In recent years, continuous innovation and progress in 3D printing technologies has led to an increase of applications in the architecture industry. Compared to traditional building molds using wood or steel, 3D printed molds only require inputting the design into 3D printing software to produce the final mold or shape. This is one of the clear advantages of using 3D printed molds for construction because of its efficiency and sustainability.
PolyCore™ ABS-5012, a PolyCore™ pellet, was selected as the material of choice for printing a mold for a custom concrete wall. This cost-effective, 20% glass fiber reinforced ABS compound material is ideal for 3D printed molds and tools used in a low-temperature ranges (ambient up to 80℃). By utilizing this material for mold printing and leveraging the large size and high precision of 3D printing technology, we created a 5m(L)*0.4m(W)*2m(H) branding wall for Polymaker.
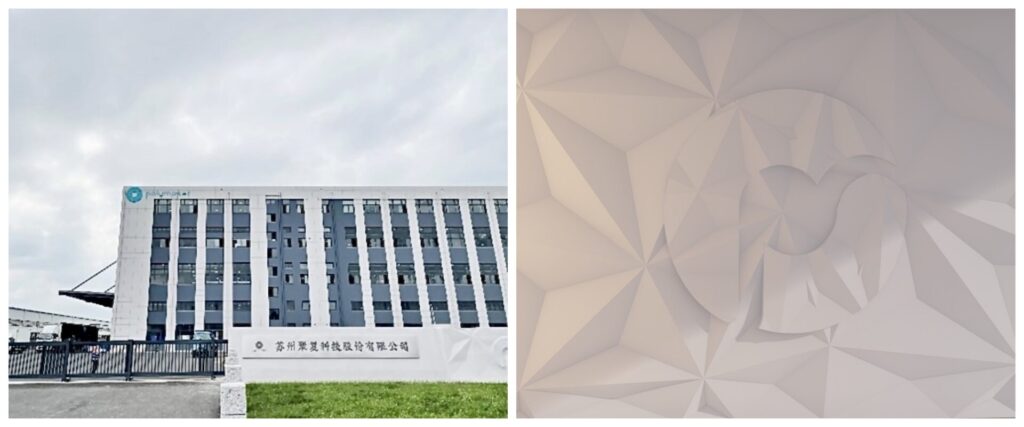
This article will reveal the step-by-step process of building this wall with PolyCore™ ABS-5012.
Initially, the designers went beyond the usual design constraints of traditional molds and createed a multi-faceted pattern, incorporating the Polymaker logo, thus utilizing the creative freedoms provided by using 3D printed technology.


For the next steps, the mold designs were printed and processed, taking a total of 16 hours. After printing, the final full-scale form was cut into four parts and the inner surface underwent additional post-processing to ensure a smooth concrete cast finish.




The mold components were then assembled using bolts, while an external support structure was assembled to facilitate a stable concrete pouring process.



Finally, the concrete pouring and demolding stage commenced. This phase involved constructing a reinforcing mesh structure inside the 3D printed form, pouring in C30 concrete, allowing it to air-dry, and then demolding and coloring the structure.



The end result was a branded wall with the Polymaker logo, which then went on to win the TCT Asia Best Application Award - Industrial Product Applications in 2024.


Through innovative research and development, Polymaker continues to enhance the stability and durability of its materials, particularly pellets, for construction applications. This aids in achieving a higher level of design freedom, shorter lead times, reduced production costs, and a lower carbon footprint in the manufacturing process.
It is anticipated that 3D printed buildings will become a key driver in the construction industry's development in the near future, delivering marvelous designs through this new additive manufacturing method, fostering innovation across the board.
SHANGHAI, May 6, 2024 - Polymaker recently won the TCT Asia Best Application Award - Industrial Product Applications for its pellet product, PolyCore™, in the 3D printing of architectural stencils. This honor not only recognizes Polymaker's innovation and excellence, but also its continued leadership in the 3D printing industry.

With the continuous innovation and advancement of 3D printing technology, utilizing the advantages of 3D printing's high precision and large size, PolyCore™ was selected as the product range to produce a 5m(L)*0.4m(W)* 2m(H) brand wall for Polymaker.
Polymaker collaborated with Shanghai Mechanized Construction Group, a subsidiary of Shanghai Construction Group (SCG) and Shanghai Kuying Technology Co., Ltd. to develop and print this wall.
The design of the wall features the Polymaker logo and a multi-faceted pattern, which demonstrates the strength and advantages of 3D printing when implementing creative design ideas in the construction Industry.

The completion of this wall is of great significance. SCG said: “The application of 3D printing technology in large scale shaped concrete formwork will revolutionize the speed and accuracy of manufacturing such as molds in municipal and construction projects. Compared with traditional molds, 3D printing technology effectively reduces the manufacturing cost and construction time, and promotes the transformation of traditional construction to digitalization, industrialization, intelligence, and low-carbonization.”
It is a significant achievement for Polymaker to be recognized at TCT Asia (The most influential additive manufacturing event in Asia) and to be awarded the Best Application Award - Industrial Product Applications, further reinforcing Polymaker’s position and portfolio within the construction field. Detailed information about this case, please click "Architecture Molding Case Printed with PolyCore™".

“We are extremely honored to win this award at TCT Asia this year. It not only recognizes our team's unremitting efforts and continuous innovation, but also brings new insights to the construction industry. Polymaker has been a pioneer in applying 3D printing to the construction field, providing a variety of pellet products for the construction industry including indoor design and outdoor construction, and successfully creating projects such as Taopu Central Park Bridge in Shanghai, China, the “Liuyun Bridge” in Chengdu,China, and Namthaja’s Rakah Roundabout Sculptures. In the future, the brand will also continue to devote itself to technological innovation and product optimization to bring more intelligent manufacturing possibilities to the construction industry and make buildings glow with the beauty of intelligent manufacturing.” Polymaker CEO Dr. Luo Xiaofan said.
In addition to the Best Application Award - Industrial Product Applications, Polymaker was also honored as a “10 Years Exhibitor” on the occasion of the 10th anniversary of TCT Asia. This honor represents Polymaker's longstanding partnership and close relationship with TCT Asia, as well as the brand's continued contributions to the 3D printing industry.

In the future, Polymaker will continue to uphold the spirit of excellence and innovation, expanding the boundaries of the additive manufacturing field, providing customers and partners with superior solutions, and ultimately advancing the development of additive manufacturing technology.
With the industrial-grade 3D printing technology gradually challenging traditional manufacturing processes such as machining and injection molding, additive manufacturing has expanded from prototype production to more critical applications in end products.


Recently, a motion control company that provides high-precision direct-drive motors was designing suitable connectors for FFC (Flexible Flat Cable) in their research and development equipment. FFC are commonly used connection structures in electronic devices, and the company needed to place them in customized connectors to connect rotary motors and optoelectronic switch devices.
Initially, the company approached an aluminum processor for a quote, but the response forced them to seek alternative solutions:
- MOQ (Minimum order quantity) limitation: 50 pieces per item
- Processing limitations: Some slot designs were too complex for traditional machining processes
- Unstable lead time: A two-week lead time with no guarantee of transportation time.
Compared to aluminum machining, 3D printing technology not only offers faster production speed but also enables lighter part weights. Additionally, 3D printing allows for the simultaneous production of parts with different specifications, achieving customized requirements more economically and efficiently. In the end, the company decided to collaborate with Amesos mfg and Polymaker to produce connectors for FFC.

In this collaboration, the customized connector features multiple holes and slots in its internal design, serving the purpose of later assembly and positioning. The connector is designed in two parts, and once assembled, it can securely hold the FFC inside, with its ends connected to the rotary motor and other electrical components.
The rotary motor drives the continuous rotation of the FFC, while the connector allows for separation and rotation. The design also includes limiting slots to prevent the cable from tangling or breaking. After the parts are printed on the same day, the customer can immediately proceed with the trial installation.



Considering that the FFC ribbon cable will experience continuous friction as it rotates with the rotary motor, the material choice for the connector must be wear-resistant while providing protective properties. In addition, the electronic components require ESD-safe characteristics. PolyMax™ PETG ESD from Polymaker becomes the ideal choice for the material used in producing these parts.
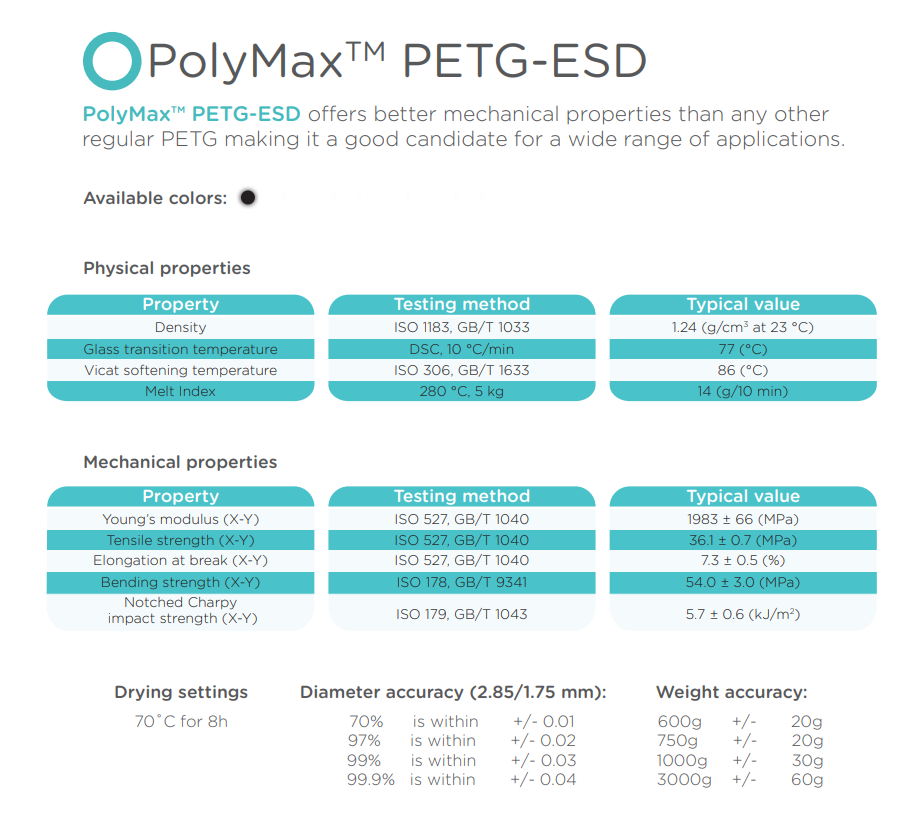

PolyMax™ PETG ESD not only offers higher strength, impact resistance, and temperature resistance compared to PLA but is also easy to print. Its ESD-safe properties make it suitable for a wide range of applications in the electronics industry, including tooling fixtures, functional prototype design, and electrical enclosure manufacturing.

Through the collaboration between Polymaker and Amesos, the customized production reduced the costs by 85% compared to aluminum machining, and the printed parts were delivered and installed within three days. This signifies that additive manufacturing:
- Enables small-batch customization, reducing production lead times by months and significantly lowering indirect costs.
- Breaks design limitations imposed by traditional processes, allowing customized parts and complex designs to be produced in a more cost-effective and efficient manner.
- Helps customers respond to market demands more quickly without the need for excessive equipment costs or expensive tooling investments, enabling operational diversification.
- Facilitates digital production, overcoming supply chain disruptions and eliminating unnecessary inventory.
Project Introduction:
Robot combat is a competitive game where participants use self-made robots of equal weight, following the competition standards, to engage in battles within designated arenas and limited timeframes using any technical means except those on the prohibited list.

Pain Points:
Traditional combat robots are predominantly made of metal plates or HDPE materials to ensure the overall stability of the robots during intense battles. Each level of the competition imposes different requirements on the robots, which means participants need to design multiple robots, significantly increasing the design and production costs. Additionally, every match consumes robot components such as internal drive motors, which reduces the lifespan of the robots. Therefore, protecting the motors from intense impacts has become a pressing issue for participants to address.

3D Printing Solutions:
With the rapid development of 3D printing technology, the range of 3D printing materials has expanded, and flexible materials are increasingly used by participants to address collisions involving electronic components in combat matches. In addition, because the robot fighting competition is usually in accordance with the weight class can be divided into ant level, beetle level and amateur level, some players will according to the needs of the tournament to design their own robot parts, and then select the appropriate material for 3D printing, so as to reduce the design cost and weight.

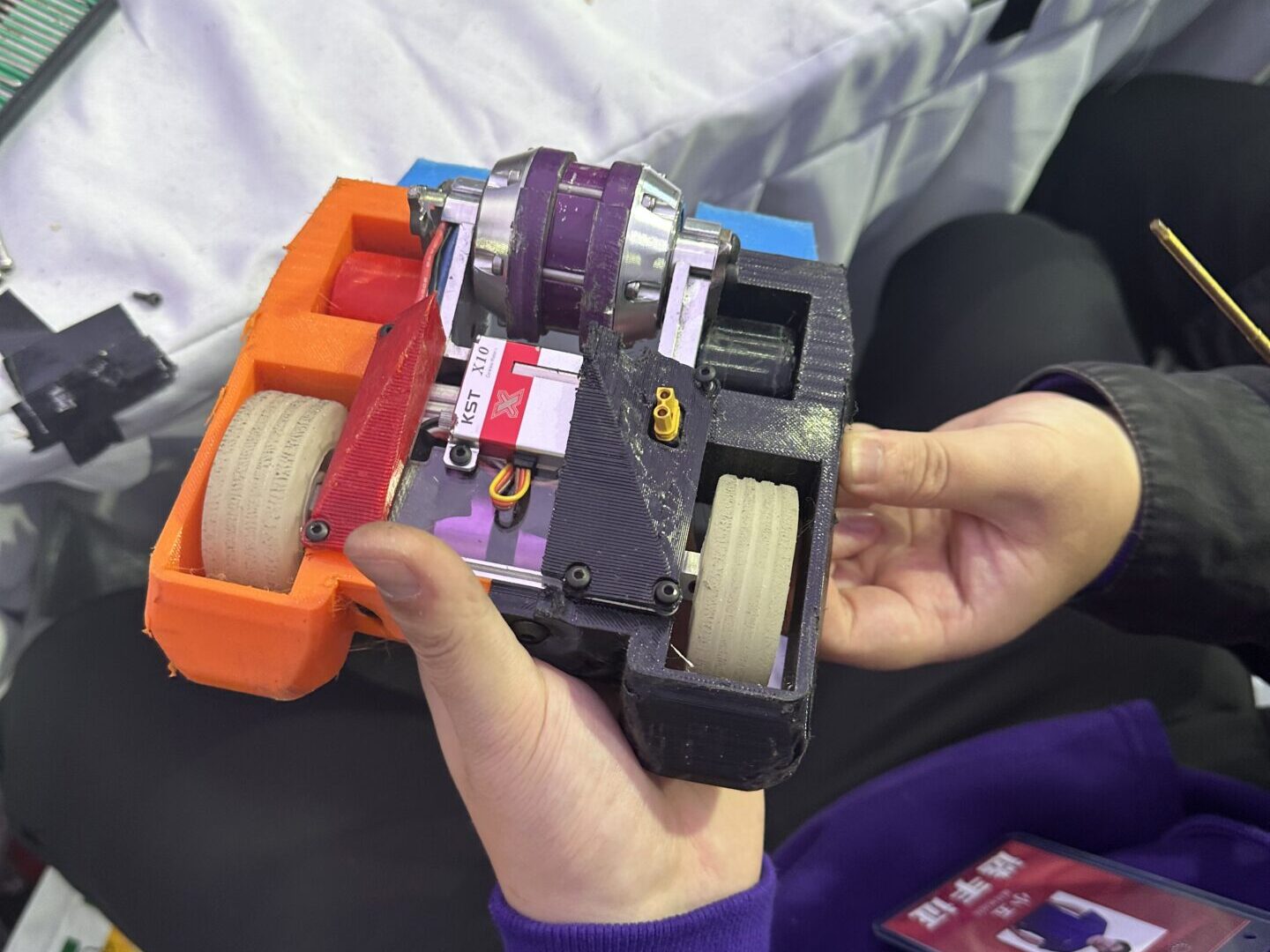
Why Polymaker:
Polymaker is reputational for its proficiency in material-extrusion based 3D printing area with comprehensive solutions. It offers three types of flexible printing materials: PolyFlex™ TPU90, PolyFlex™ TPU95, and PolyFlex™ TPU95-HF. PolyFlex™ TPU95, specifically, is a thermoplastic polyurethane material suitable for desktop-level 3D printers. It has a Shore hardness of 95A and can be stretched to over 3 times its original length without breaking. This material, with its strong interlayer adhesion and flexibility, allows print parts to securely encapsulate electronic components, protecting them from external damage. Compared to TPU90, it offers higher hardness and better absorption of external impacts among similar flexible materials. Additionally, by leveraging 3D printing, this material can achieve different levels of elasticity through model design and varying infill densities. This enables the customization of exclusive products and effectively reduces the weight of robots in their manufacturing process. Overall, PolyFlex™ TPU95 has become the favored material for robot external armor.



Overview & Outlook
In the future, with the widespread adoption of TPU95 in robot elastic armor, robot combat will experience further innovation and development. The flexibility and interlayer adhesion of TPU95 will effectively protect the internal electronic components of robots, extending their lifespan. Moreover, the flexibility of 3D printing technology will allow participants to customize robot components according to competition requirements, reducing design costs and robot weight. Innovation and collaboration will continue to be our guiding principles, making creation easier than ever before. We look forward to witnessing the breakthroughs and advancements brought by TPU95 elastic armor in the future robot combat arena.
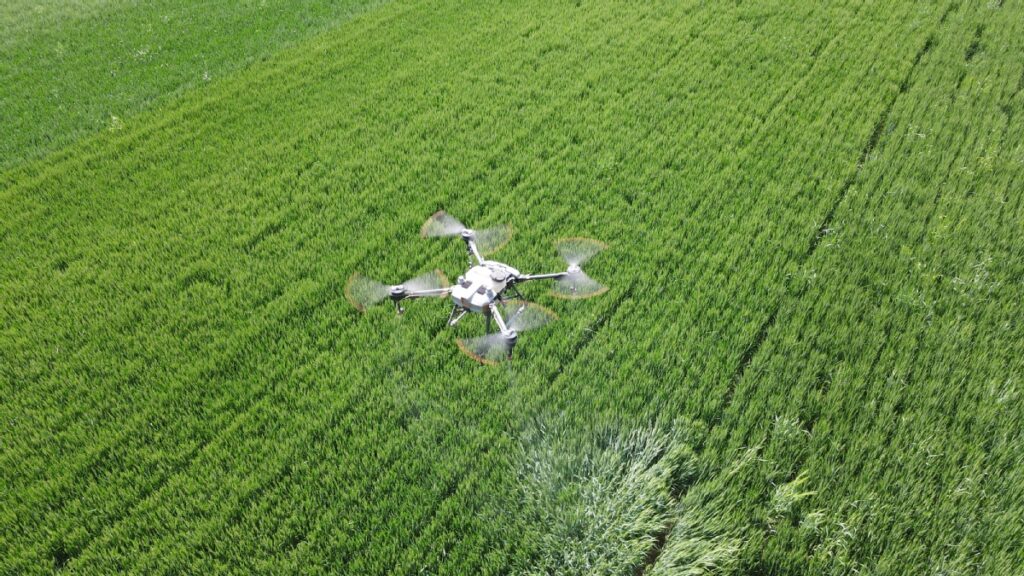
With the increasing level of mechanization, agricultural drones are being used for various agricultural operations, such as large-scale crop spraying. There are several types of agricultural drones available on the market including 4 types: flight control system, power system, spraying system, and frame structure. The spraying system is the main application module of 3D printing technology in this field, including the pesticide tank, water pump, nozzles, and related sensors.
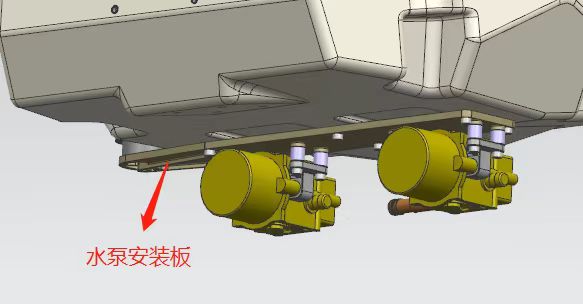
The pesticide tank of an agricultural drone stores the liquid for spraying, and during operation, the liquid is pumped out by the water pump. However, the vibration of the water pump affects the flight control system of the drone. Common methods use CNC aluminum plate processing to fix the water pump, but they have unavoidable disadvantages such as complex processes, poor corrosion resistance, low design flexibility, and lack of lightweight advantages. These factors can somewhat impact the production efficiency, payload capacity, and endurance of the drone.
By utilizing 3D printing technology, rapid prototyping and validation can be achieved, effectively solving the aforementioned problems and enabling small-batch production. After consideration, the manufacturer decided to collaborate with Amesos and Polymaker to create an additive manufacturing solution.
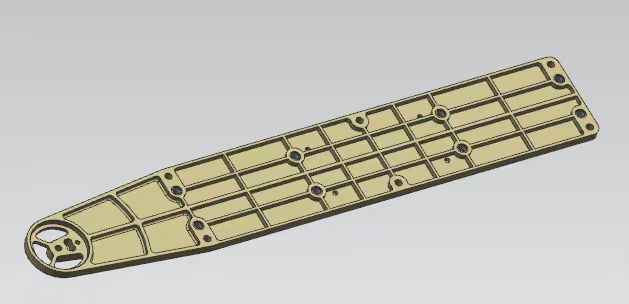
Amesos is primarily responsible for custom-designing water pump mounting plates that match the specific agricultural drone models to meet customer requirements. Within three days, four different versions were designed and tested, and the most suitable solution was selected and provided to the customer, successfully passing the installation tests. The next step was printing. The individual water pump on the mounting plate weighs around 400g, and the customer requires the installation of 2-3 water pumps. Therefore, the printed part needs to be made of a material that can withstand shocks and is not prone to breakage.
Polymaker is responsible for printing material selection. As a high-tech enterprise specializing in 3D printing materials, Polymaker began experimenting and comparing their diverse range of products as soon as they received the customer's requirements. Eventually, PolyMide™ PA612-CF material was chosen.
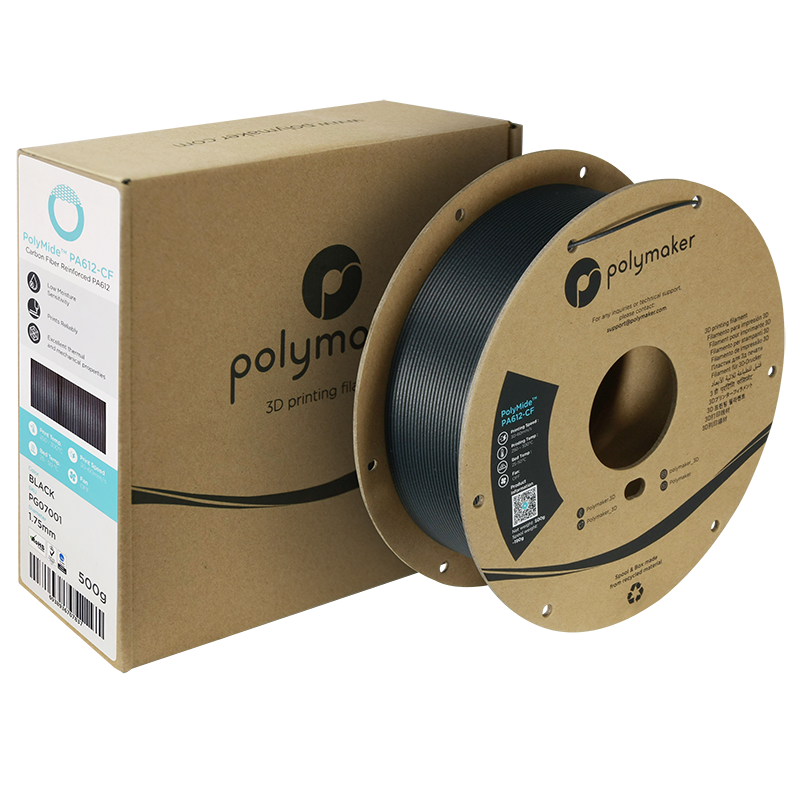
PolyMide™ PA612-CF is a carbon fiber-reinforced long-chain co-polyamide filament. Due to its chemical structure, this material has lower moisture sensitivity compared to PA6/66 and PA6-based materials, and better mechanical properties than PA12-based materials. Its advantages, such as high rigidity, toughness, and resistance to high temperatures, ensure that the water pump mounting plate printed with PolyMide™ PA612-CF is not affected by vibrations and maintains sufficient strength and stability. Additionally, its low water absorption allows for usage in humid environments, meeting the specific application requirements. Moreover, with the carbon fiber reinforcement and Warp-Free™ technology, products printed with PolyMide™ PA612-CF exhibit excellent dimensional stability, effectively prolonging the service life of the water pump mounting plate.
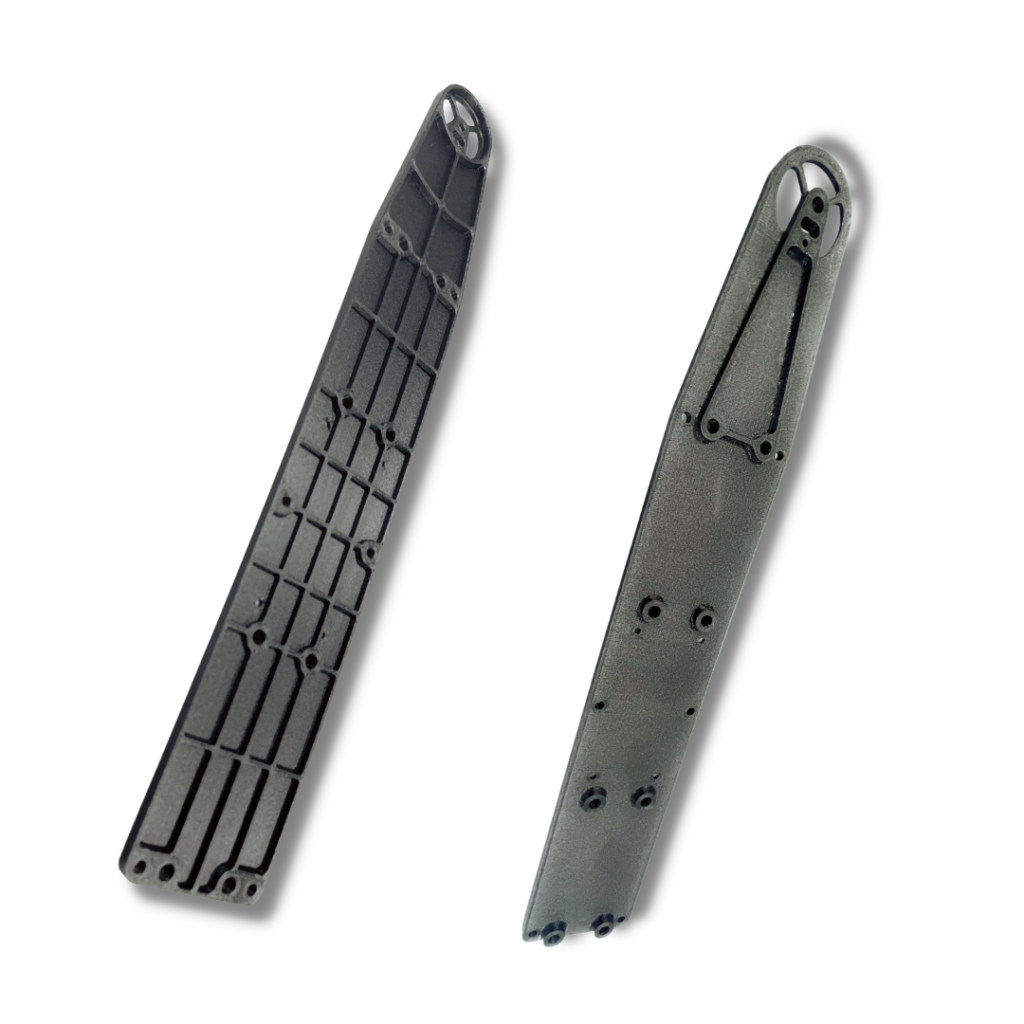
By employing 3D printing technology for the design and production of water pump mounting plates, the advantages of rapid prototyping, flexibility, and low cost are fully demonstrated. Manufacturers can quickly create prototypes, perform validation and necessary improvements, and immediately proceed with batch production and delivery. This process effectively shortens the product development cycle, enables the manufacturing of complex geometries and internal structures, and facilitates on-demand, high-efficiency production, greatly enhancing the economic benefits of production manufacturing.
Additive manufacturing technology is a rapidly evolving manufacturing technique that brings greater flexibility and efficiency to product design and production through digitization. It effectively compensates for the traditional machining processes such as turning, grinding, forging, stamping, and casting. As a result, the market shows high expectations for 3D printing technology.
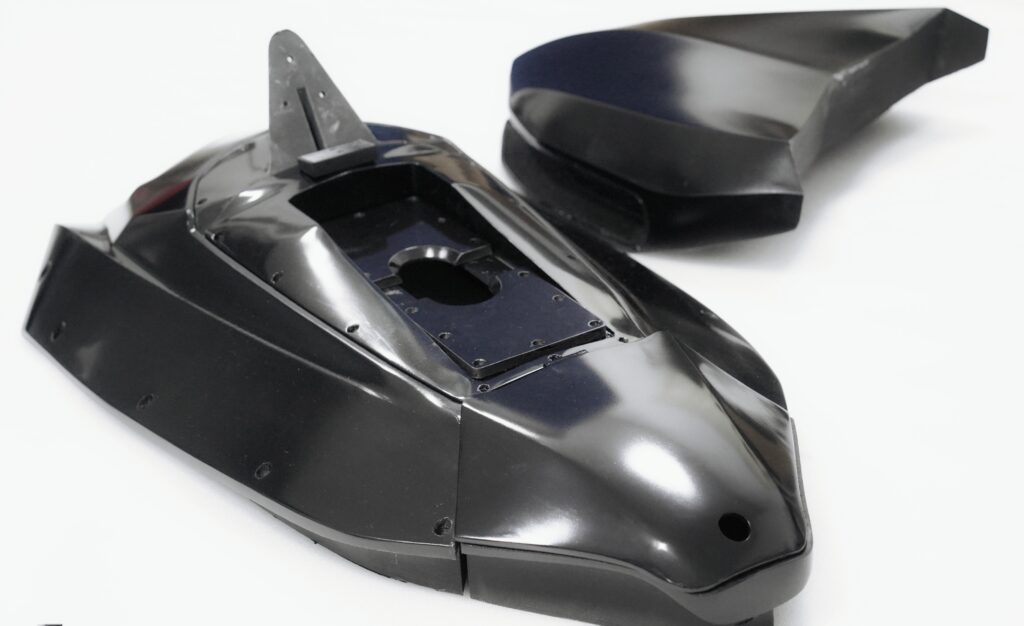
In the motorboat manufacturing industry, the advantages of 3D printing are evident, especially in terms of personalization and increased competitiveness. Polymaker decided to intensify its collaboration in this field. Meanwhile, A well-known motorboat manufacturer in the United States was adjusting their production methods and seeking a customized additive manufacturing solution. After combined efforts of research and comparison from Amesos and Polymaker, they ultimately selected PolyLite™ PETG as the printing material.
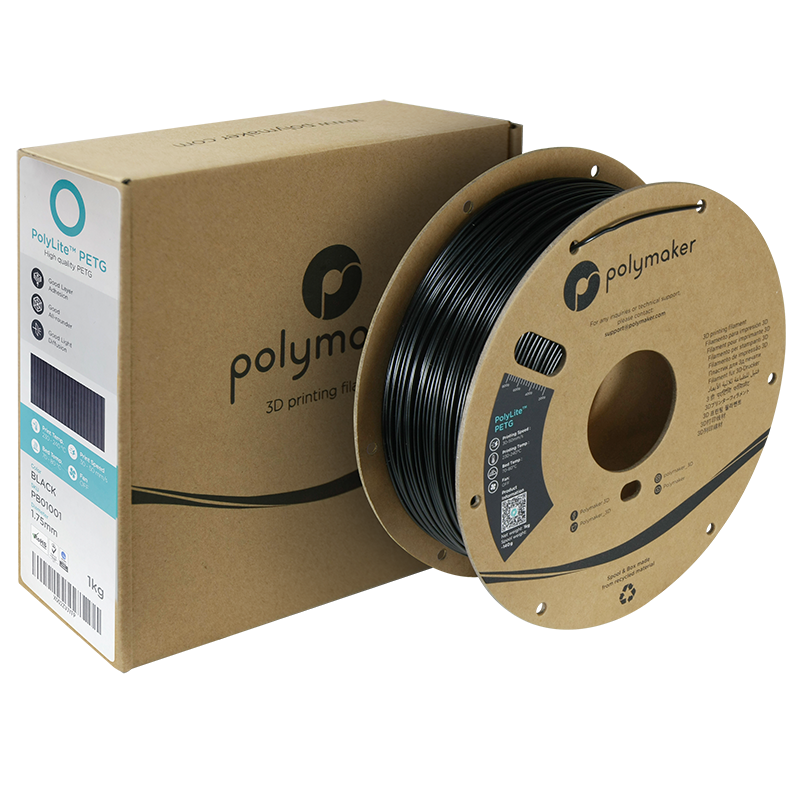
Compared to PLA, PETG has a higher heat deflection temperature and better overall mechanical properties. PETG also shows better dimensional stability compared to ABS. Overall, PolyLite™ PETG is a warp-free and cost-effective material. Its excellent impact strength, water resistance, and resistance to chemical corrosion make it the best choice for printing motorboat coverings. The total weight of this printing model, including the cockpit cover and front bumper of the motorboat, is approximately 15 kg.
During the printing process using PolyLite™ PETG, besides appropriate settings for nozzle temperature, bed temperature, and retraction, controlling the cooling fan is a critical factor that affects the print results. Due to PETG's crystalline characteristics, excessive cooling fan usage significantly reduces the interlayer adhesion of the printed parts, making them prone to breakage in the Z-direction and rendering them unsuitable for long-term use. On the other hand, completely disabling the cooling fan reduces surface smoothness and makes support removal more challenging. So selecting the appropriate fan speed has become a major challenge in this application. After several process tests and considering the structure of the motorboat components, the engineers settled on a fan speed of 20% to achieve a good balance between surface quality and layer adhesion.
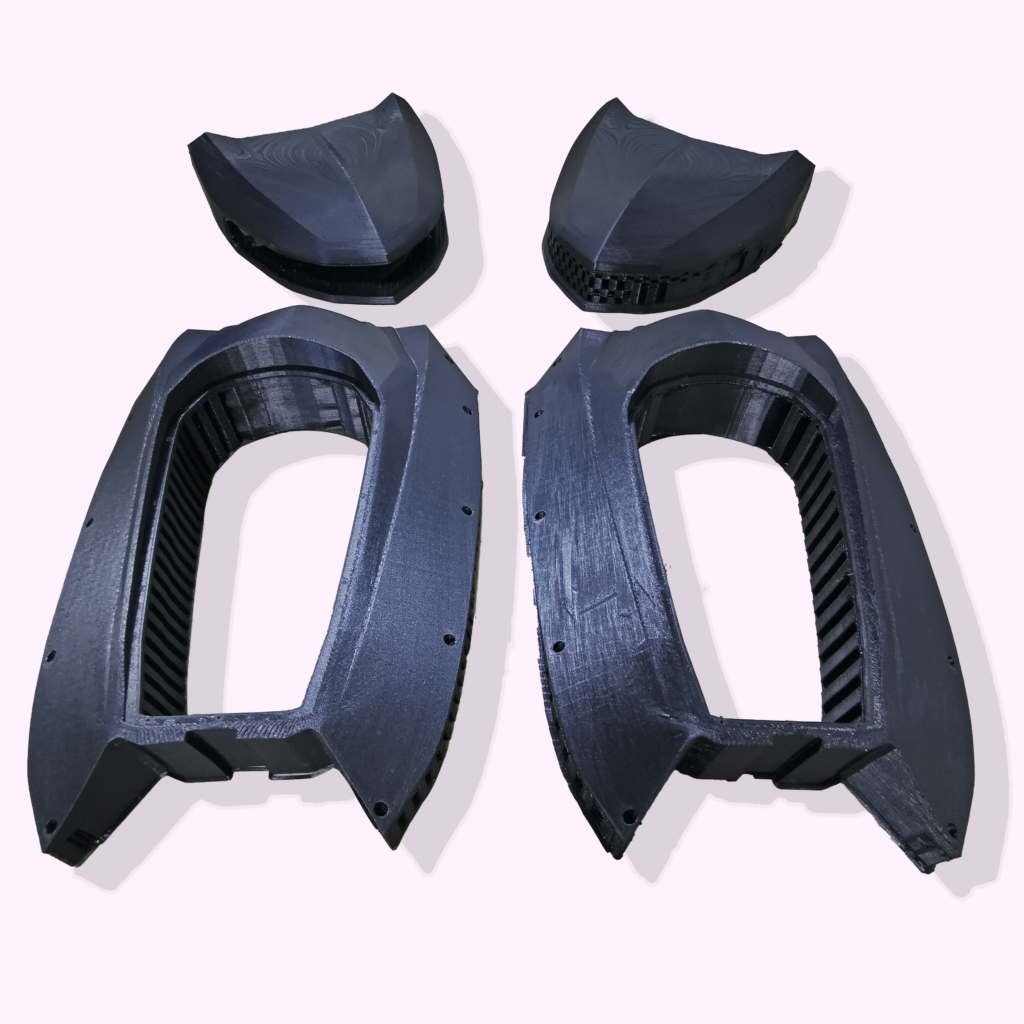
Thanks to the superior performance of PolyLite™ PETG and the stable and precise printer provided by Amesos, the engineering design of the motorboat's cockpit cover and front bumper was successfully completed. These parts were then used for small-batch continuous production, with a printing efficiency exceeding 163 cm3/hr (200 g/hr). This achievement not only represents a significant application success for Polymaker in the motorboat manufacturing industry, but also signifies the greater possibilities, increased freedom, and higher flexibility in driving innovation and experimentation.
Our long-term strategic partner and friend LulzBot has released the latest addition to their TAZ line of desktop 3D printers, the TAZ SideKick. This printer is available in two sizes and is designed to be highly configurable, so that customers can match their machine to their needs.
The LulzBot TAZ SideKick is now available in two build volumes and is the most affordable LulzBot to date. This highly configurable machine allows customers to build a personal desktop 3D printer comprised of all the features they want and need in their very own 3D printer.
The TAZ SideKick is faster, simpler, and ready to print out of the box with free software. This new printer allows users to select machine color and build volume along with adding other options now or later like build surface, electronics, and any of the LulzBot Universal Mount System Tool Heads.
One of the greatest features of this 3D printer is the self-replicating story which brought us back to the very first RepRap project: over 50% of the 3D printer is 3D printed with PolyLite™ PETG, in the constantly expanding LulzBot printer farm located in Fargo, North Dakota.
LulzBot is dedicated to open source, meaning users can easily and affordably replace any worn components by downloading the files from the LulzBot GitLab. In addition, all LulzBot 3D printers are built to last with quality components in Fargo, North Dakota, USA.
Learn more today at LulzBot.com
TAZ SideKick Ordering Information
The LulzBot TAZ SideKick is available for order immediately. To view the TAZ SideKick configurator, go to LulzBot.com/SideKick.
PolyLite™ PETG is an affordable PETG filament with balanced mechanical properties and ease of printing. PolyLite™ PETG is just as easy to print as our regular PLA (PolyLite™ PLA) while offering an additional 20˚C heat resistance and more durability. This lends PolyLite™ PETG to more functional applications where PLA would lack the durability or heat resistance such as lighting fixtures, vibrational parts or more functional product design prototypes which makes it a perfect choice to print TAZ SideKick functional parts.
PolyLite™ PETG is available for customers in 12 colors in 1kg spool, and 2 diameters (1.75 mm & 2.85 mm). PolyLite™ PETG can be purchased from
Our website: www.polymaker.com
Amazon: Polymaker PETG Filament
Resellers: Find your nearest reseller here
Polymaker rises to the top to take home the Creative Application Award at this year's TCT360 exhibition in Birmingham, UK. The LEGO Go-Kart created by Matt Denton in partnership with Polymaker impressed this year's judges and was a crowd favourite at the award ceremony, gaining lots of cheers even before the winner was announced. The Creative Application Finalist selection was filled with some fierce competition such as: Stratasys, BMW, Shapeways, Ricoh 3D and Gravity Industries among many other impressive projects.
Polymaker win 2022 Creative Application Award
The first fully-electric ridable giant LEGO Go-Kart from Matt Denton. Scaled up 3D printed LEGO blocks printed on desktop FFF printers assembled into a fully working electric Go- Kart.
While the aesthetics of the Go-Kart are inspired by the LEGO Technics kits #1972 released in 1985. It was the electrification that created a challenge that required an original solution to a design that was not intended for human transportation. The use of desktop 3D printing enabled Matt to print all the bricks needed to assemble the Go-Kart with only a few non-3D printed parts, such as motors, brakes, and electronics. The end result is something that looks like it shouldn't drive, but when it does it's guaranteed to put a smile on your face.
Matt Denton and the LEGO Go-Kart
The realisation that a fully functional Go-Kart can be 3D printed on your desktop and assembled with parts you can buy online will inspire people to think inside the blocks. Creativity can be applied to old concepts the same as new.
Absolutely everyone loves it, Matt has brought a childhood toy to life like something out of a pixar movie. Even the folks at LEGO spoke to Matt saying they love what he's doing. Matt displayed the Go-Kart on the Polymaker booth at FormNext 2021, the crowd response has been overwhelmingly positive with many people stopping to take pictures and ask Matt questions. Matt's YouTube videos have gained over 1.8 million views related to the Go-Kart project.
Sjoerd & Gisela collect the Creative Application Award at the TCT award ceremony
All materials for the Go-Kart were supplied by Polymaker. Matt choose a wide range of filaments as the material needs differed from brick to brick. The chassis bricks were printed in PolyMax™ Tough PLA, the gears in PolyMax™ Tough PETG, the axles in PolyMax™ Tough PC, the tyres in PolyFlex™ TPU95. Finally, PolyLite™ PLA was used for some cosmetics parts. The combination of materials allowed Matt to take advantage of the mechanical properties of a wide range of filaments which were all compatible with his desktop printing setup.
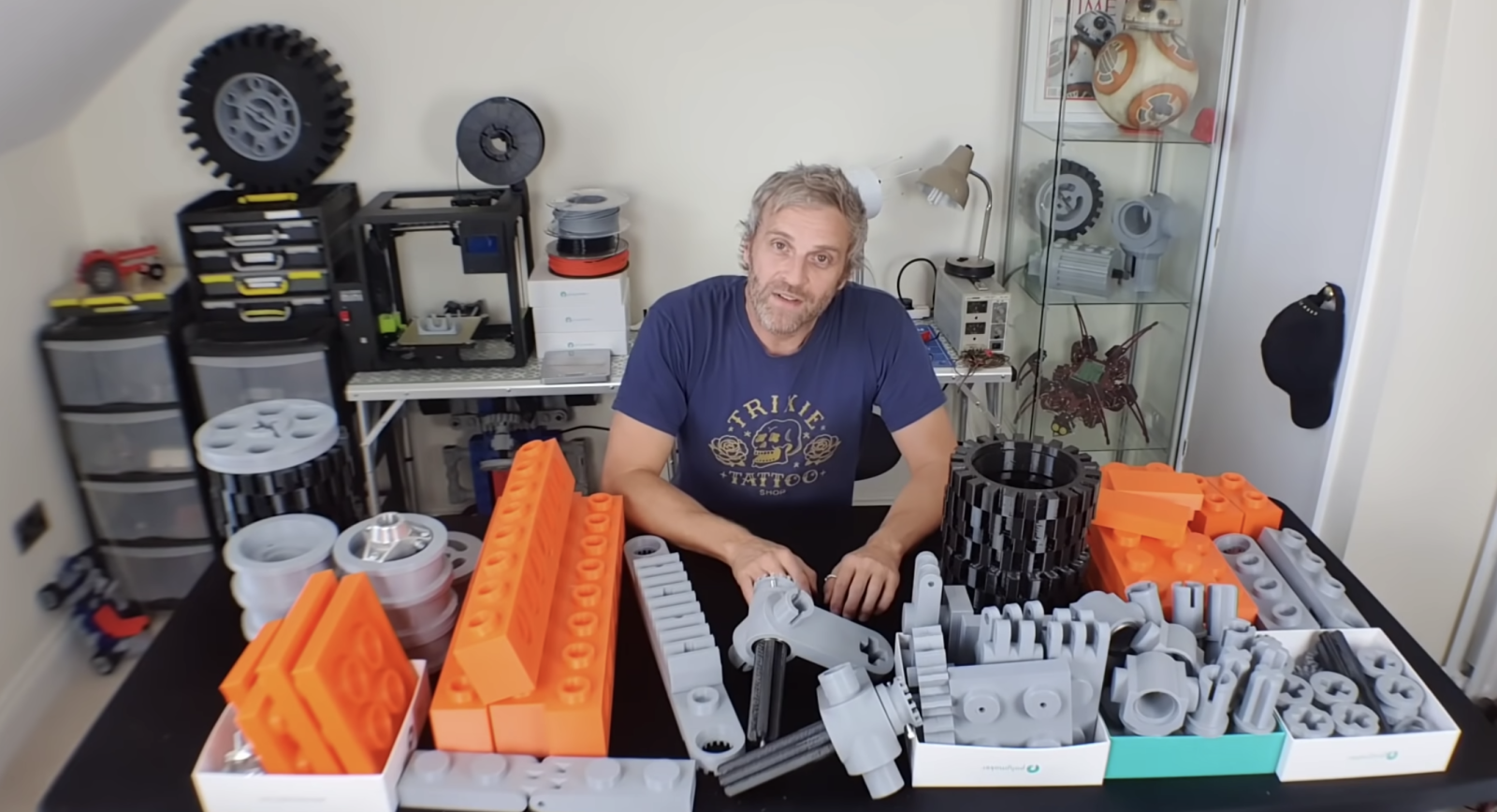
3D printing is the only way to create this Go-Kart. Even if you paid the ludicrous amount of money for the tooling of these giant blocks, a solid injection moulded brick would be too heavy. 3D printing allowed Matt to have a number of slight variations to the bricks so that they could hide bearings or route cables without spoiling the aesthetic. With a desktop 3D printer over 95% of all the parts were printed at home by Matt on a 300mm x 300mm x 300mm print bed.
Electric vehicles are the way forward as we reduce our carbon emissions. Showing people that they can print their own vehicles at home reduces heavy emitting big industry and localizes manufacturing. This, in turn, eliminates the need to ship products around the globe further reducing emissions. 3D printing gives the ability to manufacture locally and this project is a great example of what can be achieved with inexpensive desktop 3D printers at home in your bedroom.
The classic design touches a special place in our younger hearts, reminding us of a simpler time when our creativity could run free. Everyone who played with LEGO when they were a child is instantly reminded of the familiarity of this project. A large scale model on its own would still invoke this feeling, but the fact that this isn't just a model, its a rideable electric vehicle which adds even more charm to the project.
Just as the original technics kit from 1985 inspired Matt to take up engineering. He now hopes that this new generation armed with 3D printers can realize their potential by following in Matt's footsteps. The ability to design and customize parts enabled Matt to create the Go-Kart without spoiling the LEGO aesthetic. Matt's videos break down the individual parts and he explains the design choices he made. With over 20 years working in the special effects industry for TV & Film, Matt's experience paired with a fun project provides an engaging educational and problem-solving demonstration.
Matt has already posted his next video which involves some PolyMax™ PC drifting sleeves. The 3D printed sleeves will fit over the rear tyres greatly reducing the grip that the PolyFlex™ TPU95 provides, instead, the rear wheels can spin with less friction allowing Matt to drift the Go-Kart around.
Matt will reprint the PolyMax™ PETG gears to give a higher speed ratio necessary for drifting.
Wear Damage on the PolyMax™ PC drifting sleeves after intense usePoly
Polymaker recently worked with 3DQue Systems, a company that retrofits existing 3D printers for hands-free part removal and high-volume production. They are the first company who use PolyCast™ as support to print metal parts and automate this process with the Ultimaker S5.
Quinly automation system
3DQue’s automation system, Quinly, is a virtual printer operator, that can be installed on Raspberry PI and connected to 3D printers. When installed, Quinly can queue preloaded Gcodes, auto-level, execute part removal after a print job is completed, and start the next print job. 3DQue designed its VAAPRTM print bed that provides 500x adhesion when heated and allows easy release when cooled, without additional adhesives. Automated part removal is achieved using a gravity-assisted mechanism: Quinly incorporates a mechanical motion of the printer head/bed, to sweep off printed part, before starting the next print job. Quinly also provides real-time data, failure notification, and Livestream access to the print. By eliminating a significant portion of the manual tasks in a print job (filament still needs to be changed manually), Quinly reduces per part cost by 80%.
Fig (1) Quinly equipped Ultimaker
PolyCast™: Easily Removable
In this specific case, 3DQue automated metal 3D printing in a new and innovative way: Metal and PolyCast™ filament are extruded into build and support structures using a dual-head printer. PolyCast™ filament served as an effective raft material and was fully compatible with Quinly’s VAAPR™ surface. The printed rafts had excellent bed adhesion at 60°C and were fully released at 35°C. This allowed all parts to be autonomously removed from the printer via the wiper arm mechanism included in the Quinly for Ultimaker S5 automation system. The printer required only 10 minutes to cool and clear the print bed between print jobs.
Among a few other support materials 3DQue evaluated, PolyCast™ stood out for its performance in clean removal.
Fig (2) Flow chart for using Polycast™ as a support for metal prints before sintering
PolyCast™: Ash-Free
And then, printed parts were sintered with the rafts and supports in place. The PolyCast™ filament was burned away, leaving only 0.003% residue. Sintering without a raft was tested as well: the PolyCast™ rafts did not fuse with the metal filament and were easily removed by hand.
PolyCast™ is a PVB-based material designed for metal investment casting. It shares a similar formulation with the well-known PolySmooth™ and comes with ash-free technology that enables clean removal. PolyCast™ is also safe and easy to post-process. It is smoothable with IPA in Polysher™, or similar tools.
Fig (3) Ash content comparison between with Ash-Free and without Ash-Free
PolyCast™ rafts make Quinly fitted Ultimaker printers compatible with many metal filaments on the market. The raft easily slides off the bed once cooled, making metal filament bed adhesion issues a thing of the past.
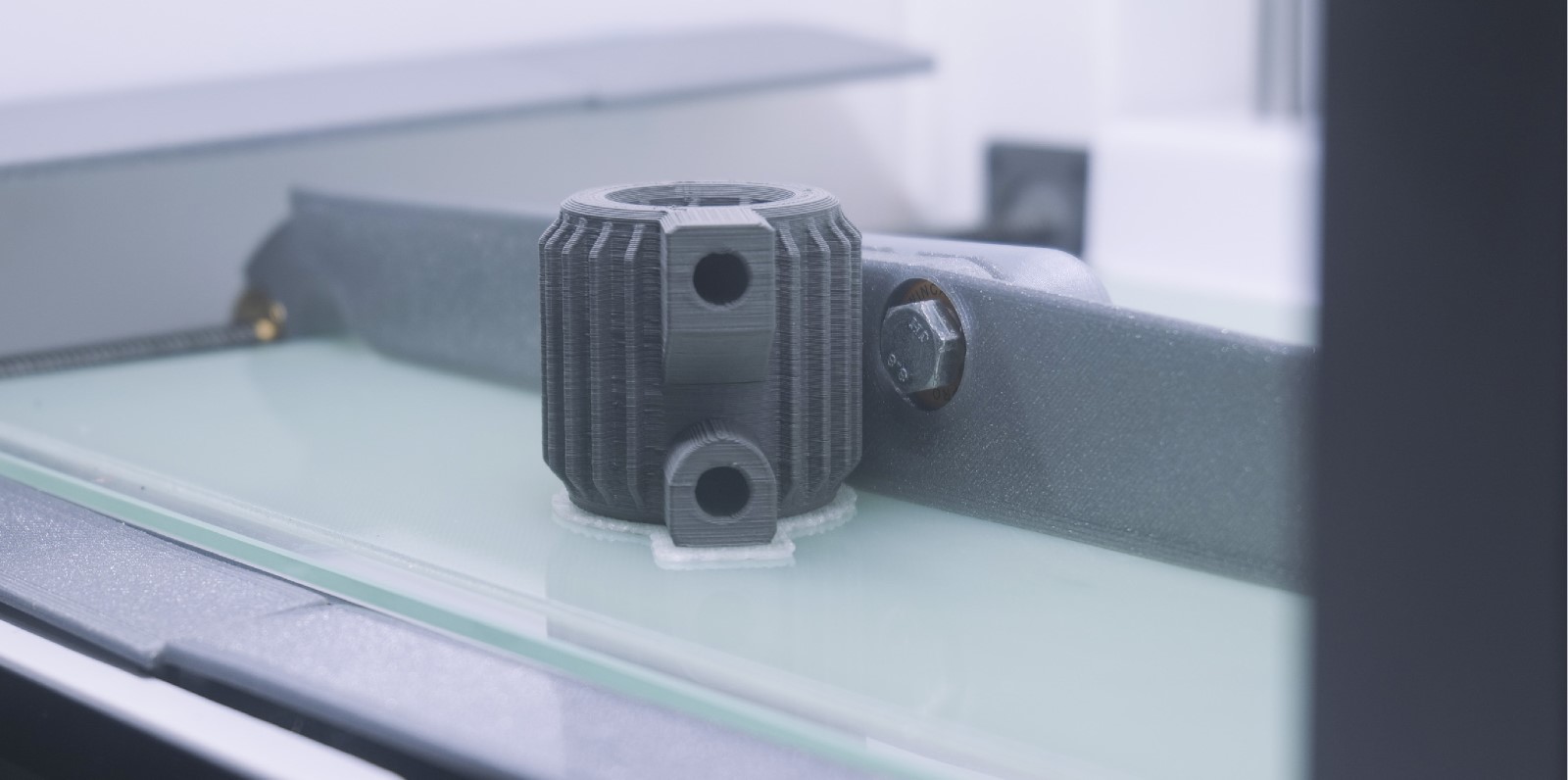
Demonstrated by 3Qque, PolyCast opens a potential avenue to mainstream manufacturing processes of metal parts. Beyond investment casting, in which PolyCast has gained significant attention, this case study brings an inspiring application of PolyCast. Due to the clean burnout nature of PolyCast, complex geometry in metal part fabrication is made possible by printing the PolyCast filament as support to the metal filament.
What’s more? Automation of the printing and part harvesting, enabled by systems such as Quinly, could make high-volume complex metal part production feasible and economically competitive.
Wisconsin Precision Casting Corporation (WPCC) is one of the leading investment casting companies that are using Ultimaker printers in combination with Polymaker filaments. WPCC has been using 3D printing for over 30 plus years. The use of printed patterns for prototype investment castings has become recognized by the industry but is yet used for massive production.PolyCast™, due to its dimension stability, print consistency, ability to polish, and low-ash feature, allowed them to streamline the investment casting process and significantly cut cost. Prior to usingPolyCast™, WPCC used several different methods including other forms of 3D printing, and wax injection to create customized patterns. They turned to Polycast in 2019 along with collaborating with Ultimaker printers.
PolyCast™ is a PVB-based material designed for metal investment casting. It shares a similar formulation with the well-known PolySmooth™ and comes with ash-free technology that enables clean burnout. PolyCast™ leaves an ash residue less than 0.003% after the burnout process operated at 600°C. PolyCast™ is also safe and easy to post-process. It is smoothable with IPA in PolySher™ or similar tools.
Figure(1) Comparison of ash content between with and without Ash-Free™
PolyCast™ is formulated to maintain excellent printability. By simply replacing the wax molding with PolyCast™ 3D printing, one could perform the rest of the investment casting process seamlessly. The nature of 3D printing, however, enables customization and iteration and significantly cuts down both the cost and lead time by eliminating the tooling process. The overall process of investment casting enabled by PolyCast™ is similar to the original process.
Figure(2) Flow chart of PolyCast™ in industrial investment casting
For example, WPCC found that it cost only $0.696 per cubic inch if PolyCast™ is used. It is less than one-third of the cost of the other pattern fabrication methods. During the testing process, they found that PolyCast™ -enabled process,
- Creates precise castings
- Is less expensive to print than purchased printed patterns
- Is faster to cast than purchased printed patterns
Figure(3) printing and casting parts from WPCC
Wisconsin Precision has used printed patterns for many years to create a prototype and low volume production castings. It is a key element of WPCC’s business strategy to provide rapid prototype investment castings for R&D projects and to acquire new customers.
The TJU Racing Team(Tongji University Racing Team) successfully announced their new racing car model, the TR21, at the 2021 New Car Model Public Announcement on October 12, 2021, in the 101 Lecture Hall of Jiren Building, Jiading Campus.
Polymaker participated in the event as one of the sponsors, and Cui Yue, a professional racer in the Porsche Carrera Cup Asia, was invited to drive the TR21.
Picture 1 | Polymaker Attended the 2021 New Car Model Public Announcement of TJU Racing Team
The TR21 is the 14th racing car independently designed and manufactured by the TJU Racing Team. The new model achieves significant innovations over previous models, oftentimes by using Polymaker’s 3D printing materials.
Picture 2 | Picture Stripes of TR21 Public Announcement
Strong Power Core
With the Triumph 675 3-cylinder engine as its power core, the TR21 uses a dry lubrication system, dual-cycle cooling system, and a more stable fuel supply system. The model is also equipped with a pure titanium exhaust muffler and hollow titanium alloy half-axles to reduce weight more efficiently. Having the power core and newly developed variable intake system work together heightens the performance of each part even further.
New Body Structure
The TR21 adopts the body structure of a full monocoque, replacing the former structure of a mono-frame. The carbon fiber layer, aluminum honeycomb panels, and PMI foam are used to provide higher strength and torsional stiffness while also keeping the body lightweight to ensure ideal weight distribution. Key parts of the body, like monocoque inserts and aerodynamic wing ribs, use PolyMide™ CoPA from Polymaker as the base material to give the parts structural stiffness.
Picture 3 | 3D-printed Front Wing Rib using PolyMide™ CoPA
The PolyMide™ product series are 3D printing filaments developed from Nylon. By adopting Polymaker’s patented Warp-Free™ technology, PolyMide™ products not only have the same engineering performance as typical Nylon materials but are also easy to print with a minimum size limit. PolyMide™ CoPA was developed from a copolymer of Nylon-6 and Nylon-6,6, a material with balanced mechanical strength and toughness. Along with the good printability, this material gives dimensional stability with its temperature resistance up to 180˚C, making PolyMide™ CoPA an ideal material for parts like gears, engine mounts, pipe connectors, and high-speed airflow pipes that are used in harsh environments.
Picture 4 | Main Characteristics and Material Properties of PolyMide™ CoPA
Innovative Aerodynamic Devices Design
The upgraded body and aerodynamic devices of the TR21 are some of its biggest highlights. Aerodynamics, which dominates the car’s design, has always been the ultimate goal for the TJU Racing Team. After observing systematic design processes and multiphysics simulations, the new aerodynamic devices is able to reach a down force of up to 1075N at the speed of 20m/s, improving the car’s external flow and aerodynamic sensitivity while significantly enhancing its curve speed. The flow deflector in the aerodynamic devices was 3D printed using Polymaker’s PolyMax™ PC material. Not only did the 3D printing material increase the car’s aerodynamic performance, but it also greatly reduced the cost and hours required to produce the flow deflector, with the only sacrifice being structural weight.
Picture 5 | 3D-printed Tail Deflector Using Polymaker PolyMax™ PC
The PolyMax™ product series are advanced 3D printing filaments produced by Polymaker’s patented Nano-Reinforcement technology, all of which have excellent mechanical properties and printing quality. PolyMax™ PC is a high-performance, polycarbonate-based filament boasting strength, toughness, heat resistance, and printing quality, lending itself to engineering applications, specifically when higher resistance for impact and vibration is needed, like in fixtures and fixing tools, furniture, small motor mounts, UAV, 3D printer parts, etc.
Picture 6 | Main Characteristics and Material Properties of PolyMax™ PC
Polymaker’s Polysmooth™ has also been used to print the front flap variable section, wing, and suspension lug cover for the TR21. Using alcohol-polishing in the materials’ post-processing allows the external flow of the whole vehicle to be optimized.
Picture 7 | 3D-printed Front Flap Using Polymaker’s PolySmooth™
PolySmooth™ is a unique and easy-to-print filament, specially designed for "freeing both hands" in post-processing. After printing with this material, Polysher™ is then applied to create a smooth surface. PolySmooth™ helps models that are difficult to polish be post-processed into a smooth surface, like statuettes or role-playing props, making PolySmooth™ optimal for product design and prototype creation as it produces a result similar to injection molding.
Picture 8 | Main Characteristics and Material Properties of PolySmooth ™
Brand New Chassis System
After a detailed analysis of tire characteristics, the original tires were replaced with Hoosier 16” high-performance racing slick tires. To match this tire, a new chassis system was designed for the TR21, equipped with a brake-by-wire stabilizing system to improve the vehicle’s dynamic performance.
Upgraded Electronic Control System
The TR21 continues to develop its electronic control system, using professional MoTeC ECU to have accurate control of the electronic throttle, pneumatic shift, and variable intake manifold while supporting wireless data acquisition. Also, the new steering wheel controller integrates radio communication, clutch-by-wire, brake-by-wire stability, ejection start control, traction control, and adjustment functions for various strategies, allowing drivers to enjoy its unlimited potential.
Picture 9 | TR21 Public Announcement Picture Groups
At this event, the TJU Racing Team announced their driverless vehicle plan for the first time, and they hope to see driverless technologies used in the next generation of TJU racing cars when they compete in the University Formula Race.
Polymaker has been actively involved in developing applications of 3D printing technology in the automotive and racing industry. Applying 3D printing materials allows for reduced costs, shortened production cycles, personalized customization, and lightweight parts to a certain extent. The diversity of Polymaker’s filaments also makes crafting different racing car parts more feasible, pushing the application of industrial-grade filament to be even more common. Polymaker's industrial-grade products include reinforced materials based on nylon mixed with carbon fibers and glass fibers, which improves their thermal properties and stiffness for interlayer bonding strength. There are also PC high fire-retardant materials and polymer alloy materials, both of which have high heat resistance and toughness.
We hope that 3D printing technology will be used widely when manufacturing and producing cars and racing cars in the near future.
Polymaker unveiled the "Liuyun Bridge", a 3D printed polymer bridge built jointly by Shanghai Construction Group Co., Ltd., Polymaker, and Shanghai Kuying Technology Co., Ltd., in Yimahe Park, Longquanyi District, Chengdu in 2021. Inspired by the free-flowing shape of the stagecoach and dancing silk, “Liuyun Bridge” achieves bold innovations in landscape design using new technology and materials unlike ever before while managing to overcome many obstacles in the 3D printing process. Polymaker was largely responsible for the conception and completion of this project, providing the materials and spearheading the exploration of landscape bridge design.
The printing process of "Liuyun Bridge"
Innovating on the printing process, the “Liuyun Bridge” takes advantage of Polymaker’s materials and creatively employs new technology to complete its construction not only quicker, but also with higher quality. The bridge manages to shorten its construction period using the Kuying Tech’s 5-Axis Milling and Additive Manufacturing Integrated Machine (BGAM), which allows for uninterrupted 3D printing to continuously occur at all hours of the day without any manual interaction, finishing the printing of “Liuyun Bridge’s” main components in only thirty-five days.
Polymaker guarantees the bridge’s stability and safety for years to come with their polymer pellets PolyCore™ ASA-3012, a material with excellent anti-aging. Another new method used to improve the printing process, closed-loop printing ensures there are minimal deformations by monitoring the temperature of the material during the printing process. The “Liuyun Bridge” consumes several tons of materials to finally complete its construction by printing segmented components to be assembled on site. Heavily dependent on Polymaker and their materials, “Liuyun Bridge” is a one-of-a-kind landscape bridge that only found its success through Polymaker.
A tremendous feat for 3D printing like the “Liuyun Bridge” never could have been accomplished without the collaboration between Shanghai Construction Group Co., Ltd., Polymaker, and Shanghai Kuying Co., Ltd. The actual design for the bridge was a product from both Shanghai Construction Group Co., Ltd. and Polymaker while Shanghai Kuying Co., Ltd. was responsible for the technology that let the material reach its fullest potential, crafting the bridge’s components with few errors and in an extremely short amount of time. However, Polymaker’s PolyCore™ ASA-3012 laid the foundation for this incredible achievement in 3D printing as the material made the design feasible in reality and continues to support its everyday use.
Materials used for “Liuyun Bridge”
The “Liuyun Bridge” used many new methods specific to Polymaker’s material to expand on the bridge’s performance. As the optimal material for the bridge, PolyCore™ ASA-3012 has mechanical properties suited for outdoor use and works specifically for large 3D prints, enhancing their dimensional stability and interlayer adhesion. Currently, most additive manufacturing technologies result in residual stress and warpage when using the fused deposition molding process. However, “Liuyun Bridge” incorporates a multi-factor analysis method, controlling ambient temperature and the three-stage melting of materials with different parameters like temperature, glass transition temperature, and single-layer printing time, to prevent any warping or deformations caused by rapid cooling.
During the printing process, heating the workspace before and after printing strengthens the layer-by-layer adhesion of the 3D printed materials, further reducing any possible problems with the printed components. Allowing the design of “Liuyun Bridge” to be fully realized, the high-precision five-axis CNC processing system of Kuying’s BGAM removes the typical margin of error reserved for printing deformations and heightens the accuracy of segmented printing components. With Polymaker’s PolyCore™ ASA-3012 being so advantageous, it solves many previous printing issues while still bolstering “Liuyun Bridge’s” stability and structure.
“Liuyun Bridge” is not the first bridge to use 3D printing technology though. Polymaker has worked in the construction of a few other 3D printed bridges, both at home and abroad, to realize new breakthroughs and accomplishments on each of their projects.
Polymaker’s 3D printed bridges in China
Shanghai Taopu Central Park Bridge
In 2019, China’s first composite landscape bridge was constructed in Shanghai Taopu Central Park by Shanghai Construction Group Co., Ltd., Polymaker, and Shanghai Kuying Technology Co., Ltd. As the first composite landscape bridge with one-time molding and a multi-dimensional curved surface, the Taopu Central Park Bridge breaks through the shackles of traditional bridge design and frees the landscape bridge to be more flexible and diverse in space. Like with “Liuyun Bridge”, the Taopu Central Park Bridge owes its conception and dynamic shape to Polymaker and their materials.
The printing process of this 3D printed landscape bridge went through nearly one hundred printing tests to be continuously optimized. The super-large gantry 3D printer, jointly developed by Shanghai Construction Group Co., Ltd. and Kuying Technology Co., Ltd., allows for more diverse printing of larger sizes while still improving the printing’s accuracy. The Taopu Central Park Bridge is also composed of Polymaker's PolyCore™ ASA-3012 material, so the bridge can withstand long-term exposure to the sun and rain.
Quanzhou Bridge
Polymaker installed China’s second 3D printed bridge in the ecological belt of Baiqi Lake in Quanzhou, Fujian in 2019 as the second collaboration between Shanghai Construction Group Co., Ltd., Polymaker, and Shanghai Kuying Technology Co., Ltd. Spanning 17.5 meters, the Quanzhou Bridge also uses Polymaker’s PolyCore™ ASA-3012 material for its body and drastically improves on the manufacturing time of traditional concrete grouting, completing its construction in only five weeks.
With the bridge’s manufacturing saving a considerable amount of time, it continues to compete with traditional grouting by providing strength that can withstand a pressure of two kilonewtons for each square meter, guaranteeing its ability to carry any amount of traffic. The Quanzhou Bridge utilizes a segmented design, unlike the Taopu Central Park Bridge, allowing its segments to be connected through a unique link mechanism to meet necessary mechanical requirements. Together, Polymaker's PolyCore™ ASA-3012 and the BGAM print the different components of the bridge to be assembled and painted for the finished construction, like with the printing process of the “Liuyun Bridge”.
The future of 3D printed bridges
Polymaker plays a role throughout the entire process of their 3D printed landscape bridges, covering many different facets from modeling, construction, and conception to data design. 3D printing technology truly emphasizes the "link of artistic inspiration with the power of science and technology" by pushing both sides to reach a product that stands above expectations. Polymaker’s application of 3D printing technology in landscape design greatly expands opportunities for technological innovation and exploration in the industry.
With 3D printing technology only continuing to grow, it has become an important consideration in constructing footbridges and large-sized printing quicker, with more cost effectiveness, and in a sustainable manner. Large-sized printing solutions are becoming more and more popular in different fields too, and Polymaker wants to fuel their growth by actively developing and producing materials that can bring ambitious projects to reality.
Without the material Polymaker has been creating, 3D printed bridges would never be as developed as they are now because Polymaker’s material not only provides the flexibility to meet any design’s needs, but also the strength to sustain the bridge for many years. Polymaker advances the world of 3D printing in more ways than only with their materials though. Their passion to push the industry and venture into unexplored territory has given 3D printing new capabilities and unimaginable possibilities.
Shanghai Construction Group Co., Ltd.:
Shanghai Construction Group Co., Ltd. is a leading enterprise in China's construction industry, ranking among the world's top 500 companies. Over the past sixty years, Shanghai Construction Group Co., Ltd. has repeatedly set records in the history of engineering construction in China and even in the world. It has contributed to many excellent projects in more than 100 cities across the country and in more than 30 countries and regions around the world. In recent years, Shanghai Construction Group Co., Ltd. has made every effort to promote national development, strengthen the synergy of the entire industry chain, and continue to form new commanding heights in business areas such as urban renewal, water conservancy, environmental governance, digital industrial construction, and construction services. They are now accelerating construction to become a widely acclaimed service provider for the whole life cycle of construction.
Shanghai Kuying Technology Co., Ltd.:
Shanghai Kuying Technology Co., Ltd. is a high-tech enterprise specializing in the research and development of super-large 3D printing solutions. The company adheres to the concept of "exploring future manufacturing methods" and is based on the innovative model of "integration of addition and reduction of materials, research and development of new materials, and intelligent control" in order to help manufacturing companies reduce costs and improve efficiency. The company’s existing intelligent equipment products include the Tech’s 5-Axis Milling and Additive Manufacturing Intergrated (BGAM), the high-speed pellet printer (SGAM), and the robotic additive manufacturing system (BRAM). These main products are widely used in architectural landscape, aerospace, shipbuilding, rail transit, energy, automobiles, medical products, and many other industries.
As one of the 20 art installations in ‘Design Shanghai 2021’, "Digital Circular Pavilion" is another innovative work of digital artist, Zihan Zhao, founder of the Spazio Z design studio. The sculpture is standing in front of the old Shikumen building in Xintiandi, Shanghai, with branches growing upward, and gradually forming an organic space to escape from the urban style of downtown Shanghai. The white surface finish of the installation contrasts strongly with the dark gray background color of Shikumen, attracting passers-by to explore and connect within.
Primarily focusing on the creation of digital art, 3D printing has become the go-to medium, transitioning digital artwork created in Spazio Z into the physical space. To achieve this, the studio has created several custom built large format 3D printers using FFF technology to create modular parts which can be assembled into a larger structure.
The Digital Circular Pavilion is the latest work to emerge from the studio. Printed in 800kg of Polymaker’s L3003, an industrial PLA filament designed for high volume printing in production, print farms and large projects. The individual sections of the pavilion are bolted together onto an aluminum armature which allows for easy assembly on site. The pavilion sections have been post-processed into one homogenous organic form by coating the printed surfaces in polyester filler and sanding smooth. This coating process helps to strengthen and protect the PLA from UV and heat radiation and provides a clean smooth surface which translates the form of the design, avoiding any textures or layer lines.
During the inspiration for the design, Zhao Zihan had one question in mind: How do we connect the independent and unrelated people in the city? People are invariably disordered and unpredictable. As a designer, all pre-planning is hypothetical. As a space device, how to realize people's exploration in the city block, social and self-satisfaction is generally accidental every time. Therefore, such a device is more of a medium, carrying a variety of space possibilities in order to bring people together.
"Digital Circular Pavilion" is a relatively transparent structure, but it still has the function of isolation. The circular form is a natural separation figure, the outer circle is open for visitors to sit and rest. While the inner circle is semi closed, which provides the possibility for a relatively private conversation. At the beginning of the concept, Zihan drew lines of different thickness, depth and density, reflecting the randomness and disorder of human activities, and then simulated them into topological forms through digital technology.
For this work, Zihan Zhao is more inclined to call it "an artistic landscape product", because the artistic expression of its form is far more than its function.
From sketch to parametric model, Zhao Zihan and his team members made a detailed and in-depth analysis on the physical force, overall load-bearing, structural curvature and other factors of a single module. After detailed analysis it was determined that PLA could be a suitable material when backed with an aluminum armature and coated in polyester filler. While there are materials with better mechanical properties available, the reliability and printability of PLA made this project possible. Spazio Z takes advantage of their own 3D printing factory, which can fully demonstrate the printing efficiency, assembly process, cost control and other aspects of production. This allowed more than three square meters of walls to be produced for load testing prior to final construction. Finally, Spazio Z completed the work at a lower cost than the same type of building using traditional methods.
Through the joint operation of 100 large-scale 3D printers, each module is printed separately in one month, and then assembled into five large module groups, which are transported to the site to complete the final assembly and fixation through aluminum alloy components. At the end of the exhibition, it can also be disassembled and recycled.
Zhao Zihan implanted his expectation in "Digital Circular Pavilion": to create a future in which devices or buildings can be reconstructed by digital technology
“Maybe it's just a starting point. When one day it's so common that it is not rare and fancy any more, it shows that it has become very popular." – Zihan
At that time, Zhao Zihan will also explore a new starting point, and the experiment to verify the interaction between architecture and human will never end.
Perfectly clear 3D printed parts are possible with PolySmooth™ and here is the story of one of our customers. Mattias has shared with us his process creating a pair of lenses for the kitchen fan lights.
From: Mattias Lundberg
July 22nd 2021
I made a thing! well, two actually. I needed to fix something in my home and like so many times before I resorted to 3d printing and my favourite filament Polysmooth. Hi, My name is Mattias Lundberg and I love 3D printing. I´ve been doing this as a hobbyist for 6 years now and love to make the impossible possible and to push the limits just to be able to hold the printed part in my hand or see it functioning the
way it was intended.
My task at hand this time was the light covers on my kitchen fan. Originally the lamps were very hot so my first attempt three years ago was with a super clear heat resistant material that...melted. But I realised that after all these years the original lights had been phased out to LEDs. THEY dont produce heat! Bingo! Lets try Polysmooth transparent!
The object this time is a simple yet complex shape that had to be separated into the lens as one part and the frame with clips as the other. The frame with flexible clips had to be printed separately with a 0.4 nozzle while the lens must be printed with a thicker nozzle and only as a single perimeter wall.
This products really is made for resin printing but when you are hell bent to make it with an FDM printer that's what you gotta do right.
Something really important in order to reach success is to know not only your personal limitations but also the slicers, printers and the filaments limitations and roll with it and use them to your advantage. In short, trick the printer and filament in doing what you want it to.
I tried many different orientations and techniques and had a lot of failed prints and semi good results until I found the way!
This is a round bulgy object, it needs to stand on its edge, have low layer height and around 190 degrees nozzle temp. And printed in vase mode or spiralized as its called in Cura.
Therefore I made a single perimeter box with the lenses bulging out on the longer sides and printed it really thick (2 mm) to make it look like the original piece. This way the nozzle could go round and round printing both lenses without any disturbances.
Next step was to simply cut it out of the box walls and treat it with 100% Isopropanol, let it dry and sand it before final IPA treatment and done! I was holding two perfectly shaped, very clear and sturdy lens shaped covers in my hand. The frame was glued on and the whole piece was snapped into place and I know its gonna last a long long time. Thank you Polymaker.
Check out Mattias post and video of the prints on facebook:
https://www.facebook.com/groups/polymaker/posts/2728308607433197/
Full size fender plug (1346mm x 660mm) 3D printed on MAKEiT2x4 Large Format 3D printer using PolyMide™ PA6-GF material made by Polymaker.
MAKEiT2x4 is a large format 3D printer able to print an entire quarter panel in one piece with industrial quality filament PolyMide™ PA6- GF from Polymaker. MAKEiT2x4 is designed and made by MAKEiT, Inc. in California.
The printer is equipped with a massive rectangular printing area of 1400x605x800mm and a powerful printhead, this makes it the premier choice for printing large automotive parts, like rectangular-shaped body models. In fact, it is recognized by the automotive aftermarket authority SEMA, the Specialty Equipment Market Association. The SEMA Show 2020 awarded our MAKEiT2x4 large format 3D printer the 2nd Best New Tool and Equipment Product.
With the printer MAKEiT 2x4 car designers and fabricators can print the original fender design, in full instead of different pieces welded together saving the time and energy spent to complete a puzzling process. It counts with an application where you can see the part being 3D printed in real time.
After days of continuous printing, when the model is finally printed and cleaned, you can test fit it right away onto the vehicle. The well tested piece can be used as a plug to make the production mold. Plus, by using the MAKEiT2x4 machine, you can keep all your original designs in house.
Due to the complex nature of making a perfectly smooth body plug, the material used to make the plug needs to be stiff and strong and able to withstand intense heat. After many trials of different kinds of filaments, we have narrowed it down to a couple filaments. Polymaker™ PA6-GF meets all the material requirements for 3D printing a good plug.
With the help of 3D scanning, computer-aided design, 3D printing and the right material, our clients are no longer sculpting clay plugs by hand. They especially love the 3D printing digital mirroring process. With a single click, a mirrored model can be printed automatically. In comparison, making opposite-side plugs perfectly symmetrical by hand is virtually impossible.
We’d like to share the following case study from one of with you from our amazing customers.
Ivan Tampi, owner of Ivan Tampi Customs, is an award-winning designer and fabricator specializing in widebody Corvette customization. He used to spend weeks making plugs by hand. With the help of MAKEiT2x4's large-format 3D printing technology, he is able to get 3D printed prototypes from the CAD design, without the need for additional tooling. He is now able to do more design work, build more exotic wide body kits faster, all at a lower cost.
A full-size passenger side rear fender cap is 3D printed on a heated carbon fiber print bed. This bed provides a massive 1400x605x800mm print envelope. The 0.6mm tungsten carbide nozzle on the powerful printer works wonders with the PA6-GF, producing 5 days of non-stop work, (except for the automatic pausing of the printer when the filament runs out). An innovative filament motion sensor detects filament exhaustion and other problems. Once a new roll of PA6-GF is installed, the printer will continue. By nature, PA6-GF is an abrasive and stiff filament. It needs a printing temperature in the range of 285C to 300C and an abrasion resistant nozzle to extrude well. Often, 3D printer bed leveling and calibration can be complicated and time consuming. But this is not the case with the MAKEiT2x4 printer. It has 100% automatic print bed leveling and calibration. The user only has to press a few buttons on the computer screen. The rest is done by the printer itself.
(3D Printed passenger side rear fender plug fitment test by Ivan Tampi Customs)
By using the digital mirroring process, the driver side rear fender is obtainable. This simple process creates a symmetrical model, and it can be 3D printed right away. The finished print is shown here.
Once the printing starts, we want it to be finished as planned, right? No one wants to see an incomplete
job. However, a random layer shift during printing poses serious risk. It can ruin the entire print. Many 3D printer users have encountered similar issues. It is very costly when printing a large size part. To prevent the "lay-shift", we have implemented the LSP (Lay Shift Prevention) in each 2x4 printer as a standard feature, ensuring reliable printing, job after job. A video clip about LSP can be found here ( https://drive.google.com/file/d/1FW9CdxKvBCXWwAC22lJqaLcFv5UnEByM/view )
A driver-side front fender plug is completed after 7 days of printing. As noted, there is support material and debris attached to the fender print. These can be easily removed before the fitment test.
After an initial fitting, the fender plug will be power sanded to make it as smooth as possible. During sanding, the nylon glass fiber print remains stable, unlike PLA. It doesn’t gum or melt at all! This is huge. The old headache of “how do I sand it” has become “I love it. I can sand it easily, as many times as I want.” Often, regular post processing filler materials like Bondo are applied onto the plug before next sanding.
While the printer is running on its own, a MAKEiT2x4 user can monitor the printing process, and control the printer remotely using a smartphone. When you visit your customer, you can show their part being 3D printed in real time!
According to Ivan, MAKEiT 3D printing technology has saved his company 75% of time and labor compared with their traditional plug-making process. 3D printing also ensures every part is symmetrical and keeps the harmonious proportion all the way through. Compared with other filaments earlier, PolyMide™ PA6-GF has become Ivan’s only go-to material. Nowadays Ivan Tampi Customs is able to turn their unique digital designs into real functional parts in days and weeks, and no extra tooling is involved.
Ivan’s beautiful widebody exotic cars can be found at:
Instagram: @custom_car_builder; @ivantampicustoms
Website: www.ivantampicustoms.com
MAKEiT2x4 Large Format 3D Printer is designed and built in California USA by MAKEiT, Inc.
Website: www.makeit-3d.com
Instagram: @largeformat3dprinter
Email: shelley@makeit-3d.com for purchase and resale opportunity
Laboratory Technologies Inc. (LTI) is a leading manufacturer of laboratory radiation instruments. It has been a supplier of laboratory radiation instruments since 1983, both in the U.S. and overseas. LTI caters to a smaller, specialized market comprised mainly of nuclear labs all over the globe.
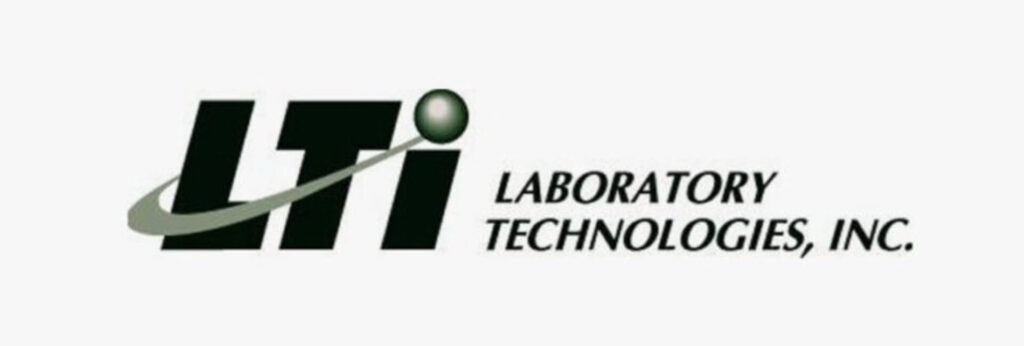
Metal Machining Had A High Cost and its Design was Restricted
LTI’s leading products include the Genesys 1000 series Gamma counters, Genesys Gamma 1 Single Well Gamma Counters, and Wiper Wipe Test Counters. The design of these products was limited by the machining process needed to make them. The original design was manufactured out of cold-rolled steel (CRS) in a single piece. The detector tower was a piece of steel pipe with a plate welded on one end. The plate was then ground down to make a closed pipe with a hole drilled into it. The other end was then threaded to allow a spacer to be screwed internally. Due to not being a simple structure, these two parts were especially expensive to make due to the machining involved.
3D Printing Allowed Smooth Product Development
LTI decided to find a suitable solution that could replace this costly process by using 3D printing in-house. After a few comparisons and trials, LTI purchased a Raise3D Pro2 Plus large-format 3D printer. LTI could experiment with a wide range of thermoplastics and brands thanks to the Pro2 Plus' high-temperature heating capacity. After some experimentation, LTI decided Polymaker polycarbonate (PC) was the right 3D printing material, also known as a filament, for manufacturing.
After choosing the best filament, LTI researched further and took advantage of 3D printing’s ability to accomplish complex angles and shapes that are too difficult to be fabricated in steel. For example, each corner is printed as a fillet instead of at the traditional sharp angle. The upper face is formed in a curved and modern outline. When LTI compared the 3D-printed parts with the equivalent machine-produced parts, the company realized that the new geometry improves appearance and safety. For these types of geometric features, traditional machining requires excessive tool head operating knowledge and a far more advanced solution.
The structure of the old model (left) is simpler than the new model (right)
Due to 3D printing’s ability to form any shape, LTI had a smoother process for their product development. Almost any outline and structure design were possible with 3D printing without additional tool changing. The appearance, as well as functional features such as assembly slots and air vents, were created precisely using CAD design software.
3D printed parts keep all designed features and are as accurate as machining
The iteration of parts development was quick because a Raise3D printer can produce many types of shapes while remaining user-friendly. The Raise3D Pro2 Plus is a smaller-sized large-format 3D printer, with a fully enclosed structure, and a 100-240V AC power supply. Therefore, the printer can be easily deployed anywhere using less space and power. LTI deployed Pro2 Plus directly next to its production line so the engineers could review any modification instantly.
Raise3D printers can be easily deployed and operated in an office environment
With Raise3D’s slicing software, ideaMaker, LTI refined numerous details in the 3D printing process for a few months, focused on achieving the best surface quality and dimensional precision. From ideaMaker’s template library, LTI selected the option with 0.1mm layer height which produces a final printing result with very high resolution and a smooth surface. When maintaining dimensional precision, LTI made the most of ideaMaker’s comprehensive toolset portfolio to mitigate filament shrink ratio. The shrink ratio determines the amount the extruded plastic will shrink when cooling. This results in an offset between the setting value and the actual value of the plastic flow width. ideaMaker allows users to define the extrusion process from multiple perspectives such as differentiating extrusion-related value for different segments, as well as applying a particular value to compensate for shrink ratio.
The Right 3D Printing Material is Essential for A 3D Printed Product
After testing different 3D printing materials, LTI found that polycarbonate (PC) was the best option. But not all PC filaments are the same. Polymaker’s PolyMax™ PC proved to be the best for LTI in the end. PC is the top choice for mechanical performance due to its excellent impact resistance and high stiffness among existing engineering-grade 3D printing filaments. As a result, a PC printed part can absorb impact and prevent deformation or cracks. In addition to these properties, PolyMax™ PC also has good printability. LTI found that a printed PC part was sufficient to protect the equipment. However, PC has a far lower density than CRS.
The success of LTI’s material application also relied on specific material science from Polymaker. For Gamma Counters and Wipers, UL fire rating is important. Flame retardancy prevents materials from burning and helps slow the spread of fire.
LTI immediately jumped at the chance to use Polymaker’s PolyMax™ PC-FR after its launch. PolyMax™ PC-FR’s has sufficient stiffness and impact resistance. Its ingredients are from world-leading polymer supplier, Covestro, which ensures both V0 performance in the UL94 flame retardancy test along with excellent toughness, strength, and heat resistance. PolyMax™ PC-FR also has the advantages of reliability and ease of use. LTI finally chose this material for its production.
A functional car jack printed by PolyMax™ PC
Finalizing 3D Printed Parts With Simple Post-Processing
LTI executed post-processing on printed PC parts as a last step of production. Once printing finished, parts were lightly sanded for 5-10 seconds to remove burrs and imperfections. All exterior parts were painted internally with a conductive nickel RF shielding paint, while external surfaces were primed to fill in the minor nooks and crannies resulting from printer extrusion. Once dried, they were again lightly sanded for 30-60 seconds and wiped clean. Then, a layer of hammered finish paint is used to give the parts a metal look.
The surface became nicely textured after simple post-processing
3D Printing Enables Better and Cheaper Products
After months of development, LTI achieved remarkable product optimization by means of 3D printing. By redesigning structures, new exterior plate by Polymaker’s PC was strong as previous design by CRS but 10 pounds (9.5kg) lighter. The reason is that PC density is only 1.2 gram/cm3 while CRS weighs six times more as 7.8 gram/cm3. In terms of cost, the total cost of a product from 3D printing process was only 25% of the original process. This was mainly resulted in 94% cheaper parts from 3D printing compared to machined parts.
Back in November 2013, Polymaker installed its first dedicated production line and developed a flexible 3D printing filament as the few flexible filaments available at the time had poor compatibility with different 3D printers. Polymaker fine-tuned the plasticity of the thermoplastic to produce a filament that was easy to print while producing soft and flexible printed parts. PolyFlex™ TPU95 marked the third product to join the growing Polymaker portfolio.
PolyFlex™ TPU95 is a thermoplastic polyurethane (TPU) based filament specifically engineered to work on most desktop 3D printers. It has a shore hardness of 95A and can stretch more than 3 times its original length.
Recently, we have seen a rapid increase in demand for flexible 3D printing materials used for various applications. In order to respond to market demand, Polymaker decided to launch two new colors of PolyFlex™ TPU95: BLUE & RED.
They are now available on www.polymaker.com and Amazon with both 1.75mm & 2.85mm diameters.
Sarolea is a revived Belgian motorcycle manufacturer that took on the historic Sarolea brand after the original company ceased production in the 1960’s. The revived brand now focuses solely on electric powered motorcycles, but at the heart of the company is the same passion of motorcycles that founded the original brand back in 1850.
Sarolea develop and manufacture their motorcycles from the ground up using in house technologies originally developed for track racing bikes. After gaining popularity of their designs on the race track, Sarolea decided to design a road going version of their first race bike the Manx 7. Sarolea have been using 3D printing technology at each stage of their production process and have established close technical relationship with Polymaker.
3D printing technology can bring huge advantages to the automotive industry in all aspects. Sarolea has integrated 3D printing into every stage of their production cycle, utilizing many different materials and their unique properties in the design, production and ultimately for the manufacture of parts that operate on the road and race bikes.
Stage 1: Design & RnD
Applications: Prototyping, concept design, design iteration
Advantages: low cost, short lead time, lightweight, design freedom, quick verification of appearance and functionality.
Description:
Both PolyMax ™ PLA and PolyMax ™ PETG are used for prototyping. For the Manx 7 electric superbike, the entire bodywork was prototyped using PolyMax ™ PLA. The printability, reliability and toughness play a role in this application. On the N60 model, Sarolea used PolyMax ™ PETG for bodywork prototyping. Compared to PolyMax ™ PLA, PolyMax ™ PETG is easier to sand and polish, offering an additional 20°C heat resistance compared to PLA. This allowed Sarolea to print and test body work with a professional finish.
PolyMax ™ PLA for bodywork prototyping
PolyMax ™ PETG for bodywork prototyping
Stage 2: Production
Application: mould making, production jigs, manufacturing fixtures
Advantages: fast and low-cost manufacturing of specific tools for custom parts, effectively reduce production cycle by printing in house. Print negative moulds for direct carbon fibre lay-up.
Description:
Sarolea are 3D printing moulds in PolyMide™ CoPA which they are using to produce final parts in carbon fibre. Both the Manx 7 and N60 have a carbon fiber monocoque chasis, this requires a number of intricate moulds that help with the lay up of the carbon fibre. PolyMide™ CoPA can withstand the high heat and pressures involved in vacuum curing process while the carbon fiber is baked in the autoclave. PolyMax™ PETG is also widely used to make production tools, jigs and fixtures necessary when assembling the bikes.
PolyMide™ CoPA mould
Stage 3: Aftermarket
Application: Printing production ready parts, customization and spare parts
Advantages: Print finished parts in advanced materials, provide full customization to customers on existing parts, keep digital database of spare parts.
Description:
Sarolea features a number of 3D printed parts in final production thanks to the advanced materials that Polymaker offer. PolyMide™ PA6-CF is used widely in the high velocity air flows and Polymaker™ PC-PBT in use as a cell holder within the custom-made batteries. PolyMax™ PC-FR offers a fire rated material to print fixtures and holdings for the many high voltage circuits and wires that are necessary to run the bike.
Polymaker™ PC-PBT cell holder
PolyMide™ PA6-CF air duct
Sarolea has found that Polymaker materials are an invaluable tool not only in prototyping but also in the manufacturing and final production of parts for their motorbikes. The technical partnership between the two companies allows Sarolea to push the boundaries of vehicle electrification.
Belgian based electric superbike manufacturer Sarolea has joined forces with Polymaker under a technical partnership.
Sarolea is a revived motorcycle brand that now focuses solely on electric superbikes. Their bikes are built from the ground up and they have been utilizing 3D printing in every stage of production. Sarolea is using a wide range of Polymaker materials in their production processes and sought to gain a closer relationship with Polymaker by using their application engineer's expertise in tuning and printing of parts. This has proven to be valuable for Sarolea as they explore the printing of new materials such as Polymaker PC-PBT in their battery configurations.
"We use the Polymaker filaments during the design process to check components and assemblies. We also use printing as rapid tooling to create moulds for carbon fibre components and thanks to the incredible high quality of Polymaker filament and the expertise of their engineers, certain components on our racing and production bikes are accurately printed. Components that are inhibitively complex and onerous to make with traditional production processes." - Rob Mitchell, Sarolea
Polymaker will be featuring the N60 electric superbike at the Polymaker booth during FormNext 2019 (Booth Number 1211-E111). Displaying three parts that represent stages of production in use at Sarolea. Furthermore, Rob Mitchell from Sarolea will be hosting an open talk during the show on the Polymaker booth, explaining Sarolea's relationship with 3D printing and the journey from prototyping to production.
3D printing technology has become a preferred method for DIY persons, however, the model post-processing to remove layers, the bonding between different parts, painting and so on stay a challenge. A few weeks ago, we noticed an amazing Halo cosplay on social media, the costume was 3d printed using PolyLite™ PLA. This amazing work was done by Alpha to Zeta Industries, and we were very excited to contact them and ask if they would like to share their professional experience with us. We were glad to hear back from Anthony from Alpha to Zeta Industries, they kindly explained all the manufacturing process to achieve such results and were also happy to share it with our community.
If you are interested in cosplays or have challenges building your costumes, you can reach them on social media: Facebook or Instagram. If you are interested in Halo cosplay, you can also visit their group of Halo cosplayers on 405th.com. They have a lot of knowledge to share and are happy to assist new members.
Here is the reply from Anthony explaining how he post-processed his costume:
Hello,
Thank you for reaching out to us about working with Polylite PLA. We are big fans of the video game franchise Halo. And for about 3 years now we have been creating costumes from that franchise under our page, Alpha to Zeta Industries (on Instagram and Facebook). Our primary tool to create these costumes is our 3D printer, our Lulzbot Taz 6. Just recently we created a new version of our Spartan Recluse suit using Polylite PLA. To create this suit, we started with files from Halo 5 Guardians. From there we extensively reworked the models for 3D printing and added details. Once we were ready to print, we selected Polylite PLA due to the positive results we have had with it in the past. To describe the process, I will talk you through how we finished the chest armor. Picture 1 (Attached) is a picture of the raw 3D print fresh off the printer and assembled.
Picture 1
The first problem that we tackled was hiding the seams. This is accomplished by filling each seam with a mixture of baby powder and super glue (CA). Once the seam is filled, an accelerant is added to solidify the bond. We then sand down these seams to make the area flush. Picture 2 (Attached) shows the seams after they have been filled. And Picture 3 (attached) shows them after they have been sanded down.
Picture 2
Picture 3
We then cover the whole piece with a product from Smooth-On called XTC3D. This is a two-part epoxy that fills a large amount of the layer lines while also adding a degree of strength. Once the epoxy has cured, we begin the extensive process of sanding. This process is three parts. First, we apply Bondo spot putty to the piece in any areas that need filling. Once it is dry, we sand the piece down with a high to medium grit sandpaper. Then, lastly, we apply filler primer to the whole piece. This process is repeated until the piece is smoothed to our satisfaction. Picture 4 (Attached) shows the piece after one of the rounds of filler primer.
Picture 4
Once the print lines and any other imperfections are filled to our liking, we then wet sand the whole piece up to 1500 grit sandpaper. This ensures an extremely smooth surface. Once wet sanding is complete the fun really begins. Time for color. We first put down a metallic base coat on the piece. This base coat is then covered with a clear coat. This way when the main color is scrapped off the metal will show for a desired ‘weathered’ look. Picture 5 (Attached) is the piece with the basecoat applied.
Picture 5
After this has dried completely, we then apply the base color and any other desired details. The final result is the piece ready for cosplay! Picture 6 (attached) shows the completed piece.
Picture 6
It can be a process. But our goal is to garner the smoothest finish possible on our costumes and this process has worked great for us so far. The base print quality afforded by Polylite PLA definitely makes it easier than it has been in the past. To close, if anyone is interested in costuming or if there are any questions please feel free to message us on our social media channels. Lastly, if you are interested in Halo cosplay specifically checkout the 405th.com. The 405th is a group of Halo cosplayers who have a wealth of knowledge and are happy to be of service to new members.
Thanks again!
-Anthony
Alpha to Zeta Industries
The Indiana School for the Blind and Visually Impaired (ISBVI) have embraced 3D printing to a degree exceeding all other bodies of education with 3D printed models entering the curriculum in every subject taught on campus. Three years ago, ISBVI started a 3D printing Fab Lab at the school, managed by former student Jacob Ayers.
Dr. Matthew Maurer Ph.D. a professor at ISBVI instantly saw the value of 3D printing and helped Jacob to grow the 3D printing lab into a full-scale operation. With recent boosts in funding and donations, the ISBVI Fab Lab has grown from a janitor’s cupboard with Jacob operating his personal kit-built RepRap to a fully functioning print farm with over 200 3D printers in operation.
Jacob reached out to Polymaker seeking a donation of PolySmooth™ to help provide 3D printed models to the students at ISBVI. Polymaker we happy to donate five hundred pounds of PolySmooth™ 3D printing filament and 5 Polyshers to help post-process the models.
“We’ve been using PolySmooth almost exclusively for the past 2 years of the 3 years we’ve been running. We use the plastic because its: easy to print, it’s easy to post-process, it sands well, it files well compared to other plastics and its smoothable with the Polysher” – Jacob Ayers, Fab Lab Manager, ISBVI.
“When we started this project, the main aim was making models for the classroom, which is important because a lot of blind children see objects only in two dimensions, usually through raised lined drawings. When you put a 3D printed model in their hands, there is a eureka moment when everything falls into place and the subject makes sense for the students.” – Dr. Matthew Maurer, Ph.D. ISBVI
The ISBVI Fab Lab is now encouraging students to join workshops and learn about additive manufacturing as part of design & technology as well as in extracurricular activities. This allows students to gain knowledge of 3D printer operation, CAD software, and post-processing of materials.
“We see some game-changing employment possibilities and workforce development, we are very excited about the possibilities of training students in the additive manufacturing world. Students can learn from the materials and equipment that we have and then drive that knowledge into a career.” – Dr. Matthew Maurer, Ph.D. ISBVI
One project that the seniors are working on is a 3D printed face model of all the class members that are graduating this semester. In this project, the students are learning 3D scanning and file preparation, 3D printing and post-processing. The end result is a 3D printed object they can feel and touch to gain a deeper understanding of their classmate's appearance while also learning new skills.
“We can make the ultimate tactile friendly surface for someone who is blind or visually impaired. When we are creating a tactile object for classroom use, where the information being presented is vital. We don’t want to misconstrued print imperfections for detail. With the Polysher and PolySmooth, we can eliminate all of that with minimal work.” – Jacob Ayers, Fab Lab Manager ISBVI
ISBVI has also partnered with the Benjamin Harrison Presidential Site in Indianapolis, who are working on digitizing their collection of over 10,000 artifacts detailing the life and times of the 23rd President. Charles Hyde, President, and CEO of the Benjamin Harrison Presidential Site explains how digitizing museum artifacts can help educators access and utilize the collection in a compelling and engaging way. The ISBVI Fab Lab is helping print and process the artifacts to create a touch box of five selected artifacts from the Benjamin Harrison collection to give to the students at ISBVI.
“We are literally taking the collection and putting it in the hands of their students. So, we can explain what these five objects are and how they share the wider story of an American presidency.” – Charles Hyde – President & CEO Benjamin Harrison Presidential Site.
The students can then visit the home of Benjamin Harrison and experience the smells and sounds of the presidential home built-in 1874.
The Benjamin Harrison Presidential website have 3D scanned over 60 items, ranging from chairs to swords to top hats. All the OBJ files are free to download through their sketchfab collection.
HP Star is a high-pressure research laboratory investigating environments that mimic conditions found at the core of our solar system’s largest planets. By creating enormous pressures and temperatures on a micro scale the scientists at HP Star can study the effects of the universe’s most abundant elements in the most extreme environments.
The goal of this research is to understand what happens to the basic elements when they are subjected to enormous pressure and temperature which will allow us to gain a deeper understanding of what actually goes on inside the core of a planet. Jupiter, Saturn, and our solar system’s jovian planets are made up of mostly Hydrogen and Helium. These two abundant elements are the main focus for high-pressure experiments conducted at the HP Star labs.
To achieve such high pressures within a laboratory in Shanghai, HP star scientists trap hydrogen gas within a sample chamber which is clamped in between two diamonds. A small piece of metallic foil is laser drilled to create a sample chamber ranging from 20-200 microns. The metallic foil acts as a gasket which is precisely pressed between two diamonds providing a sample chamber for the experiments.
Once the sample gas is trapped between the diamonds the scientists can slowly increase the pressure by tightening steel cells that clamp the diamonds together. This crushes the trapped gas to enormous pressures within the chamber thanks to the incredible hardness and carbon structure of the diamonds. The other benefit of using diamonds to create high-pressure chambers takes advantage of their optical clarity. This allows the scientists to fire powerful infrared lasers through the diamonds into the high-pressure chambers recreating the extreme temperatures and pressures found at planetary cores.
Dr. Dalladay-Simpson is using 3D printing to create cell holders that serve as a platform to conduct the experiments. The cell holders contain the steel cells which provide the clamping force exerted on the diamonds. The material requirements for these cell holders are very demanding as the localised pressure and temperature within the chamber can reach 400 GPa and over 3800°C. While this immense pressure and temperature is very localised within the diamond chamber and only occurs for a short period of time, the material of the cell holders still needs to be very rigid and heat resistant to produce reliable experiments.
“The Earth’s core has a pressure of 320 gigapascals (GPa), in our experiments, we can reach pressures of 400 GPa, when we increase the pressure past this point our diamonds tend to explode under pressure, when they go, it’s pretty spectacular.” – Dr. Dalladay-Simpson
PolyMide™ PA6-CF, the latest material from Polymaker has been the material of choice for the lab. “the rigidity and strength of the carbon-filled nylon produces a really solid cell holder, our focal range works in a tolerance of microns and the cells stay dead on after increasing the pressure.” – Dr. Dalladay-Simpson
With a heat deflection temperature of 215°C, PolyMide™ PA6-CF proves itself as a very good candidate for many types of custom lab equipment not just these cell holders. “Previously for custom lab equipment we expected a 2-3 week lead time from our in-house machine shop and often we would need to further modify the equipment. These new materials [PolyMide™ PA6-CF & GF] rapidly expedite that process, while also producing superior and more formative lab equipment.” – Dr. Dalladay-Simpson
At the other end of the temperature spectrum, PolyMide™ PA6-GF has been used to create cryo boxes which study elements at extremely cold temperatures. These cryo boxes are used for cryogenically cooling the diamond tips until they’re cold enough to condense samples on, either as a solid or a liquid depending on the specimen element.
This allows high-pressure research experiments on solid chlorine, hydrogen sulfide, and other high-temperature superconductors. This research gives insight into the atmospheric conditions experienced by our solar system's gas giants. “We’ve been pouring liquid nitrogen straight into the 3D printed cryo boxes to rapidly cool our cells, we’ve experienced some non-fiber reinforced filaments crack under the heat shock, the PA6-GF performs very well when subject to these conditions.” – Dr. Dallday-Simpson
For Dr. Dalladay-Simpson the end goal is to produce metallic hydrogen in his lab which has been described as the holy grail of high-pressure physics. Metallic hydrogen is a phase of hydrogen in which it behaves like an electrical conductor and was first theorized in 1935 by Eugene Wigner and Hillard Bell Huntington. Researchers believe that metallic hydrogen is present in large quantities in the hot and gravitationally compressed interiors of Jupiter and Saturn. By using an in-house developed RAMAN scattering technique, Dr. Dalladay-Simpson can probe vibrations inside the sample chamber which he hopes will reveal the metallic hydrogen.
Pascal Ballot, French Chef and owner of STYX is using 3D printing to customize his chic restaurant in Shanghai. Using basic shapes Pascal quickly creates a sleek looking napkin holder customized with the STYX logo. The napkin holder positions the STYX napkins so they stand up displaying the branding of the restaurant, they are printed in black PolySmooth™ and finished in the Polysher™. Pascal first prints the individual shapes then assembles the parts with IPA before polishing and sealing the whole utensil in the Polysher™.
Watch Pascal take us through the process below...
Lulzbot has just released their PolyCast™ bundles alongside a comprehensive guide for turning your 3D printed parts into metal parts. This tutorial shows the workflow from CAD to metal part using PolyCast™ 3D printing filament with Ash-Free™ technology. The unique properties of PolyCast™ allow for a very clean burn out when curing ceramic molds during the investment casting process. This leaves a very clean surface on the inside of the ceramic mold which is perfect for metal casting. Ash-Free™ technology typically leaves an ash residue of 0.003%. The Lulzbot Taz 6 has a very large build volume capable of producing very large patterns for investment metal casting. Paired with their wide range of interchangeable tool heads, PolyCast™ patterns can be printed extremely fast with their MOARstruder (1.2mm nozzle) or users can achieve incredible detail suitable for jewelry with their new Aerostruder V2 Micro (0.25mm nozzle) and everything in between.
"3D printing patterns for investment casting is increasingly becoming the go-to solution for artisans, engineers, and industrial professionals alike. With LulzBot 3D Printers and PolyCast™, users are able to test designs, iterate faster, and quickly produce short runs while reducing expensive tooling and long lead times. At a fraction of the cost of most additive manufacturing investment casting solutions, LulzBot 3D Printers enable companies of all sizes to speed innovation while reducing costs." - Lulzbot
Read their full article here: https://www.lulzbot.com/learn/tutorials/3d-print-patterns-investment-casting
3D Printed Bridge & The Potential of Large Scale 3D Printing
The world's first 3D printed pedestrian bridge has now been installed in a Shanghai park serving as a physical landmark in the downtown park, as well as a landmark in large scale 3D Printing. The Bridge weighs in at 5,800kg, of which 12.5% are glass fibers that run through the material adding stiffness and toughness to the ASA-3012 3D printing material developed by Polymaker. The Bridge was printed in just over 30 days and is the first project to be completed by the Shanghai Constructions Group's new large format printer.
The printer has a current build volume of 144 meters cubed the majority of which is consumed by a 25m Y axis allowing for very long objects to be printed. This allows the construction group to venture into unchartered territories for extrusion-based 3D printing on a scale never witnessed before. As we've seen 3D printing penetrate almost every other industry it was only a matter of time until the construction guys got involved.
The pedestrian footbridge can take a load of 13 metric tonnes which equates to 4 people per square meter and the bridge is expected to operate for 30 years in the park. The material used to print the bridge is an acrylonitrile styrene acrylate reinforced with glass fibers and developed by Polymaker through their industrial range of materials. ASA-3012 was chosen as the material of choice due to its weather resistance and good mechanical properties. The addition of the glass fibers (12.5% by weight) adds both stiffness and toughness to the material while also lowering the coefficient of thermal expansion.
This means that when the material is heated and printed the expansion and contraction is much more controlled creating flat layers and eliminating internal stress within the material. The extruder on the 3D printer was developed by Coin Robotic who employed a tamping system to ensure all layers are completely level. The extruder is a pellet fed screw drive system with three heating zones, at the business end there is a 5mm nozzle which can pump 8kg of material per hour in 10mm layers.
Retaining heat on this scale proved to be a big issue in the testing phase of building this system, as it can take over 2 hours before the nozzle passes over the previous layer allowing the material to fully cool and crystallize reducing strength between the layers and producing a strong warp. This led Coin Robotic to add four industrial heat guns to their extruder system that bring the previous layer back up to heat prior to laying down a new layer, by raising the previous layer to the glass transition temperature it greatly increases the interlayer adhesion creating boosting the strength and eliminating the warping as the internal crystal structure can grow through the layers.
As development continues in large scale printing it made me wonder what role this technology could play on a grander scale, what if recycled plastics were repurposed to a 3D bridge instead of continuing the cycle of single-use plastic objects and ultimately ending up in our oceans. PETG used to create disposable drinks bottles is by far the most recycled plastic worldwide and shares many of its properties with ASA, what if we could repurpose the recycled plastic creating a long term solution to plastic waste. 3D printing large structures secures all the repurposed plastic in one place on land which is easy to manage, has a defined lifetime and can benefit thousands of people. While I'm always careful to dispose of my PETG bottles in the recycling bin, allowing the plastic to be turned into another single use bottle, how can I trust the next person will also recycle the plastic? Actually, by recycling the material I've given it another chance to end up in the wrong places, polluting our beaches and oceans. Imagine a third bin next to the current recycling and regular bins, called repurposing, a bin in which all materials are repurposed into long term 3D printed projects that can lock the plastic on land and benefit a huge number of people.
Footage of world's largest plastic 3D printer printing pedestrian bridge
Polymaker just released footage of Shanghai Construction Group’s 3D printer in the process of producing a pedestrian footbridge, which will take 30 days to complete as it will be 15 meters long and weigh 5,800kg. SGC has a reputation for going big as they built the second tallest building in the world, the Shanghai Tower. The 3D printer was built by Shenyang Machine Group and the extruder system was manufactured by Coin Robotic (who also built the bed), together totaling some $2.8 million in investment. Polymaker Industrial developed the ASA (acrylonitrile styrene acrylate) plastic for the print, a material chosen for its favorable properties of weather and chemical resistance, thermal stability, and toughness. To determine the best plastic for the job, Polymaker 3D printed a 5-meter version of the bridge with several different compounds before choosing AS100GF for its overall strength and printability. The bridge will be rated to hold 13 tons or four people per square meter, so strength is vitally important.
The plastic is 12.5% glass fibers by weight, adding strength and also reducing the warping effect that plagues large 3D prints. 3D Printing bigger isn’t as simple as just making a bigger printer because so much of 3D printing is related to heat retention and even heating, which becomes a trickier task the bigger the print/printer. In this case, the build chamber is 24 meters long, 4 meters wide, and 1.5 meters high, with a planned expansion to 3 meters high. That’s 144 cubic meters to keep heated, which is achieved by a large bellowed tent that moves with the gantry. The tent is heated to 38°C and blankets are placed on top of the print to slow the cooling process, allowing the polymer chains to relax without warping; the blankets also protect the print from dust. Yes, the build chamber is so large that technicians work inside the 3D printer while it’s operating to monitor the print and move the blankets.
But heating is only one 3D printing issue that’s exacerbated by increasing scale as there’s also layer levelness as well as bed and layer adhesion. For layers to bond well, they should be joined when they’re at a similar temperature; on this print, each layer takes several hours, so the previous layer has cooled significantly by the time the extruder comes back around for the next layer. The blankets and the glass fibers help slow this cooling, but the print head does a lot of work here by reheating the print with four 600°C hot air guns aimed around the extruder. The air guns ensure the print is always hot around where the extruder is working for maximum layer adhesion.
The layer levelness issue is solved here by a novel approach not seen on other 3D printers: tamping. Nozzles are round, meaning their extrusion is round, and when pushed flat as a layer they have a tapered top, which is not ideal for layer adhesion. For a desktop 3D printer with a nozzle size of 0.35mm, the taper is small enough to mostly not notice, but the SGC 3D printer uses a nozzle over 14x that size at 5mm so the tamping of the plastic right after it’s extruded makes a big difference in layer levelness and adhesion. And considering that, despite its gargantuan size and the fact that it’s extruding up to 8kg of plastic per hour, the printer is accurate to 0.1mm, those differences in levelness really matter. To get the first layer to adhere to the print bed, ASA pellets were glued to wooden planks that were then clamped to the steel bed. Sometimes the low-tech solution is the best solution.
A pedestrian bridge over a lake is a great way to showcase the largest 3D printed plastic object as it’s both an everyday, practical application and an interactive one that involves people touching and even relying upon (to keep them from getting wet) a 3D printed thing. Many people have never touched a 3D printed object and they still think of it as part fantasy and part future tech, so projects like this do a lot of good in terms of exposing the public to the reality and the possibilities of 3D printing.
Nicolas Tokotuu, designer and creator of Nikoss Toys comes from a Pacific island called Wallis and Futuna. This small island of 10,000 inhabitants is located in the middle of the Pacific Ocean between Fiji and Samoa. Resources on the island are very limited. Although the vital resources are still coming by boat, you will never see a lot of “extra” resources imported, especially toys.
“You will not find any toys on my Island [Wallis and Futuna] or you may do but at an insane price. And that’s one of the reasons why when I discovered 3D printing last year I had the idea of creating Nikoss’ Toys.” – Nicolas Tokotuu, Nikoss Toys
Nikoss’ Toys is a brand of digital toys which will be downloadable and printable from all over the world. Starting out 6 months ago, Nicolas begun designing different series of figurines: Nikoss’ Animals, Nikoss’ Insects, Nikoss’ Dinosaurs, Nikoss’ Creatures, Nikoss’ Fish. He chose figurines as his first toys because they are the perfect accessories when children create stories. Children make the toys interact by talking, waving at each other, following each other, etc. This actually makes the child dive into their own story and helps them create their own world. 3D printing allows this world to be limitless, which means the imagination of children will be limitless. Children will not need to create their story according to the toys they have at home anymore, they will be able to imagine a whole new world everyday and print as many different toys as they want. Unfortunately, 3D printed toys so far have not been very attractive for children, especially because of the surface quality. Rough, fade and drafty are not what children are looking for.
“I love PolySmooth, it is just as easy to print as PLA and children can safely watch the printing process without being exposed to nasty fumes. Furthermore children can actually participate in the creation of their toys from downloading to the printing & polishing, truly creating an end product.” – Nicolas Tokotuu, Nikoss Toys.
Nicolas used to print his toys with ABS and PLA, then post processing the toys to make them smooth and attractive to children. But he faced a lot of problems: ABS may be the easiest to post process but if you have children at home it is not very safe to let them participate to the creation of their own toys. The fumes from the printing can be toxic, and the acetone from the polishing process can be dangerous in many ways. Moreover, the printing conditions of ABS are quiet specific. Whereas PLA is the easiest to print, you would want to keep your child away from any of the solvents used in post processing. Furthermore, the post process itself is not easy to accomplish correctly. Polymaker has solved all of these problems by creating PolySmooth and its new desktop machine the Polysher.
“I love PolySmooth, on one hand it is just as easy to print as PLA and children can safely watched the printing process without exposing them to fumes. No more hassle with ABS. On the other hand, I love this material because the support is as easy to remove as ABS. Last but not least, the Polysher allows a polishing process completely effortless and semi automated, while most importantly, much safer for children. Which means that children can actually participate in the creation of their toys from downloading to the end product.” – Nicolas Tokotuu, Nikoss Toys.
If you love Nikoss Toys as much as we do you can download all the files from Nicolas’s Thingiverse account
Carbon Wasp Ltd is a UK based company that designs and makes one off custom carbon fibre parts, with a focus on bicycle products. It makes custom products for individuals and while also providing prototyping and development projects for other companies and industries.
Carbon Wasp has been developing its process for several years and a key part of that is the use of 3D printed moulds. Using pre-preg carbon fibre to create their custom bike frames Carbon Wasp needed a plastic that strong enough hold up against the large internal pressures while withstanding high temperatures of up to 130℃. Polycarbonate is an obvious choice of material, but they had real difficulty finding a brand of filament that met their needs.
“We tried many different types of polycarbonate filament, from a number of manufacturers, but only PC-Plus from Polymaker provides the result we need.”
-Adam Smith
PC-Plus is strong, temperature resistant, but most importantly for Carbon Wasp it prints very well. Its moulds can be large single pieces which take many hours to print, so reliability of printing is really important. PC-Plus is easy to print, gives consistent results and doesn’t suffer most common issues with PC, such as excessive warping. Polymaker’s PC-Plus has thus become a key part of Carbon Wasp’s working process.
Italian electric car company XEV and 3D printing material company Polymaker organized a joint press conference at the China 3D-Printing Cultural Museum in Shanghai. The first mass-producible 3D-printed electric car in the world was launched and shown to the public.
Although this new vehicle attracts much attention, this conference is not just about launching and exhibiting the car. It is more about how 3D printing technology brings revolutionary changes to automotive manufacturing industry. This car, named LSEV, could be the milestone product in the adoption of 3D printing into mainstream production.
“XEV is the first real mass production project using 3D printing. By saying real, I mean there are also lots of other companies using 3D printing for production. But nothing can really compare with XEV in terms of the size, the scale, and the intensity.” Said, Dr. Luo Xiaofan, the co-founder and CEO of Polymaker.
XEV CEO, Stanley said that “after the research and investigation of the global auto market, they decided to design a small electric vehicle that can achieve C2M (Customer-to-Manufacturer) manufacturing which is stated as a main goal of the Industry 4.0 strategy.”
To fulfill this target, it requires mass customization production, fast and cost-effective R&D, and the ability to produce lighter-weight parts that could lead to greater fuel efficiency.
“And then, 3D printing technology becomes the only way to realize it”, said Stanley.
Surely there are many difficulties when utilizing 3D printing technology in auto volume production, Polymaker was chosen as the strategic partner and successfully helped XEV to solve them, not only with material solutions, but also post-processing options in-line with the automotive industry.
“Without Polymaker, we couldn’t make this happen. We really like our interactions with Polymaker, this can be called as know-how combination. Without this kind of interaction, we also couldn’t find the solution we have today. So, we really appreciate what Polymaker do and create for us, we are like brothers, not just strategic partners.” said, Stanley.
Polymaker developed dozens of kinds of engineering plastics for XEV to meet their needs of practical applications. As a result, 3 crucial achievements have been accomplished.
XEV has decreased the plastic parts and number of components in a car from more than 2,000 to 57, and the finished LSEV weighs only 450 kilograms, much lower than similar sized vehicles usually weighing between 1 and 1.2 metric tons.
Apart from the chassis, seats and glass, all the visible parts of the car are made by Polymaker materials through 3D printing. This switch of production leads to more than 70 percent reduction of the investment cost in comparison with a traditional production system.
Conventionally the R&D process of a car model takes about 3-5 years, but it only takes XEV 3-12 months to finish a new design.
Polymaker have also come up with solutions to help with surface treatments and color. These solutions are enormously helpful in customized production and 3D printing volume production.
XEV has already received 7000 orders from Europe even before mass production commences. 5000 orders come from Poste Italiane. And the other 2000 orders come from ARVAL, a vehicle leasing company fully owned by BNP Paribas. XEV plans to start production in the second quarter of 2019.
This strategic partnership between XEV and Polymaker leads to a revolutionary change in automotive manufacturing. It is possible that similar changes, related with 3D printing technology, will happen to every aspect of manufacturing very soon. As Polymaker proves that the 3D printing materials they provide are ready for not only end-use parts but also mass production of finished products.
COMPUTATIONAL HYDROGRAPHIC PRINTING WITH POLYSMOOTH
Recently Polymaker visited Zhejiang University where professor Kun Zhou and his team in the Computer Science Department have developed an interesting new method of precisely coating 3D objects. Their process uses hydro transfer as a method of delivering a 2D printed sheet onto a 3D object. The magic behind the technology is the software developed by the team. The simulation software creates a 3D texture map between the colors on the film and the surface locations on the model. This 3D texture map is then transformed into a 2D image that you can print directly onto the PVA film. The software can predict exactly where the mask will hit the water and compensate the 2D image so that it stretches in the right places. The degree of accuracy that can be achieved with this method is astonishing. Since you need a 3D model of your object for the software to calculate the texture map, this technology seems perfectly matched to 3D printing.
Until now professor Kun Zhou has not been satisfied with the surface quality of FFF/FDM prints for his technology. The problem being the rough layered surface doesn’t take the film very well due to all the pits and falls in between layers. This forced him to shell out on an industrial SLA printer capable of matching the quality that his software can produce. However the nature of the technology is very low tech, all you need is a regular 2D inkjet printer, PVA film, a tub and a linear rail. So it seems like the extremely expensive industrial printer doesn’t match the relatively low tech nature of the coating process.
Polymaker introduced PolySmooth to professor Kun Zhou as a solution to this problem. By using PolySmooth models as a base you create a perfect clean surface for the PVA film to morph too. Professor Kun Zhou even noticed he gained more accuracy once he started using PolySmooth due to the layers being eliminated. As the software made its calculations based on parametric surfaces the extra surface area for the ups and downs of the layers was not accounted for previously. Now with PolySmooth the process can be even more refined allowing multiple immersions with incredible dimensional accuracy. Furthermore with the low cost of the Polysher & PolySmooth, this technology is available to a much wider audience, including home users and hobbyists. Allowing PolySmooth & the Polysher to take FDM/FFF printers into the league of industrial machines.
For more information on this process watch our video below