Polymaker recently worked with 3DQue Systems, a company that retrofits existing 3D printers for hands-free part removal and high-volume production. They are the first company who use PolyCast™ as support to print metal parts and automate this process with the Ultimaker S5.
Quinly automation system
3DQue’s automation system, Quinly, is a virtual printer operator, that can be installed on Raspberry PI and connected to 3D printers. When installed, Quinly can queue preloaded Gcodes, auto-level, execute part removal after a print job is completed, and start the next print job. 3DQue designed its VAAPRTM print bed that provides 500x adhesion when heated and allows easy release when cooled, without additional adhesives. Automated part removal is achieved using a gravity-assisted mechanism: Quinly incorporates a mechanical motion of the printer head/bed, to sweep off printed part, before starting the next print job. Quinly also provides real-time data, failure notification, and Livestream access to the print. By eliminating a significant portion of the manual tasks in a print job (filament still needs to be changed manually), Quinly reduces per part cost by 80%.
Fig (1) Quinly equipped Ultimaker
PolyCast™: Easily Removable
In this specific case, 3DQue automated metal 3D printing in a new and innovative way: Metal and PolyCast™ filament are extruded into build and support structures using a dual-head printer. PolyCast™ filament served as an effective raft material and was fully compatible with Quinly’s VAAPR™ surface. The printed rafts had excellent bed adhesion at 60°C and were fully released at 35°C. This allowed all parts to be autonomously removed from the printer via the wiper arm mechanism included in the Quinly for Ultimaker S5 automation system. The printer required only 10 minutes to cool and clear the print bed between print jobs.
Among a few other support materials 3DQue evaluated, PolyCast™ stood out for its performance in clean removal.
Fig (2) Flow chart for using Polycast™ as a support for metal prints before sintering
PolyCast™: Ash-Free
And then, printed parts were sintered with the rafts and supports in place. The PolyCast™ filament was burned away, leaving only 0.003% residue. Sintering without a raft was tested as well: the PolyCast™ rafts did not fuse with the metal filament and were easily removed by hand.
PolyCast™ is a PVB-based material designed for metal investment casting. It shares a similar formulation with the well-known PolySmooth™ and comes with ash-free technology that enables clean removal. PolyCast™ is also safe and easy to post-process. It is smoothable with IPA in Polysher™, or similar tools.
Fig (3) Ash content comparison between with Ash-Free and without Ash-Free
PolyCast™ rafts make Quinly fitted Ultimaker printers compatible with many metal filaments on the market. The raft easily slides off the bed once cooled, making metal filament bed adhesion issues a thing of the past.
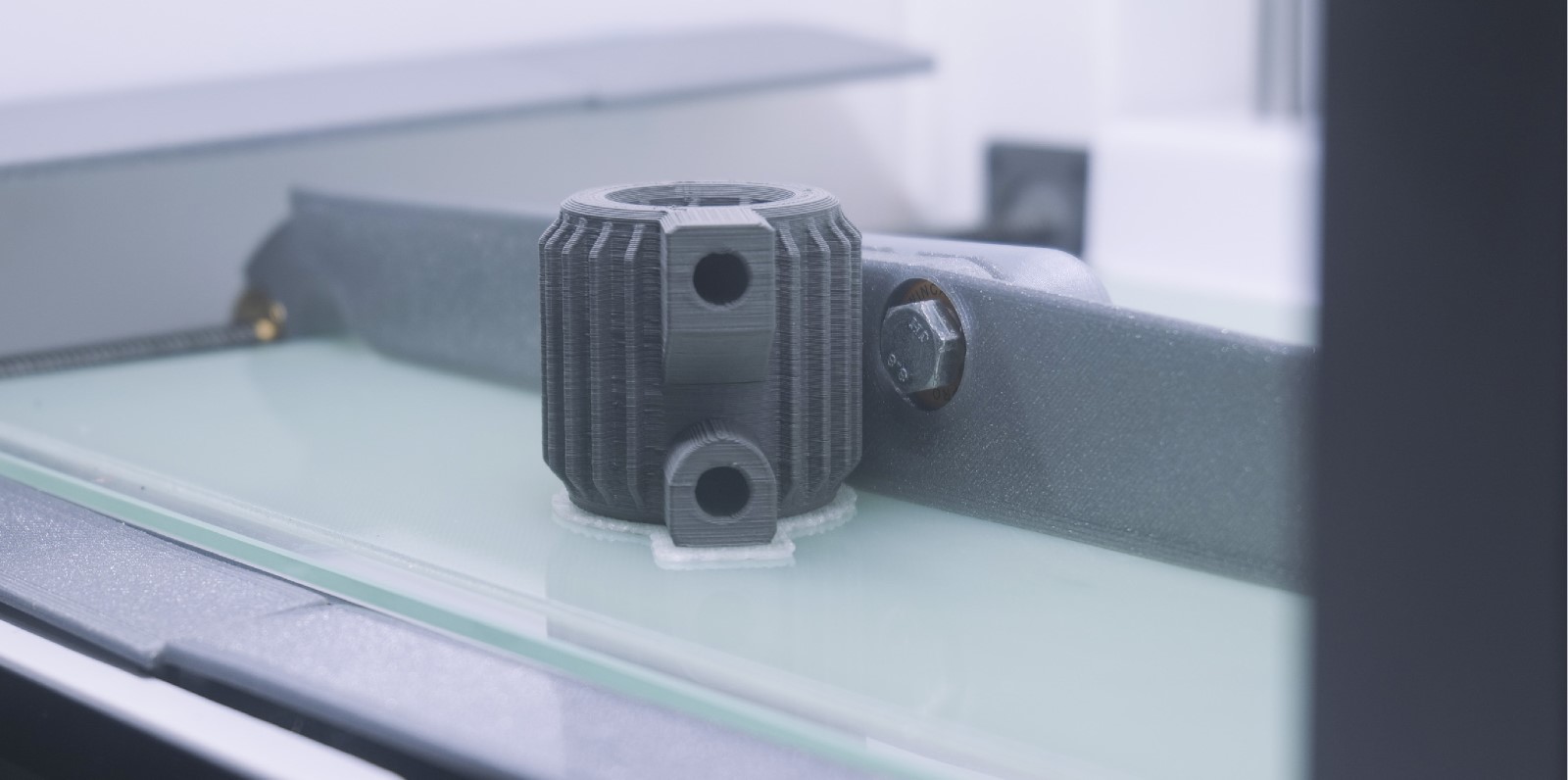
Demonstrated by 3Qque, PolyCast opens a potential avenue to mainstream manufacturing processes of metal parts. Beyond investment casting, in which PolyCast has gained significant attention, this case study brings an inspiring application of PolyCast. Due to the clean burnout nature of PolyCast, complex geometry in metal part fabrication is made possible by printing the PolyCast filament as support to the metal filament.
What’s more? Automation of the printing and part harvesting, enabled by systems such as Quinly, could make high-volume complex metal part production feasible and economically competitive.