SHANGHAI, May 6, 2024 - Polymaker recently won the TCT Asia Best Application Award - Industrial Product Applications for its pellet product, PolyCore™, in the 3D printing of architectural stencils. This honor not only recognizes Polymaker's innovation and excellence, but also its continued leadership in the 3D printing industry.

With the continuous innovation and advancement of 3D printing technology, utilizing the advantages of 3D printing's high precision and large size, PolyCore™ was selected as the product range to produce a 5m(L)*0.4m(W)* 2m(H) brand wall for Polymaker.
Polymaker collaborated with Shanghai Mechanized Construction Group, a subsidiary of Shanghai Construction Group (SCG) and Shanghai Kuying Technology Co., Ltd. to develop and print this wall.
The design of the wall features the Polymaker logo and a multi-faceted pattern, which demonstrates the strength and advantages of 3D printing when implementing creative design ideas in the construction Industry.

The completion of this wall is of great significance. SCG said: “The application of 3D printing technology in large scale shaped concrete formwork will revolutionize the speed and accuracy of manufacturing such as molds in municipal and construction projects. Compared with traditional molds, 3D printing technology effectively reduces the manufacturing cost and construction time, and promotes the transformation of traditional construction to digitalization, industrialization, intelligence, and low-carbonization.”
It is a significant achievement for Polymaker to be recognized at TCT Asia (The most influential additive manufacturing event in Asia) and to be awarded the Best Application Award - Industrial Product Applications, further reinforcing Polymaker’s position and portfolio within the construction field. Detailed information about this case, please click "Architecture Molding Case Printed with PolyCore™".

“We are extremely honored to win this award at TCT Asia this year. It not only recognizes our team's unremitting efforts and continuous innovation, but also brings new insights to the construction industry. Polymaker has been a pioneer in applying 3D printing to the construction field, providing a variety of pellet products for the construction industry including indoor design and outdoor construction, and successfully creating projects such as Taopu Central Park Bridge in Shanghai, China, the “Liuyun Bridge” in Chengdu,China, and Namthaja’s Rakah Roundabout Sculptures. In the future, the brand will also continue to devote itself to technological innovation and product optimization to bring more intelligent manufacturing possibilities to the construction industry and make buildings glow with the beauty of intelligent manufacturing.” Polymaker CEO Dr. Luo Xiaofan said.
In addition to the Best Application Award - Industrial Product Applications, Polymaker was also honored as a “10 Years Exhibitor” on the occasion of the 10th anniversary of TCT Asia. This honor represents Polymaker's longstanding partnership and close relationship with TCT Asia, as well as the brand's continued contributions to the 3D printing industry.

In the future, Polymaker will continue to uphold the spirit of excellence and innovation, expanding the boundaries of the additive manufacturing field, providing customers and partners with superior solutions, and ultimately advancing the development of additive manufacturing technology.
To round off another successful year, Polymaker was awarded the Material Company of the Year at the 3D Printing Industry Awards. This broad category is open to all additive manufacturing technologies: resin, metal powder, polymer powder, bio-printing as well as filaments. This marks the second time in five years that Polymaker has won the award, justifying that portfolio diversity and focus on research and development can drive 3D printing forward with Polymaker at the helm.
Heading into the new year, Polymaker will continue to take steps forward to enhance the experience for 3D printing users. Polymaker is already underway with the construction of a world-class R&D Center and Intelligent Factory, which will be equipped with a higher degree of automation and digitalization initiatives. This will enable more product launches of breakthrough materials with a higher standard of quality and repeatability. In 2023 Polymaker’s product launches will target four sectors: Firstly, as high-speed printing has become an emerging solution to bring 3D printing production mainstream, Polymaker plans to develop a brand-new product family focused purely on high speed 3D printing. Furthermore, a brand-new family of composite materials with high performance is on the schedule to deliver engineering plastics to desktop users. In the world of color, Polymaker will expand its current range introducing new colors not only in PLA but also in other trending materials, with more focus on unique colors / filler combinations. Finally, Polymaker will actively reach more end-users and iterate existing materials according to their needs, to continually improve the product offering and user experience.
Since its establishment, Polymaker strived to develop and manufacture diverse 3D printing materials and has maintained its position as the pinnacle of the extrusion-based 3D printing materials industry. While investing in R&D, the company has also done some eco-friendly work by changing the spool and outer package of all its products from plastic to recyclable cardboard in 2022 and cooperating with ONE-TREE-PLANTED to offset the carbon emissions generated by the manufacturing process of materials by planting trees. To date, more than 340,000 trees have been planted in 15 different regions spanning 6 continents and this cooperation has offset 6,800,000 Kg of Co2 in under 2 years with the trees set to continually offset Co2 for decades to come.
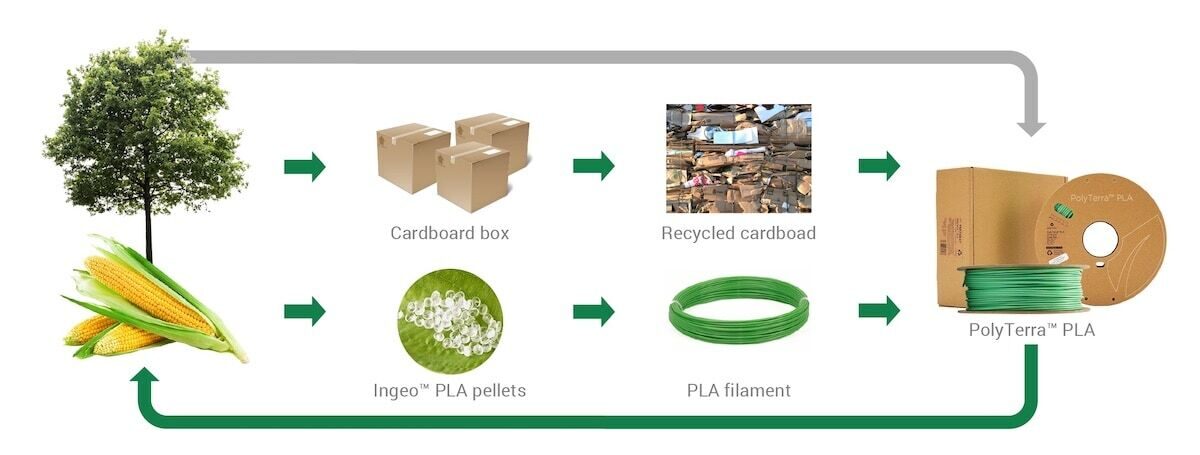
When it comes to product innovation in 2022, Polymaker introduced a number of breakthrough materials such as PolyMax™ PETG-ESD which is a perfect choice for applications in electronics industry by offering electrostatic dissipation through carbon nanotubes paired with tough PETG, a nylon material named PolyMide™ PA612-CF with excellent mechanical and thermal properties as well as good size stability for industrial and engineering tooling, automotive, and end-use industry, and PolySupport™ for PA12, an easy-to-use breakaway support material for long chain nylons, which have filled a gap in the market. At present, Polymaker products, including 3D printing filaments, 3D printing pellets and related hardware, can effectively cover all three-major application needs of consumer, professional & industrial and production.
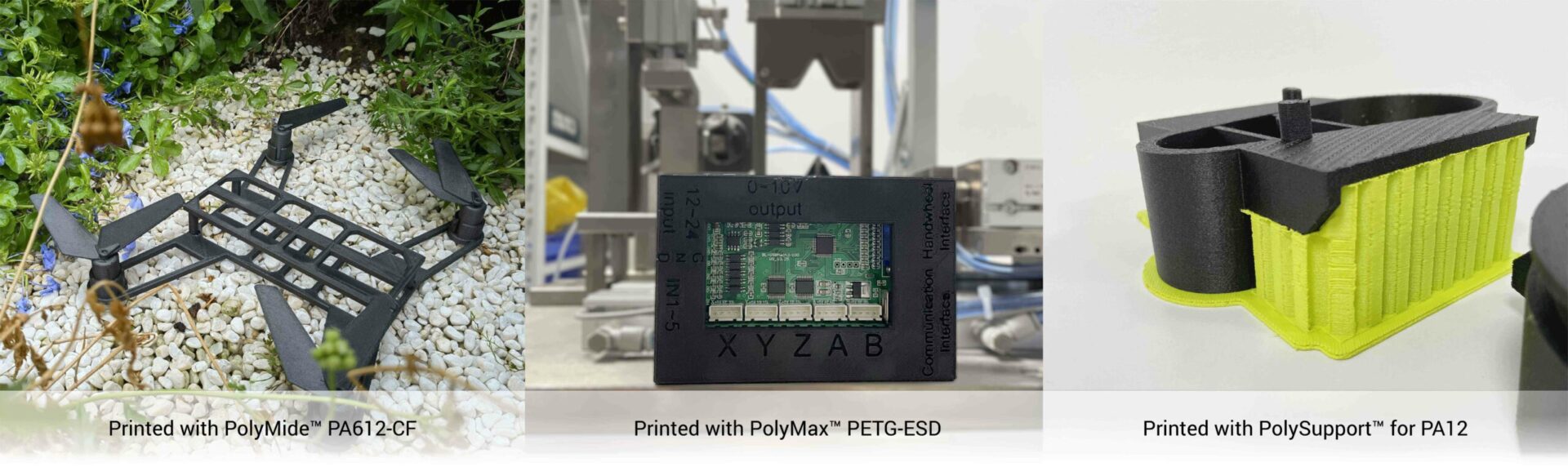
This award is recognition of Polymaker’s continuous innovation and dedication to the 3D printing industry. Polymaker will stay focused on high-performance 3D printing materials and will keep delivering material solutions to help realize widespread end-use production of 3D printed parts. At the end of the day, it was Polymaker customers that participated in the 155,000 votes received by 3DPI. In a popularity contest against leading consumer brands such as: Prusament, Filamentum, and eSun, and in the race against chemical giants such as GE Additive and BASF, it was Polymaker who triumphed to claim Material Company of the Year.
Polymaker rises to the top to take home the Creative Application Award at this year's TCT360 exhibition in Birmingham, UK. The LEGO Go-Kart created by Matt Denton in partnership with Polymaker impressed this year's judges and was a crowd favourite at the award ceremony, gaining lots of cheers even before the winner was announced. The Creative Application Finalist selection was filled with some fierce competition such as: Stratasys, BMW, Shapeways, Ricoh 3D and Gravity Industries among many other impressive projects.
Polymaker win 2022 Creative Application Award
The first fully-electric ridable giant LEGO Go-Kart from Matt Denton. Scaled up 3D printed LEGO blocks printed on desktop FFF printers assembled into a fully working electric Go- Kart.
While the aesthetics of the Go-Kart are inspired by the LEGO Technics kits #1972 released in 1985. It was the electrification that created a challenge that required an original solution to a design that was not intended for human transportation. The use of desktop 3D printing enabled Matt to print all the bricks needed to assemble the Go-Kart with only a few non-3D printed parts, such as motors, brakes, and electronics. The end result is something that looks like it shouldn't drive, but when it does it's guaranteed to put a smile on your face.
Matt Denton and the LEGO Go-Kart
The realisation that a fully functional Go-Kart can be 3D printed on your desktop and assembled with parts you can buy online will inspire people to think inside the blocks. Creativity can be applied to old concepts the same as new.
Absolutely everyone loves it, Matt has brought a childhood toy to life like something out of a pixar movie. Even the folks at LEGO spoke to Matt saying they love what he's doing. Matt displayed the Go-Kart on the Polymaker booth at FormNext 2021, the crowd response has been overwhelmingly positive with many people stopping to take pictures and ask Matt questions. Matt's YouTube videos have gained over 1.8 million views related to the Go-Kart project.
Sjoerd & Gisela collect the Creative Application Award at the TCT award ceremony
All materials for the Go-Kart were supplied by Polymaker. Matt choose a wide range of filaments as the material needs differed from brick to brick. The chassis bricks were printed in PolyMax™ Tough PLA, the gears in PolyMax™ Tough PETG, the axles in PolyMax™ Tough PC, the tyres in PolyFlex™ TPU95. Finally, PolyLite™ PLA was used for some cosmetics parts. The combination of materials allowed Matt to take advantage of the mechanical properties of a wide range of filaments which were all compatible with his desktop printing setup.
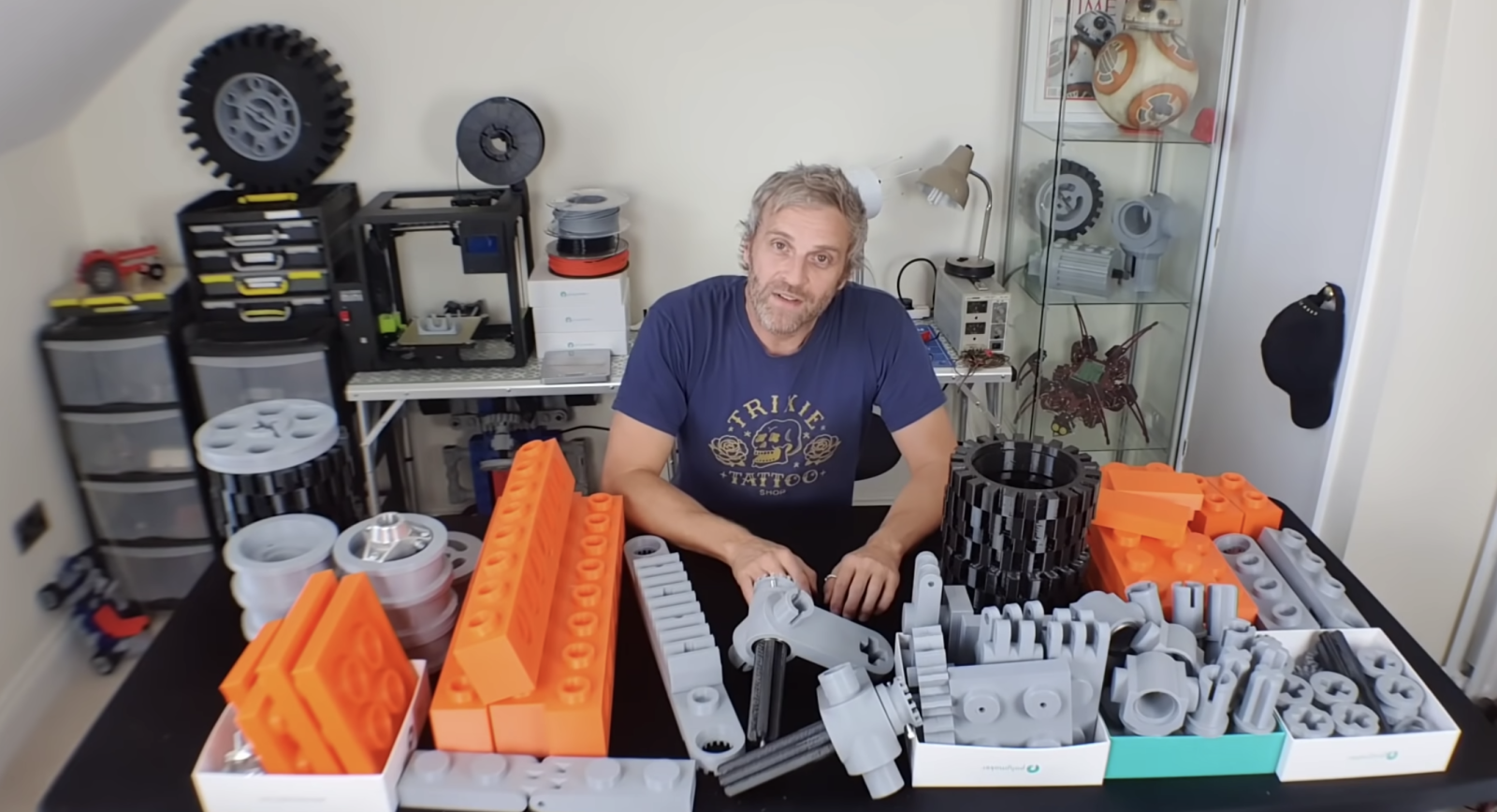
3D printing is the only way to create this Go-Kart. Even if you paid the ludicrous amount of money for the tooling of these giant blocks, a solid injection moulded brick would be too heavy. 3D printing allowed Matt to have a number of slight variations to the bricks so that they could hide bearings or route cables without spoiling the aesthetic. With a desktop 3D printer over 95% of all the parts were printed at home by Matt on a 300mm x 300mm x 300mm print bed.
Electric vehicles are the way forward as we reduce our carbon emissions. Showing people that they can print their own vehicles at home reduces heavy emitting big industry and localizes manufacturing. This, in turn, eliminates the need to ship products around the globe further reducing emissions. 3D printing gives the ability to manufacture locally and this project is a great example of what can be achieved with inexpensive desktop 3D printers at home in your bedroom.
The classic design touches a special place in our younger hearts, reminding us of a simpler time when our creativity could run free. Everyone who played with LEGO when they were a child is instantly reminded of the familiarity of this project. A large scale model on its own would still invoke this feeling, but the fact that this isn't just a model, its a rideable electric vehicle which adds even more charm to the project.
Just as the original technics kit from 1985 inspired Matt to take up engineering. He now hopes that this new generation armed with 3D printers can realize their potential by following in Matt's footsteps. The ability to design and customize parts enabled Matt to create the Go-Kart without spoiling the LEGO aesthetic. Matt's videos break down the individual parts and he explains the design choices he made. With over 20 years working in the special effects industry for TV & Film, Matt's experience paired with a fun project provides an engaging educational and problem-solving demonstration.
Matt has already posted his next video which involves some PolyMax™ PC drifting sleeves. The 3D printed sleeves will fit over the rear tyres greatly reducing the grip that the PolyFlex™ TPU95 provides, instead, the rear wheels can spin with less friction allowing Matt to drift the Go-Kart around.
Matt will reprint the PolyMax™ PETG gears to give a higher speed ratio necessary for drifting.
Wear Damage on the PolyMax™ PC drifting sleeves after intense usePoly