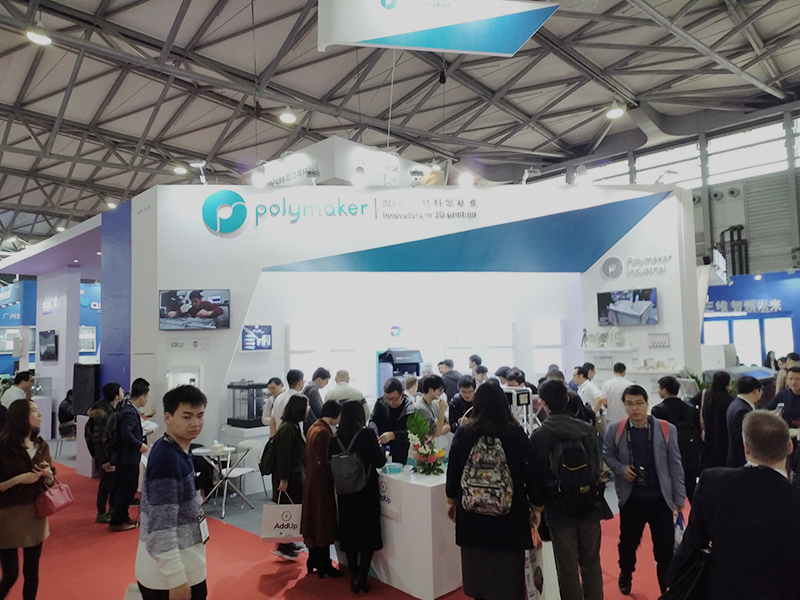
Rapid + TCT 2019
Date: 21st - 23rd May
Venue: Cobo Center, Detroit, MI, USA
Booth Number: To be announced
RAPID + TCT is North America's preeminent event for 3D manufacturing. The newest products and technologies are often firstly announced here. Polymaker will also bring the latest innovations and new products there.
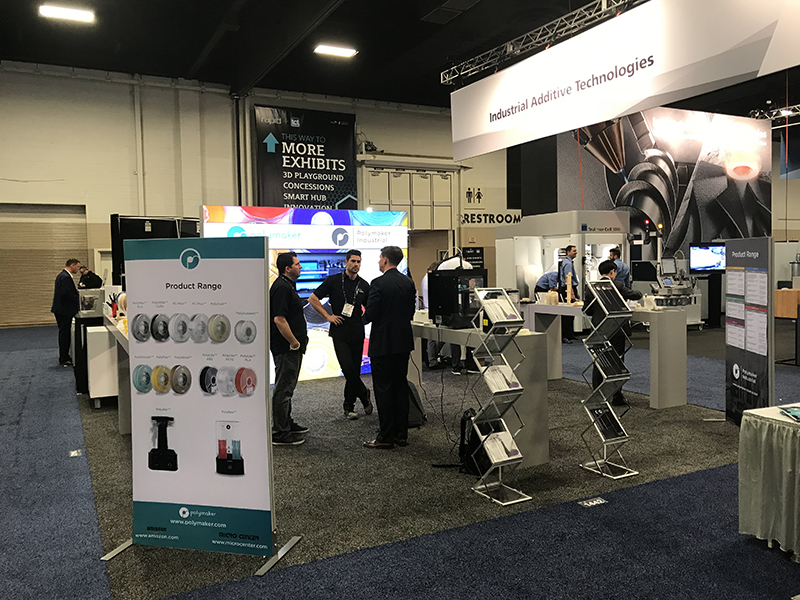
Formnext 2019
Date: 19th - 2nd November
Location: Frankfurt, Germany
Booth Number: To be announced
Formnext is the leading exhibition for additive manufacturing technologies, 3D printing, as well as tool and mould making. Polymaker will highlight its industrial-grade products and 3D printing solutions at Formnext.
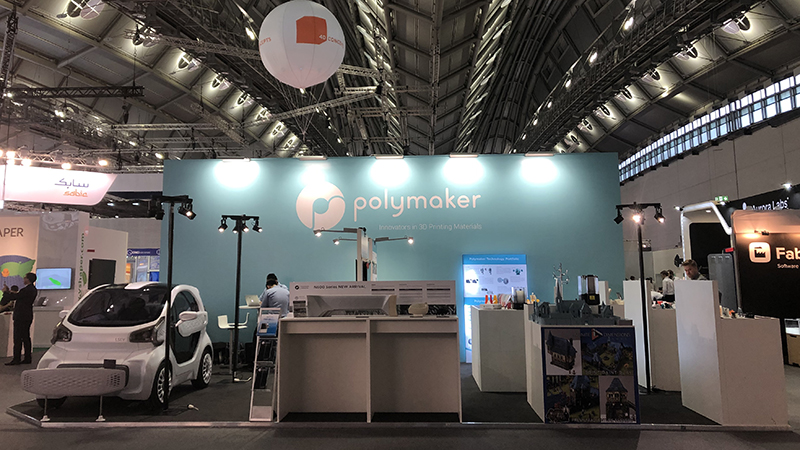
Footage of world's largest plastic 3D printer printing pedestrian bridge
Polymaker just released footage of Shanghai Construction Group’s 3D printer in the process of producing a pedestrian footbridge, which will take 30 days to complete as it will be 15 meters long and weigh 5,800kg. SGC has a reputation for going big as they built the second tallest building in the world, the Shanghai Tower. The 3D printer was built by Shenyang Machine Group and the extruder system was manufactured by Coin Robotic (who also built the bed), together totaling some $2.8 million in investment. Polymaker Industrial developed the ASA (acrylonitrile styrene acrylate) plastic for the print, a material chosen for its favorable properties of weather and chemical resistance, thermal stability, and toughness. To determine the best plastic for the job, Polymaker 3D printed a 5-meter version of the bridge with several different compounds before choosing AS100GF for its overall strength and printability. The bridge will be rated to hold 13 tons or four people per square meter, so strength is vitally important.
The plastic is 12.5% glass fibers by weight, adding strength and also reducing the warping effect that plagues large 3D prints. 3D Printing bigger isn’t as simple as just making a bigger printer because so much of 3D printing is related to heat retention and even heating, which becomes a trickier task the bigger the print/printer. In this case, the build chamber is 24 meters long, 4 meters wide, and 1.5 meters high, with a planned expansion to 3 meters high. That’s 144 cubic meters to keep heated, which is achieved by a large bellowed tent that moves with the gantry. The tent is heated to 38°C and blankets are placed on top of the print to slow the cooling process, allowing the polymer chains to relax without warping; the blankets also protect the print from dust. Yes, the build chamber is so large that technicians work inside the 3D printer while it’s operating to monitor the print and move the blankets.
But heating is only one 3D printing issue that’s exacerbated by increasing scale as there’s also layer levelness as well as bed and layer adhesion. For layers to bond well, they should be joined when they’re at a similar temperature; on this print, each layer takes several hours, so the previous layer has cooled significantly by the time the extruder comes back around for the next layer. The blankets and the glass fibers help slow this cooling, but the print head does a lot of work here by reheating the print with four 600°C hot air guns aimed around the extruder. The air guns ensure the print is always hot around where the extruder is working for maximum layer adhesion.
The layer levelness issue is solved here by a novel approach not seen on other 3D printers: tamping. Nozzles are round, meaning their extrusion is round, and when pushed flat as a layer they have a tapered top, which is not ideal for layer adhesion. For a desktop 3D printer with a nozzle size of 0.35mm, the taper is small enough to mostly not notice, but the SGC 3D printer uses a nozzle over 14x that size at 5mm so the tamping of the plastic right after it’s extruded makes a big difference in layer levelness and adhesion. And considering that, despite its gargantuan size and the fact that it’s extruding up to 8kg of plastic per hour, the printer is accurate to 0.1mm, those differences in levelness really matter. To get the first layer to adhere to the print bed, ASA pellets were glued to wooden planks that were then clamped to the steel bed. Sometimes the low-tech solution is the best solution.
A pedestrian bridge over a lake is a great way to showcase the largest 3D printed plastic object as it’s both an everyday, practical application and an interactive one that involves people touching and even relying upon (to keep them from getting wet) a 3D printed thing. Many people have never touched a 3D printed object and they still think of it as part fantasy and part future tech, so projects like this do a lot of good in terms of exposing the public to the reality and the possibilities of 3D printing.
Polymaker announces another round of investment and launches of PolyMax™ PETG, PolyDissolve™ S1, and PolyCast™ at Formnext
Polymaker recently announced another round of investment led by Skytrace Capital and followed by ShareLink Capital.
Polymaker, known for producing high quality and innovative 3D printing materials throughout the industry, has been growing rapidly ever since it was founded. Polymaker has developed a global distribution channel in over 100 countries and regions which is headquartered in Shanghai with offices in Utrecht, Netherlands and Savannah, U.S.
Polymaker produces high quality 3D printing materials with a comprehensive range of properties and functions, ranging from high engineering strength to unique aesthetic solutions. Polymaker keeps adding new innovative, cutting edge materials to continually grow their portfolio.
To meet the industrial-grade and enterprise-level needs, Polymaker Industrial was established at the beginning of 2017. In a short time, many milestone achievements have been realized up to date.
“Polymaker succeeded again in gaining investment against the trend of depressive capital winter. It proves the fact that 3D printing industry is still developing rapidly, and Polymaker’s development and strategies obtain the trust from both the capital and markets.” Polymaker President Dr. Xiaofan Luo explained.
Polymaker has contributed 6 new products this year and taken part in many ground breaking applications in 3D printing, such as the XEV 3D printed vehicle and the world’s largest plastic printer. At Formnext 2018 in Frankfurt on 13th – 16th November, Polymaker exhibited 3 new products: PolyMax™ PETG, PolyDissolve™ S1, PolyCast™.
- PolyMax™ PETG offers better mechanical properties than any other regular PETG making it a good candidate for a wide range of applications.
- PolyDissolve™ S1 is a water dissolvable support for PLA, TPU, PVB and Nylon based filaments from our portfolio. It is specifically engineered to have a perfect interface with these materials while also displaying good solubility.
- PolyCast™ is a filament designed to produce investment patterns for investment casting applications. 3D printing significantly cuts down both the cost and lead time by eliminating the tooling process.
New N600(Nylon 6) series from Polymaker industrials were firstly shown to the public at Formnext as well. The N600 series are a new set of Nylon 6 based filaments with excellent mechanical properties and heat resistance. Designed for applications that require strong parts such as tooling in automotive, aerospace, industrial manufacturing and consumer goods. The N600 series is equipped with Polymaker’s Warp-Free™ Technology which allows large scale printing without a heated chamber. The first three N600 series products are N600 (Nylon 6), N600GF25 (Glass fiber reinforced Nylon 6) and N600CF20 (Carbon fiber reinforced Nylon 6).
- N600 is a PA6 filament with excellent mechanical properties and printability.
- N600GF25 is a glass fiber reinforced PA6 filament with excellent toughness and heat resistance.
- N600CF20 is a carbon fiber reinforced PA6 filament with extreme stiffness and excellent heat resistance.
Apart from these new amazing products, Polymaker also showed some of latest industrial-grade and enterprise-level applications.
Belgium automotive modification company, Custom Import Arts, uses PolyMide™ CoPA to make customized air intake for NSX sports car. The air intake part shown at Formnext has been sanded and painted, it can be used as final part. This application illustrates the great advantage of 3D printing large size part with PolyMide™ CoPA. Polymaker patented Warp-Free™ Technology allows large scale printing without worrying about warping problem. And it is easy to do post-processing for PolyMide™ CoPA, the outstanding mechanical and thermal properties also make it a perfect choice for a wide range of practical applications.
Indian company, Drona Aviation, chooses to use PolyMax™ PLA to fabricate the frame of their new generation product Pluto X. PolyMax™ PLA is equipped with Polymaker’s Nano-reinforcement technology which makes it around 8 times tougher than normal PLA and about 20% tougher than ABS. Pluto X is an easy DYI, programmable and crash resistant drone thanks to PolyMax™ PLA.
Czech brand, Laura Jonas, uses PolyMax™ PLA, PolySmooth™, and PolyWood™ to design and produce jewelry including: Necklace, earrings, bracelet or even rings. The high quality Polymaker materials and unique aesthetic options allow Laura Jonas to bring their design to life. Skilled designers take full advantages of 3D printing technologies, Polymaker materials’ aesthetic colors, the great toughness of PolyMax™ PLA, and the unique surface finish of PolySmooth™ and PolyWood™.
One of the most attractive case studies of the Polymaker booth was made in partnership with Infinite Dimensions. This whole village has been printed using PolySmooth™. After polished by Polysher™, these miniatures maintain all the details and can be easily painted.
Polymaker is working closely with Shanghai Construction Group (SCG) and Coin Robotics to unlock large scale 3D printing. SCG is behind the shanghai tower (second tallest tower in the world) and the Shanghai subway (largest underground network system in the world). The goal of the first project is to print a large pedestrian bridge. With their 24m by 4m by 1.5m 3D printer, they are using our special ASA reinforced material to ensure the best properties for the process and application.
Polymaker provides polycarbonate C515FR to China Eastern airline helping them to manufacture the cabin interior parts replacements by 3D printing them in house in order to save cost and cut down lead time. C515FR is a flame-retardant material which can score V-0 in a UL-94 test. It also has excellent mechanical properties and can be easily post processed.
The world first mass-producible 3D printed car – LSEV appeared on Polymaker booth. This car is planned to be mass produced using extrusion based 3D printing with the new Polymaker Industrial N600 series of materials. The bumper and rocker cover from the 2rd generation of LSEV prototype were exhibited to demonstrate the agility and iteration capability of adopting 3D printing in manufacturing.
It was a great opportunity for Polymaker to present new products, new technologies and the latest industrial applications at Formnext. A lot of interests, inquiries and compliments were received. Polymaker will continue to display new innovations in 3D printing through the application of their materials.
About Polymaker
Polymaker is a company dedicated to developing new and functional materials for the 3D printing industry. Polymaker has won two major awards in 2017: "Material Company of The Year" from 3D Printing Industry and "Technology Innovation Award – Materials" from TCT. This marks the company's growing reputation which has become more widely recognized at a global scale. Headquartered in Shanghai, China, Polymaker now has global offices in the USA, Netherlands and Japan. With their state-of-the-art research and development center, Polymaker is pioneering the development of engineering grade materials for use across many industries.
POLYMAKER SELECTS NEXEO SOLUTIONS FOR GLOBAL DISTRIBUTION OF INDUSTRIAL GRADE 3D PRINTING FILAMENTS
Nexeo Solutions 3D to expand its 3D printing portfolio with filaments specifically developed for industrial use
THE WOODLANDS, Texas, June 26, 2018 - Nexeo Solutions, Inc. (NASDAQ:NXEO), a leader in chemicals and plastics distribution, announced today that it has entered into an arrangement with Polymaker to distribute its new industrial 3D printing filaments C515, C515-FR and SU301, globally.
Headquartered in Shanghai China, global 3D printing material producer Polymaker is committed to innovation, quality and sustainability by developing high-quality materials with enhanced strength and durability for industrial manufacturing.
“Expanding our portfolio to include industrial grade filaments from Polymaker Industrial gives our customers access to a wider range of filaments that solve new 3D printing challenges and meet the demands of manufacturers.” said Paul Tayler, Vice President of EMEA at Nexeo Solutions. “Industrial customers benefit from Nexeo Solutions’ access to world leading plastic producers coupled with additive manufacturing technical expertise.”
“Our Polymaker Industrial filaments stand out because of their printability while also offering all the intrinsic material properties that engineers get with molding technology,” said Wildrik van der Weiden, Business Development Manager, at Polymaker. “We have made it our mission to develop the highest quality filaments, and together with Nexeo Solutions 3D, we are now able to put our materials in the hands of engineers all over the world, allowing more companies to benefit from our extensive R&D.”
Polymaker Industrial C515 is an advanced polycarbonate (PC) filament optimized for 3D printing providing superior printability combined with a low warping effect. Due to its outstanding toughness, the C515 polymer is ideal for industrial applications such as high-volume jigs and fixtures or sports equipment.
Polymaker Industrial C515FR is a flame retardant polycarbonate (PC) filament developed and high-impact resistant filament initially for the aerospace industry. The C515FR filament is suited for industrial applications across many industries such as drones and electronic housings.
Polymaker Industrial SU301 is a polyvinyl alcohol (PVA)-based polymer developed specifically as a support material for FFF printers. Compatible with the most used 3D printing materials such as PLA, TPU, Nylon and PETG based filaments, SU301 is a water soluble filament that considerably simplifies the post-printing process.
Nexeo Solutions 3D will introduce additional Polymaker materials throughout 2018. Explore Nexeo Solutions 3D full range of 3D printing materials at www.nexeo3D.com.
About Nexeo Solutions, Inc.
Nexeo Solutions 3D is a specialized group within Nexeo Solutions that focuses primarily on premium 3D printing solutions for FFF (fused filament fabrication), servicing a broad cross-section of markets, including automotive, industrial, electronics and healthcare among others. Nexeo Solutions 3D Application Development Engineers Team can provide expert guidance to help customers at every stage of their 3D printing adoption process.
Nexeo Solutions is a leading global chemicals and plastics distributor, representing products from world-class producers to a diverse customer base. From product specification to sustainable solutions, the Company goes beyond traditional logistics to provide value-added services across many industries, including chemicals manufacturing, oil and gas, coatings, personal care, healthcare, automotive and 3D printing. The Company leverages a centralized technology platform to identify efficiencies and create solutions to unlock value for suppliers and customers. Learn more at www.nexeosolutions.com.
About Polymaker Industrial
Polymaker Industrial is a series of engineering grade materials aimed at the industrial 3D printing sector. Offering full customisation of polymer compounds, Polymaker’s material scientists can tailor material characteristics to match your applications. With an ever-growing portfolio of materials, Polymaker Industrial has solutions to high heat applications, flame retardance, dissolvable support, specialty casting materials and other solutions covering a wide range of industries. All materials are formulated in house by Polymaker with the focus on creating the highest quality materials for the industry. At the heart of Polymaker Industrial is a large research and development laboratory which drives the company forward through constant innovation and testing. Learn more at www.polymakerindustrial.com
FOR FURTHER INFORMATION PLEASE CONTACT
Media Relations, Nexeo Solutions
Tel: +1.281.297.0851
Media.Relations@nexeosolutions.com
Investor Relations, Nexeo Solutions
Tel: +1.281.297.0856
Investor.Relations@nexeosolutions.com
SHANGHAI, April 24, 2018 /PRNewswire/ -- Materials manufacturer Covestro and its partner Polymaker launched a website designed to aid the use of polycarbonate in 3D printing. It is called 3DPC (www.3dprintingpc.com) and is available as of April 24th. The information platform offers know-how on 3D printing with polycarbonates - from material options to printing conditions. Polycarbonates are one of the most widely used plastics around the world, largely thanks to its excellent mechanical properties and process ability. 3DPC provides the knowledge of industrial experts under one platform, providing the vital information necessary to create 3D printed parts in mass production.
As an engineering plastic, polycarbonate can be found in many different industries from automotive to healthcare and aerospace. The rapid rise of 3D printing in the last half decade has unlocked new potential applications for this already popular polymer. As 3D printing unlocks new geometries that traditional processing techniques couldn't achieve, polycarbonate offers the mechanical properties that bring functionality to the form. 3DPC demonstrates the optimal printing and processing techniques to further penetrate polycarbonate into new industries and dynamic applications.
Recently, the 3D printing industry has witnessed a shift to more specialised applications with printer manufacturers targeting engineering groups directly linked to specific applications. Simultaneously, material development is moving in a similar direction as both printer and material manufacturers create the perfect conditions for the reliability and repeatability demanded by industrial users. This means that more specific data and process knowledge is needed to drive 3D printing into mainstream manufacturing, increasing the accuracy, strength and speed of printed parts. 3DPC serves as the informational platform dedicated to polycarbonate in 3D printing.
As more industries are adopting 3D printing into their research, development and final production, 3DPC highlights current case studies and applications where users can gain more insight into the applications of polycarbonate. One application featured on 3DPC highlights a specially developed fire rated (UL-94, V0) polycarbonate material, designed for the aerospace industry. The focused research and development into specific applications for fire rated polycarbonate will serve as a basis to trickle down into different industries concerned with safety and fire rating.
Polycarbonate is also naturally transparent while displaying high heat resistance which makes it the material of choice for lighting applications previously unseen in the industry. Paired with polycarbonate's high impact strength and wide availability, this resilient material is perfectly positioned to deliver repeatable production via 3D printing - and 3DPC offers the knowledge to apply it in just the right way.
About Covestro:
With 2017 sales of EUR 14.1 billion, Covestro is among the world's largest polymer companies Business activities are focused on the manufacture of high-tech polymer materials and the development of innovative solutions for products used in many areas of daily life. The main segments served are the automotive, construction, wood processing and furniture, and electrical and electronics industries. Other sectors include sports and leisure, cosmetics, health and the chemical industry itself. Covestro has 30 production sites worldwide and employs approximately 16,200 people (calculated as full-time equivalents) at the end of 2017.
About Polymaker:
Polymaker is a company dedicated to developing new and functional materials for the 3D printing industry. Polymaker has won two major awards in 2017: "Material Company of The Year" from 3D Printing Industry and "Technology Innovation Award – Materials" from TCT. This marks the company's growing reputation which has become more widely recognized at a global scale. Headquartered in Shanghai, China, Polymaker now has global offices in the USA, Netherlands and Japan. With their state-of-the-art research and development center, Polymaker is pioneering the development of engineering grade materials for use across many industries.
About 3DPC:
3DPC is an informational stepping stone aiding the adoption of polycarbonate 3D printing into worldwide industries. Offering all you need to know about 3D printing polycarbonate, this informational platform covers all processes, transforming practical ideas into dynamic applications. Sharing information across material options, software, post processing and 3D printers; 3DPC draws expert knowledge from its partners at Covestro and Polymaker to deliver the vital information for end users to best utilize this practical material.
This press release is available for download from the Covestro press server at www.covestro.com. Photos are available there for download as well. Please acknowledge the source of any pictures used.
Find more information at www.covestro.com, www.polymaker.com and www.3dprintingpc.com.
Forward-looking statements
This news release may contain forward-looking statements based on current assumptions and forecasts made by Covestro AG. Various known and unknown risks, uncertainties and other factors could lead to material differences between the actual future results, financial situation, development or performance of the company and the estimates given here. These factors include those discussed in Covestro's public reports which are available at www.covestro.com. The company assumes no liability whatsoever to update these forward-looking statements or to conform them to future events or developments.
Italian electric car company XEV and 3D printing material company Polymaker organized a joint press conference at the China 3D-Printing Cultural Museum in Shanghai. The first mass-producible 3D-printed electric car in the world was launched and shown to the public.
Although this new vehicle attracts much attention, this conference is not just about launching and exhibiting the car. It is more about how 3D printing technology brings revolutionary changes to automotive manufacturing industry. This car, named LSEV, could be the milestone product in the adoption of 3D printing into mainstream production.
“XEV is the first real mass production project using 3D printing. By saying real, I mean there are also lots of other companies using 3D printing for production. But nothing can really compare with XEV in terms of the size, the scale, and the intensity.” Said, Dr. Luo Xiaofan, the co-founder and CEO of Polymaker.
XEV CEO, Stanley said that “after the research and investigation of the global auto market, they decided to design a small electric vehicle that can achieve C2M (Customer-to-Manufacturer) manufacturing which is stated as a main goal of the Industry 4.0 strategy.”
To fulfill this target, it requires mass customization production, fast and cost-effective R&D, and the ability to produce lighter-weight parts that could lead to greater fuel efficiency.
“And then, 3D printing technology becomes the only way to realize it”, said Stanley.
Surely there are many difficulties when utilizing 3D printing technology in auto volume production, Polymaker was chosen as the strategic partner and successfully helped XEV to solve them, not only with material solutions, but also post-processing options in-line with the automotive industry.
“Without Polymaker, we couldn’t make this happen. We really like our interactions with Polymaker, this can be called as know-how combination. Without this kind of interaction, we also couldn’t find the solution we have today. So, we really appreciate what Polymaker do and create for us, we are like brothers, not just strategic partners.” said, Stanley.
Polymaker developed dozens of kinds of engineering plastics for XEV to meet their needs of practical applications. As a result, 3 crucial achievements have been accomplished.
XEV has decreased the plastic parts and number of components in a car from more than 2,000 to 57, and the finished LSEV weighs only 450 kilograms, much lower than similar sized vehicles usually weighing between 1 and 1.2 metric tons.
Apart from the chassis, seats and glass, all the visible parts of the car are made by Polymaker materials through 3D printing. This switch of production leads to more than 70 percent reduction of the investment cost in comparison with a traditional production system.
Conventionally the R&D process of a car model takes about 3-5 years, but it only takes XEV 3-12 months to finish a new design.
Polymaker have also come up with solutions to help with surface treatments and color. These solutions are enormously helpful in customized production and 3D printing volume production.
XEV has already received 7000 orders from Europe even before mass production commences. 5000 orders come from Poste Italiane. And the other 2000 orders come from ARVAL, a vehicle leasing company fully owned by BNP Paribas. XEV plans to start production in the second quarter of 2019.
This strategic partnership between XEV and Polymaker leads to a revolutionary change in automotive manufacturing. It is possible that similar changes, related with 3D printing technology, will happen to every aspect of manufacturing very soon. As Polymaker proves that the 3D printing materials they provide are ready for not only end-use parts but also mass production of finished products.
CHINA UNVEILS THE WORLD’S LARGEST 3D PRINTED STRUCTURE
When it comes to 3D printing the ever- growing list of absolutely massive, large size 3D printing ventures is hard to ignore. You might remember Vulcan Pavilion which was record holder of the world’s biggest 3D printed structure in 2015 the Guinness World Records. Comprised of 1023 individual 3D printed units and standing at 8.08 meters long by 2.88 meters high. Well, they say that ‘records are made to be broken’ and thats exactly what happened in the 3D printing world. Beijing’s amazing 3D PRINTED Vulcan Pavilion has been ousted as the world’s largest 3D printed structure.
The new pavilion was officially awarded the Guinness World Record for largest 3D printed structure on August 20th, 2016. Beijing-based DeFacto was commissioned to design a structure for their client, Rise Education.
Rise Pavilion is certainly more than impressive. The pavilion weighs in at 1.87 tons, stands more than 11 feet tall, and spans over 1180 square feet. Each of the pavilion’s 5 arcs represents a sector of the competition: heath, transportation, society, education, art and design.
Constructed with over 5,300 poly-blocks that will all be up-cycled into a number of new and decorative pieces. The story behind creation of Pavilion is even more then amazing as the ultimate goal of the project is to make young generations think about recycling and ecological design and to encourage “a shift towards multi-functional and environmentally friendly goods.” Currently, the Rise Pavilion as part of the ongoing Young Creator Cup exhibition in Beijing. As the structure has been constructed with modularity in mind and can be built and rebuilt by simply removing individual blocks, this means when the exhibition wraps up on September 6th, all of the student participants will be allowed to take home a block from the structure to be used as they like.
The blocks are designed to be printed without support material and they are made entirely with PolyMaker’s PolyPlus biodegradable filament produced with patented Jam-Free™ technology that ensures consistent extrusion and prevents jams. For the project they employed 70 desktop 3D printers, with DeFacto’s partner UCrobotics, printing out all the parts in 45 days.
Check out our interview with David Doepel, the designer of Rise Pavilion.